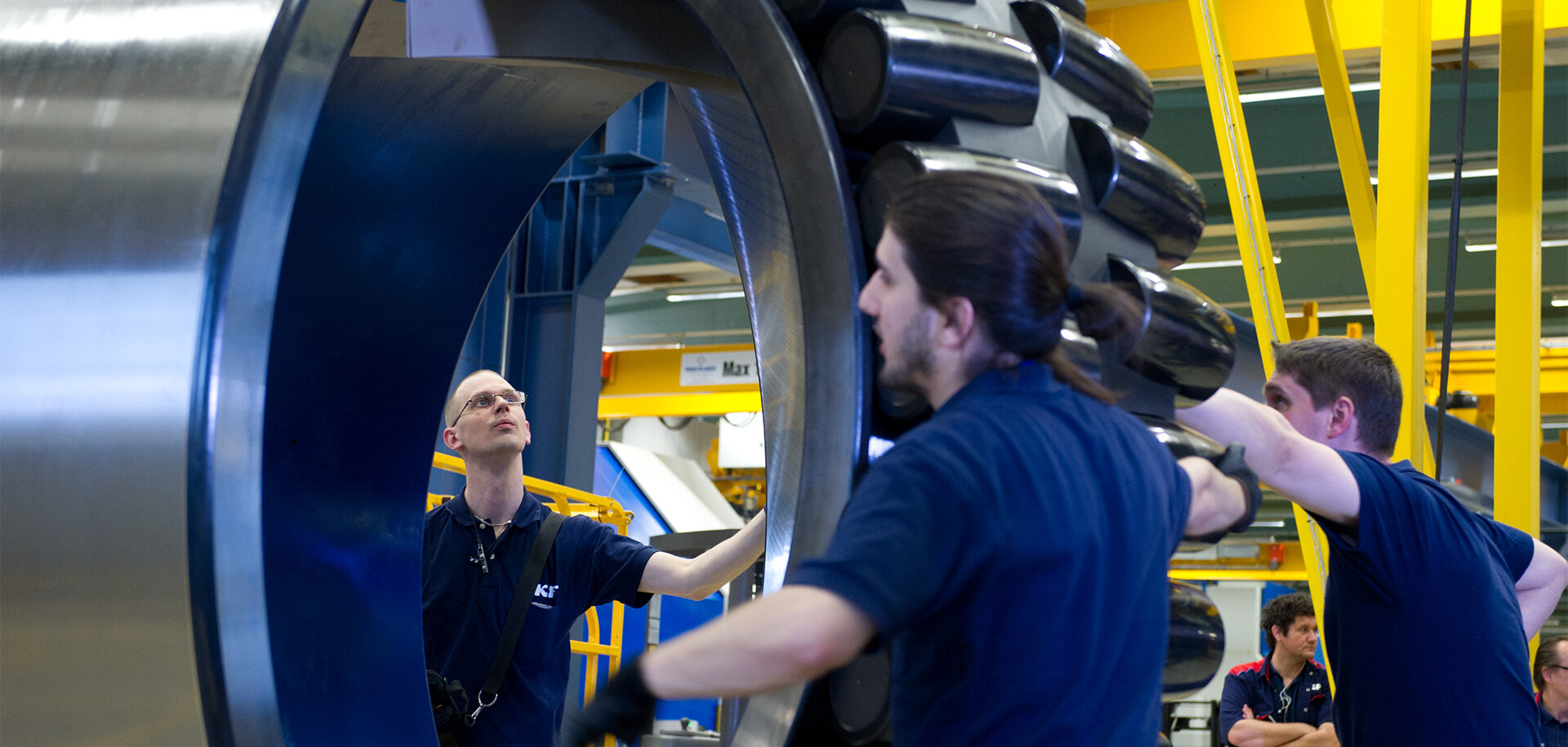
Покрытия для улучшения характеристик подшипников
Покрытия позволяют увеличить срок службы и оптимизировать характеристики подшипников качения и скольжения. Выбор покрытия может зависеть от рабочих условий и эксплуатационных требований. Компания SKF предлагает более 35 различных специализированных покрытий.
Считается, что подшипники качения могут работать практически бесконечно, если соблюдены следующие условия эксплуатации:
- приложенное напряжение не превышает определенное значение;
- используется надлежащая смазка;
- отсутствуют загрязнения. Разумеется, в некоторых случаях условия эксплуатации значительно отличаются от идеальных или возникают непредвиденные проблемы, повышающие расходы на эксплуатацию и техническое обслуживание.
Чтобы продлить срок службы подшипников и оптимизировать их характеристики в неидеальных рабочих условиях, были разработаны различные стратегии. Одна из стратегий — использование покрытий, которые могут влиять на следующие характеристики:
- износостойкость;
- повышенное или пониженное трение;
- коррозионная стойкость;
- свойства скольжения;
- улучшенная смазка или сокращение потребности в смазке во время работы;
- электроизоляция;
- водородный барьер;
- защита от фреттинг коррозии;
- улучшение внешнего вида.
Покрытие — это стандартная стальная подложка подшипника, на которую нанесен обладающий определенными свойствами материал, значительно улучшающий рабочие характеристики. Подшипники с покрытием также могут использоваться для устранения разрыва между стандартными стальными подшипниками и гибридными керамическими подшипниками. В некоторых областях используются керамические роликовые подшипники (хорошее, но дорогое решение), которые бывает сложно найти на рынке. В этом случае обеспечить нормальный уровень работы стандартных подшипников можно с помощью покрытий.
Некоторые покрытия наносятся очень тонким слоем, что обеспечивает важное преимущество. Покрытия толщиной всего лишь несколько микрон позволяют использовать стандартные, серийно производимые подшипники без дополнительных расходов на изменение настроек обрабатывающих станков.
Обзор технологий нанесения покрытий
Как показано на рис. 1, в компании SKF используют различные технологии нанесения покрытий. Их можно разделить на три основные категории:
- Методы с использованием газообразного состояния, когда материал покрытия перед осаждением на поверхность преобразуется в газовую или паровую фазу. Сюда относятся такие технологии вакуумного напыления, как физическое осаждение из паровой фазы (PVD) и плазмохимическое газофазное осаждение (PACVD).
- Методы с использованием жидкого состояния, когда материал покрытия находится в жидкой фазе перед тем, как осадится на поверхности в виде твердых частиц. Методы можно разделить на категории химического (химическое осаждение, электролитическая обработка, гомогенные химические реакции, погружение и жидкостное распыление) и электрохимического осаждения, например гальваническое осаждение металлического покрытия на электроде посредством электролиза.
- Методы с использованием расплавленного материала, когда перед осаждением материал покрытия расплавляется или расплавляется частично (размягчается), а затем с помощью источника высокой мощности осаждается на поверхность в виде твердого вещества. Методы подразделяются на осаждение распылением (охватывает широкий спектр технологий с быстрым нагревом материала в горячей газообразной среде и одновременном направлении материала с большой скоростью на поверхность для формирования покрытия) и технологию лазерной плакировки.
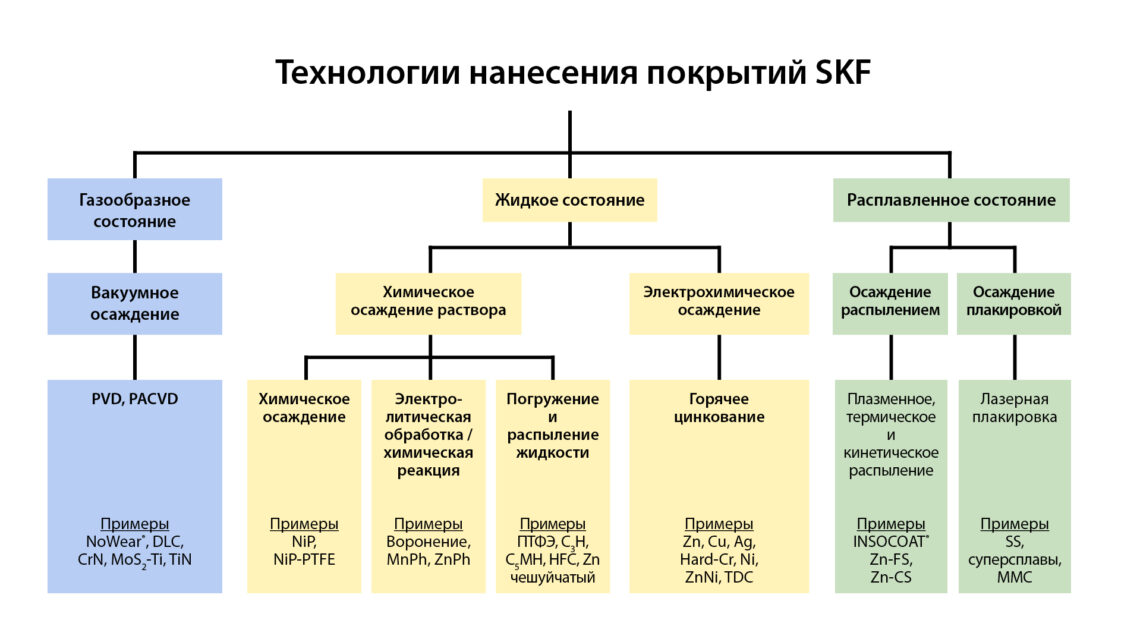
Мир покрытий SKF
Ассортимент SKF включает более 35 современных покрытий, которые можно использовать в самых разных областях, для различных частей подшипников. Все покрытия оптимизированы с учетом особых требований, предъявляемых к подшипникам, и выполнены в соответствии с точными спецификациями и под строгим контролем качества. Покрытия производятся на технологичных предприятиях по нанесению покрытий, требования на которых часто превышают требования стандартов для покрытий и оборудования, и которые обеспечивают максимальное качество, надежность и воспроизводимость.
Некоторые покрытия наносятся очень тонким слоем, что обеспечивает важное преимущество
В этой статье рассматриваются некоторые из наиболее часто используемых покрытий SKF. Полный список покрытий SKF вместе с их физическими, химическими и трибологическими свойствами опубликован онлайн в каталоге покрытий SKF.
Подшипники качения
На рис. 2 перечислены 12 основных покрытий, которые обеспечивают пять основных характеристик для подшипников качения, включая защиту сепараторов от износа при трении скольжения, электрическую изоляцию, защиту от фреттинг-коррозии, защиту от коррозии и износа для дорожек качения.
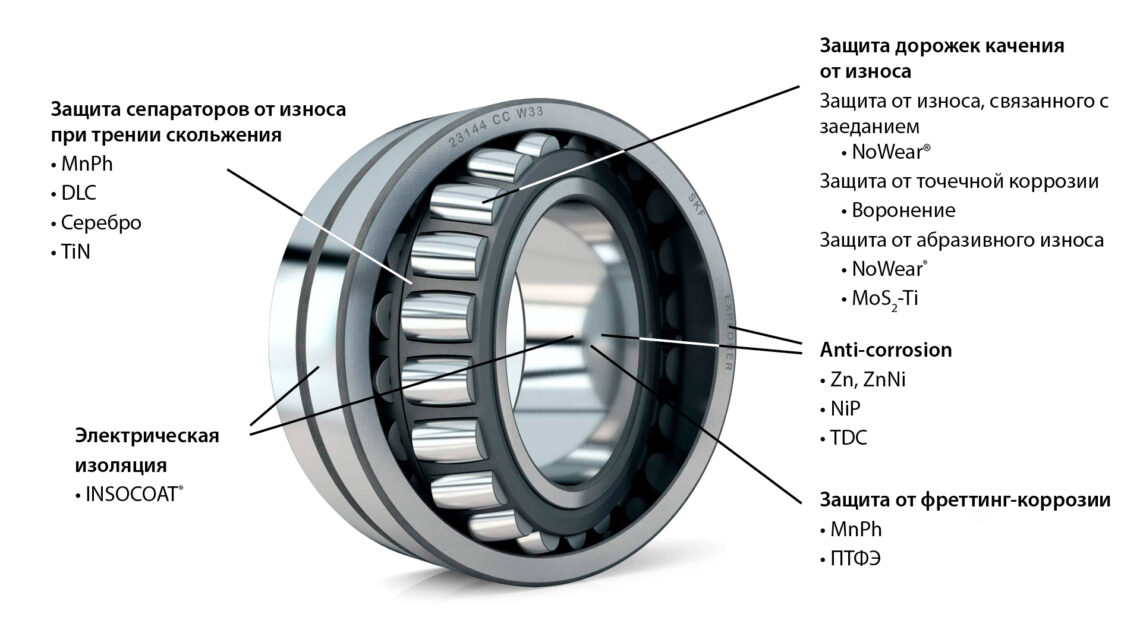
a. Защита дорожек качения от износа
Black Oxide: Обработка поверхности с помощью химической реакции на поверхности стальных компонентов подшипника. Покрытие наносится на поверхности всех компонентов подшипника. Детали погружаются в различные водно-солевые щелочные растворы при температуре 140–150 °C. В результате реакции между железом в легированной стали и реагентами формируется черный слой толщиной около 1 мкм, состоящий из хорошо образованной смеси FeO, Fe2O3 и Fe3O4. Покрытие обладает множеством преимуществ, в том числе минимизирует износ при трении скольжения и адгезионный износ. Оно также улучшает процесс приработки, обеспечивая очень гладкую поверхность, что приводит к более низкому окончательному стационарному трению по сравнению с подшипниками без покрытия. Другое преимущество — улучшение адгезии масла, что создает защиту от легкой коррозии. Воронение также образует защитный барьер от гидрогенизации, защищая расположенную под покрытием сталь. Кроме того, слой покрытия повышает устойчивость к точечной коррозии, заеданиям, сколам, фреттингу и трещинам на поверхности и преждевременной усталости. Наконец, покрытие защищает поверхность от наносящих вред противозадирных присадок (EP), которые часто применяются в смазках для редукторов ветровых турбин.
NoWear®: Компания SKF стала первым в мире производителем подшипников с углеродным покрытием. Покрытие можно наносить на поверхность всех компонентов подшипника, но лучшие результаты получают при нанесении покрытия только на ролики. Детали вместе с химическими веществами размещают в вакуумной камере и используют метод PACVD. В процессе физических реакций смесь паров углерода и металла, создаваемой плазмой, конденсируется на компоненте при температуре ниже 180 °C. Получаемое темно-серое аморфное покрытие толщиной около 3 мкм характеризируется средней твердостью и очень низким трением даже в сухом состоянии. Это покрытие оптимально подходит для дорожек качения подшипников при высоком контактном давлении. Покрытие NoWear®, запатентованное в 1999 г., уменьшает адгезию, заедание, поверхностную усталость, микроточечную коррозию и обеспечивает крайне низкий износ в условиях недостатка смазки. Кроме того, разработанное многослойное покрытие содержит специальный слой-подложку для повышения адгезии и верхний графитовый слой для улучшения процесса приработки.
MoS2+Ti: Аморфный слой из дисульфида молибдена (MoS2), легированный титаном (Ti), толщиной около 1–3 мкм, который по своей твердости аналогичен покрытию NoWear®. Специально разработанное покрытие отличается очень низким трением и высокой износостойкостью при использовании в сухих, вакуумных средах и в условиях чистой комнаты. Детали помещают в вакуумную камеру и используют метод PVD. В результате физических реакций пар, создаваемый плазмой, конденсируется на детали при температуре ниже 180 °C.
b. Защита от коррозии
Zn и ZnNi: Слои из цинка и никель-цинкового сплава толщиной 1–15 мкм осаждаются электролитическими методами и далее пассивируются для обеспечения улучшенной защиты. Обычно такое покрытие не применяется для дорожек качения подшипников. Традиционный способ защиты от коррозии — применение цинка, но использование никель-цинкового сплава позволяет устранить некоторые недостатки исключительно цинкового покрытия, например его низкую твердость. Помимо антикоррозионных свойств цинк обеспечивает большой коэффициент трения, что можно использовать для противоскольжения и защиты от фреттинг-коррозии наружных поверхностей подшипника, внутренних отверстий или отверстий в корпусе подшипников.
NiP: Слой из никель-фосфорного сплава серебристого цвета толщиной 10–50 мкм осаждается автокаталитическим химическим методом. Используются три варианта с различной концентрацией фосфора в диапазоне 6–14 %. Увеличение концентрации фосфора улучшает антикоррозионные свойства, но ухудшает твердость и износостойкость. Такие покрытия обычно используются там, где требуется комбинация антикоррозионных и противоизносных свойств, исключая дорожки качения. При этом покрытия толщиной менее 3 мкм также могут применяться для дорожек качения.
TDC (хромовое покрытие низкой плотности): Поликристаллическое хромовое покрытие серебристого цвета толщиной 2–5 мкм. Покрытие наносится методом электролиза с хромовым кислотным электролитом. Для образования тонкого слоя хрома с узловатой структурой процесс далее катализируется, например, с помощью дихромата калия. Слои TDC можно наносить на дорожки качения подшипников и на наружные поверхности. Помимо хорошей коррозионной стойкости покрытие обла
c. Защита от фреттинг-коррозии
PTFE: Полимерное покрытие толщиной 10–20 мкм. Политетрафторэтиленовый (ПТФЭ) порошок распыляется на поверхность методом воздушного или электростатического распыления, формирование слоя осуществляется в процессе теплового спекания. Покрытие отличается великолепными антифрикционными свойствами, очень низким трением и обеспечивает защиту от прерывистого скольжения. Оно придает подшипникам свойства для постоянной и эффективной защиты от фреттинг-коррозии внутренних или наружных диаметров колец подшипников.
d. Электрическая изоляция
INSOCOAT®: Это электроизоляционный слой оксида алюминия толщиной 100–300 мкм, который наносится плазменным напылением в атмосферной среде. Расплавленные частицы Al2O3 распыляются на стальную подложку и, соответственно, заполняют пористую структуру. Дополнительный этап чистового шлифования помогает обеспечить корректные размеры подшипников. Покрытие наносится либо на наружные поверхности внешнего кольца подшипника, либо на внутреннюю поверхность канала внутреннего кольца. Основные преимущества покрытия INSOCOAT® связаны с электрической изоляцией , которая препятствует прохождению электрического тока через подшипник, вызывающего эрозию поверхностей качения.
e. Защита сепараторов от износа при трении скольжения
Ag: Слои серебра (Ag) толщиной 2–4 мкм осаждаются гальваническим способом. Для увеличения адгезии серебра обычно используется медная подложка. Это мягкий металлический слой с характеристиками сухой смазки используется при высоких температурах и в вакуумных средах. Данное покрытие характеризуется исключительной электропроводностью и обеспечивает хорошую антикоррозионную защиту от воздействия химических веществ (умеренные щелочи и кислоты). По большей части такое покрытие напыляется на стальные сепараторы и в редких случаях на кольца и ролики для областей применения с высокими требованиями, например в качестве сухой смазки в вакуумных средах, в пищевой и аэрокосмической промышленности.
TiN: Покрытия из нитрида титана (TiN) представляют собой слои золотистого цвета толщиной 1–5 мкм. Детали помещают в вакуумную камеру и используют метод PVD. В результате физических реакций пар, создаваемый азотной плазмой, распыляется с титановой мишени и конденсируется на детали при температуре ниже 180 oC. Такие покрытия используются для защиты от износа сепараторов при наличии смазок и для внутренних втулок подшипников для пищевой промышленности.
Подшипники скольжения
На рис. 3 представлены восемь основных покрытий, придающих подшипникам скольжения три главных свойства: антикоррозионные и износостойкие покрытия для подшипников с густой смазкой или без нее.
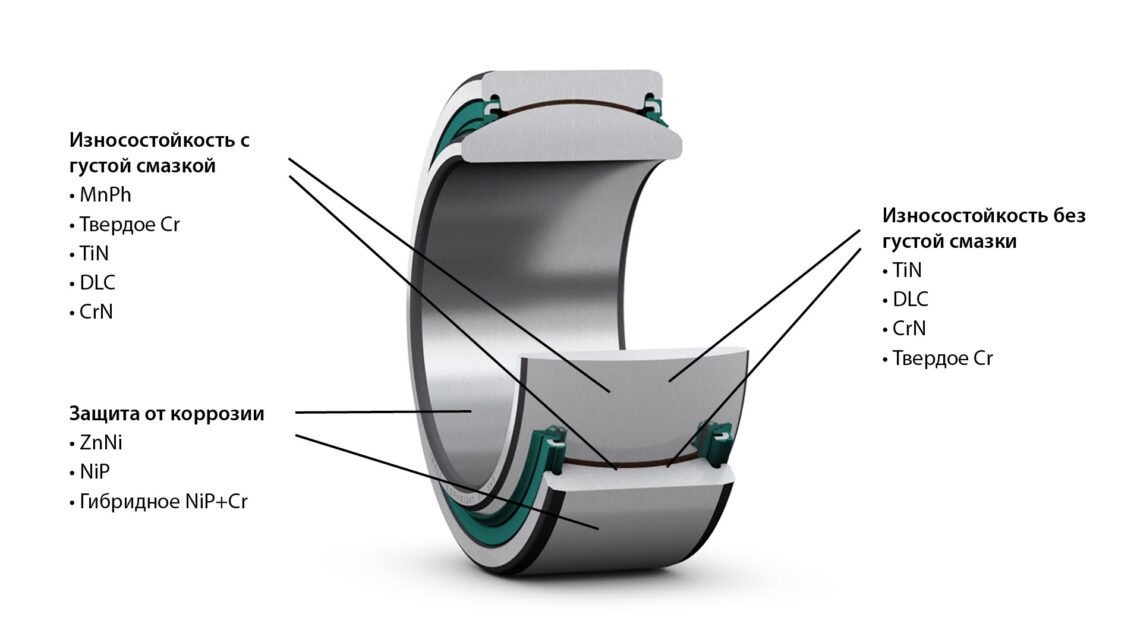
a. Износостойкость без густой смазки
Твердое хромирование Это покрытие представляет сбой твердый слой хрома (Cr) серебристого цвета толщиной 3–15 мкм, осажденный методом электролитического осаждения с использованием кислотного электролита с хромом. Процесс завершается очисткой, удалением шестивалентного хрома [Cr(VI)] и нанесения защитного масла. Покрытие обеспечивает хороший скользящий контакт между компонентами подшипника скольжения, отличается большой твердостью и высокой износостойкостью. Нанесенный слоя хрома содержит микротрещины, что ограничивает антикоррозионные свойства при малой толщине покрытия.
CrN: Покрытие из нитрида хрома (CrN) представляет собой нанесенный методом PVD слой серебристо-сероватого цвета толщиной 1–6 мкм. Детали помещаются в вакуумную камеру, где твердотельные мишени из чистого хрома бомбардируются ионами плазмы Ar+N, которые испаряют хром («металлизация напылением»). Атомы Cr соединяются с N и конденсируются на детали при температуре ниже 180 °C. Результат — твердое покрытие, которое хорошо защищает от износа при трении скольжения, а также обеспечивает защиту в некоторых коррозионных средах. Покрытие также может применяться в подшипниках качения вместе с кольцами с покрытием из CrN и роликами с покрытием NoWear®. Кроме того, покрытие используется в качестве подложки для других покрытий с целью увеличения устойчивости к контактному давлению.
DLC (алмазоподобный углерод): Это общее название группы углеродных покрытий, содержащих смесь графитовых и алмазных микроструктур. Такие покрытия могут включать или не включать водород, толщина покрытий обычно составляет 2–4 мкм. Обрабатываемые детали помещают в вакуумную камеру, где на поверхность компонентов подшипников наносится несколько слоев методом PVD или PACVD в соответствии с областью применения. Состав слоев влияет на свойства покрытий. Покрытия DLC предназначены для эксплуатации в условиях высокого износа и недостатка смазки. Такие покрытия отличаются высокой стойкостью к износу при трении скольжения и адгезионному износу, способностью выдерживать высокую нагрузку, великолепной абразивной защитой и малым трением, а также обеспечивают защиту поверхности при недостатке смазки. Покрытия DLC идеально подходят для подшипников скольжения, подшипников линейных приводов, подшипников валов, втулок, штифтов, взаимодействующих с кулачками и скользящих деталей в подшипниках качения (например, сепараторы и уплотнения). Разработанное металлокерамическое покрытие NoWear® также относится к этому семейству углеродных покрытий; однако существуют некоторые различия. Значения твердости покрытий DLC для подшипников скольжения находятся в диапазоне 18–30 ГПа (1800–3000 HV (твердость по Виккерсу)), а покрытий NoWear® (используются в подшипниках качения) около 12 ГПа (~ 1200 HV).
b. Износостойкость с густой смазкой
MnPh: Марганцевое фосфатное покрытие (MnPh) — серый или черный слой толщиной 2–15 мкм. Покрытие наносится путем химической реакции, как правило, на поверхности всех деталей. Детали погружаются в раствор для фосфатирования, содержащий марганец, железо в деталях реагирует с катионами марганца и анионами фосфата в растворе. Покрытие обладает свойствами защиты от износа и фреттинг-коррозии, что значительно улучшает защиту от заедания и повышает стойкость к микроточечной коррозии. Покрытие также обеспечивает защиту при низкой относительной диэлектрической постоянной (каппа) и характеризуется улучшенной адгезией маслу. Кроме того, покрытие MnPh отличается хорошей защитой от коррозии (в смазанном состоянии) и характеристиками электроизоляции.
c. Защита от коррозии
Гибридное покрытие NiP+Cr: Это твердое покрытие, состоящее из никель-фосфорного и хромистого слоев общей толщиной 10–30 мкм. Процесс покрытия состоит из двух отдельных частей. Сначала на поверхность для улучшения защиты от коррозии и придания химической устойчивости химическим способом наносится NiP, затем методом электролитического осаждения добавляется твердый слой хрома, который обеспечивает механическую прочность.
Путь к устойчивому развитию
Устойчивое развитие в сфере подшипников включает такие аспекты, как сбережение энергии и ресурсов, минимизация отходов, повышение эффективности процессов и использование возобновляемых материалов. Компания SKF — мировой технологический лидер, который рассматривает техническое преобразование как ответственность и отличную возможность. Повторное использование промышленных материалов и компонентов, например масла и подшипников, может стать отличным началом. Предложения, от простых уплотнений и подшипников до ключевых промышленных компонентов и систем, помогают, к примеру, разрабатывать легкие решения с малым трением для автомобильной промышленности, которые способствуют уменьшению выбросов CO2. Другой подход, отвечающий целям устойчивого развития, — использование технологий покрытий, которые в некоторых областях применения уменьшают трение (и, соответственно, энергопотребление) и увеличивают срок службы подшипников (тем самым снижая расход сырья).
Заключительные замечания
Использование покрытий для подшипников вызывает все больший интерес. Выбор материалов и структуры покрытий позволяет создать изделие с уникальными физическими, механическими и трибологическими свойствами для удовлетворения постоянно возрастающих технологических потребностей. В частности, проводился тщательный анализ покрытий SKF с целью достичь оптимальных характеристик; в некоторых случаях в соответствии с различными областями применения процессы были скорректированы с превышением требований стандартов DIN и ISO.
В данной статье кратко описаны некоторые типы покрытий SKF и поясняются некоторые терминологические и технические аспекты, а также конструкция покрытий. Подробнее см. в нашем каталоге покрытий SKF.