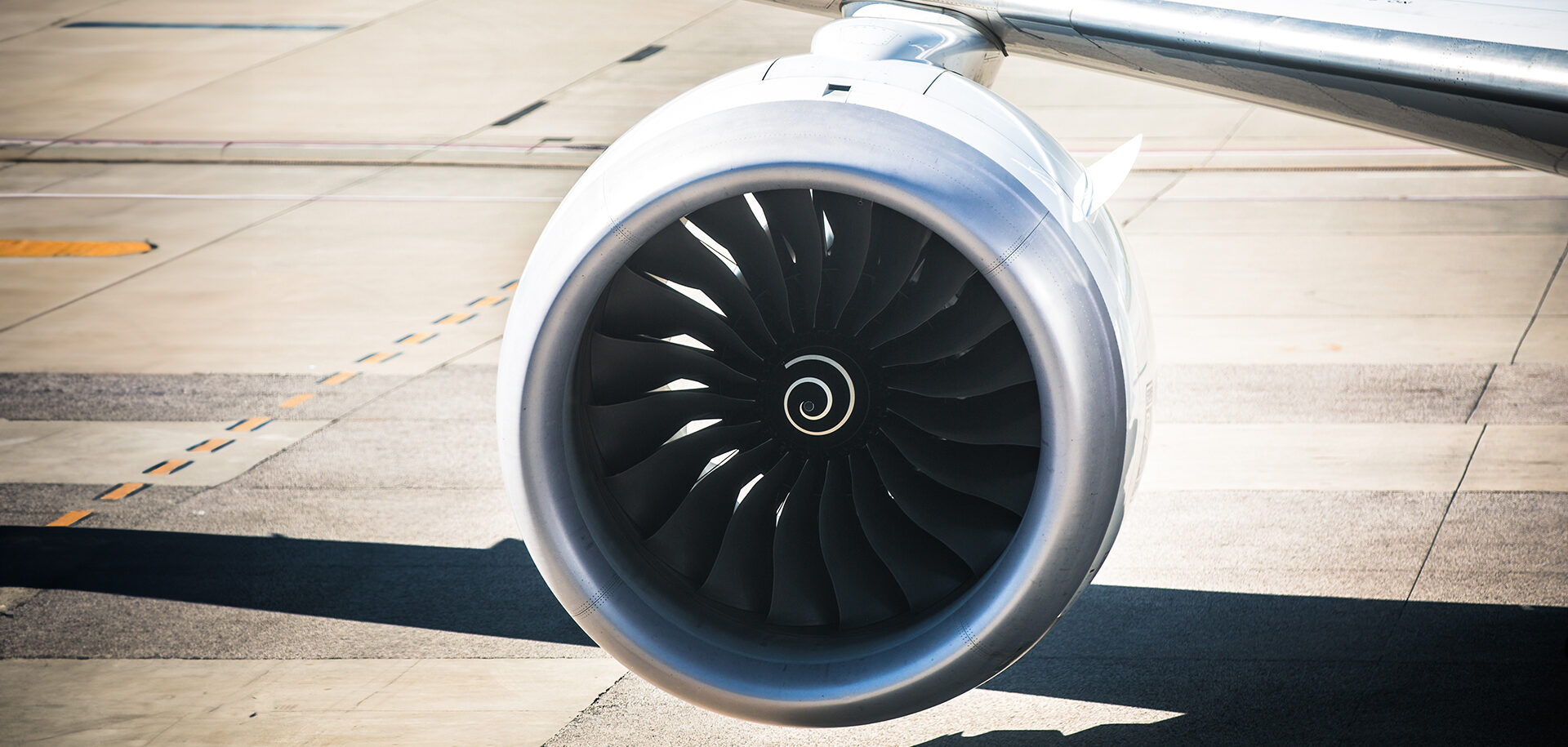
Совместные инновации для полетов будущего
Центр аэрокосмического развития компании SKF совместно с клиентами разрабатывает ключевые технологии для воздушных судов будущего.
Последние годы были поистине бурными для мировой авиационной отрасли. Сначала резкий упадок пассажирских перевозок из-за локдаунов и ограничений в результате пандемии коронавируса. Затем, когда мир начал возвращаться к нормальной жизни, отрасль столкнулась с мощным эффектом возрождения: только в 2022 г. количество авиапассажиров возросло на 47 %.
По мнению экспертов Международной организации гражданской авиации, в 2023 г. спрос на пассажирские авиаперевозки превысит уровень до пандемии, а самолетостроительные компании сообщают о занятости производственных линий и заполнении портфеля заказов.
И хотя это отличные новости, авиационная отрасль в долгосрочной перспективе по-прежнему будет сталкиваться с серьезными проблемами, в числе которых — задачи по устойчивому развитию, поставленные властями различных стран мира. Однако, в отличие от многих других отраслей, здесь еще не определены технические решения, необходимые для создания воздушного транспорта с нулевым уровнем выбросов.
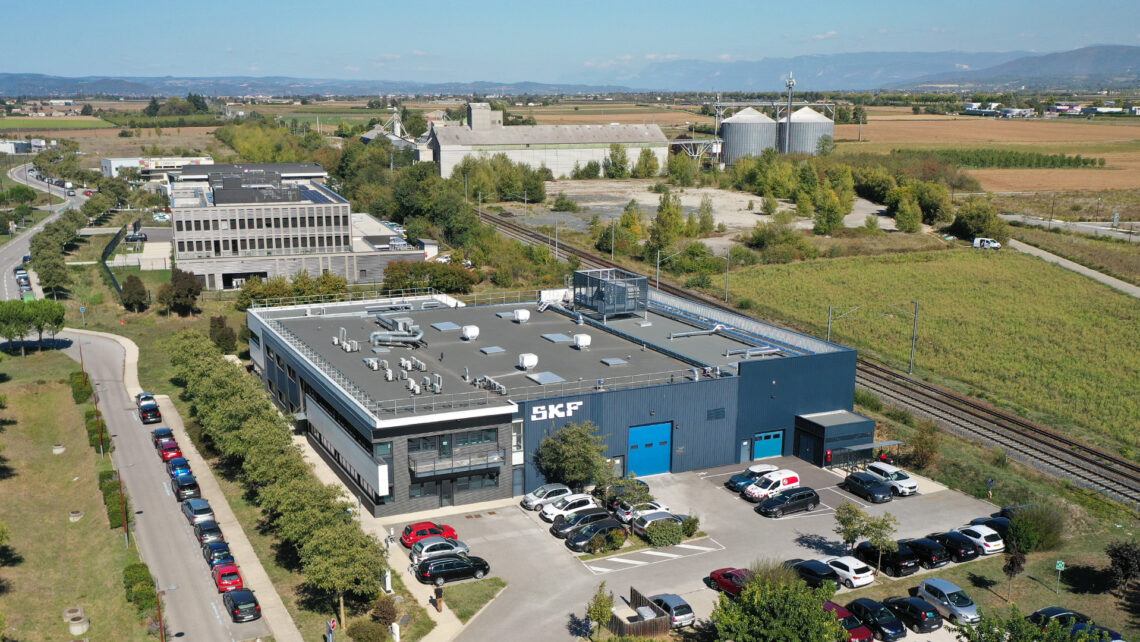
Ключевая партнерская роль SKF
Компания SKF вносит вклад в разработку аэрокосмических технологий нового поколения благодаря своему Центру аэрокосмических разработок с обновленным испытательным стендом в городе Валанс, Франция.
Многие проекты, над которыми мы работаем сегодня, будут реализованы в самолетах, построенных не ранее 2030-х годов
Ив Маэо, директор Центра аэрокосмического развития компании SKF
«Впервые мы располагаем стендом, оборудованным для проведения испытаний любых используемых в летательных аппаратах компонентов, — говорит Паоло Андольфи, руководитель аэрокосмического подразделения компании SKF, — будь то качение или скольжение, компоненты, вращающиеся с частотой несколько тысяч оборотов в минуту, или компоненты, которые вообще не двигаются».
Разработка аэрокосмической продукции — это длительный процесс с высоким уровнем совместной работы. «Срок разработки инновационных аэрокосмических технологий может составлять до 10 лет, — продолжает Ив Маэо, директор Центра аэрокосмических разработок. — Многие проекты, над которыми мы работаем сегодня, будут реализованы в самолетах, построенных не ранее 2030-х годов». В отличие от других отраслей, заказчики принимают участие в инновационных проектах с самых ранних этапов.
«Мы сотрудничаем с заказчиками на всех уровнях, — поясняет Маэо. — Наши заказчики делятся с нами своими технологическими планами, а мы предоставляем им свои. Инженеры заказчиков приезжают в Валанс, где вместе с нашими сотрудниками участвуют в испытаниях и разработке».
Такие тесные рабочие отношения помогают SKF глубже понять потребности заказчиков в реализуемых проектах. «Один из примеров — Textilub, новый самосмазывающийся текстильный композит, используемый в приводах летательных аппаратов, — поясняет Маэо. — У самолетов долгий срок службы, их детали неизбежно изнашиваются и требуют замены. Мы прилагаем множество усилий для того, чтобы такие компоненты функционировали как можно дольше. Общаясь с клиентами, мы выяснили, что детали с долгим сроком службы — это хорошо, но гораздо важнее равномерный и предсказуемый износ запчастей, позволяющий упростить управление ремонтом и заменой. Данные сведения мы использовали при разработке нового материала».
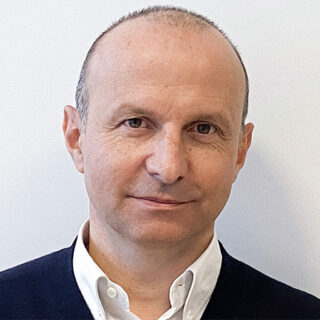
руководитель аэрокосмического подразделения компании SKF
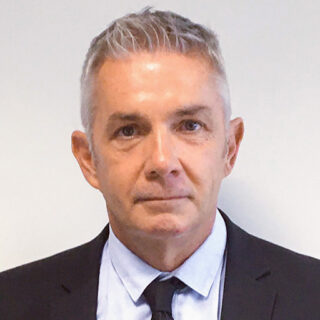
директор Центра аэрокосмического развития компании SKF
Высокотехнологичные гибридные композитные материалы
Другой областью повышенного исследовательского интереса в настоящее время является разработка подшипников для реактивных двигателей будущих поколений. Такие компоненты располагаются в центре современных самолетов и поддерживают быстро вращающийся ведущий вал в больших турбореактивных двигателях авиалайнеров.
В современных двигателях ведущий вал установлен на более, чем 10 подшипниках. А двигатели, конструкция которых включает коробку передач между вентилятором в передней части двигателя и компонентами компрессора за ним, требуют использовать дополнительные сильно нагруженные подшипники.
Возможности подшипников, устанавливаемых в двигатель, значительно влияют на эффективность его работы. Подшипники должны выдерживать высокие нагрузки, большую частоту вращения и надежно работать на протяжении всего срока службы в жестких условиях эксплуатации в среде с высокой температурой. Кроме того, при определении архитектуры конструкции нового двигателя инженеры должны найти пространство для подшипников.
В каждой новой конструкции нагрузки на подшипники возрастают, а конструкторы ищут способы более эффективного использования доступного пространства. Такое развитие приближает существующие конструкции и материалы подшипников к их физическому пределу.
По результатам недавно завершенного проекта, связанного с экспертизой SKF, был разработан новый материал, который привел к качественному изменению характеристик будущих подшипников для двигателей. Проект ARCTIC (Advanced Bearing Technologies to Increase Capabilities, «Передовые технологии подшипников для повышения эксплуатационных характеристик») финансировался совместным предприятием Clean Sky 2 Joint Undertaking, действующим в рамках программы Европейского Союза по исследованиям и инновациям Horizon 2020, при участии компании Rolls-Royce, которая выступила основным спонсором.
«В настоящее время в авиационных двигателях применяются высокопроизводительные подшипники гибридной конструкции, — говорит Александр Монделен, инженер по разработке продукции в SKF. — Такие подшипники включают керамические элементы качения и стальные кольца». В подобных конструкциях предельные значения характеристик подшипника определяются возможностью стального кольца справляться с высокими контактными напряжениями от жестких керамических шариков.
Задача проектов ARCTIC — создать новый стальной сплав, совместимый с керамическими поверхностями качения, который был бы способен выдерживать на 15 % большее контактное напряжение и на 25 % большую частоту вращения по сравнению с традиционными аэрокосмическими подшипниковыми сталями. Разработка такого материала с чистого листа — крайне сложная задача. Стали, применяемые в современных подшипниках двигателей, разработаны во второй половине XX века. «Исключительно необычно также и то, что разработка новой стали велась с учетом индивидуального применения», — добавляет Жан-Батист Кудер, инженер по технологии разработок в SKF.
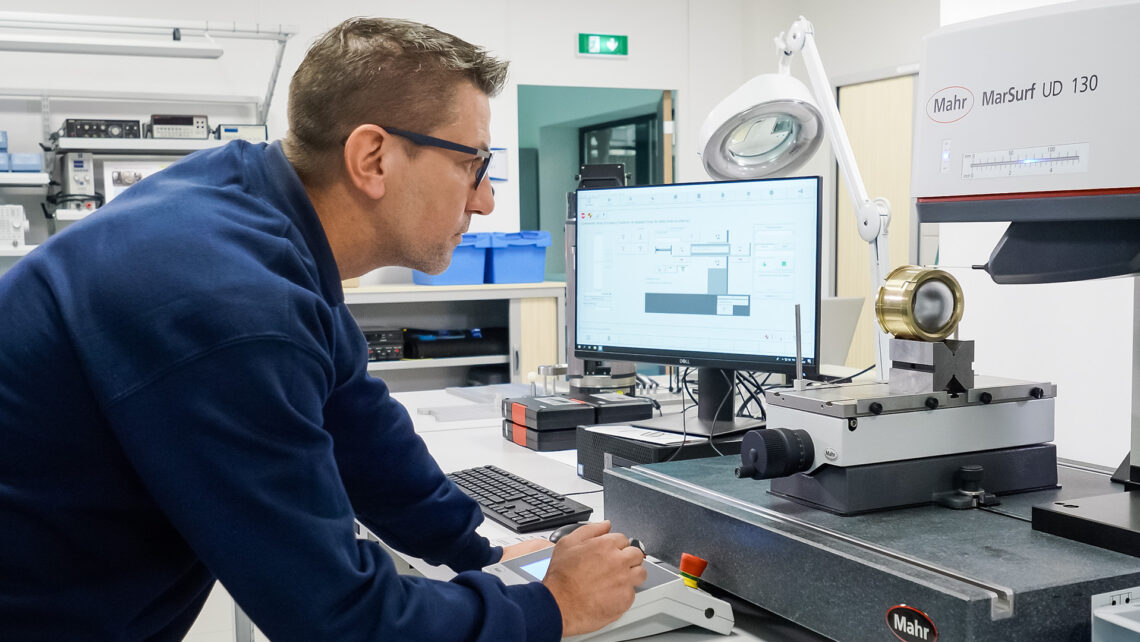
Новый сплав
В ходе разработки новой стали группа центра исследований и разработки SKF в Нидерландах использовала накопленные в течение десятилетий экспертные знания в сфере материаловедения и провела десятки испытаний прототипов с помощью собственного программного обеспечения для моделирования материалов Thermo-Calc. Специалисты разработали новый цикл термической обработки и представили экономичный промышленный способ производства материала и термической обработки. Затем Иву Маэо и его группе в Валансе потребовалось разработать новый высокоскоростной стенд высокой мощности для полномасштабных испытаний произведенных подшипников ведущего вала.
Результат — запатентованный сплав, который назвали ARCTIC15, соответствующий всем задачам проекта. Возможно, увеличение несущей способности на 15 % не выглядит убедительным, но это вызывает значительное улучшение рабочих характеристик двигателя. Гибридные подшипники, произведенные из новой стали, выдерживают нагрузку на 50 % больше по сравнению с подшипниками традиционной конструкции. Это позволяет использовать в двигателях подшипники меньшего размера и ведущий вал меньшего диаметра.
Применение данной технологии к текущей конструкции позволяет сократить потери мощности на 25 %, уменьшить объем систем смазки и охлаждения и непосредственно снизить вес. Дальнейшая оптимизация конструкции позволяет увеличить удельную мощность, что ведет к повышению топливной эффективности и уменьшению на 25–30 % выбросов углекислого газа и оксидов азота (цели, поставленные заказчиком).
В ходе испытаний материал ARCTIC15 продемонстрировал ряд дополнительных преимуществ. Материал долговечнее обычной стали, особенно в условиях недостаточной или некондиционной смазки. Кроме того, гибридные керамические подшипники из ARCTIC15 характеризуются меньшим уровнем вибрации по сравнению с обычными подшипниками, что улучшает общую производительность и надежность двигателя.
В настоящее время SKF сотрудничает с компанией Rolls-Royce в отношении промышленной реализации, следующей за испытаниями гибридных подшипников ARCTIC15 на прототипах производителя двигателей UltraFan® H2, в которых используется турбореактивный двухконтурный двигатель с приводом от редуктора следующего поколения, предназначенный для гражданских авиалайнеров.
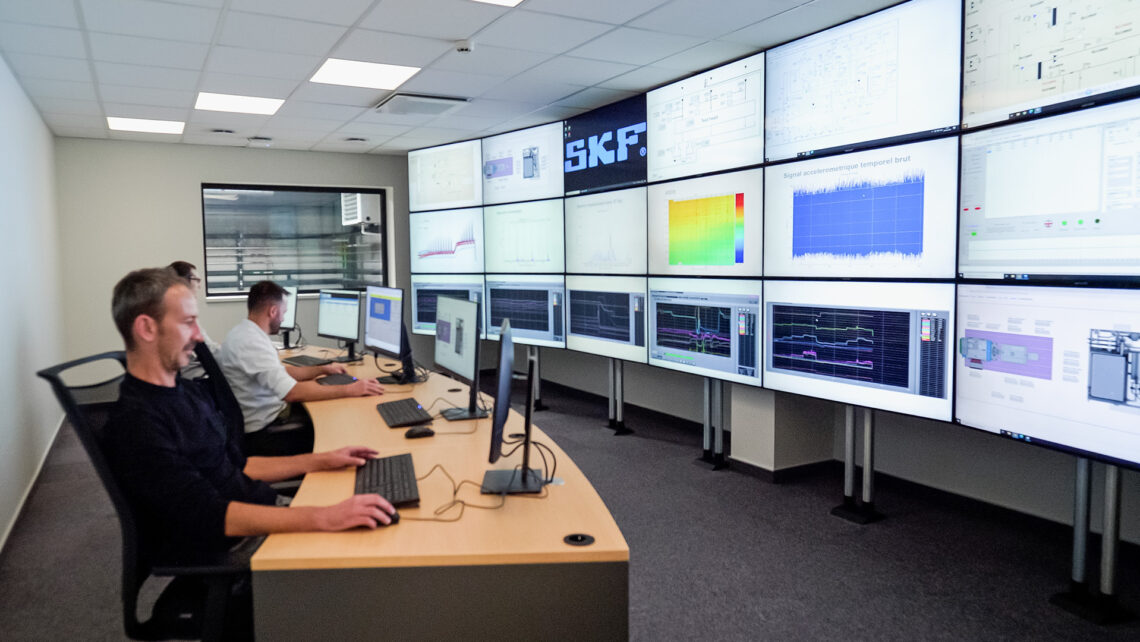
Количество авиапассажиров увеличивается
Отрасль авиаперевозок оказалась среди тех, кто сильнее всего пострадал от пандемии коронавируса в результате ограничений в передвижении. Соответственно, обрушился спрос на пассажирские рейсы. Сейчас, три года спустя после первых локдаунов, в большинстве стран сняты последние действующие ограничения. Даже в Китае, где были приняты наиболее строгие меры, в марте 2023 г. заявили о возврате допандемических правил в отношении виз для иностранных туристов и пассажиров, связанных с бизнесом.
Люди устремились в небо. В 2022 г. количество авиапассажиров возросло на 47 % по сравнению с предыдущим годом, а общая протяженность поездок увеличилась на 70 % благодаря тому, что снова стали популярными полеты на большие расстояния.