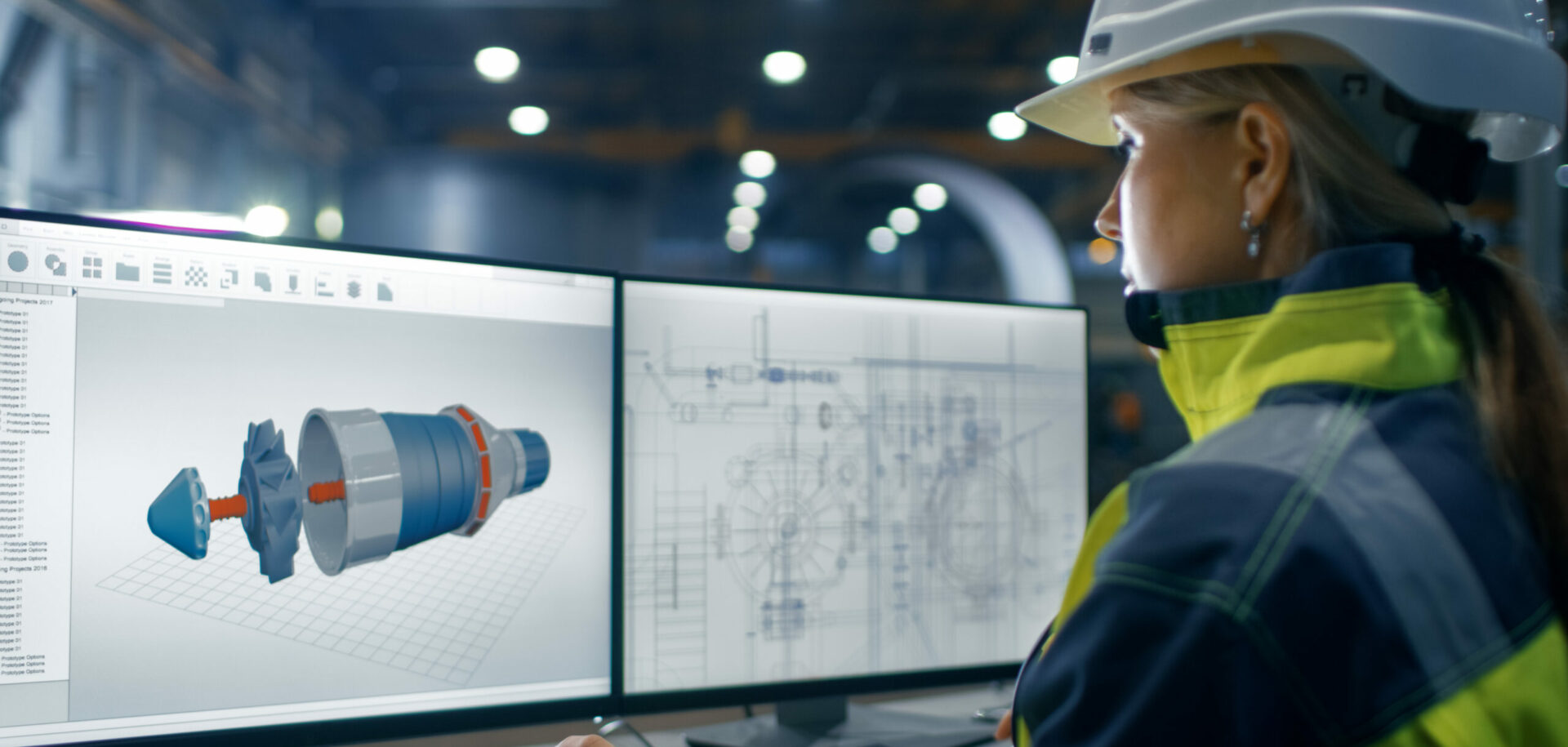
Series production of HBU 3 with ABS sensor
SKF has been producing hub bearing units for the automotive industry for almost 60 years.Following small improvements at the beginning, the trend to front wheel drive in the late 60s brought with it a decisive stage in development. In addition to demands for compactness, it was important to be able to satisfy the ever-increasing demands in respect of:
SKF has been producing hub bearing units for the automotive industry for almost 60 years.Following small improvements at the beginning, the trend to front wheel drive in the late 60s brought with it a decisive stage in development. In addition to demands for compactness, it was important to be able to satisfy the ever-increasing demands in respect of:
- service life
- stiffness
- shock resistance
- freedom from maintenance
- safety (anti-blocking of brakes) etc.
The hub bearing became a “system” and an integral part of the total wheel suspension (see figure 1). Since its introduction, the numbers of Hub Units fitted to cars are approximately:
- Hub Unit 1: 150 million
- Hub Unit 2: 50 million
- Hub Unit 3: 25 million
The more recent trend in the European automotive industry to reduce the manufacturing level by outsourcing, although not in itself new, has gained in priority because of heightened competition.
Development contract
In mid-1991, Adam Opel AG gave SKF the official contract to develop a Hub Unit for the rear axle of their J car. Better known as the Vectra, this car initially took over the bearing arrangement of its predecessor the Ascona without modification (similar to figure 2).
Besides the demand for appreciable total cost savings, the following conditions were specified:
- a bearing service life corresponding to at least 160,000 km
- freedom from maintenance for the life of the car
- ability to withstand constant operating temperatures of 125 °C
- optional sensor integration and the ability to maintain the signal voltage of 120 mV at 2.0 km/h, and 100 V at 280 km/h
- easy service
- a limit to the outside diameter in the vicinity of the brake to maximum 68 mm
- a hole pitch diameter for four-hole rims of 100 mm
- a flange width of 78 mm
It was also expected that prior to official vehicle tests, the functional viability would be proven by appropriate in-house testing at SKF. A time limit of two years was set out in the contract for the completion of the development work and of the preparations for series production.
In recent years, hub bearing units of the second generation have proved ideal for non-driven wheels. The rotating outer ring with its weight and strength-optimised flange replaces the conventional hub.
As a further step towards a complete “system”, an additional integration of the attachment flange with the inner ring (HBU 3) was considered. This would satisfy the demand for maximum component strength. However, initial studies showed that an appreciable part of the cost savings so far achieved would be eaten up by the relatively high production costs and the costs for mounting the sensor.
It was therefore decided that, in addition to calculation work, a practical comparison would be made of an HBU 3 with rotating outer ring (A) and one with rotating inner ring (B), see figure 3.
This direct comparison showed that there were no significant differences between the two versions. It was, therefore, decided together with Opel Engineering that further tests would be carried out on the more cost-favourable HBU 3 with rotating inner ring (see figure 4).
Sensor integration
Anti-blocking systems for brakes (ABS) make a considerable contribution to active vehicle safety. The most recent studies suggest that from the year 2000, all cars and light commercial vehicles will be fitted with ABS as standard.
By integrating ABS sensors into Hub Units, several advantages are gained, of which the most interesting for the vehicle manufacturer are the cost savings. These derive from:
- the unit concept
- simplified assembly
- the fact that signal verification is not required
- no machining is needed for sensor attachment
The integral ring sensor proposed by SKF acts as a passive ABS sensor according to the induction principle. An impulse ring with 29 teeth rotates past a permanent magnet which is positioned in a coil. As the wheel moves, an electric signal is induced in the coil; the frequency and amplitude of the signal depend on the rotational speed.
In contrast to the conventional sensors used today, the SKF arrangement offers the following additional technical benefits:
- improved rust protection
- savings in weight and space
- more robust because of the air gap between sensor and impulse ring
- a stronger signal (see figure 5)
The stronger signal means that the lower speed limit, which is usually 3.7 km/h, can be reduced to approximately 2.0 km/h. According to Opel, this means that vehicle safety will be further enhanced.
Temperature measurement
The operating temperatures which actually occur are of importance to the output signal and, of course, for the choice of the correct materials. Therefore, together with Opel, temperature measurements were made on an SKF-owned car on the Grossglockner. Under a maximum load corresponding to the permissible axle weight the following temperatures were recorded:
- on the outside of the ABS cover: maximum 115 to 120 °C
- on the outer ring between the ball rows: maximum 125 to 130 °C
This proved that the criteria laid down in the SKF specification are on the safe side, and that the Opel requirements are fully satisfied.
The bearing arrangement was optimised, both as regards load carrying capacity and stiffness, for the worst load case drum brakes and 900 kg axle load. This means, among other things, that for the assumed driving conditions of
- five percent left-hand and five percent right-hand curve taking with 0.25 g lateral acceleration
- 90 percent straight-ahead driving without lateral acceleration
- the calculated bearing life is approximately 300,000 km
Another decisive factor for operational performance is the bearing internal clearance in the unit on delivery, and also its possible change in service. As figure 6 shows, the optimum lies at a negative clearance (preload) of about 30 mm. By using the “loose inner ring” it was possible to reduce the preload tolerance to a maximum 35 mm. The danger of relative movement and consequent loss of preload is prevented partly by the tight fit of the inner ring and partly by the axial clamping of the joint by tensioning screws.
The operational reliability of the integral seal at the outboard side of the unit is also of great importance where bearing service life is concerned. The R-Safe seal has a stainless steel flinger which extends over the outer ring and prevents water and dirt from directly impinging on the sealing lip.
Naturally, all the parameters relevant to performance have been exhaustively rig tested and approved.
Series production
After the positive completion of vehicle tests at Opel, series production of the HBU 3E (with and without ABS sensor) was started in September 1993. In the meantime it has been decided to use SKF bearings also for the rear wheel bearing arrangements of the Astra. This means that in the final phase the annual production volume will be some two million units.
Outlook
Because of the ever-increasing demands on service life, stiffness, freedom from maintenance etc. as well as other requirements, which are just starting to come to the forefront in importance, such as reliability, weight saving, integration of additional functions and suitability for modular concepts, the trend to a higher degree of integration will become stronger. Thus, the Hub Unit 3 will play an increasingly important role in the various hub bearing arrangement concepts. Future activities will be expanded to a driven Hub Unit 3 with integral ABS sensor.
Georg Hochrein,
SKF GmbH,
Gunnar-Wester-Strasse 12,
D-97421 Schweinfurt,
Germany