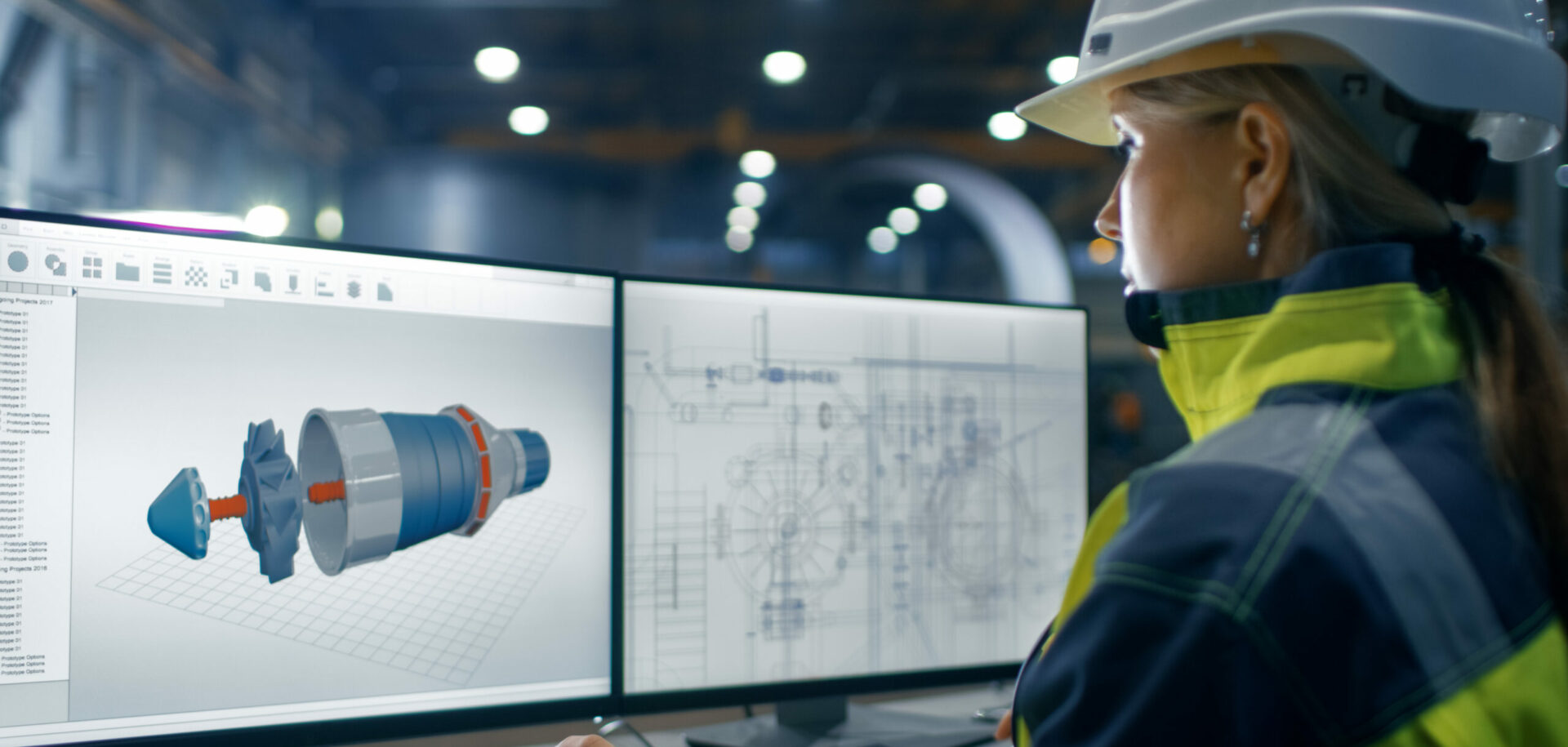
Slewing bearings break new ground
Recent developments at SKF have been able to increase slewing bearing life by around 400% using software-based analysis.By their very nature, slewing bearings have to accommodate very high specific roller loads, large misalignments and possible distortion factors created by axial and radial loads as well as tilting moments. Such bearings operate in harsh conditions – dirty, corrosive environments with heavy loads and short life expectancy.
Typically slewing bearings are used in heavy engineering applications in the construction, offshore, defence and marine industries. Often the bearings are of a considerable size, and any unscheduled maintenance, repair or replacement in the field because of bearing problems can be not only inconvenient but also very costly.
In particular, a tunnel boring toolhead is one of the most arduous applications for slewing bearings supplied by SKF, and it demonstrates the importance of having the capability for specialist solutions. This includes the development of new software to help RKS design engineers select the most appropriate slewing bearing for a particular application. It can also help during initial calculations relating to raceway, bolting and gear selection.
The initial design criteria have a major influence on bearing performance and functional lifespan. Slewing bearings are usually mounted on frames that are less rigid than shafts and housings used for conventional cylindrical and taper roller bearings. This can have an impact on operating life.
SKF has been able to increase slewing bearing life by around 400% using its “logarithmic” profile. This derives from the mathematical expression for the stresses in the roller/raceway contact zone. These stresses are an important factor in determining bearing life and improving load-carrying capacity through more favourable load distribution. They also prevent the creation of edge stress peaks at the end of the bearing rollers.
By applying SKF theory on the relation between profile and bearing life, it has been possible to establish and optimise specific profiles for SKF slewing bearings. Although logarithmic, they differ from those used in conventional roller bearings. They take into account the very high specific roller loads in combination with the large misalignments, which are characteristic of slewing bearings. With a misalignment of 0.23º, the reduction of the highest Hertzian pressure is about 12% compared with a standard logarithmic profile.
In tunnel boring machines, each slewing bearing is specially made. This means that specific technical designs and calculation data sheets are made for each project. Normally, the range of slewing bearings used on tunnel boring machines is between 2.5 and 6 m in outer diameter, although larger diameters can be produced if required.
In addition to tunnel boring machine applications, SKF offers a wide range of slewing bearing designs to meet other heavy engineering applications. This includes four-point contact ball bearings, double row angular contact ball bearings and single or double row crossed roller bearings.
Maryse Perdu,
SKF RKS S.A., Avallon, France