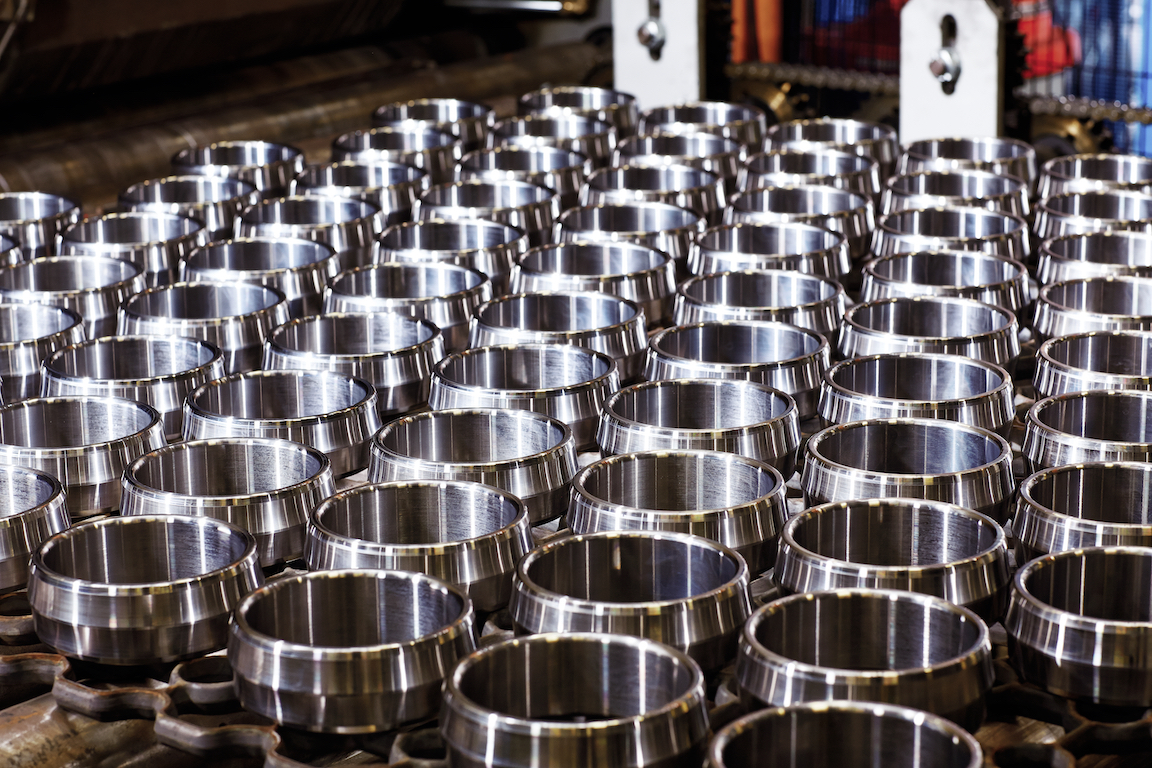
Spanning the Future
Thirty years ago, G&G Steel was a small firm with seven employees. Today it employs more than 100 workers and is one of the largest steel fabricators in the United States. The firm brought that experience to bear when it recently completed work on a state-of-the-art bridge in one of the world’s busiest cities.
Summary
Bearing the brunt
The SKF bearing at the centre of the new Third Avenue Bridge in New York City has two claims to fame.
First, it is the largest bearing ever to be used in a swing bridge. Second, it is the first time SKF has used its special NoWear coating on a bearing in a bridge.
NoWear is often used where there is limited ability to lubricate a surface. The NoWear coating, which has undergone extensive development at SKF, provides a low-friction, ceramic coating that prevents micro welding and preserves surface integrity.
“The bridge moves at a low speed,” says Gill Detweiler, SKF senior applications engineer. “Normally, rollers ‘aquaplane’ on a hydrodynamic oil film. But here it’s metal to metal contact, so NoWear will help.”
The weight of the bridge rests on this single bearing in the centre. The bearing enables the bridge to rotate horizontally about one pivot point in the middle of the river.
“It is balanced like a see-saw, but it pivots flat on its own flat plane,” says Detweiler.
Normally, bearings for swing bridges don’t have rollers, but this one does. The NoWear coating will protect the rolling surfaces and make them last longer. The rolling function was requested as a hazard and security measure, to protect against things such as earthquakes or bombs.
“This is New York,” explains Detweiler.
The spherical roller thrust bearing also has a high contact angle for added safety.
Detweiler says the New York City Department of Transportation had a “wonderful reaction” to SKF’s proposals. In addition, SKF expects to be retained to do periodic checks on the bridge.
“SKF has a special way of looking at the vibrations of a bearing as it rotates,” Detweiler adds.
“We can measure vibrations and evaluate the condition of the bearing roller surfaces.”
Thirty years ago, G&G Steel was a small firm with seven employees. Today it employs more than 100 workers and is one of the largest steel fabricators in the United States. The firm brought that experience to bear when it recently completed work on a state-of-the-art bridge in one of the world’s busiest cities.
Bret Gist only has to gothrough one traffic light to get to his job in Russellville, Alabama. While his morning commute in this rural town of 10,000 people is simple, his business is not.
Gist and his family own G&G Steel, a fabrication and manufacturing company that’s just completed work on a sophisticated new bridge for one of the world’s busiest cities. The Third Avenue Bridge spans New York City’s Harlem River, a 13-kilometre tidal straight that separates the city from the boroughs of the Bronx and Queens.
There are 14 bridges crossing the Harlem River. All of them can open up to let ships pass through, but the Third Avenue Bridge is special: When it opens, it swings.
Engineering enthusiasts admire swing bridges such as the Third Avenue Bridge because of their unique design. Imagine a bicycle tyre lying on its side: The bridge has an axle in the middle of its span. The axle, placed in the middle of the river, will rotate just like the bicycle tyre – only horizontally – so it can swing open. The bridge carries five lanes of traffic, and more than 70,000 cars cross it every day.
One of the largeststeel fabricators in the United States, G&G Steel has a history of doing jobs for the United States Army Corps of Engineers, including working on locks and dam gates. It has also done extensive work for steel mills, aluminium mills and concrete industries. G&G Steel has been in business since 1974, when Gist’s father, Danny, started the firm with just seven employees. Today the company has 140 workers and a 28,000-square-metre facility.
“We’ve handled large movable systems, so we were well suited for this bridge, rather than working on a fixed-span bridge,” says Gist. He says the company plans on doing further work with heavy, movable systems and especially wants to tackle more bridge projects.
In the Third Avenue Bridge, the entire 2,700 tonnes of the bridge will rest on a single spherical roller thrust bearing situated at its centre, which was designed and manufactured by SKF.
“This bearing type has been used for swing bridges, but my understanding is that it is the largest one that’s been used so far,” says John Gimblette, senior project engineer for the bridge’s design firm, Hardesty and Hanover in New York.
“We made the components that married the bearing to the bridge,” says Gist. “We have the expertise and highly skilled workers. It’s very critical to be well versed and well trained on how this machinery has to go together.”
Hiring an all-in-one firmsuch as G&G Steel made things easier for the New York City Department of Transportation, which oversees the city’s bridges.
G&G Steel produced the drawings for the bridge and began manufacturing the 111-metre-long structure in 2002. Because of its extensive capabilities, it was also brought in on the mechanical side of the project.
“We were able to fabricate it and assemble it,” says Gist. “Having complete capabilities made us a great fit for the mechanical side of the project as well.”
Those mechanical aspects were no small matter.
The last time the bridge was replaced was in 1898. So it was more than 100 years later when the new bridge was installed, following months of collaboration and innovation.
The old structure, says Gimblette, was a rim-bearing bridge, so its load went down to multiple wheel assemblies that rode on a circular track. The new bridge is based on the centre pivot, meaning that the bearing takes the majority of the load.
Gimblette says that while the new bridge was designed from scratch, the truss built by G&G Steel was designed to look like the old one. “So, when you view it from afar, it will share some of the same elements; it keeps some of that old world charm and is aesthetically the same,” he says.
Once the bridge was completed,G&G Steel shipped the swing span truss to Mobile, Alabama, loaded it on a barge and floated it around the Florida panhandle and up the Atlantic Coast to New York. After its 2,900-kilometre journey, the structure was transferred to two river barges and moored south of the old bridge. Work on the electrical and mechanical systems, the control house and the roadway grating continued. The bearing, meanwhile, was installed in G&G Steel’s Russellville facility, then brought to Manhattan. It was floated into the middle of the river and put on top of a pedestal. The new truss was then brought in on barges and floated over the pedestal. The barges were sunk into the river to lower the truss onto the pedestal.
“The SKF bearing was a very important part of the job,” says Gist. He points out that SKF is not new to the company, since G&G Steel’s sister company, Franklin Manufacturing has used SKF’s bearings in other projects for many years. The bearing also features SKF’s NoWear coating, which protects the rolling surfaces to greatly increase bearing service life.
“The NoWear coating is what sold the engineers on having SKF be the ones to manufacture this bearing,” Gist says.
G&G Steel is currently working on another bridge project in Manhattan – the 145th Street Bridge; the company has been hired to fabricate, assemble and test all the mechanical aspects.
“The Third Avenue Bridge has opened up a different avenue for us,” Gist says.
FACTS
The SKF spherical roller thrust bearing has a 900 mm bore diameter and 1,520 mm outside diameter. The bearing has a NoWear coating to enable a service life of 50 to 100 years. The outer ring is supported by a housing that looks like a salad bowl and is roughly 2 metres in diameter.