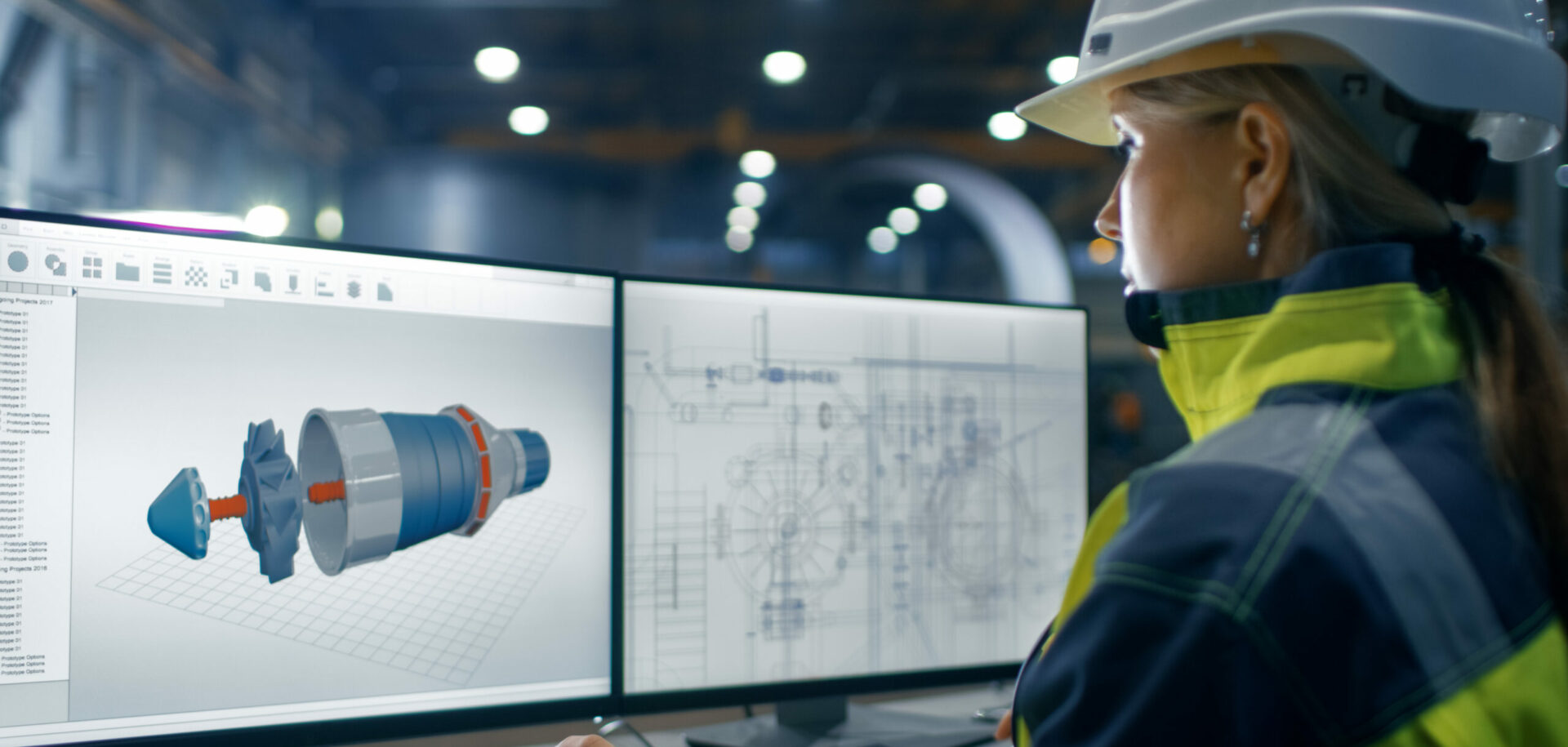
Stathis Ioannides – devoted to the fight against friction
The term “tribology” comes from the Greek words tribos (“rub”) and logos (“principle”), so it is perhaps fitting that one of the world’s leading experts in the field should hail from the Hellenic Republic.
Facts
AGE: 67
EDUCATION: An MSc in Mechanical and Electrical Engineering from the Technical University of Athens, an MSc and a PhD in Applied Mechanics from Imperial College of Science, Technology and Medicine in London, England
FAMILY: Married, one son
LIVES: London, England.
The term “tribology” comes from the Greek words tribos (“rub”) and logos (“principle”), so it is perhaps fitting that one of the world’s leading experts in the field should hail from the Hellenic Republic.
Stathis Ioannides was born in Athens, but moved to London in the swinging 1960s to study at the Imperial College of Science, Technology and Medicine. “Engineering was a tradition in the family,” Ioannides explains. “My father had an engineering consultancy firm in Athens, and as a child I spent a lot of time taking mechanical toys apart to see how they worked, so engineering was a fairly natural choice.”
After completing his studies, Ioannides went on to become an internationally acclaimed expert in the field of tribology, the science of rubbing surfaces. In December 2008, he was awarded the highest honour in the industry – the Gold Medal from the Tribology Trust, administered by the United Kingdom Institution of Mechanical Engineers – in recognition of his achievements in tribology, and in particular his work in the field of rolling bearings. It was presented to him by HRH Prince Philip, Duke of Edinburgh, at a ceremony at Buckingham Palace, London, in June 2009.
“I think my fascination with bearings comes from the fact that from a distance, they look like very simple components,” Ioannides explains. “They have been optimized over 100 years of use, and so further development and optimization requires expert knowledge of quite a number of scientific and technological discip-lines such as material science, lubrication and fluid mechanics. We’re now at a point where many disciplines have to come together to produce the answers we are looking for, and that’s quite a technological challenge.”
Indeed, Ioannides roseto that challenge when he developed a theory for rolling contact fatigue, which was met with international acclaim when it was published in 1984. Ioannides showed that the calculations for establishing bearing life had not kept up with the rolling bearing development and offered a new way to calculate bearing life that gave a much more accurate result. As a consequence, he demonstrated that bearings most often were being overdesigned and that smaller bearings could be used and still meet the demands of an application, offering considerable savings in all areas. “This method subsequently became the ISO standard for the calculation of bearing life, which was quite an achievement,” he says.
Ioannides joined SKF in the Netherlands in 1981 as a senior engineer and became product R&D director in 1995. In tandem, he has been a visiting professor at the Imperial College since 1986. “The two institutions have kept me at the forefront of tribological research, which has been absolutely fascinating and hugely rewarding,” Ioannides says. “I consider myself very lucky.”
In 2005, Ioannidesbecame the coordinator for the SKF “Green Bearings” project, funded by the European Commission in Brussels, as part of the LIFE programme, which supports environmental and nature conservation projects. The project was proposed to develop more energy-efficient rolling bearings, and the SKF team came up with two new bearing families offering at least 30 percent lower frictional moment than standard bearings. As well as tapered roller and deep groove ball bearings, the new E2 Energy Efficient approach also included a new way to calculate and optimize the design of slewing bearings for blade pos-itioning in wind turbine applications. More recently, the E2 Energy Efficient concept was extended to spherical and cylindrical roller bearings.
“There is a very interesting duality in these new E2 bearings,” Ioannides explains. “They benefit the customer because life-cycle costs are lower, but they also benefit the environment because the energy required over time to rotate them is also lower. There are more than 50 billion bearings operating in the world at any time, and they are the second most widespread machine element after nuts and bolts, so one can
imagine the potential for energy savings.”
Indeed, protecting the environmentand encouraging energy efficiency are primary drivers for research in the bearing world. Others include lowering costs, improving performance and expanding operating cap-abilities to accommodate particularly difficult applications where special solutions are required. “There is also an increasing interest in applying tribological know-ledge to micro- and nano-technology,” Ioannides says, “because at this level the relative importance of friction increases compared with inertia forces, and the effects can be quite different on these very small scales.”
Mechatronics, or the combination of electronics and mechanical components, especially when combined with artificial intelligence, is another key research area for rolling bearings. “If you can instrument a bearing so that it can tell you the temperature and loads under which it has been running, you have a better possibility of relubricating when necessary, rather than automatically, and you can plan out the machine servicing with less disruption,” he says. “You open the world to much more efficient use of the machinery you have around you.”
On the eve of his retirement, Ioannides is happy that the world is starting to realize the importance of tribology and how its theories can be applied to such a wide range of applications. “A recent Chinese academic delegation to the UK presented an ‘Investigation on the Present Situation of Tribological Applications and Research on the Development Strategy of Tribology in China [Jan 2006 – Oct 2007]’,” he says. “This indicates potential savings of 1.55 percent of GNP in China by the thorough application of tribology in industry. That’s a great deal of money even if only half of it is realized!”