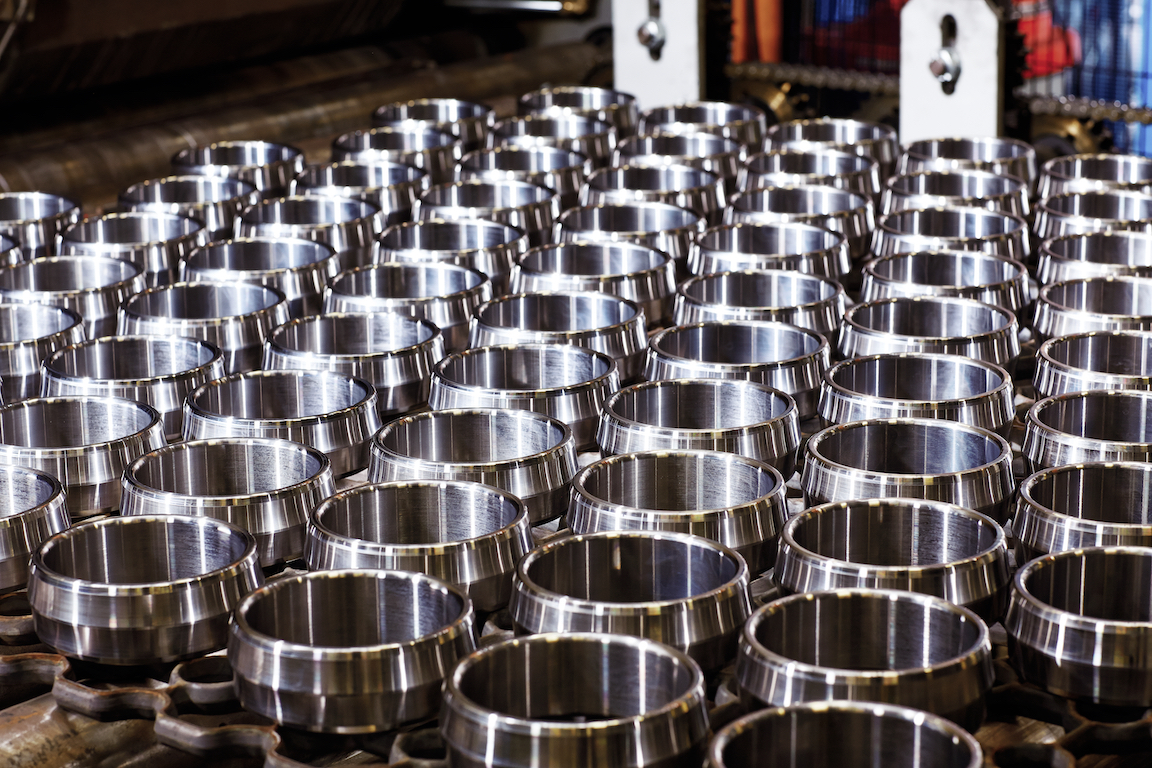
Summary
A system solution
Earlier, when Stahlwerke Bremen replaced bearings in its continuous caster, it threw the used ones away. Nowadays, it sends the bearings to SKF Industrial Services Centre, where they are inspected, cleaned, and – when still usable – reconditioned and returned.
This arrangement has advantages for both companies. “We can see where the problems are in the machine and look for solutions,” says SKF application engineer Jens Bode.
For Stahlwerke Bremen, a leading user of SKF applications and solutions, the service cuts overall maintenance costs by reducing the number of bearings in inventory and by allowing 50 percent of the old bearings to be reused. The customer also gets a detailed bearing inspection report from SKF, allowing to optimise the different bearing systems.
Bode explains that not all casters are alike when it comes to trying out new bearing solutions. Improving efficiency of a bad caster is easy, but with a caster like Stahlwerke Bremen’s, which already operates to a high standard, the process is more challenging.
Depending on where the bearings are located in the caster, Stahlwerke Bremen uses sealed CARB® bearings, CARB bearings sealed on one side only, or sealed spherical roller bearings – all from SKF. Each of these arrangements has cut costs, reduced maintenance and lowered grease usage.
In this respect, the system solution with a spherical roller bearing in the locating position of a roller, and CARB in the non–locating position, is of particular importance.
The CARB bearing in particular offers the caster some very special advantages, including higher load–carrying capacity, misalignment capability and axial displacement capability.
“It is very important to have a partner like Thomas Groth,” says Bode, noting that Stahlwerke Bremen’s maintenance manager is continually testing new applications and trying improvements. “We learn together,” he adds. “Both of us get something out of this.”
For German steelmaker Stahlwerke Bremen, continuous casting is a core process. That’s why the company gives it continuous attention.To the casual observer, they look like two rivers of red–hot lava, moving slowly and steadily across a darkened landscape. But to professionals in the steel industry, these glowing parallel strands represent the metamorphosis of molten steel into something more valuable – hardened steel slabs.
The machine that performs this transformation is no volcano, but a continuous caster. However, with a height of 12 metres and a length of 33 metres, its bulk and dimensions are still impressive.
On a typical day at northern Germany’s Stahlwerke Bremen GmbH, the continuous caster is operating – as its name implies – continuously. That means 24 hours a day, seven days a week, in inferno–like heat, accompanied by water and grime.
Running at full capacity, the continuous caster at Stahlwerke Bremen produces an average of 465 tonnes of crude steel per hour. In simple terms, the process works like this: molten steel at a temperature of more than 1,500 degrees Celsius is poured into one end of the water–cooled machine. In about half an hour, or less time than it takes to bake a cake, it emerges from the opposite end as solid slabs of steel at a relatively chilly 900 degrees.
This process of continuous casting with controlled water cooling enables Stahlwerke Bremen to manufacture steel slabs with a flawless surface and a consistent interior composition – attributes necessary to the production of high–quality steel.
Thomas Groth, who has worked for nine years as maintenance manager for the continuous caster, says he is always looking for new ways to increase the machine’s efficiency. He believes this can be done by increasing the life span of the caster’s components, cutting costs and reducing grease consumption, which also has added benefits for the environment.
In 1999, Stahlwerke Bremen completed a project to rebuild and modernise the continuous caster. The goal was to improve the quality of the steel slabs it produced, while increasing the machine’s performance and output.
The continuous caster at Stahlwerke Bremen consists of 24 separate segments, which use a total of 3,000 bearings. One segment alone can contain between 40 and 320 bearings, depending on its size and location.
For many of these bearings, contamination from water and scale is the main threat to performance. “In these cases,” says Groth, “we are not using grease for lubrication, but rather for sealing the bearing.”
Other complications result from the high heat of the casting strand and the ferrostatic pressure, in which the still–molten core presses against the solidifying outer shell of the casting strand and, in turn, the machine’s slow–moving guide rollers.
“Every six to eight weeks, the continuous caster undergoes a planned eight–hour shutdown for routine maintenance,” says Groth.
The problem is that the bearings cannot be worked on or repaired while they are still in the machine.
“The entire segment must be removed from the machine and replaced with another,” he says. Since it takes two to four hours just to change segments, Groth strives to minimise surprise interruptions.
can cost over 100,000 German marks (USD 54,000) in lost production,” he says. To guard against this, when a segment is serviced, all of its bearings are changed whether they need to be or not.
Stahlwerke Bremen, located just north of Bremen near the Weser River, is one of Europe’s most efficient steel mills. In business since 1957, the mill produces more than 3 million tonnes of high–quality steel annually, dealing exclusively in hot–rolled, cold–rolled and surface–treated flat steel products.
Since 1994, Stahlwerke Bremen has been a core member of the flat steel sector of the worldwide ARBED Group, a Luxembourg–based organisation with a tradition of steel production that spans more than 100 years.
Employing about 5,000 people, Stahl–werke Bremen is a fully integrated metallurgical plant. This means all production facilities – from the melting of iron ore to the processing of thin sheet metal – are located on the same grounds, which cover about seven square kilometres.
With 1998 sales of more than DEM 2 billion (USD 1.08 billion), the company has a global market, although most of its products are sold in Germany and elsewhere in Europe. The company’s clients are mainly in the automotive industry, but also include businesses ranging from steel drum manufacturers to makers of electrical appliances and computer housing.
A demanding journey
The continuous caster is basically automatic, with only three people needed to monitor the entire production process. A ladle feeds molten steel into the machine, where it first passes a vertically oscillating mould 900 millimetres in length and allows for variable casting widths of up to 2,670 millimetres. The mould has water–cooled walls, so in the 30 seconds needed for the steel to pass through it, the casting strand develops a hardened outer shell 15 millimetres thick.
Special combinations of upper and lower guide rollers are used next to steer the casting strand through a 90–degree curve and into a cooling chamber, where the surface of the solidifying steel is sprayed with water. The higher the temperature, the more wear on the rollers, so they too are cooled with water internally.
Guide rollers continue directing the casting strand through the machine until it finally ends its journey in a horizontal position as solid steel. The strand is then cut into individual slabs to customer–specified lengths and allowed to cool to room temperature.
Andreas Kröker–Buhé, manager of the continuous caster, points out that, whereas other steel mills will typically have two or three casting machines, Stahlwerke Bremen has only one. This explains the company’s continued emphasis on efficiency and performance.
“The machine has to run a lot,” Kröker–Buhé says matter of factly. He adds that, operating at full capacity, his caster runs, on average, 98 percent of the time, with only 2 percent downtime spent on repairs.
Another notable achievement, he says, is that Stahlwerke Bremen holds the record for completing the most uninterrupted castings in a single month. The mill turned out 1,150 castings, with the machine’s two casting strands running simultaneously 95 percent of the time.
A long process
Because of the unique nature of the continuous caster at Stahlwerke Bremen, its overall performance and its tight maintenance standards, it can take a long time to test new solutions in the machine.
“A segment must break down three times before I am able to install a new bearing solution,” explains Groth, adding that this adds months to the process. “When everything goes successfully, we’re still talking about a period of two years passing before we know the results of a test.”
Since he began making improvements to the caster in 1995, Groth has increased performance by up to 50 percent in various segments of the machine. In some segments, by switching to sealed bearings, he has also eliminated grease consumption completely.
Groth puts these figures into perspective, saying, “There will always be intermediate results, but no end results.” The innovation process, then, works much like the caster itself – continuously.
Kathleen Saal
a business journalist based in Munich
photos Stahlwerke Bremen