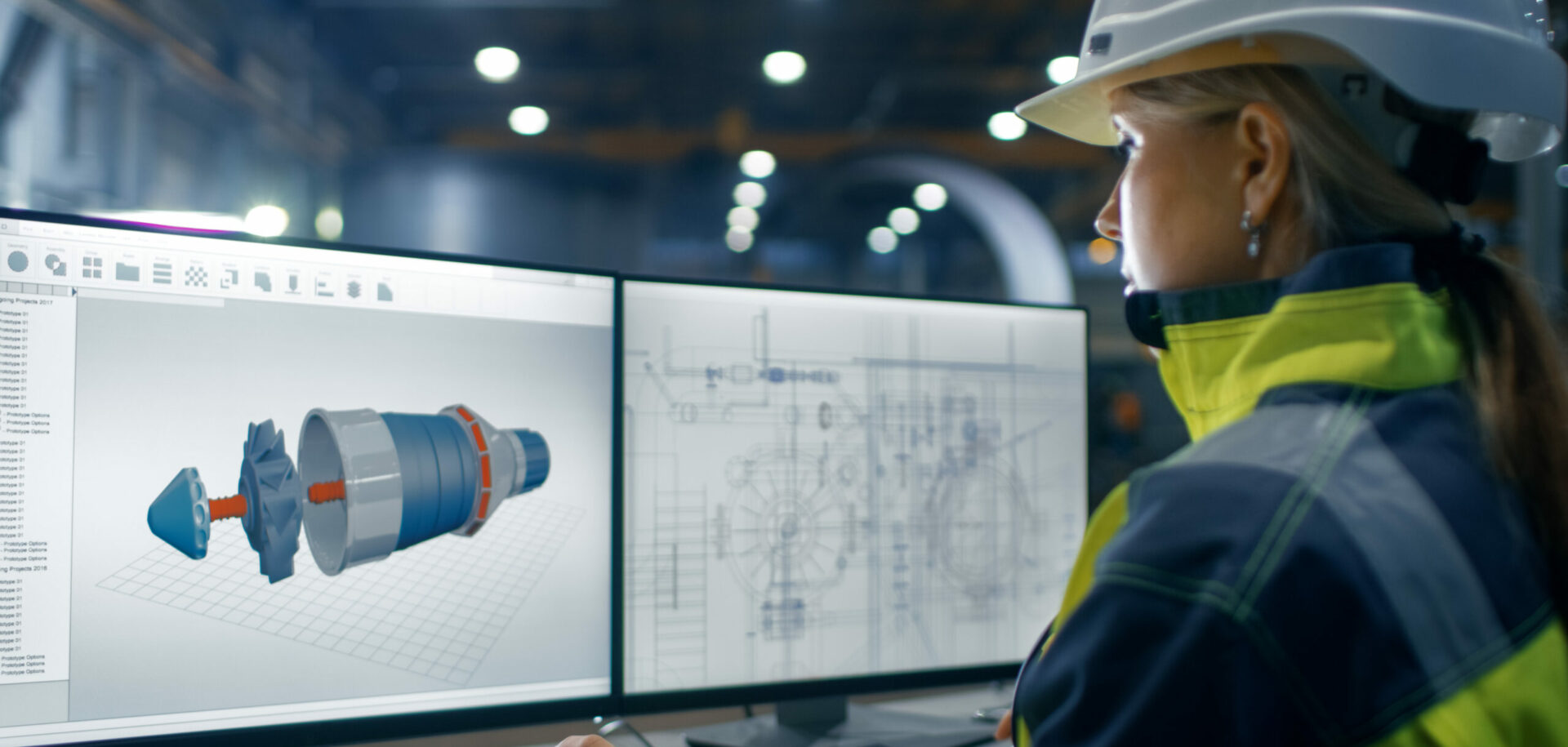
Steering new course with sensors
A reduction in maintenance costs is achieved, for example, by lowering overall energy consumption of the industrial truck. For steering, electric systems have far lower energy consumption in comparison to hydraulic steering systems. Up to 60 % savings on the steering system are possible with electric as compared to hydraulic alternatives (fig. 1). Electric steering systems are used for industrial trucks which are optimised for efficiency.
Material flow within plants continues to be an important area for company rationalization. The euphoria over automation has given way to the realization that conventional industrial trucks are the most economic and flexible solution for the majority of in-plant material flow tasks.Further rationalisation is now being achieved by making industrial truck designs more cost effective. Cost-effectiveness can be improved not just by lower initial procurement and maintenance costs but also by increasing material-
handling performance.
A reduction in maintenance costs is achieved, for example, by lowering overall energy consumption of the industrial truck. For steering, electric systems have far lower energy consumption in comparison to hydraulic steering systems. Up to 60 % savings on the steering system are possible with electric as compared to hydraulic alternatives (fig. 1). Electric steering systems are used for industrial trucks which are optimised for efficiency.
A major aspect in increasing material-handling performance is the ergonomic design of the driver’s workplace. This creates a fatigue-free working environment and consequently raises performance levels.
The design and position of the steering mechanism, coupled with the design of the controls, play a key role in determining the ergonomic layout of the driver’s workplace. This design philosophy was applied to the steering mechanism of a new high rack stacker (fig. 2) developed by Jungheinrich AG in Germany.
Ergonomics
To fulfil the ergonomic requirements for the steering mechanism while still providing a flexible design solution, five factors must be considered:
- manual force
- shape of steering wheel
- steering reduction ratio
- steering wheel position
- legroom
All these design factors need to be optimised. It was found that fully electric steering offered the greatest optimisation potential.
Fully electric steering offers the greatest degrees of freedom in relation to the design of steering forces and reduction ratios, as these two variables are independent of each other. The shapes and positions of steering wheels can be freely selected according to ergonomic requirements. The conventional round steering wheel is found to be the most appropriate type in high rack stackers.
Steering wheel assembly
Legroom influences the well-being of the driver, but is only indirectly linked to the steering function. However, legroom is directly involved in the design of the steering system. If steering assistance systems are used, a steering column is positioned close to the driver’s knees, which leads to restrictions in legroom.
With fully electric steering, however, the steering requirement is detected by sensors, which supply a steering-angle setpoint signal to an electronic control unit.This unit calculates the necessary actuator travel for the wheel to be turned and actuates a steering motor accordingly. This steering system concept eliminates the need for a steering column and consequently improves legroom.
To maximise legroom, the sensor electronics should be fitted to the steering shaft and its bearing assembly in such a way that maximum space saving is achieved.
The steering wheel bearing assembly is subject to some design considerations. Forces induced by the driver, for example when he grabs the steering wheel on entering the cab, have to be capable of being absorbed by the steering wheel bearing assembly. This results in the need to design a sturdy bearing assembly, which takes up a large amount of space.
In addition, the sensor electronics which detects the steering wheel movement has to meet statutory provisions. For safety reasons, it is better to use two sensors providing identical signals. These signals are compared electronically, and any deviation between the two can be compared and evaluated. Should either sensor malfunction, the steering system is still able to function properly because of the redundancy in the design.
Some commercially available sensor electronics only have restricted redundancy and cannot maintain the required safety margin. Should the sensor fail, the vehicle is no longer operable (example: the use of a tachogenerator and an inductive proximity switch). This disadvantage of restricted redundancy has a direct impact on the availability of the industrial truck.
Design
Commercially available sensors are unsuitable because of the costly flanging and the sometimes considerable space requirements. This is particularly true if a robust steering wheel bearing assembly and the more sophisticated sensor electronics are to be combined in as space-saving and inexpensive a way as possible.
New avenues were therefore explored in designing the sensor electronics to detect steering wheel movement for the latest generation of the Retrak high rack stacker from Jungheinrich.
After extensive technology searches, it was found that integrating the sensor electronics into the bearing units would meet all stated requirements. The sensorised bearing was designed in co-operation with SKF for use in a steering wheel bearing assembly.
As two independent sensors are necessary to fulfil the statutory safety provisions, both deep groove ball bearings used in the steering wheel bearing assembly are equipped as sensorised bearings (fig. 3).
Assessment
The fully electric steering used in the new generation of Retrak high rack stackers has two sensorised bearings fitted to the steering wheel to detect its rotation. As a result, considerable mechanical effort can be saved. The omission of the steering wheel column means that there is no mechanical connection to the wheel to be steered. This allows for more freedom of layout for ergonomic optimisation, and the driver’s legroom is not restricted (fig. 4).
The benefits of this solution for a steering wheel bearing assembly are:
- sturdy construction
- easy assembly
- substantial reduction in space requirement
- increased functionality
- cost reduction
Conclusion
The trend towards optimising the functions of industrial trucks will persist. New technologies not yet employed in industrial trucks will permit higher performance with improved characteristics. The increased sophistication of electrical and electronic components will make possible further improvements in operating behaviour and create greater scope for designing ergonomic operator interfaces.
Efficient and inexpensive sensors make possible optimised reactions to the actual conditions experienced by the industrial truck and therefore better operating characteristics.
The sensorised bearing is a successful example of the trend towards creating inexpensive solutions with increased functionality by integrating different functions into a single component.
The challenge for the future lies in identifying further opportunities for integration. It is only in this way that the increased market pressure on costs and the improvements in performance and functionality of industrial trucks demanded by customers can be successfully and convincingly reconciled in new generations of industrial trucks.
Sensorised bearings
The sensorised bearing combines the functions of a rolling bearing with an incremental sensor. Developed by SKF in the late 1980s, this component allows the measurement of position, speed, speed variation and direction of rotation yet is compact, maintenance-free and ready-to-mount.
Based on the well-established deep groove ball bearing technology, the sensorised version has an impulse ring fitted to the inner ring and a sensor ring at the outer ring. The sensor uses the Hall effect which is the deflection of current flow in a conductor as the result of the application of a magnetic field. This leads to an electric potential gradient transverse to the direction of current flow.
The impulse ring is divided radially into magnetic segments, the number of which depends on the bearing size (typically 32 or 64 pairs of poles). The Hall probes incorporated in the sensor ring are offset 90° in phase which allows the detection of the direction of rotation. The rotational movement of the inner ring is detected by means of the variation in the magnetic field.
Shielding was an important aspect of the bearing design to prevent interference from external magnetic fields. Even the output cable that delivers the signal was chosen with this criterion in mind.
The sensorised bearing was subjected to extensive testing and fulfils the requirements of the European standard EN 50082-2: 1995. It also qualifies for the CE approval mark.
Axel Krause and Hans-Joachim Doss,
Jungheinrich AG
Norderstedt, Germany