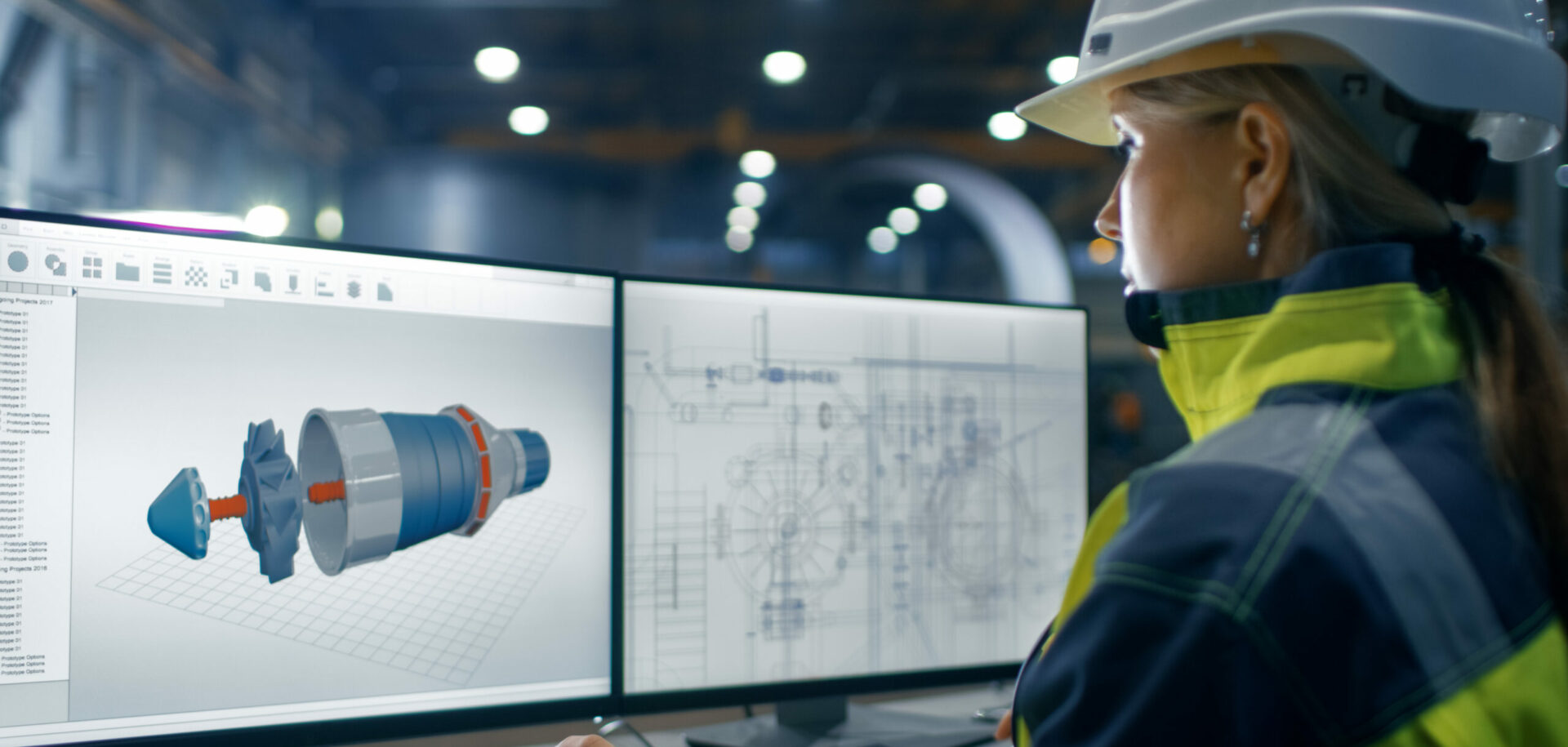
The power of speed
From its start in academia, Turbo Genset has become a main player in the fast-growing market for high-speed turbo generators.
Summary
Distributed power generation is regarded as a major future direction for the power industry because of the benefits it offers in terms of flexibility, economics and the environment. Turbo Genset gas-based systems include 400 kW and 1.2 MW generator designs based on the novel “permanent magnet axial flux” principle that has been pioneered and patented by the company.
The Turbo Genset natural gas 1.2 MW generating system is a compact, gas-turbine generating unit designed for efficient electricity generation, ease of transportation, low emissions, low noise and easy installation into a wide variety of temporary power applications. It is also well suited for combined heat and power applications to greatly enhance overall efficiency.
Turbo Genset recognizes that magnetic bearings have advantages in terms of life-cycle costs and performances and awarded a contract to SKF in 2003 to deliver magnetic bearing systems.
A low-cost, compact, conical magnetic bearing design was selected for this application. SKF’s advanced rotordynamic modelling and simulation at the beginning of the project verified the bearing and shaft design. The magnetic bearing system provides advanced condition-monitoring capability and the adaptive vibration control (AVC) in the magnetic bearing system provides vibration-free operation.
The generator itself only weighs 350 kg and operates at a design speed of 20,000 r/min. The 1.2 megawatt design is estimated to have 40 to 70 percent lower installed costs than competing power systems.
Competing technology, consisting of conventional skid-mounted, slow-speed generators coupled to a diesel or natural gas engine or coupled to a gearbox and gas-turbine drive, is not well suited for primary power applications because operating and maintenance costs are much higher.
From its start in academia, Turbo Genset has become a main player in the fast-growing market for high-speed turbo generators.
Justin Hall was a third year student in mechanical engineering at Imperial College London in 1990 when he received an offer he couldn’t refuse – to help take the college’s developments in high-speed electrical machines and advanced power electronics onto the open market.
Along with some of his lecturers, including Colin Besant, Hall found himself part of a group setting up a company called Turbo Genset. He was one of the company’s first employees and is now it operations director. Turbo Genset may have its roots in academia, but it is now one of the leading global product developers for the emerging distributed power-generation industry. It produces and develops packaged turbogenerator systems focusing on power ranges between 200 kilowatts and 2 megawatts, as well as reciprocating engine products from 80 to 200 kilowatts.
In July 2000 the company was floated on the London Stock Exchange and obtained a second listing in Toronto. More recently it has developed channel partnerships in North America, India, the Middle East and Australia.
From its expanding headquarters alongside Heathrow Airport in West London, the company develops and manufactures products that are divided into gas turbine and reciprocating engine-based systems for various applications, using advanced power generation and power electronics solutions.
The gas-turbine-based systems include 400 kilowatt and 1.2 megawatt generator designs based on a permanent magnet axial flux principle, which has been pioneered and patented by Turbo Genset. The 400 kilowatt unit was introduced in 2003 and is unique to the industry. A 1.2 megawatt unit, to be launched in 2005, will be driven by an industrial gas-turbine engine (and will be one of the largest commercially available high-speed generators in the world).
“The company was founded solely to commercialize technology being developed at the college, “ Hall explains. “For the first few years it existed only as a means to raise funds to develop the technology for high-speed machines designed to capture the energy in gas turbines and convert it into electrical energy.”
Considering its closeness to an airport runway, the Turbo Genset offices are extremely quiet, and the décor echoes the precise simplicity of engineering and its components. For example, the small round windows that look out over the stairs have riveted steel frames that look more like a generator component than a porthole. Reassuringly for makers of a product that depends on clarity and precision in design, there are no cluttered surfaces, no wayward tools, and everything is spotless.
This is how Hall likes it. “I have a real passion for symmetry in design,” he says, picking up a stainless-steel cooling fan. “Look at this. It’s like a work of art; its symmetry and balance could be inspired by nature.” He’s right. With its circle of blades that have a backsweep for the efficient compression of air, it looks like a flower. “We designed it,” Hall says proudly. “We simulated its design in a virtual environment. The devil is in the detail. If something is ignored, it comes back to bite you.”
Much of the detail in high-speed machine design involves dealing with stresses in materials, the management of heat loss, the cooling of devices, rotordynamics, and making sure the system doesn’t have vibration problems. This is where bearings come into the picture. “If the shaft’s natural frequency is below the running speed, then you have to design a bearing system to cater for that. This was something of a challenge when we began designing our flagship product, the 1.2 megawatt generator,” Hall says. “In our machines, the specific areas of focus are the high speeds of rotation. They are very fast, especially at 1.2 megawatts. We asked ourselves, ‘How can we get away from lubricated ball bearings, which have a limited life of three to four years in these applications?’”
The answer lay in painstaking research. After considering two non-contact bearing systems, air bearings and magnetic bearings, the company settled for the latter. “We knew by using magnetic bearings we would be beating the conventional solution on life-cycle costs, by reducing maintenance and power consumption,” Hall explains. “The magnetic bearing system is an intelligent device. Microprocessor controlled, it offers an ability to monitor the condition of machines in service. It’s ‘fit and forget’ for life. You never have to service it.”
In 2003, SKF Magnetic Bearings was asked to deliver three active magnetic bearing systems for the new 1.2 megawatt high-speed generator. “We worked with SKF to design the bearing to fit in the envelope of our generator and tuned the bearing system to match the rotordynamic performance,” Hall explains. “They provided a complete understanding of rotordynamics and high-speed machinery. I’m very pleased. We have a growing relationship with SKF and great synergy. The SKF Revolve team did a superb job in putting together a solution for Turbo Genset.”
In the works area behind the offices, a 1.2 megawatt generator sits in one of five test “cells.”
It took only two to three days to assemble but was the result of more than a year of painstaking research and design. Pressure and temperatures are being measured and the bearing controller, which looks something like a CD player, sits in a room a few metres away with a row of other computers.
A short walk away, through high, wide, pristine corridors, the smell of glue being cured wafts out of the stator cell. The bright gleam of copper coils, waiting to be incorporated into the stators, where the electricity is generated in each machine, shines on a granite workbench. In the final assembly area, the generator cell, a 400 kilowatt generator core, is waiting to go into its casing, and on the workbench a bearing cartridge lies in a plastic box. Pinned to a display board is a drawing that shows the internal workings of a 400 kilowatt generator. It gives the room an academic air, as if the diagram is there for students. But like Hall, who once spent years as a student, researching techniques for measuring friction losses on rotating discs, Turbo Genset has moved away from the college laboratory.