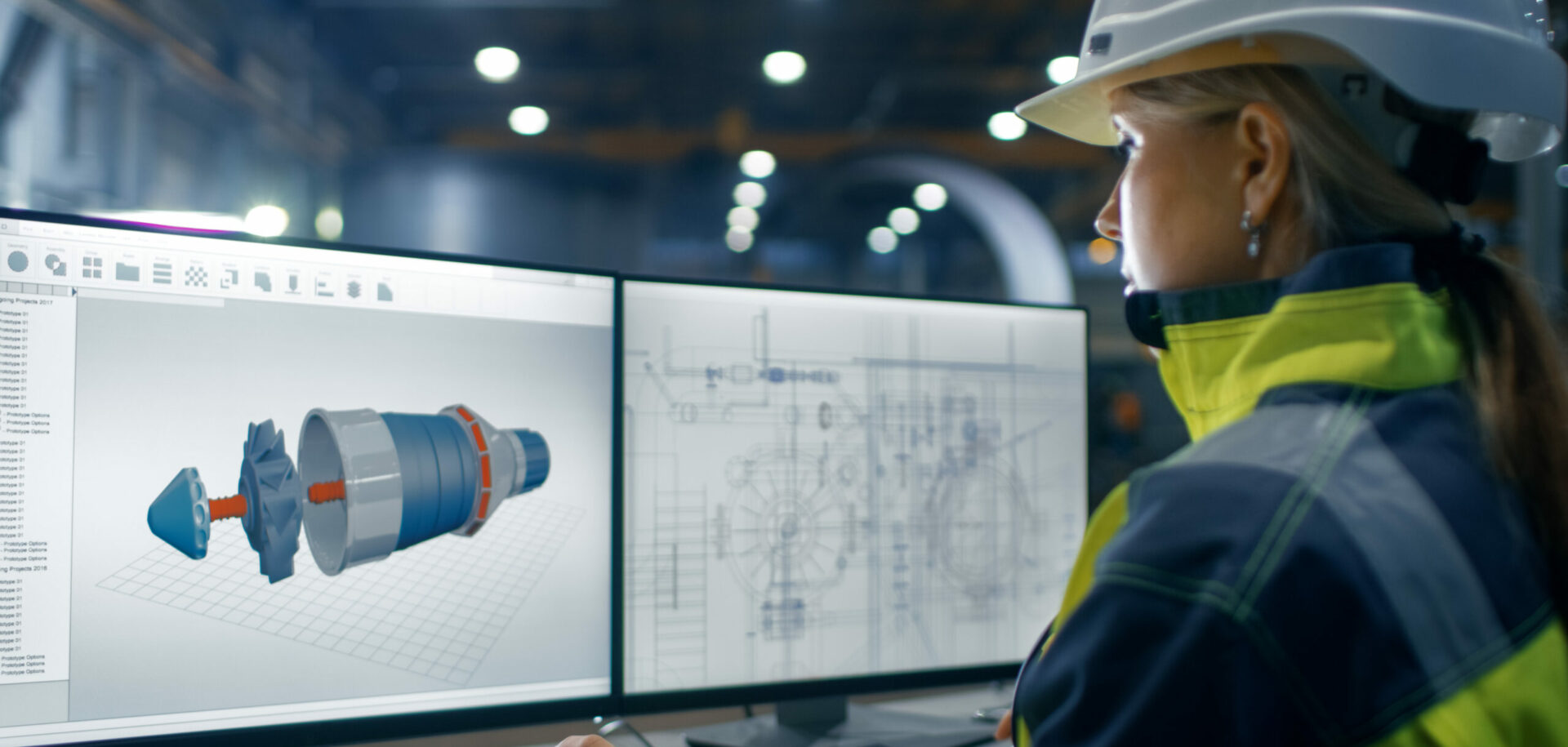
Thinking outside the box
Analyzing engineering problems to arrive at elegant solutions is the forte of consultant David Wood.
Looking much like Auguste Rodin’s famous sculpture The Thinker, David Woods picks up a can of soda and starts analyzing the industrial design that went into making the cylindrical container for liquids with a minimum amount of material.
“This is classic engineering evolution,” says Wood, who runs an engineering consultancy in automotive design, motorsport and general industry in the UK. “Remember the old thick-walled clunky cans that you had to open with a can opener? This can is a great example of something that is fit to its purpose. The concave bottom of the can prevents it from bulging under the internal pressure, the pull tag now remains with the can, and the material is so thin it does the same job with 50 percent less material.”
Wood is a metals guy. Actually, he is a motor guy. Wood has spent his 40-year career in powertrain design, which includes everything in a vehicle that has to do with the engine, the gears and the transmission – all the way to the rear wheels.
Officially, and on his CV, Wood has been director of advanced powertrain technologies, project manager for experimental Formula 1 test engines, engineering manager for powertrain systems, and development engineer for rally and race car engines.
But Wood compares himself more to a hands-on carpenter, albeit working with metals instead of wood.
“There are two types of engineers,” says Wood. “There are the technology guys who like all the math and analysis. And then there are people like me at the other end of the spectrum who like designing, manufacturing and developing the hardware. I can look at a component and ascertain how it is going to work for me. I can tell you almost instinctively what a particular powertrain component is capable of and where it will eventually fail.”
In extreme motorsports, as in just about any other industry, the name of the game has always been to do more with less.
Not unrelated, the 2010 Nobel Prize in physics was awarded to Konstantin Novoselov and Andre Geim for their discovery of graphene, or wafers of carbon, which could transform electronics because of their unusual properties relating to conductivity and their low weight and mass – as strong as steel but featherweight.
And in extreme motorsports such as Formula 1 and World Championship Powerboating, the weight-to-power ratio is a kind of holy grail.
“The target in developing power-train components for extreme motorsports is to take away as much material as possible where the stresses are low and yet make it sufficiently strong to do the job at hand, like win a race or, as in the case of current Formula 1 race regulations, more than one,” says Wood.
Wood paraphrases Colin Chapman, the founder of Lotus Cars and Team Lotus, which consistently won Formula 1 races between 1962 and 1978, who once said: “If the wheels fall off, the gearbox seizes and the engine blows up after you cross the finish line that’s OK, just so long as you have won the race.”
Says Wood: “This is perhaps not an acceptable solution in these days of austerity and reusable resources, but it is a true racer’s focus nonetheless.”
Wood agrees that it is somewhat of a handicap to look at the world from an engineering perspective. From soda cans to cover plates on engines and the number of bolts used, Wood says that he constantly analyzes why things are done the way they are.
“It is my natural state, and it still teaches me a lot,” he says.
In 2008, the Powerboat P1 organizing body, which runs high-speed boat races in places such as Malta, Italy, France and Sweden, approached Wood to put in place a system to test the engine power of the 20 participating racing boats.
The problem was that although the teams were required to declare the power of their engines (the power is used to determine the race weight of the boat), their declarations were taken on trust and never proven. This of course led to some teams understating their power so they could run lighter, more competitive boats.
At first, Wood tested each individual boat’s engines pre-season and installed sensors. The results from the race data captured by the sensors could then be compared with the original tests to see if there was any tinkering.
“This was a very expensive and complex procedure, and at the end of the day the teams were still finding ways to circumvent the rules,” says Wood.
“As the consultant in charge of ensuring engine legality, midway through the 2009 race season, I proposed a radical plan for the design and production of a system that could measure the torque and speed of each engine and provide the scrutineers and officials with a record of the real-time power output of the engine throughout the race,” he explains. “This would, in effect, be likened to fitting a miniature dynamometer to each engine. At the same time the torque sensor unit itself needed to be virtually impervious to outside interference by the teams, resistant to failure by being the strongest component in the drivetrain and robust enough to survive in a seawater environment.”
Working together with ABB and SKF, Wood developed this torque sensor system for Powerboat P1.
“In the 2010 competition, cheating was stopped dead in its tracks,” says Wood, with a big smile. “We nailed it.”