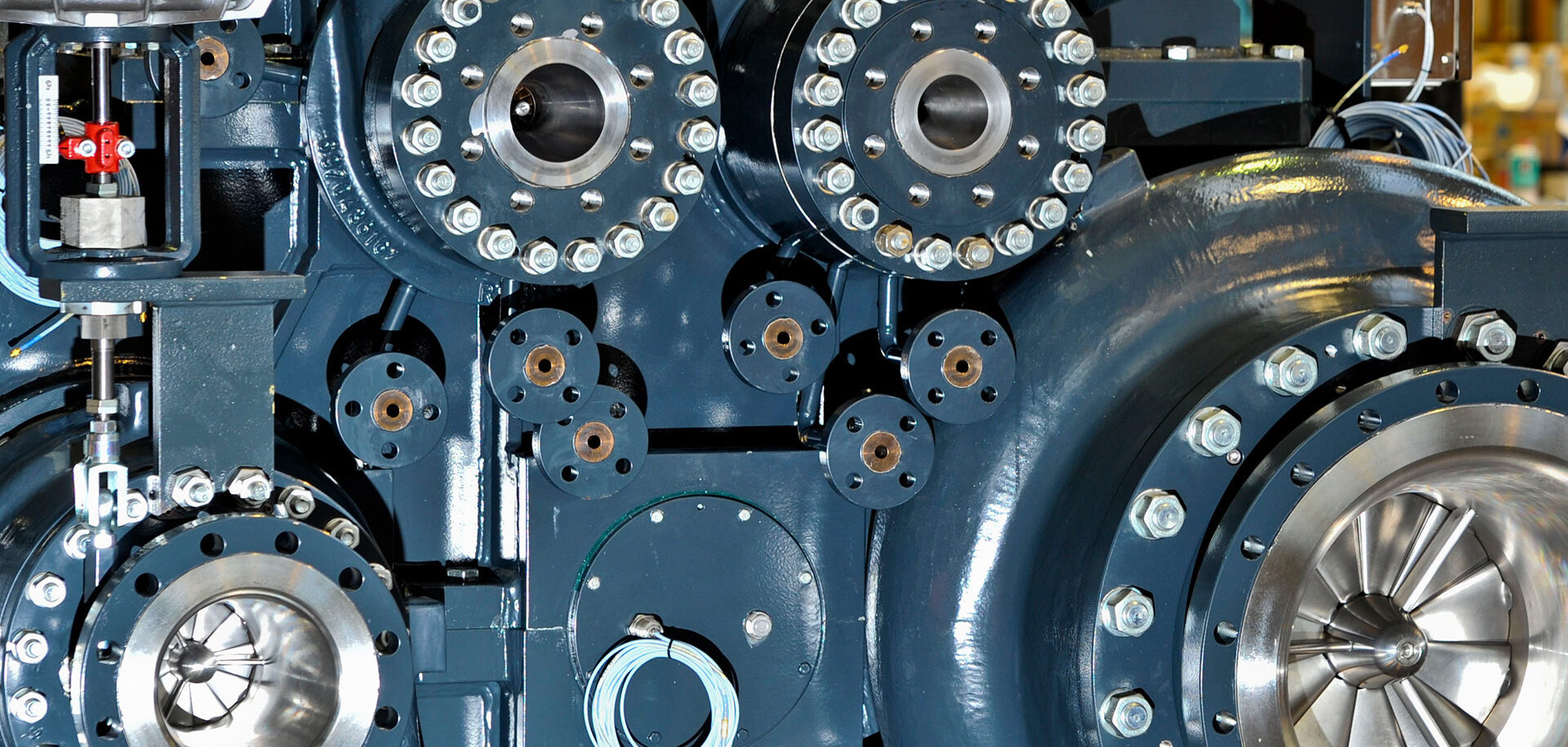
Transition from hydrodynamic to rolling bearings wins benefits
SKF solutions and engineering capabilities enable the transition from hydrodynamic fluid film bearings to more efficient rolling bearing systems.
The criticality of energy and resource efficiency, particularly in industrial production and power supply, is on the global agenda as almost never before. Despite technological progress, a lot of energy is still wasted in the world because of mechanical friction and fluid-dynamic losses in rotating machinery, including compressors, turbines, blowers and pumps. Here we show explanations and real-life examples in which considerable energy and cost savings could be obtained by replacing hydrodynamic fluid film bearings with modern rolling element bearings.
For industrial equipment such as pumps, compressors and blowers, yearly runtimes of 4,000 to 8,000 hours are quite common, which implies that the electrical energy to drive those machines is usually by far the largest contributor to life cycle cost (LCC) and emissions. In many cases, a powerful means of improving energy efficiency is the use of direct-drive variable speed drives (VFDs), as well as the choice and careful design of the impeller, bearings and sealing system.
For thousands of years, mankind has applied rolling elements (bars, rollers, balls) to reduce friction and heat loss in transport and rotating machinery and to provide accurate and reliable positioning of rotating shafts. That is why rolling element bearings are sometimes also called anti-friction bearings or precision bearings. However, for different technical and historical reasons, a lot of “friction bearings” are still used in the world, typically called plain, sliding, journal, fluid film or tilting pad bearings, or more specifically hydrodynamic or hydrostatic bearings.
Hydrodynamic versus rolling element bearings
Hydrodynamic fluid film bearings rely on fluid (oil) films to separate the steel surface of the rotating shaft from the stationary housing support, using the long-known principles of hydrodynamic lubrication. Well-lubricated hydrodynamic bearings show practically no fatigue or mechanical wear, and they provide more fluid film damping than ball or roller bearings. Due to the relatively thick oil film, dirt and other particles have less impact on their performance because hard particles are partly embedded in the softer sleeve or pad materials and thus cannot harm the countersurfaces.
However, hydrodynamic bearings have rather large clearances and will suffer from wear and scuffing in frequent start-stop operations or at very low speeds, which can be the case in VFD-driven applications. When the lubricating oil viscosity is low or the oil becomes heavily diluted by the process media, lubricant film build-up may not be sufficient anymore for good performance of hydrodynamic bearings, especially for the thrust tilting pad bearings. In this respect, rolling element bearings are a good alternative as they can operate with lower viscosity lubricants and dilution, especially when ceramic rolling elements are used.
Rolling element bearings are also often the preferred choice for intermittent operations and cold environments because of their low start-up friction, especially when using hybrid bearings with ceramic rolling elements. But what is more important for energy efficiency is that running friction is usually much lower for rolling element bearings, at least at low and medium speeds. According to a statement from J/E Bearing & Machine Ltd [1], the full fluid film in hydrodynamic plain bearings requires up to three times more energy to operate, even if start-up losses are excluded. The schematic figure below illustrates a typical result when comparing friction (power) losses in journal bearings compared with ball or roller bearings.
On the winning track: rolling bearings in turbochargers and crankshafts
As engineers and enthusiasts for high-performance cars know, ball bearing turbochargers have dominated the motorsport scene since the first ball bearings replaced journal bearings in turbochargers in the 24-hour LeMans races in the 1990s. There were two main reasons for this. Firstly, ball bearing systems showed lower running friction. And secondly, they avoided the need for high-pressure oil pumps that create power losses in journal systems where a lot of oil must be pumped through thin holes in the journal sleeves. Recent designs apply space saving cartridge units with hybrid ceramic ball bearings, taking performance to even higher levels.
Huge savings in the production of green electricity
A recently built 250 MW geothermal power plant in Asia is using the organic Rankine cycle (ORC) technology to produce green electric energy from geothermal heat. Almost 200 so-called screw expanders are used to drive the electricity generators. Screw expanders are based on the same mechanical principle as twin-screw compressors, but operate in the “opposite direction” to produce energy from expanding vapour, similar to a steam turbine. A particular engineering challenge was to reach the efficiency targets set by the plant owner. First tests showed that this could not be achieved when using hydrodynamic bearings. Note that five or six hydrodynamic bearings are used in each of the large screw expanders.
For this reason, SKF engineers supported re-engineering the expander to use rolling element bearings. In addition to lower running friction, the tight tolerances of rolling bearings allow the screw machines to run with very narrow end gap clearances between screw shafts and housing, which further increases efficiency. Calculations and tests showed that the related energy losses could be substantially reduced, typically from 30 kW to 12 kW, which means that a single expander can produce 18 kW more electricity output when a rolling bearing system is used.
Saving 18 kW of power losses can mean more than 100,000 kWh of additional electrical energy output – per machine and per year. Multiplied by the large number of screw expanders used in one plant, this translates into more than a million dollars of additional profit per year.
Industrial chillers and heat pumps
Large commercial or industrial chillers or heat pumps typically engage centrifugal or reciprocating compressors, which compress a refrigerant gas to enable heat transfer from a lower-temperature source to a higher-temperature sink. Traditionally, many refrigerant compressors were or still are gear-driven designs, often comprising hydrodynamic bearings lubricated with an oil-refrigerant mixture.
The introduction of new environmentally friendly refrigerants (e.g., hydrofluoroolefins (HFO) with low global warming and ozone depletion potential) and the much higher temperature levels needed in heat pumps or data centre chillers often have an unwanted effect: the rate of dilution of the oil by the refrigerants is increased, sometimes up to dilution ratios of 50 % or more. In some cases, the oil viscosity becomes too low for hydrodynamic bearings and the compressors’ bearing arrangement needs to be changed to rolling bearings, which also gives the additional advantage of lower frictional losses and higher impeller positioning accuracy.
Together with some application experts and key customers, data for frictional losses were collected from testing and field experience and consolidated for a typical medium-sized (~300kW) centrifugal chiller (fig. 3). In this comparison, the following types of losses were considered: bearing friction, volumetric sealing gap losses, check valve losses and heat transfer losses due to contamination of the heat exchangers by oil mixing with the refrigerant gas.
The data show that rolling bearings create lower bearing friction losses and also lead to lower volumetric seal gap losses due to better running accuracy. A positive effect on efficiency is also attributed to the fact that rolling element bearings require much less oil (typically less than 10 %) for lubrication than hydrodynamic bearings and so less oil is mixing into the refrigerant, leading to lower oil contamination in the heat exchangers. Therefore, chiller efficiency improvements of 3 % to 4 % can be achieved by using oil-lubricated rolling element bearings instead of journal or hydrodynamic bearings. Another major step in improving efficiency may be achieved by designing oil-free chillers, based on either SKF magnetic bearings or SKF Pure Refrigerant Lubricated (PRL) bearing solutions as written in SKF’s Evolving Chiller Performance brochure and in this Evolution article.
Large ammonia screw compressor
Recently, SKF was deeply involved in the design of a new generation of large ammonia screw compressors for chiller and refrigeration applications. The customer, a leader in this field, typically used hydrodynamic journal bearings with relatively large bearing clearance to accommodate the radial loads and angular contact ball bearings for thrust loads. Currently cylindrical roller bearings with tight radial clearance tolerances are piloted as an alternative to hydrodynamic bearings. This improves the volumetric efficiency of the compressor; the oil consumption of the compressor system can also be reduced.
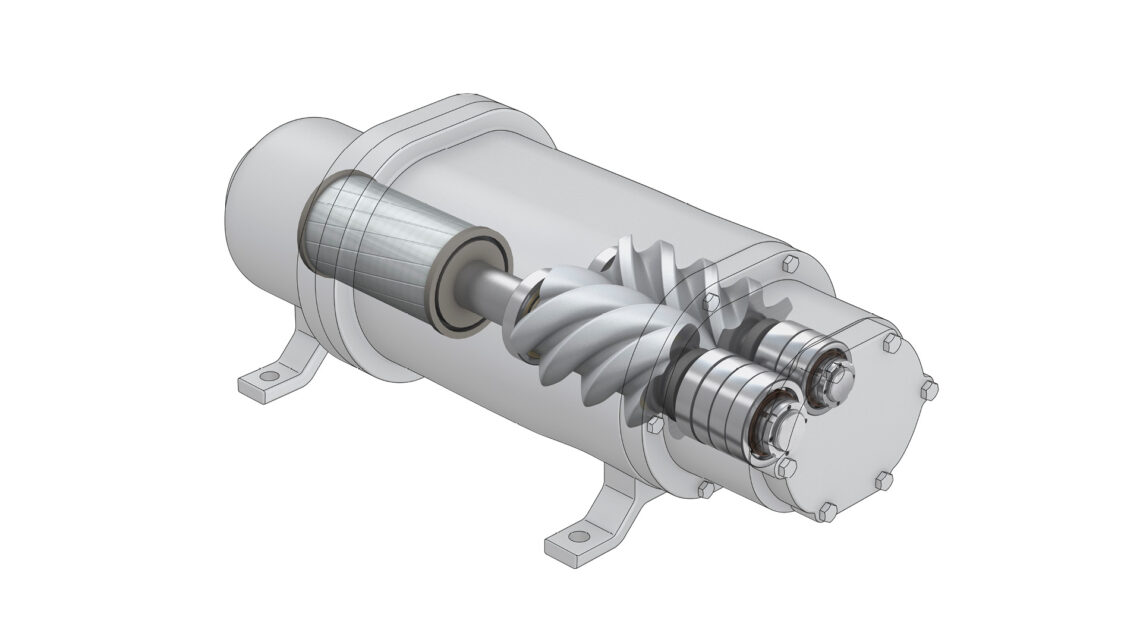
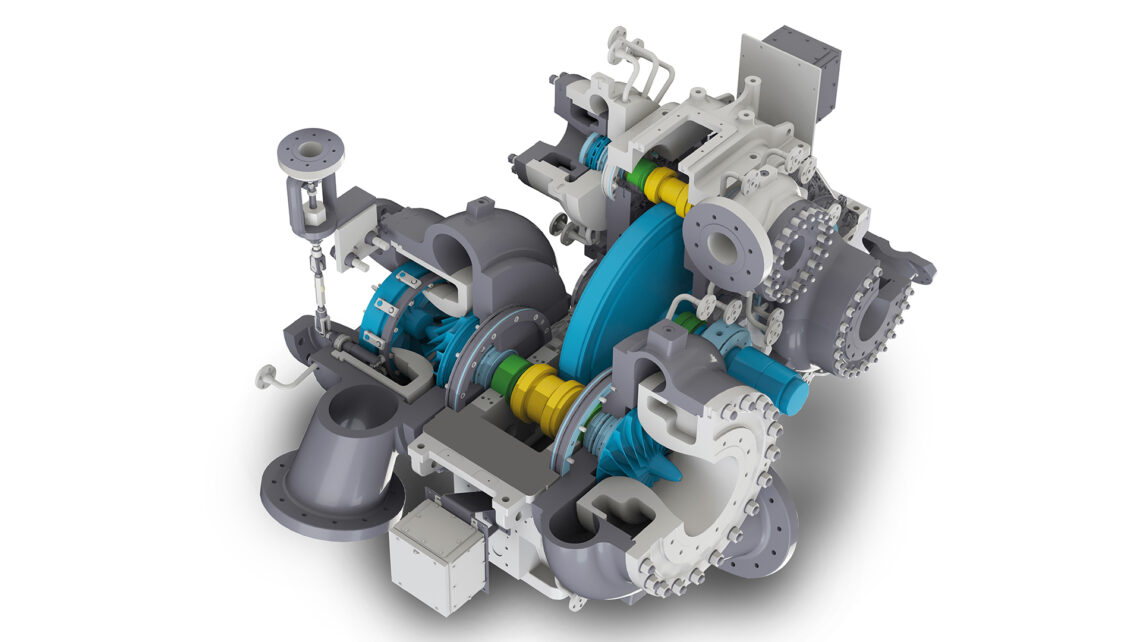
This image and main image courtesy of Atlas Copco Gas and Process.
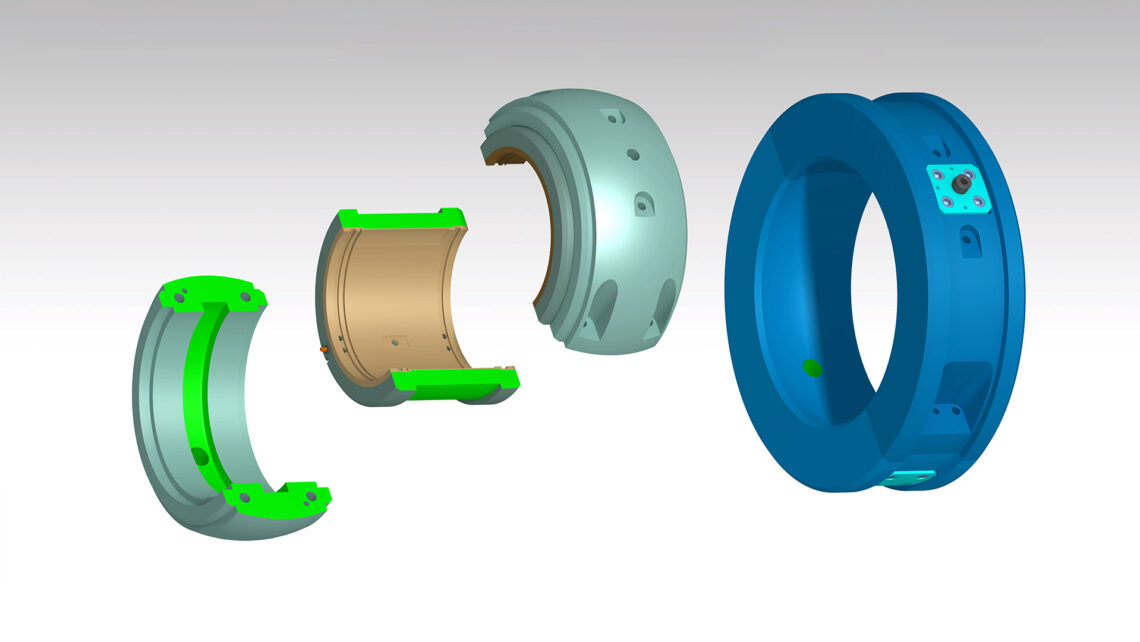
Benefits of rolling element bearings versus hydrodynamic plain bearings:
- High positioning accuracy allows low gap values for seals and impellers, which reduces flow losses (volumetric losses)
- Lower bearing running friction
- Better suited for frequent start-stop operations or very low speeds (e.g., for VFD drives)
- Can deal with low viscosity and heavy dilution of the oil
- Typically 90 % lower lubricating oil volumes needed, and less oil system maintenance
- Reduced system complexity and cost of overall system
- Simpler bearing arrangements for thrust and combined loads or large misalignments.
[1] J/E Bearing & Machine Ltd., “Plain or Rolling Bearings – Which is Best?”
[2] Vanhaelst R, Kheir A, Czajka J, “A Systematic Analysis of the Friction Losses on Bearings of Modern Turbocharger”, Combustion Engines 1/2016 (164), pages 22–31.
[3] Morales G E, Hauleitner R, Wallin H H, “Pure Refrigerant Lubrication Technology in Oil-Free Centrifugal Compressors”, Evolution 2 March 2017.
[4] “SKF GBLM – A New Rating Life Model Applied to Hybrid Bearings”, Evolution 4 February 2021.