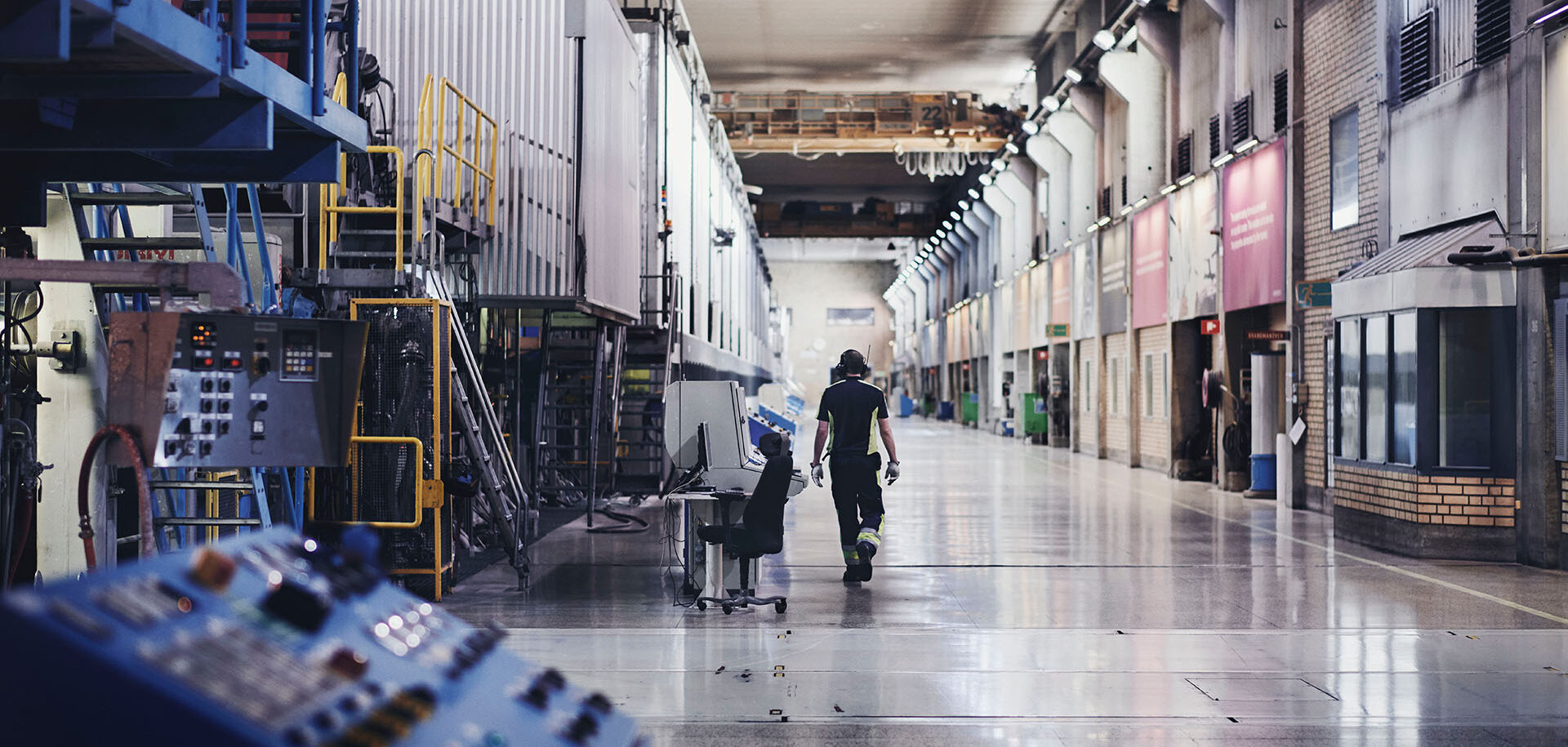
Uptime All the Time
Apart from planned stops, the machines in Sweden’s Iggesund pulp and paperboard mill run day and night, all year round – in hot, humid and high-pressure conditions. SKF monitoring devices play a crucial role in ensuring that the equipment keeps running.
To supply the market for such fine packaging material is a demanding process. For one thing, the customers have exacting quality requirements. In addition, responding to the high demand means the mill has to be in motion all the time. Apart from planned maintenance stops, the machines run day and night, all year round.
That’s no small feat because the mill’s equipment is pushed to its absolute limit, in extreme heat, moisture and pressure. These tough operating conditions take their toll on the machine components, including the bearings. The risk of a breakdown is a constant concern for Iggesund. Since the process is so cyclical, streamlined and interconnected, an unforeseen stop in production costs as much as 200,000 Swedish kronor (18,000 euros) an hour.
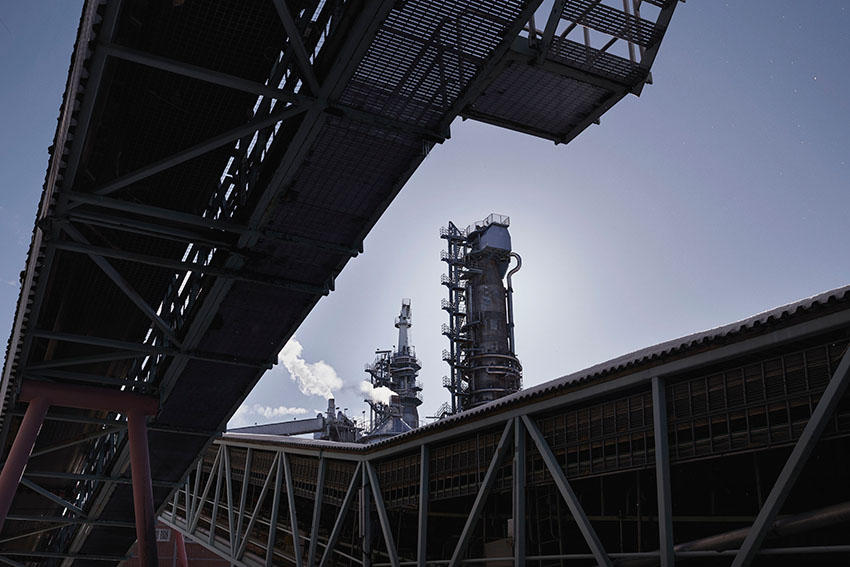
The monitoring process
Yet the machines seldom fail, and that’s due to Iggesund’s extensive and exhaustive monitoring process, in which SKF plays a vital supporting role. The mill makes use of almost the entire SKF bearing range, so SKF visits Iggesund every three weeks for regular check-ins. The companies have a close working relationship.
This time we got lucky, it could have been a matter of hours before it failed completely.
Some of the mill’s appliances have automatic monitoring devices installed; others need to be checked manually. SKF monitoring devices collect and interpret machine data to be analysed by the person responsible for monitoring the particular machine. Approximately 250 measuring points are connected to the SKF condition monitoring devices.
Here’s an example of how it works. When Lennart, a member of the monitoring team, noticed an anomaly in the graph reporting on the performance of a machine he was monitoring, he was able to use a planned stop to inspect the flagged CARB roller bearing.
A few days later, when the time came to dismount the bearing, the team discovered that it was on the verge of breaking down. “This time we got lucky,” Lennart says. “It could have been a matter of hours before it failed completely.”
SKF and Iggesund
SKF is proud to be part of the process at the Iggesund mill. It takes the best match-up of hardware, software, knowledge and experience to provide reliable rotation in this versatile and demanding operating environment. But thankfully, between Iggesund and SKF, there’s about 400 years of experience and knowledge to fall back on.
Iggesund Mill
Today the integrated pulp and paperboard mill is under the majority ownership of the Holmen Group, which has invested heavily in making Iggesund a world leader.
Iggesund has a highly sustainable approach to producing its high-end paper. The integrated mill manages different kinds of raw material and uses all the waste from its production to make either pulp or energy.
All of the pulp used to make paperboard is produced on location and is pumped in a wet state to the board machine. The pulped wood, which has the viscosity of sour milk, is boiled in massive water towers before it is dried, pressed, rolled up and made ready to deliver.
In operation, the mill produces all the heat it needs and can also provide district heating to the nearby community. It also produces nearly all the electricity needed for the mill.