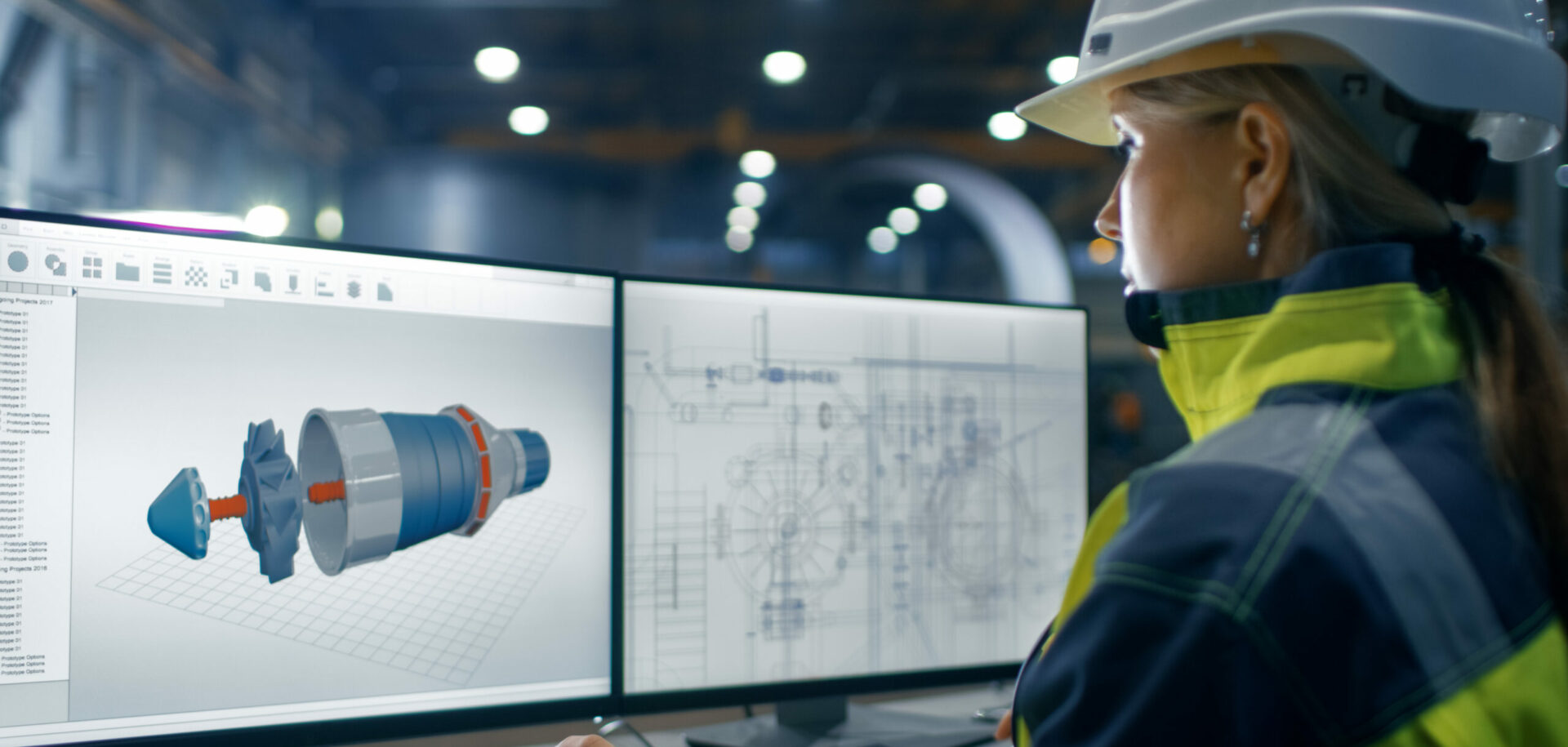
X-TRACKER
How asymmetrical hub bearing units improve high-performance car handling
How asymmetrical hub bearing units improve high-performance car handling
For high-performance cars,maintaining good handling characteristics under all conditions is important to the overall driving experience. SKF engineers provided an award-winning solution through the development of an innovative asymmetrical hub bearing unit that resolved a long-standing issue of calliper piston knock back that can happen during cornering at high speeds or when driving on rough roads.
Calliper piston knock back results in increased brake pedal travel after severe cornering manoeuvres that affects the braking response time and the precision of the Electronic Stability Control (ESC) system.
It happens when deflection occurs in the knuckle, hub and brake calliper assembly (fig. 1). Very heavy lateral forces at the tyre/road contact area cause such deflections. When the wheel hub deflects, the relative motion between the brake disk and the calliper piston causes displacement of the piston. When the relative motion exceeds the roll back limits of the calliper piston seal, the piston will slide on the piston seal and will be held in a retracted position. This creates excessive running clearances between the disk and the brake pad. The piston remains in a retracted position (knock back) until the next brake action is applied. This means that subsequent applications of the brake exhibit longer brake pedal travels before the engagement is sensed (fig. 2).
High-performance braking
Naturally, high-performance vehicles must deliver exceptional handling and braking by delivering predictable, linear responses under all driving circumstances. As high- performance vehicles are often driven at or near their dynamic limits, the ability to drive deep into a corner and apply the brakes with absolute confidence is critical if the vehicle’s capabilities are to be met.
Ironically, the strategies used to improve vehicle platforms to create high-performance such as special brakes and tyres can have the adverse effect of increasing the conditions for knock back. In particular, the wheel hub has to accommodate heavier forces, resulting in amplified wheel hub deflection and a larger diameter brake disc can exaggerate the geometric sensitivity to camber deflection at the hub.
Excessive brake knock back also has a negative effect on the effectiveness of the ESC system, as it will increase the running clearances between the brake disc and the brake pad. The running clearance creates a system compliance that must be overcome by the ESC prior to generating braking forces, and this can delay or reduce the effectiveness of ESC interventions.
Identifying the problem
During vehicle development, the 2006 Cadillac STS-V developed knock back behaviour. Before developing a solution, the SKF engineering team, together with General Motors (GM) engineers, took a systems approach. They carried out vehicle testing to define the problem areas and used laboratory testing to reproduce the problem. They also identified potential concerns related to aspects of improving the wheel hub design.
These were:
-
The base vehicle architecture may severely restrict the options available to improve hub camber stiffness
-
Wider tyres often result in less favourable wheel offsets, negatively affecting the bearing stance
-
Wider performance tyres can have better adhesion and generate heavier camber loads
-
Larger wheels often result in taller static-ally loaded tyre radius, resulting in heavier camber loads for a given contact patch force
-
Larger diameter brake discs amplify hub camber deflections at the calliper piston
-
Fixed, opposed piston callipers have less compliance and exhibit an increased sensitivity to hub camber deflections.
The essence of hub bearing unit development.
Traditionally hub bearing units are designed on the basis of their radial and axial loading, low friction relative movement between wheel and knuckle, providing support to the brake disc and the wheel. For the bearing unit itself, parameters that need to be considered are the bearing load carrying capacity, the sealing, strength of the structural flanges and its retention or clamping mechanism. There are also benefits of looking outside the hub bearing unit to consider its influence on the behaviour of the surrounding chassis and brake components.
Because of the constraints of the vehicle architecture, the engineers need to be creative in maximizing camber stiffness while maintaining the interface with the existing vehicle components.
There are four main attributes that affect hub stiffness. These are the hub geometry, the bearing preload, the bearing stance, which is the distance between the bearing pressure centres defined by the distance between the two rows of rolling elements, their pitch circle diameter and the contact angles. The final parameter is the point about which the hub flange bends. The engineering team realized that they could make changes that would improve stiffness. To reduce hub bending, they increased the flange thickness, changed from preload retention by snap rings to orbital forming, increased the row-to-row distance and increased the pitch circle diameter of the outboard row to further increase the stance (figs. 3 and 4).
This defined the concept for the asymmetric hub bearing unit. The inboard row has a relatively small pitch diameter, to fit existing vehicle geometry, while the outboard row has a larger pitch diameter to include more rolling elements for increased stiffness. Additionally, the flange thickness was increased by 3 mm (fig. 6).
The design provides significantly increased camber stiffness while fitting within the existing vehicle architecture. Vehicle testing showed a 56 % reduction in knock back over the original design, providing the vehicle with consistent, predictable brake pedal response and precise ESC even under challenging driving situations (fig.5). This significantly reduced brake calliper piston knock back. To date, SKF has developed three versions of the X-Tracker: a ball bearing version (fig. 6), a ball and tapered roller bearing version (fig. 7), and a tapered roller bearing version (fig. 8).