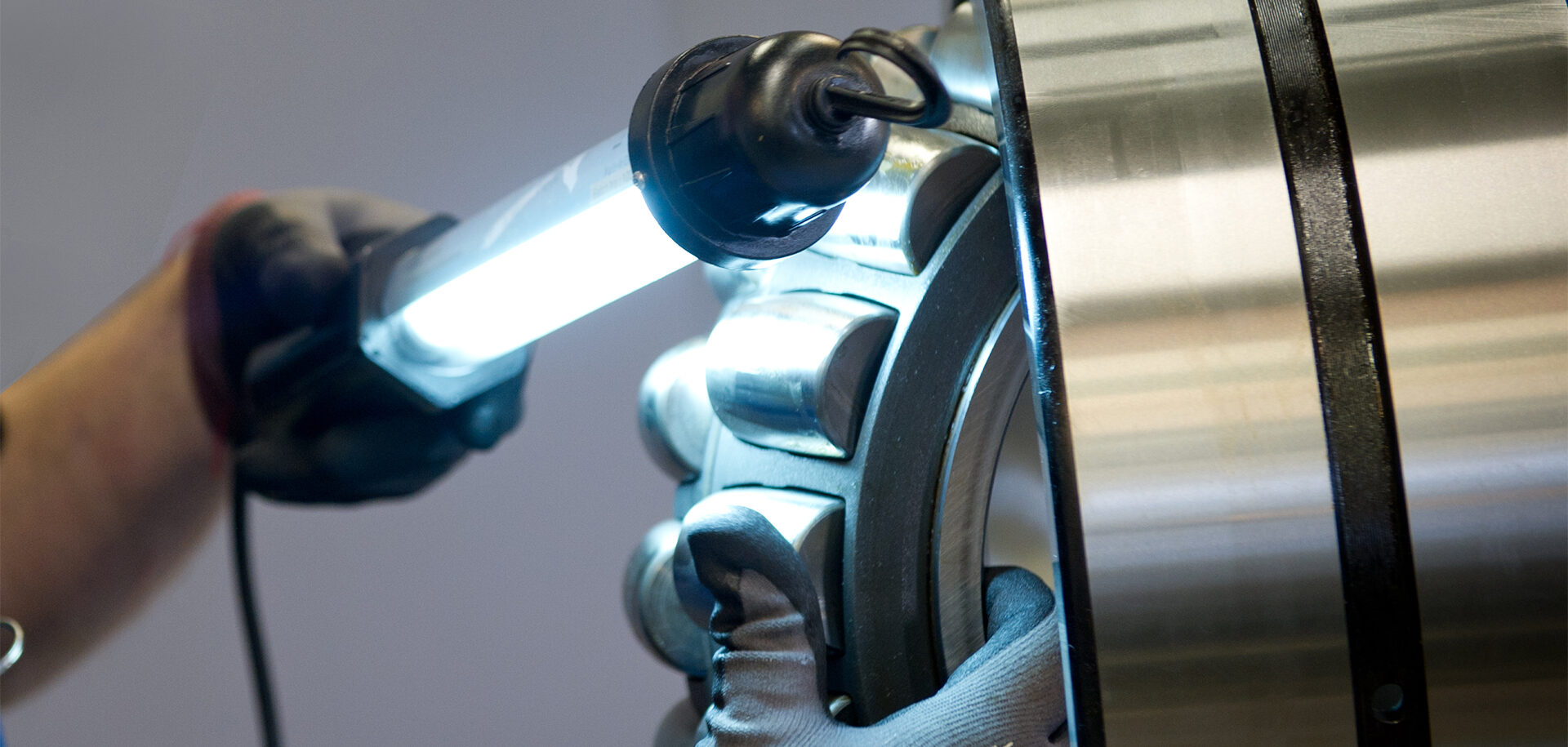
最全的轴承失效模式和原因都在这里
识别滚动轴承的失效模式,并查明造成损伤的原因是避免重复损伤、提高设备可靠性的第一步。
作为现代工业机械设备中最常见的部件之一,轴承以最小的摩擦将旋转部件(轴)和固定部件(轴承座)组合在一起。有了轴承,汽车、飞机、发电机、输送机、印刷机等各种旋转设备得以平稳运行。
对于经常和工业设备打交道的人来说,应该更好地了解轴承的工作方式以及在运行中过早失效的原因。
为此,国际标准化组织 (ISO) 发布的 ISO 15243标准对滚动轴承的不同失效模式进行了分类,并对每种失效模式的特征、外观变化及其可能产生的原因进行了描述。该标准的最新版本于 2017 年发布。
除了了解失效模式的特征和外观,了解导致失效的原因也很重要。认识了这些,有助于采取所建议的纠正措施来避免失效的再次发生。当然,如果轴承一直运行到失效(RTF)并发生卡死,则可能无法识别失效模式及其原因。
本文总结了滚动轴承的 ISO 失效模式及其原因。在此之前,首先介绍一些基础信息。
轴承基础知识
滚动轴承是由高硬度轴承钢制成的高精密机器部件,现在越来越多的滚动轴承采用陶瓷滚动体。轴承由内圈和外圈、滚珠或滚子及保持架组成,图 1 显示了滚动轴承的常用部件。有些轴承还带有密封或防尘盖,这种密封式轴承出厂时已预填润滑脂,润滑油或润滑脂对于分隔滚动体和滚道所需要建立的润滑膜厚度至关重要。必须为设备选择合适的轴承,并正确安装,确保轴承润滑良好且无污染。在寻找损伤迹象时,正确理解轴承内部几何形状以及轴承的工作原理非常重要。
失效原因
导致轴承无法正常运行并失效的原因是什么?
了解失效模式本身很重要,但了解导致失效的原因也许更重要。
对于这个问题,不同的人有不同的答案。为了服务客户和开展研究,SKF进行了许多轴承检测和损伤分析调查。调查结果记录在SKF轴承分析报告软件 (BART) 中。这种基于云的软件会跟踪所运行的轴承被拆卸的原因以及造成轴承失效的原因,以及一些其他数据。基于这些数据,SKF 便可以解答这个问题:为什么轴承会停止运行?
数据表明,大多数轴承因运行过程中振动和噪声过大而被拆卸下来。当对设备进行维护或温度过高时,轴承也会被拆卸(图 2)。
轴承运行期间的ISO 15243失效模式分类
ISO 15243: 2017 [参考文献1] 对安装在设备中的轴承在运行期间发生的失效模式进行了分类,也就是说不包括部分缺损等制造型缺陷。ISO 将失效模式分为六个大类:滚动接触疲劳、磨损、腐蚀、电蚀、塑性变形、以及裂纹和断裂(图 4)。每一大类都包含子类别,以便对失效模式进行更具体的分类。
《轴承损伤和失效分析》手册 [参考文献2] 可用于识别轴承失效模式和原因。
关于六大类失效模式的描述如下:
滚动接触疲劳 (ISO 5.1)
滚动接触疲劳分为两个子类:次表面起源型疲劳和表面起源型疲劳。次表面起源型疲劳(ISO 5.1.2)(图 5)是由滚动接触表面的循环载荷引起的,随着时间的推移会导致材料结构发生变化,从而产生微裂纹。微裂纹通常在表面下轴承钢中的夹杂物处萌生,随后扩展至表面,发生剥落。这种疲劳受轴承质量、施加的载荷、润滑和清洁度的影响。这类似于轴承额定寿命 L10mh 。如果轴承因瞬时过载或其他削弱材料性能的运行状态而承受高应力,则次表面疲劳可能加速扩展。在这些情况下,疲劳寿命很短(只有L10mh 的 5% 到 10%)。表面起源型疲劳(ISO 5.1.3)(图 6)是起源于滚动表面的疲劳,通常由润滑不良或污染导致的表面损伤引起。润滑油膜厚度不足和固体污染物过度碾压会引起金属与金属接触,从而造成表面微凸体相互剪切。之后相继出现微裂纹和微剥落,最后导致表面起源型疲劳。
磨损 (ISO 5.2)
第二类是磨损。ISO 将磨损分为两个子类:磨粒磨损和粘着磨损。磨粒磨损(ISO 5.2.2)(图 7)是指在颗粒污染物等磨粒的作用下,表面材料逐渐移失。润滑不充分时,也会发生磨粒磨损。其特征通常是表面外观变暗。磨粒磨损是一种退化过程,最终会破坏轴承滚动表面的微观几何形状。磨粒会迅速磨损内外圈滚道、滚动体以及保持架兜孔。污染物侵入润滑剂和轴承,以及滚动接触中的润滑剂不足都有可能引起磨粒磨损。
腐蚀 (ISO 5.3)
第三类是腐蚀,分为三个子类:锈蚀、蠕动腐蚀和伪布什压痕。锈蚀(ISO 5.3.2)(图 9)是湿气进入轴承的常见问题。高硬度轴承材料的耐腐蚀性低,当轴承处于静止状态时,湿气会在对应滚动体间距的位置形成锈蚀,表面氧化后会在后续运行中产生次表面起源型疲劳。湿气极大地降低了润滑剂在运行的轴承中形成一定厚度油膜的能力。蠕动腐蚀(ISO 5.3.3.2)(图 10)发生在配合面之间的界面产生微小运动时,例如轴承内圈和轴之间以及轴承外圈和轴承座之间。这可能是由于轴承与轴或与轴承座的配合错误,还取决于所施加的载荷。例如,内圈旋转和载荷恒定的轴承要求其内圈与轴具有一定的最小过盈配合,以避免蠕动腐蚀。同样,内圈旋转和内圈上施加旋转载荷的轴承要求轴承外圈与轴承座具有一定的过盈配合,以避免蠕动腐蚀。蠕动腐蚀表现为界面上的黑红色氧化。伪布什压痕(ISO 5.3.3.3)(图 11)发生在承受小幅振摆或振动的滚动体和滚道之间的接触区。滚动体间距位置上形成凹陷,导致表面的原始抛光面脱落,并且还会在表面上产生类似于蠕动腐蚀的黑红色氧化。磨损量取决于外加载荷的强度、振摆和振动的强度以及润滑条件。
电蚀 (ISO 5.4)
电蚀分为两类:过电压电蚀和漏电流电蚀。过电压电蚀(ISO 5.4.2)(图 12)发生于电流通过滚动体从轴承的一个套圈传递到另一套圈时。在接触表面上,该过程类似于电弧焊(小接触表面上的高电流密度)。材料被加热到从回火到熔化的温度范围,这会导致出现尺寸大小不一的变色区域,该处的材料经过回火、二次淬火或被熔化,由于轴承的旋转作用,在材料熔化并剥离的地方会形成环形坑,凸起的材料会被磨掉。在焊接设备接地不当情况下对机器进行焊接修补时,设备上产生的电火花可能会导致过电压电蚀。漏电流电蚀(ISO 5.4.3)(图 13)发生在低强度电流流过轴承时。损伤通常呈现彼此靠近的环形浅坑,并且随着时间的推移会出现灰色搓板纹。滚动体可能呈现灰色、暗淡的外观,并且润滑剂也会变色。损伤的程度取决于电流强度、持续时间、轴承载荷、转速和润滑剂。当轴未正确接地或者电机由变频驱动器 (VFD) 控制时,漏电流电蚀在有杂散电流的电机中很常见。
塑性变形 (5.5)
ISO 将塑性变形分为两类:过载变形和颗粒压痕。过载变形(ISO 5.5.2)(图 14)是由静态过载引起的机械损伤,造成静态过载的原因包括搬运不当(轴承从高处掉落)、安装不当(锤击轴承)、设备运行时承受冲击载荷等。表现为滚道压痕或对应于滚动体间距位置的凹陷,保持架、密封和防尘盖的损伤等。颗粒压痕(ISO 5.5.3)(图 15)出现在当固体颗粒污染物或碎屑在轴承滚动接触区过度碾压时,从而导致滚道和滚动体产生压痕(变形)。损伤的范围受颗粒的大小、类型和硬度的影响。压痕处被持续碾压后会导致表面起源型疲劳 (ISO 5.1.3)。
裂纹和断裂 (ISO 5.6)
最后一个ISO失效类别是裂纹和断裂,分为三个子类:过载断裂、疲劳断裂和热裂。过载断裂(ISO 5.6.2)(图 16)发生在应力超过材料的抗拉强度时。过载断裂的常见原因是过盈配合过紧,或者圆锥孔轴承在锥形轴颈或安装套上的推进距离过大,会产生过高的环向应力。疲劳断裂(ISO 5.6.3)(图 17)发生在循环弯曲条件下,应力超过材料的疲劳强度时。反复弯曲会导致裂纹萌生,并扩展到套圈或保持架上。如果轴承承受重载,并且轴承座的支撑刚度不够大时,会使外圈承受高循环应力,轴承中便可能出现疲劳断裂。热裂(ISO 5.6.4)(图 18)发生在两个表面相互滑动,并产生摩擦热时。如果滑动很大,表面局部会二次淬火,再加上很高的残余拉应力的扩展会导致裂纹,裂纹通常垂直于滑动方向。例如,静止的轴承座与旋转的轴承套圈接触,就会发生热裂。
有关轴承失效模式和原因的更详尽描述,请参见参考文献 2。
值得注意的是,受损轴承内的润滑剂(润滑油或润滑脂)也可以为轴承失效研究提供有价值的信息。需要对旧润滑剂采样,再与新样品进行对比。对润滑剂的分析应考虑颗粒和水分污染的含量、粘度变化、润滑脂稠度变化等因素。
检查轴承密封或防尘盖以及其他部件(例如安装套)也可能获得有用信息。
预测性维护(PdM)或基于状态的维护(CBM)技术,例如振动分析、热成像、油液分析等,可用于在轴承发生严重损伤以及可能对安装轴承的设备损坏之前进行的故障检测。这样可以更好地鉴别失效模式。在发生大面积损伤之前将大型轴承(内径 > 200毫米)拆卸,就有可能对其进行修复。通过修复使轴承“焕然一新”,从而降低维护成本和对环境的影响(图 19)。
最常见的失效模式
SKF的分析数据1 确定了五种最常见的ISO失效模式,即磨粒磨损 (26%)、表面起源型疲劳 (16%)、锈蚀 (14%)、粘着磨损 (7%) 和漏电流电蚀 (7%)(图20)。这些失效模式约占轴承研究中确定的所有失效模式的 70%。虽然在大多数轴承中都可以看到蠕动腐蚀(即使是轻微的),但不构成主要的失效模式。其他 ISO 失效模式在数据中也有所体现,但并不多见。
SKF 轴承分析报告软件 (BART)
SKF 工程师使用的SKF轴承分析报告软件现可供广大客户使用。SKF为客户提供有关轴承知识、轴承检测技术和SKF轴承分析报告软件使用方法的基本培训。客户与 SKF 应用工程师或专家密切合作以完成检测报告,轴承分析报告软件生成的检测报告经由SKF 专家审核。通过这种检测,可以判定轴承是否应该更换、能否再次使用、能否进行修复或是必须报废。它还可用于记录对新轴承投入使用前的检查,这对于已存放很长时间的轴承非常有用。
在必要时,SKF 应用工程师可以对轴承进行全面的损伤分析,为提高可靠性提供建议。 SKF 工程师可借助人工智能[参考文献3] 来提高轴承损伤分析水平。人工智能使用计算机视觉系统,通过数码照片来评估轴承损伤情况。该系统采用人工智能形式的神经网络算法进行图像识别,并利用SKF档案中数千张失效轴承的图片进行学习。
总结
综上所述,ISO 15243 有助于对在设备运行中的滚动轴承的失效模式进行分类,并识别失效原因。通过了解常见的轴承失效模式及其原因,便可以采取纠正措施以避免再次发生失效。此举可大幅降低出现意外和重大故障的风险,并有望提高设备的可靠性和利用率。由于维护需要而拆卸的轴承,可以进行能否重新使用或进行修复的检查。
SKF正在收集轴承失效模式及其原因的数据,以及其他相关数据,以更好地了解轴承运行状况。 SKF 使用的轴承分析报告软件也可供客户生成轴承检查和损伤分析报告。
1 SKF 轴承分析报告软件
参考文献
[1.] International Standard ISO 15243:2017, “Rolling bearings damage and failures – terms, characteristics and causes”
[2.] SKF brochure 14219, “Bearing damage and failure analysis”
[3.] SKF Evolution article, “The future of bearing failure analysis is here” (2022)