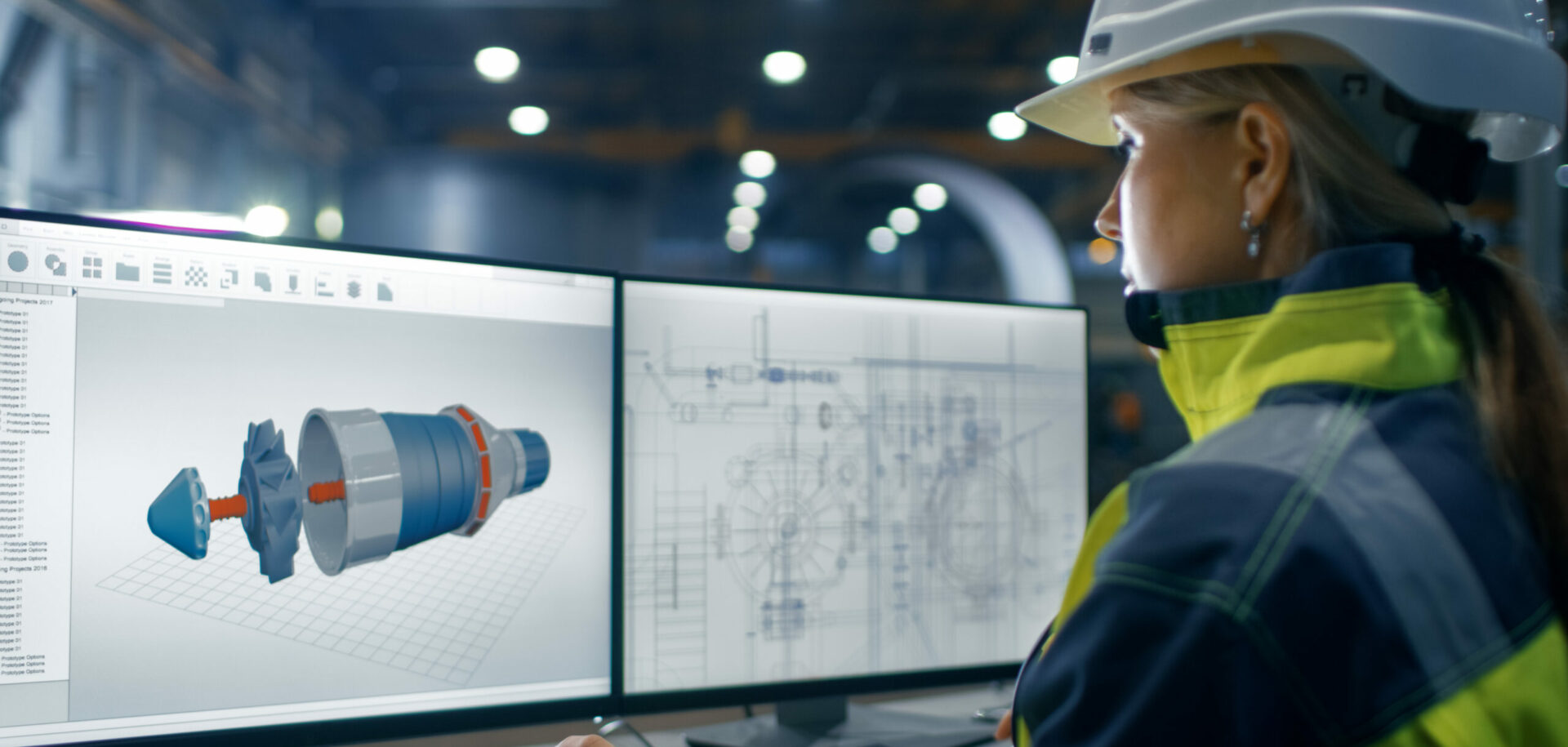
Vorteile der Verwendung brünierter Lager in Windkraftanlagen
Da Windkraftanlagen immer größer und leistungsfähiger werden, hat auch ihr Antriebsstrang steigende Anforderungen zu erfüllen.
Zusammenfassung
SKF nutzt das Brünierverfahren, um Windkraftanlagen, die unter schwierigen Betriebsbedingungen betrieben werden, einen besseren Schutz vor Lagerschäden zu bieten. Hierbei werden die Lagerkomponenten mit einer Beschichtung versehen, die nicht nur vor chemischen Einwirkungen und Korrosion schützt, sondern auch verhindert, dass es zu Schäden in der wichtigen Einlaufphase kommt.
Windkraftanlagen sind während des Betriebs vielfach wechselnden Temperaturen, Windgeschwindigkeiten und -lasten ausgesetzt [1]. Diese Betriebsbedingungen könnten in Verbindung mit potenziell schädlichen Einflüssen infolge von Verschmutzung oder tribochemischen Reaktionen, aufgrund der chemischen Einwirkung von Schmierölen und Feuchtigkeit, Lagerschäden hervorrufen (Bild 1) [2]. Dies hätte eine erhebliche Verkürzung der Lagerlebensdauer zur Folge.
Eine Möglichkeit zur Verhinderung solcher Schäden ist eine verbesserte Oberflächenbeschaffenheit, die für einen besseren Einlauf sorgt, sich durch Korrosionsbeständigkeit auszeichnet und gegenüber ungünstigen chemischen Reaktionen durch aggressive Schmierstoffmedien inert ist. Aufgrund langjähriger Zusammenarbeit mit der Windindustrie betrachtet SKF das Brünieren als eine von vielen Lösungen zur Verbesserung der Betriebssicherheit.
Das Brünierverfahren
Beim Brünieren handelt es sich um eine Oberflächenbehandlung, die infolge einer chemischen Reaktion zur Bildung einer schwarzen Oxidschicht auf der Lagerstahloberfläche führt. Diese Schicht bildet sich beim Eintauchen der zu behandelnden Teile in eine alkalisch-wässrige Salzlösung bei einer Temperatur zwischen etwa 130 °C und 150 °C. Die chemische Reaktion zwischen dem Eisen, der Eisenlegierung und den Reagenzien lässt eine Oxidschicht aus dem Oberflächenmaterial der Lagerkomponenten entstehen, die aus einer wohldefinierten Mischung aus FeO, Fe2O3 und Fe3O4 besteht. Das Ergebnis ist eine tiefschwarze Schicht mit einer Stärke von etwa 1–2 μm. Das Verfahren besteht insgesamt aus rund 15 unterschiedlichen Eintauchvorgängen, wobei diese hinsichtlich Chemikaliengehalt, -konzentration, Temperatur, Eintauchdauer und Fluidverhalten in den einzelnen Behältern variieren können [3].
Die Vorteile des Brünierens
Nachfolgend werden nur die wichtigsten Vorteile des Brünierens für die Windindustrie aufgeführt. Diese werden in drei Gruppen unterteilt und zeigen, wie die Risiken der einzelnen Ausfallmechanismen durch Brünieren verringert werden können.
1. Geringeres Risiko vorzeitiger Ausfälle
Bei manchen Antriebssträngen von Windkraftanlagen kann es aufgrund von Rissen, Ausbrüchen oder weiß anätzenden Rissen, sogenannten „White Etching Cracks“ (WEC), zu vorzeitigen Ausfällen von Windgetriebelagern kommen. WEC zeigen sich im veränderten Stahlgefüge durch Polieren und Ätzen eines Mikroschliffs. Ausfälle können bei verschiedenen Windgetriebelagerstellen auftreten, und zwar in Planetenradlagern, sowie Lagern in der Zwischen- und Ausgangswelle.
In der Windindustrie sind vorzeitige WEC-bedingte Ausfälle ein häufig diskutiertes Thema, das von Windkraftanlagen-, Windgetriebe- und Lagerherstellern sowie von Universitäten und verschiedenen Instituten unabhängig voneinander untersucht wird. Viele aktuelle Hypothesen gehen von an der Oberfläche wirkenden Einflüssen aus, wie etwa dem Eindringen von Wasserstoff und seinen Wechselwirkungen an Einschlüssen unter der Oberfläche, oder rein spannungsbedingten bzw. tribomechanischen Entwicklungen infolge des Lagerbetriebs. Weitere Ausführungen zu gängigen Hypothesen über WEC-bedingte Ausfallursachen sind unter [4] zu finden.
Laufende Untersuchungen und Ausführungen in der Literatur weisen darauf hin, dass unterschiedliche Mechanismen das Risiko für WEC-bedingte Ausfälle verringern können, wie beispielsweise:
- Die Reduzierung tribologischer und chemischer Einflüsse [5] („Passivierung“)
- Eine verminderte Wasserstoffdiffusion in den Lagerstahl [6] („Passivierung“)
- Korrosionsschutz [7]
- Die Stabilisierung des Laufbahngefüges [8].
Eine Brünierung der Lagerkomponenten kann sich positiv auf die oben genannten Einflüsse auswirken. Nachfolgend werden die Vorteile des Brünierens anhand mehrerer Laborversuche und Untersuchungen aufgezeigt.
1.1 Tribochemische Einwirkungen durch Schmierstoffe und Additive
Bei der Entwicklung von Getriebeölen geht es um die Optimierung der Getriebeleistung. In den meisten Fällen werden dem Getriebeöl zur Steigerung der Getriebeleistung Verschleiß- und Korrosionsschutzadditive beigemischt. Es besteht die Möglichkeit, dass sich dies nicht immer günstig auf den Wälzlagerbetrieb auswirkt. Bei Zahnkontakten ist das makroskopische Gleiten erheblich größer (Gleit-Roll-Verhältnis bis zu 30 %) als bei Lagern (Gleit-Roll-Verhältnis bis zu 4 % je nach Lagerart). Daher unterscheidet sich die Dynamik (Bildung und Beseitigung) des Reaktionsschichtenaufbaus bei Zahnrädern von der bei Wälzlagern.
Wenn Lager unter Grenzschmierbedingungen (Grenz- und Mischreibung) betrieben werden, kommt es im Wälzkontakt zu Reaktionen zwischen den Additiven im Getriebeöl und der Stahloberfläche. Die bei der Bildung einer Reaktionsschicht einwirkende chemische Energie verändert zusammen mit der mechanisch eingebrachten Energie vermutlich das Lagerstahlgefüge im oberflächennahen Bereich [9]. Infolgedessen können sich die mechanischen Eigenschaften der Oberfläche und somit auch das tribologische Verhalten (Reibung, Verschleiß und Oberflächenermüdung) verändern. Im ungünstigen Fall kann es durch Veränderungen des Gefüges im oberflächennahen Bereich zu Mikrorissen an der Oberfläche kommen.
Beim Testen von Getriebeölen haben Pasaribu und Lugt [10] eine positive Wechselbeziehung zwischen der Oxidschichtstärke und dem Lagerverhalten nachgewiesen. Es zeigte sich, dass die Passivierung von Lageroberflächen ungünstige Reaktionen zwischen Getriebeölen und Lageroberflächen hemmen kann. Daher verringert eine zuvor aufgebrachte Oxidschicht mit einer Stärke von etwa 1–2 μm (wie eine Brünierung) das Risiko ungünstig verlaufender Reaktionen zwischen Getriebeölen und Lageroberflächen.
Der Vorteil des Brünierens zur Vermeidung von Oberflächenanrissen lässt sich demonstrieren, indem man brünierte Oberflächen grenzgeschmierten tribologischen Kontakten aussetzt. Beispielsweise wurde hierfür ein Kugel-Scheibe-Test mit einem geringfügig aufgebrachten konstanten Schlupf verwendet. Die Kugel und die Scheibe werden unabhängig voneinander angetrieben, wobei das für den Lagerbetrieb wichtige Gleit-Roll-Verhältnis gesteuert werden kann. Bild 2 zeigt die Prüfergebnisse mit Öl, das aggressive Verschleißschutzadditive enthält. Die unbehandelte Stahloberfläche hat Mikrorisse an der Oberfläche, während die brünierte Oberfläche keinerlei Spuren solcher Risse aufweist.
1.2 Wasserstoffversprödung
Als ein Verfahren zur Passivierung von Oberflächen kann Brünieren das Eindringen von atomarem Wasserstoff in den Lagerstahl und chemische Einwirkungen effektiv mindern. Diese Eigenschaft wurde anhand der Prüfergebnisse von C-Ring- und Wasserstoffdurchdringungstests untersucht [11].
Zur Beurteilung der wasserstoffinduzierten Spannungsrisskorrosion (HISCC) im Schmierkontakt wurde ein speziell entwickelter C-Ring-Prüfstand verwendet [12]. Bild 3 zeigt den Innenring eines Zylinderrollenlagers, aus dem ein Stück herausgeschnitten ist. Der Ring wird über eine Schraube belastet, um eine bestimmte Zugspannung auf der Oberfläche zu erzeugen. Unter dieser Zugspannung wird durch die Aufnahme von Wasserstoff im Schmierkontakt die lokale Bildung eines an der Oberfläche beginnenden Sprödanrisses gefördert. Die Lebensdauer des C-Rings, welche definiert ist als die Zeitdauer bis zum Bruch des C-Rings unter einer bestimmten Zuglast, spiegelt die Widerstandsfähigkeit gegenüber HISCC wider. Das Diagramm von Bild 3 zeigt, dass brünierte C-Ringe gegenüber unbeschichteten Ringen eine längere Lebensdauer aufweisen.
Die Beständigkeit der Brünierung gegenüber der Wasserstoffaufnahme lässt sich auch mithilfe eines elektrochemischen Wasserstoffdurchdringungstests beurteilen, wobei der atomare Wasserstoff in einem elektrochemischen Prozess erzeugt wird. Der Wasserstoff durchdringt die Stahlplatte und wird anhand der elektrochemischen Oxidation gemessen, sobald er auf einer anderen Seite der Stahlplatte freigesetzt wird. Bei einer Oberflächenbeschichtung lässt sich der Wasserstoffeinbruch beurteilen, indem man den gemessenen Wasserstoff-Durchdringungsfluss (Strom) mit dem des unbeschichteten Prüflings vergleicht. Bild 4 zeigt, dass Stahlplatten mit einer brünierten Oberfläche einen erheblich schwächeren Wasserstoff-Durchdringungsfluss aufweisen als der unbeschichtete Prüfling. Dies ist so, weil im Unterschied zur Diffundierung in den Stahl atomarer Wasserstoff (zum Proton) ionisiert werden muss, damit er eine Oxidschicht durchdringen kann. Die starke Wechselwirkung zwischen den ionisierten Wasserstoffatomen und den Anionen des Eisenoxids lässt eine Oxidschicht wie eine Barriere wirken, welche eine Wasserstoffdurchdringung verlangsamt [13].
1.3 Schäden durch Feuchtigkeit (Stillstandskorrosion)
Große Temperaturgefälle bewirken, dass Wasser aus feuchter Luft kondensiert. Auch wenn die Gefahr eines erhöhten Wassergehalts bei Anwendungen in Windkraftanlagen oft nicht direkt genannt wird, weiß man, dass gelöstes Wasser die Funktionsfähigkeit von Verschleißschutzadditiven beeinträchtigen kann [14], und dass freies Wasser die Korrosion und die Wasserstoffaufnahme fördert [15][16]. Das Korrosionsrisiko nimmt zu, wenn es während Wartungsarbeiten an der Windkraftanlage oder bei Windstille zu Stillständen kommt [7].
Das Gefüge der schwarzen Oxidschicht besitzt eine gewisse Porosität, welche die Affinität des Schmierstoffs oder des Korrosionsschutzmittels auf der Beschichtung verbessert und damit auch die Beständigkeit gegen Feuchtigkeit oder Stillstandskorrosion. Bei einem Salzsprühnebeltest [17] zeigten brünierte Prüflinge eine erheblich bessere Korrosionsbeständigkeit als unbeschichtete Prüflinge (Bild 5).
2. Erschwerte Betriebsbedingungen bei Mangelschmierung oder Oberflächenschäden
2.1 Adhäsiver Verschleiß; Schäden aufgrund von Anschmierungen oder Schlupf
Wenn Rollenlager mit einer zu geringen Belastung, das heißt, unter der erforderlichen Minimallast, betrieben werden, kann dies einen erheblichen Unterschied in den Abwälzgeschwindigkeiten zwischen Innenring und Rollensatz hervorrufen, was wiederum ein hohes Gleiten zwischen den Wälzkörpern und dem Innenring zur Folge hat [18]. Bei anspruchsvollen Anwendungen, wie etwa der Ausgangswelle eines Windgetriebes, können Leerlaufbedingungen und Lastzonenwechsel mitunter zu hohen Gleitwerten führen. Folglich besteht ein großes Schadensrisiko durch Anschmierungen [19] [20].
Die Ergebnisse der Windgetriebe-Leerlauftests haben gezeigt, dass eine Brünierung der Wälzlager von Ausgangswellen einen verbesserten Schutz vor Anschmierungen bietet. Bild 6 zeigt den auf einer unbeschichteten Rolle und den Innenringoberflächen entstandenen Schaden im Leerlaufbetrieb nach 45 Minuten, während brünierte Ringe selbst nach 30 Stunden keinen erheblichen Schaden aufwiesen.
Der Schutzmechanismus der brünierten Oberflächen lässt sich dadurch erklären, dass nach dem Einlaufen eine verminderte Reibung auftritt und der Schmierstoff besser an der Oberfläche haftet als bei unbeschichteten Oberflächen.
2.2 Oberflächenzerrüttung
Bei der Oberflächenzerrüttung handelt es sich um eine mit schlechten Schmierbedingungen und Grenz-/Mischreibung einhergehende, unterhalb der Oberfläche beginnende Ermüdung im Oberflächenrauheitsbereich [21]. Sie tritt insbesondere an Verzahnungen, manchmal aber auch bei Lagern auf. Im letzteren Fall kann sie sich besonders nachteilig auf die Lagerfunktion auswirken.
Auch wenn die Oberflächenzerrüttung nicht unbedingt zu den Hauptausfallarten bei Wälzlagern zählt, so kann sie doch das Auftreten anderer Ausfallmechanismen, wie etwa Eindrückungen durch Fremdkörper, Ausbrüche im oberflächennahen Bereich und Mikrofressschäden, begünstigen oder beschleunigen [22]. Die Gefahr des Auftretens einer Oberflächenzerrüttung lässt sich auf verschiedene Weise vermindern, beispielsweise durch eine Reduzierung der Oberflächenreibung, eine bessere Verteilung der oberflächennahen Spannungen bzw. eine Verringerung der Festkörperkontaktdrücke oder eine Optimierung des Einlaufprozesses. Eine Möglichkeit, um dies zu erreichen, ist die Aufbringung von schützenden Beschichtungen, wie etwa eine Brünierung.
Obwohl die Oberflächenzerrüttung im Allgemeinen theoretisch und experimentell schon ausgiebig untersucht wurde (siehe z. B. Literaturhinweise unter [21]), wurde der Einfluss von Beschichtungen auf diesen Ausfallmechanismus bislang noch nicht ausreichend erforscht. Daher wurde eine Reihe von Versuchen mit brünierten Rollen [23] auf einem geeigneten Prüfstand unter Laborbedingungen durchgeführt [14] [21], einschließlich des kontrollierten Gleit-Roll-Verhältnisses, der Schmierbedingungen, Temperatur, Belastung und Drehzahl. Die Belastungseinheit des verwendeten Prüfstands ist in Bild 7 schematisch dargestellt: Eine sich drehende Rolle befindet sich in Kontakt mit drei aus gehärtetem Lagerstahl gefertigten Scheiben. Der Prüfling besteht aus einer kleinen Rolle (mit einem Durchmesser von 12 mm), die aus einem Pendelrollenlager stammt, und drei größeren Gegenlaufkörpern, die den Innenringen von Zylinderrollenlagern entsprechen. Die Rolle und die Ringe können durch Schleifen und/oder Honen endbearbeitet werden, um ein gewünschtes Rauheitsmuster zu erzielen. Die geprüften Rollen und Gegenlaufkörper sind aus Lagerstahl nach ANSI-52100 gefertigt. Die Schmierbedingungen während der Prüfungen variierten von Grenzschmierbedingungen bis hin zu Mischreibung. Anschließend wurden die Rollenoberflächen auf Oberflächenzerrüttung geprüft und die Prüfergebnisse von beschichteten und unbeschichteten Rollen unter gleichen Bedingungen miteinander verglichen.
Wie in Bild 7 dargestellt, zeigen die mit diesem Prüfstand erzielten Versuchsergebnisse, dass die Brünierung einen gewissen Schutz vor Oberflächenzerrüttung über das gesamte Spektrum der Prüfbedingungen [23] bietet.
Darüber hinaus wurde bei den beschichteten Oberflächen [23] eine parametrische Analyse des Oberflächenzerrüttungsmodells [22] durchgeführt, einschließlich der Einflüsse von Reibung sowie der Steifigkeit und Dicke der Beschichtung. Dabei wurde festgestellt, dass das Vorhandensein einer optimalen Beschichtungsdicke für eine minimale Oberflächenzerrüttung sorgt. Anhand von experimentellen und theoretischen Ergebnissen konnte nachgewiesen werden, dass eine Brünierung gegenüber unbeschichteten Lagerstahloberflächen eine gesteigerte Schadensfreiheit hinsichtlich Oberflächenzerrüttung bewirkt und somit die Bandbreite der Einsatzbedingungen vergrößert.
3. Lagertest und praktische Erfahrungen
Brünierte Lager wurden unter starker Mischreibung in einem Lebensdauertest getestet. Die Ergebnisse bestätigten den Vorteil brünierter Lager im Vergleich zu unbeschichteten Lagern beim Einlaufvorgang [24] und bei niedrigen Kappa-Bedingungen.
Bei diesem Test liefen alle brünierten Lager ohne Ausfall die festgelegte Testdauer durch. Die Prüfergebnisse zeigten eine geschätzte nominelle Lebensdauer L10, die ca. 2–3 Mal höher war als die von unbeschichteten Lagern.
Neben dem oben genannten Komponententest und den Lagerprüfergebnissen belegen auch praktische Erfahrungen den Vorteil einer Brünierung im Hinblick auf eine Verringerung des Risikos vorzeitiger Ausfälle. In den Berichten von Herstellern von Windgetrieben und Windkraftanlagen wird bestätigt, dass bei der Verwendung brünierter Lager im Vergleich zu unbeschichteten Lagern eine erhebliche Verbesserung bei der Senkung der Lagerausfallrate feststellbar ist [25] [26].
Ferner wurde bei [8] und [25] festgestellt, dass eine schonende Wiedererwärmung unterhalb der Anlass- oder Umwandlungstemperatur das Stahlgefüge ohne Härteverlust optimieren und festigen kann, und dass sich dadurch eine Verlängerung der Lagerermüdungslebensdauer ergibt. Diesem Konzept folgend kann eine Brünierung bei einer ähnlichen Temperatur zu vorteilhaften Veränderungen im oberflächennahen Bereich des Stahlgefüges führen, was sich in einer Verringerung der Halbwertsbreite (FWHM oder b/B) der XRD-Peaks um >0,1 Grad zeigt.
Schlussfolgerung
Anhand von Laboruntersuchungen, Lagertests und praktischen Erfahrungen wurden einige Vorteile einer Brünierung nachgewiesen. Eine Brünierung bietet einen gewissen Schutz vor tribochemischen Einwirkungen, verringert die Wasserstoffdurchdringung und verbessert die Resistenz gegen feuchtigkeitsbedingte Schäden (z. B. Stillstandskorrosion). Außerdem erhöhen brünierte Lagerstahloberflächen den „sicheren Arbeitsbereich“ bei Ausfallarten wie etwa adhäsivem Verschleiß/Anschmierungen oder Oberflächenzerrüttung. Positive praktische Erfahrungen bestätigen diese Feststellungen.
Zusammenfassend lässt sich sagen, dass das von SKF eingesetzte Brünierverfahren die Lagerkomponenten besser vor Schäden schützt. Brünierte Lager werden nicht nur in der Erstausrüstung eingesetzt, sondern auch als Ersatz für herkömmliche Lager im Rahmen der Wartungsroutinen von Windparks. Dies bedeutet, dass die Vorteile einer Brünierung bei sämtlichen Lagerarten genutzt werden können, die in kritischen Windgetriebesystemen in der gesamten Windbranche eingesetzt werden. Dabei sollen auf Empfehlung von SKF nicht nur brünierte Innen- und Außenringe, sondern auch brünierte Wälzkörper verwendet werden, um eine optimale Lagerleistung zu erzielen.
Referenzen
[1] J.Rosinski, D.Smurthwaite, Troubleshooting wind gearbox problems, Gearsolutions 2010
[2] K.Stadler, Wie brünierte Lager dazu beitragen, Betriebs- und Wartungskosten für Windkraftanlagen zu senken, Evolution #4 2013
[3] DIN 50938, Brünieren von Bauteilen aus Eisenwerkstoffen
[4] K.Stadler, A.Stubenrauch, Premature failures in industrial gearboxes, Antriebstechnisches Kolloquium Aachen, ATK 2013 und SKF Evolution #2 2013
[5] W.Holweger, Interaction of rolling bearing fatigue life with new material phenomenons, VDI Kongress „Antriebsstränge in Windenergieanlagen“ 2012
[6] H.Uyama, The mechanism of white structure flaking in rolling bearings, NREL workshop, Broomfield November 2011
[7] I.Strandell, C.Fajiers, T.Lund, Corrosion – one root cause for premature bearing failures, 37th Leeds-Lyon Symposium on Tribology, 2010
[8] J.Gegner, L.Schlier, W.Nierlich, Evidence and analysis of thermal static strain aging in the deformed surface zone of finish-machined hardened steel, PowderDiffraction 24-2009 pp45-50
[9] M.Reichelt, T.E.Weirich, J.Meyer, T.Wolf, J.Loos, P.W.Gold, M. Fajfrowski, TEM and nanomechanical studies on tribological surface modifications formed on roller bearings under controlled lubrication conditions. J. Mater. Sci. 41, 4543-4553 (2006)
[10] H.R.Pasaribu, P.M.Lugt, The Composition of Reaction Layers on Rolling Bearings Lubricated with Gear Oils and Its Correlation with Rolling Bearing Performance, Tribology Transaction, Vol. 55, 3, 351-356, 2012
[11] ASTM G38, „Standard practice for making and using C-ring stress-corrosion test specimens“ und ASTM G148, „Standard practice for evaluation of hydrogen uptake, permeation and transport in metals by an electrochemical technique“
[12] B.Han, B.X.Zhou, R.Pasaribu, C-ring Hydrogen Induced Stress Corrosion Cracking (HISCC) – Tests in Lubricating Liquid Media, EuroCorr 2011 Proceeding
[13] R-H.Song, S-I.Pyung, R.A.Oriani, The hydrogen permeation through passivating film on iron by modulation method, Electrochemica Acta Vol 36, No. 5/6, pp. 825-831, 1991
[14] V.Brizmer, R.Pasaribu, G.E.Morales, Micropitting Performance of Oil Additives in Lubricated Rolling Contacts, Tribology Transactions, Vol. 56, 5, pp. 739-748, 2013
[15] R.J.K.Wood, Tribology and corrosion aspects of wind turbines, Wind Energy – Challenges for Materials, Mechanics and Surface Science, IoP, London 2010
[16] D.A.Jones, Principles and Prevention of Corrosion – 2nd Ed., Page 335, ISBN: 0-13-359993-0, 1996
[17] ASTM B117-09, Standard Practice for Operating Salt Spray (Fog) Apparatus
[18] M.Volkmuth, K.Stadler, R.Heemskerk, Slippage measurements in roller bearings, Antriebstechnisches Kolloquium ATK Aachen 2009
[19] R.Hambrecht, Anschmiererscheinungen in Wälzlagern bei Fettschmierung, Dissertation, Erlangen 1999
[20] B.J.Scherb, J.Zech, A study on the smearing and slip behavior of radial cylindrical roller bearings, Schaeffler Gruppe 2001
[21] G.E.Morales, K.Stadler, V.Brizmer, Understanding and preventing surface distress, Gear solutions 2012
[22] G.E.Morales-Espejel, V.Brizmer, Micropitting Modelling in Rolling-Sliding Contacts: Application to Rolling Bearings, Trib. Trans., 54, pp. 625-643, 2011
[23] V.Brizmer, A.Rychahivskyy, B.Han, Anti-Micropitting Performance of Black Oxide Coating, Word Tribology Congress, Turin 2013
[24] H.v.Lier, C.Hentschke, Untersuchungen zum Betriebsverhalten brünierter Wälzlager, VDI-Bericht Nr. 2202, 2013
[25] J.Luyckx, Hammering Wear Impact Fatigue Hypothesis WEC/irWEA failure mode on roller bearings, NREL workshop, Broomfield November 2011
[26] SKF Kommunikation mit führenden Herstellern der Windenergiebranche.