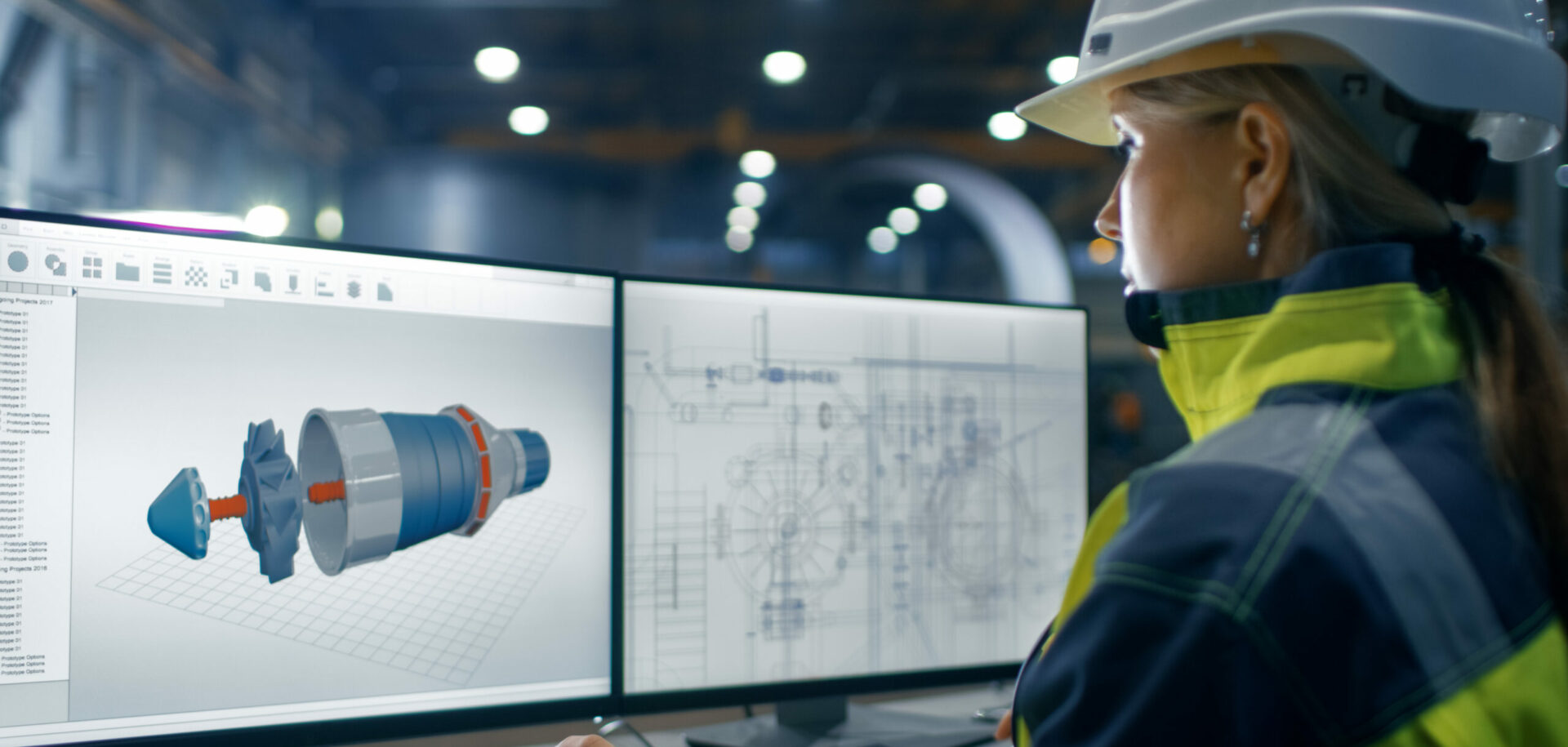
Energy-efficient minimal quantity lubrication for high-speed spindles
The exact supply of minimal quantities of appropriate lubricant is one of the essential requirements for the optimal operation and long service life of high-precision bearings. This led SKF to develop an innovative oil microdosage system.
Summary
The SKF Microdosage System addresses the shortcomings of oil+air lubrication and meets the machine tool industry’s increasing demands for greater efficiency, increased service life and reduced energy consumption. The system is capable of generating four high-precision, nearly continuous volumetric flows with constant quality monitoring in the range of 0.5 to 5 mm³/min.
For high-speed precision spindles operating at speed factors above 2 million n×dm (more than 30,000 r/min on conventional tool spindles), reliable lubrication with precisely matched lubricant quantities in a very consistent flow is crucial for optimal bearing operation. Within the optimal quantity range, the frictional moment in the bearings is the lowest possible, without causing mixed friction and thus avoiding increased wear (fig. 1).
In addition to spindle systems equipped with bearings that are lubricated for life, relubrication systems are usually employed, especially at high speed factors. In these systems, a defined quantity of lubricant is delivered to the bearings at a defined interval, based on the arrangement design, bearing type, loads and operating conditions. Shorter lubrication intervals and smaller lubricant quantities provide a more continuous and reliable lubrication cycle.
Current problem
Oil+air lubrication is a widely used form of spindle lubrication. It consists of defined quantities of oil that are transported to the bearings via tubing containing a constant flow of compressed air. The airflow transports lubricant and also spreads the small quantities of oil into an oil streak that increases the continuity of lubricant delivery (fig. 2). The airflow rate and the timing required to generate the quantity of oil can be adjusted to the particular lubrication task and application, providing a very flexible system usage.
However, these systems also have a number of drawbacks. These include long response times to modified dosage, such as timing, limited metering accuracy and a constantly higher consumption of compressed air (regardless of timing), and the volumetric flow of lubricant is typically monitored on a purely comparative basis.
The solution: SKF Microdosage System
SKF has developed a new lubrication system – the SKF Microdosage System – to address the shortcomings of oil+air lubrication and meet the machine tool industry’s increasing demands for greater efficiency, increased service life and reduced energy consumption. The system is capable of generating four highprecision, nearly continuous volumetric flows with constant quality monitoring in the range of 0.5 to 5 mm³/min. This corresponds to about one-hundredth to one-tenth of an oil droplet per minute. Core components of the system are precision microvalves that, together with a flow sensor and complex controls, can deliver quantities of lubricant down to a few nanolitres (fig. 3).
The microvalves are opened for a defined time in the microsecond range, which creates a metering pulse with a defined quantity of lubricant and causes this lubricant to enter the connected lubricant capillary line. Many metering pulses are generated in very quick succession (a matter of milliseconds), creating a nearly continuous volumetric flow in the capillary line leading to the lubrication point (fig. 4).
Since the microvalves cannot generate pressure on their own, priming pressure must be applied to the lubricant fed to the lubrication system. This is done by a special reservoir. In the first product design, this priming pressure is generated quasi-statically and linearly using compressed air in the reservoir. With an upstream throttle valve, the compressed air functions as an excellent linear spring. The microdosage system thus consists of a metering unit and a reservoir. Both components are connected to the machine control unit, through which they can be controlled and monitored (fig. 5). This allows the quantity of lubricant to be adjusted almost in real time (via a machine program), for example.
The modular design also enables decentralized installation of the individual modules. The metering unit with safety class IP67 is mounted on or near the spindles, and the reservoir can be positioned outside the machine, for example in the fluid cabinet (fig. 6).
Permanent monitoring and self-calibration
The high and constant precision with minimum volumetric flows is achieved by considering numerous parameters. In addition to the open times of the microvalves, the oil viscosity, ambient temperature and other factors influence the quantity of lubricant delivered. There may also be fluctuations in priming pressure from the compressed air system and possible manufacturing tolerances (e.g., on the valves). In order to deal with these, the system constantly monitors and calibrates itself. The integrated volumetric flow sensor records the quantities delivered through the individual valves and compares these measurements with stored target and reference values. If predefined tolerances are exceeded, the system adjusts the valve open time per pulse. The calibration is performed for each active outlet (valve) separately and sequentially (fig. 7).
Ultimately, this provides each valve with its own parameter set, e.g., a specific open time per pulse. The output quantities measured at the flow sensor or the outlets then correspond to the target value (fig. 8).
Additionally, the calibration process is triggered by events, such as switching the system on after a period of downtime or in case of a temperature change of ± 5 Kelvin as detected by an integrated temperature sensor. The firmware of the metering unit stores such events. The system calibrates itself automatically every four hours of operation.
Initial application results
To demonstrate the effects of micrometering on the spindle bearings in the total speed range, SKF conducted comparative tests using a simplified, belt-driven spindle bearing without temperature control. The bearing temperature on the outer ring was selected as the comparison value, because it is relatively easy to measure and provide initial information on the state of lubrication. The lubricant was fed through the outer ring of the bearing. The speed range of 0 to 2.4 million n×dm was passed through in increments of 3,000 r/min. Each speed level was maintained for 30 minutes to make sure that the system reached a steady state. The resulting speed of the bearing with a mean diameter of 54 mm was between 0 and 45,000 r/min. The microdosage system was operated with different quantity settings than a conventional oil+air system.
Results: At low speed factors, between 0.5 and 1.0 million n×dm (with a minimum lubricant quantity of 30 mm3/h), the recorded bearing temperature was approximately 2 to 3 Kelvin lower. At higher speed factors, between 1.8 and 2.4 million n×dm (with metered quantities adjusted accordingly), the bearings remained up to 8 Kelvin cooler thanks to the microdosage system (fig. 9).
Potential savings
Continuous, demand-based lubrication using the SKF Microdosage System can do more than minimize the quantities of lubricant fed. In particular, it can eliminate the energy-intensive generation of compressed air as needed in conventional oil+air systems. The compression, filtering and drying of compressed air requires approximately 0.1 kWh per Nm³. At domestic electricity prices in central Europe, for instance, the use of the SKF Microdosage System can save up to 130 euros per year and per lubrication point. Since tool spindles are typically equipped with three or four bearings, savings of up to 390 or 520 euros per year can ultimately be achieved.
Further, the absence of compressed air brings substantial benefits in terms of lower emissions. At speed factors up to approximately 2 million n×dm, the measurements on the test bench demonstrated a reduction in noise emissions of up to 10 dB(A) compared with conventional oil+air systems.
The new SKF Microdosage System thus makes a significant contribution to the energy-efficient, low-emission, high-precision lubrication of high-speed bearings. This potential is best exploited when the new SKF Microdosage System and the spindle bearing arrangement are harmonized.