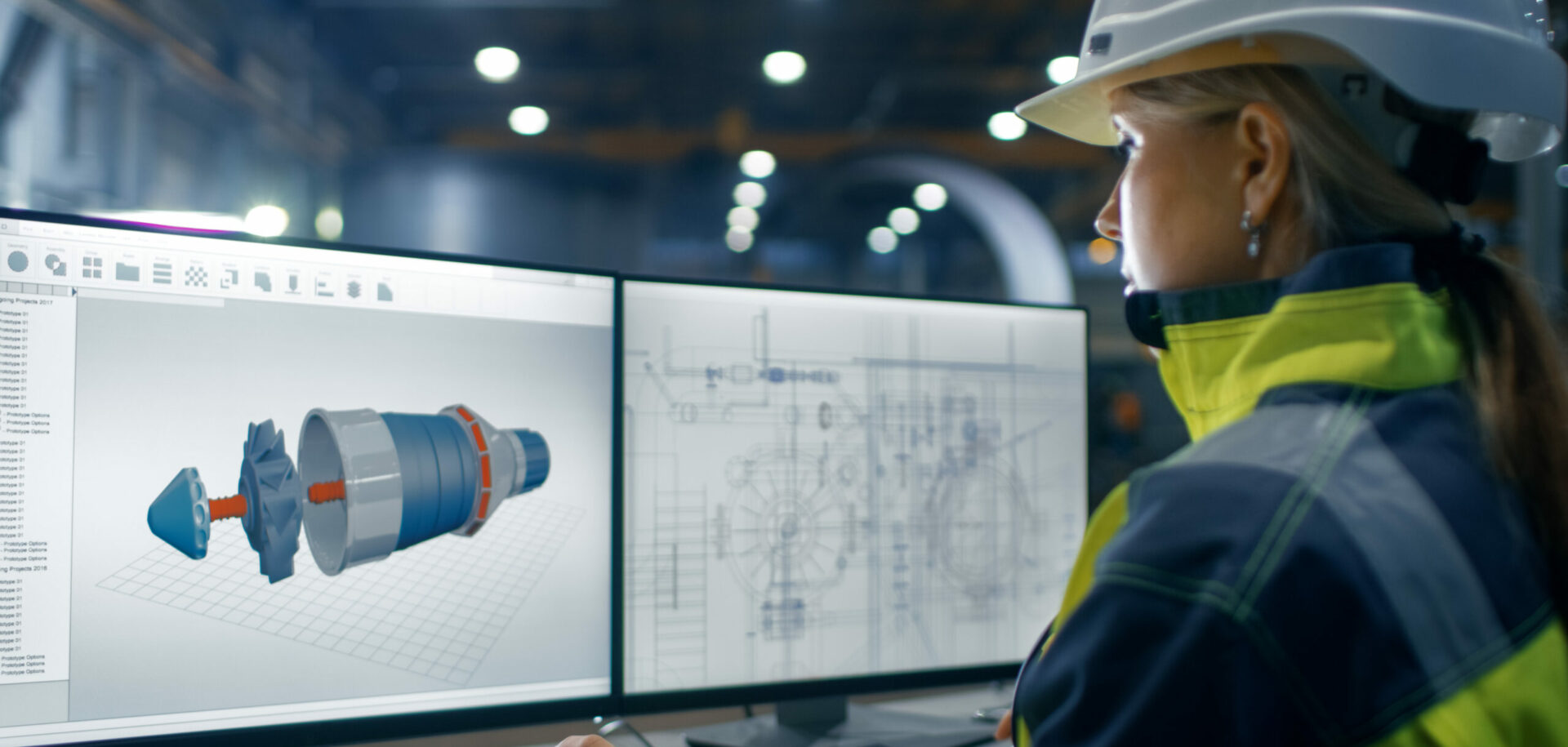
Avantages offerts par l’utilisation de roulements « black oxide » dans les applications d’éoliennes
L’augmentation constante de la taille des éoliennes visant à accroître la capacité de production d’énergie s’accompagne d’une hausse des efforts appliqués sur les organes de transmission.
Résumé
Pour répondre aux exigences opérationnelles difficiles du secteur éolien, SKF utilise un procédé de traitement spécial, baptisé « black oxide ». Par le biais de ce procédé, les éléments du roulement sont revêtus d’une couche résistante aux agents chimiques et à la corrosion qui protège le roulement des défaillances prématurées dès les premières phases d’exploitation.
En fonctionnement, les éoliennes sont soumises à des températures, des vitesses de vent et à des charges extrêmement variables [1]. Ces conditions de service, combinées aux potentiels effets néfastes de la contamination solide, de l’usure tribochimique due à la chimie de l’huile et de la contamination par l’eau, pourraient endommager les roulements (Fig. 1) [2] et réduire ainsi considérablement leur durée de service.
L’un des prérequis, pour éviter ces défaillances, réside dans l’obtention de meilleures propriétés mécaniques des surfaces et ainsi d’obtenir une amélioration du processus de rodage, une meilleure résistance à la corrosion et une sensibilité moindre aux substances chimiques agressives contenues dans les lubrifiants. La collaboration de longue date entre SKF et l’industrie de l’énergie éolienne ont permis d’identifier le traitement « black oxide » comme étant une des solutions pour améliorer la fiabilité des installations.
Processus « black oxide »
Le processus « black oxide » est un traitement de surface basé sur une réaction chimique qui s’opère au niveau de la couche d’acier superficielle des roulements. Ce procédé d’oxydation par brunissage consiste à immerger des pièces dans une solution aqueuse de sels alcalins à une température comprise entre 130 et 150 °C environ. La réaction entre le fer de l’alliage ferreux et les réactifs produit sur la surface extérieure des éléments de roulement une couche d’oxyde composée d’un mélange défini de FeO, Fe2O3, produisant du Fe3O4. On obtient ainsi un revêtement noir foncé d’environ 1–2 μm d’épaisseur. Le procédé consiste au total en une quinzaine d’étapes d’immersion différentes ; pour bon nombre de ces étapes, il est possible de paramétrer les substances chimiques, la concentration, la température, la durée de l’immersion et le comportement du fluide à l’intérieur du réservoir [3].
Avantages du revêtement « black oxide »
Nous nous contenterons ici de présenter ses avantages les plus significatifs pour l’industrie éolienne. Ils sont décrits succinctement en trois catégories et montrent comment le revêtement à l’oxyde noir peut contribuer à réduire les risques relatifs à chaque mécanisme de défaillance.
1. Réduction des risques de défaillances prématurées
Dans les organes de transmission d’éoliennes, les roulements du multiplicateur, par exemple, peuvent présenter des défaillances prématurées causées par des fissures, des écailles ou des fissures à partir de phase blanche – dites White Etching Crack (WEC) – irrégulières. Le terme de « fissure blanche » fait référence à l’aspect de la microstructure altérée de l’acier après polissage et attaque d’une microsection. Ces défaillances peuvent être observées en différentes positions de roulements au sein du multiplicateur : roulements des roues planétaires, de l’arbre intermédiaire et de l’arbre grande vitesse.
Les défaillances prématurées, dues aux fissures WEC, sont l’objet de nombreux débats au sein de l’industrie éolienne et de recherches menées de façon indépendante par les fabricants d’éoliennes, les fabricants de multiplicateurs et les fabricants de roulements, sans oublier les universités et organismes tiers. Bon nombre des hypothèses actuelles se concentrent sur des phénomènes concernant la surface, comme la pénétration d’hydrogène et l’interaction avec des inclusions en sous-couche ou des développements de contraintes/tribomécaniques purs liés au comportement de la surface. Pour plus d’informations sur les hypothèses relatives aux causes des défaillances WEC, consultez la référence [4].
D’après des recherches en cours et des informations tirées de la littérature, différents mécanismes peuvent contribuer à réduire les risques de défaillances WEC :
- réduction de l’usure tribologique et de l’attaque chimique [5] (« passivation ») ;
- réduction de la diffusion d’hydrogène dans l’acier des roulements [6] (« passivation ») ;
- protection anti-corrosion [7] ;
- stabilisation de la microstructure des pistes [8].
Le revêtement « black oxide » peut contribuer à protéger les roulements du processus de défaillance susmentionné. Les avantages du revêtement « black oxide » sont confirmés par les différents essais en laboratoire et recherches repris ci-dessous.
1.1 Usure tribochimique causée par le lubrifiant et les additifs
Les huiles pour engrenages sont formulées pour optimiser les performances de ces derniers. Dans la plupart des cas, des additifs anti-usure et des inhibiteurs de corrosion sont ajoutés à l’huile afin d’améliorer les performances des engrenages. Malheureusement, la formulation chimique des huiles pour engrenages ne contribue pas toujours au bon fonctionnement des roulements. Le glissement macroscopique qui s’opère au niveau des contacts d’engrènement (rapport glissement sur roulement pouvant atteindre jusqu’à 30 %) est nettement plus élevé que dans les roulements (rapport glissement sur roulement de 4 % max., selon le type de roulement). Par conséquent, la dynamique (formation et élimination) des couches de réaction dans les engrenages est différente de celle observée dans les roulements.
Lorsque les roulements fonctionnent dans des conditions de lubrification médiocres (mixte ou limite), des réactions s’opèrent entre les additifs contenus dans l’huile pour engrenages et la surface en acier au niveau des contacts roulants. L’énergie chimique qui accompagne la formation d’une couche de réaction et l’énergie tribologique modifient probablement la microstructure de l’acier à proximité immédiate de la surface [9] qui entraîne à son tour une altération des propriétés mécaniques de la surface et, par conséquent, des performances tribologiques (frottement, usure et fatigue en surface). Si les réactions qui s’opèrent sont défavorables, la microstructure à proximité immédiate de la surface est altérée de manière significative et des microfissures apparaissent en surface.
Grâce à des tests réalisés sur les huiles pour engrenages, Pasaribu et Lugt [10] ont montré la corrélation positive entre épaisseur des couches d’oxyde et performances des roulements. Il en ressort que la passivation des surfaces des roulements retarde les réactions défavorables entre ces surfaces et les huiles pour engrenages. Par conséquent, des couches d’oxyde de ~1–2 μm, comme le revêtement « black oxide », réduisent le risque de réaction négative entre les surfaces des roulements et les huiles pour engrenages.
L’impact du traitement « black oxide » dans la prévention de l’apparition de fissures superficielles peut être évalué en soumettant les surfaces traitées à des conditions de lubrification limite au niveau des contacts tribologiques. Il est possible par exemple de réaliser un test avec un tribomètre bille-disque oblique lubrifié. La bille et le disque sont entraînés séparément, ce qui permet de contrôler le rapport glissement sur roulement qui constitue un paramètre important dans le fonctionnement du roulement. La Fig. 2 présente les résultats des tests réalisés avec de l’huile contenant des additifs anti-usure agressifs. La surface en acier non traitée présente des microfissures superficielles, tandis qu’aucune microfissure n’apparaît sur la surface traitée « black oxide ».
1.2 Fragilisation par l’hydrogène
Le brunissage par oxydation superficielle, en tant que traitement de « passivation » de la surface, peut permettre de réduire efficacement la diffusion de l’hydrogène atomique et l’attaque chimique de l’acier des roulements. Cette propriété a été évaluée dans les résultats d’essais de type C-ring (anneau en C) et de perméation de l’hydrogène réalisés en laboratoire [11].
Un banc d’essai C-ring a été spécialement mis au point pour étudier les fissures de corrosion dues à l’hydrogène (HISCC) dans les contacts lubrifiés [12]. La Fig. 3 montre une bague intérieure de roulement à rouleaux cylindriques avec un segment manquant. Une charge est exercée sur la bague à l’aide d’une vis de manière à soumettre la surface à une contrainte de traction définie. Les fissures initiées en surface sous l’effet de la contrainte de traction sont favorisées par la présence d’hydrogène liée à l’environnement de lubrification. La durée de vie de la bague ouverte, qui correspond à la durée écoulée avant l’apparition d’une fissuration de cette bague sous une contrainte de traction donnée, constitue la résistance à la fissuration HISCC. Comme le montre le graphique de la Fig. 3, les bagues ouvertes traitées « black oxide » présentent une durée de vie supérieure par rapport à l’échantillon non traité.
La résistance du traitement « black oxide » à la pénétration d’hydrogène peut également être évaluée par le biais d’un test de perméation électrochimique de l’hydrogène pour lequel l’hydrogène atomique est généré par une charge électrochimique. L’hydrogène pénètre la plaque d’acier par perméation. Le flux de perméation est mesuré à travers l’oxydation électrochimique au moment de son apparition de l’autre côté de la plaque. La pénétration de l’hydrogène dans un revêtement de surface peut être évaluée en comparant le flux de perméation de l’hydrogène mesuré avec celui de l’échantillon non revêtu. La Fig. 4 montre un flux de perméation de l’hydrogène nettement inférieur pour les plaques en acier revêtues d’oxyde noir par rapport à l’échantillon non revêtu. Ceci s’explique du fait que, contrairement à la diffusion dans l’acier de base, l’hydrogène atomique doit être ionisé (proton) pour pouvoir traverser la couche d’oxyde. L’interaction solide entre les atomes d’hydrogène ionisé et les anions dans l’oxyde de fer permet à la couche d’oxyde noir d’agir comme une barrière à la perméation de l’hydrogène [13].
1.3 Corrosion due à l’humidité (corrosion à l’arrêt)
Des écarts de température importants favorisent la condensation de l’eau contenue dans l’air humide. Bien que le risque de contamination par l’eau soit rarement directement évoqué en ce qui concerne les applications éoliennes, les effets néfastes potentiels de l’eau dissoute sur les performances des additifs anti-usure [14] sont bien connus, de même que la présence d’eau favorise l’apparition de corrosion et la pénétration de l’hydrogène [15] [16]. Le risque de corrosion est accru à l’arrêt, lorsque l’éolienne est immobilisée pour une intervention de maintenance ou en l’absence de vent [7].
La microstructure du revêtement « black oxide » présente une certaine porosité, ce qui contribue à une meilleure adhésion et distribution du lubrifiant (et/ou des agents conservateurs) sur le revêtement et améliore ainsi la résistance à l’humidité ou à la corrosion à l’arrêt. Lors d’un test au brouillard salin [17], des échantillons traités ont présenté une résistance à la corrosion nettement supérieure par rapport aux échantillons non revêtus (Fig. 5).
2. Conditions de service sévères avec une lubrification insuffisante, ou fatigue de surface
2.1 Usure par adhérence ; dommages dus au grippage ou au glissement
Lorsqu’un roulement à rouleaux est soumis à une charge insuffisante (inférieure à la charge minimale requise), les vitesses de rotation de la bague intérieure, d’une part, et du jeu de rouleaux, d’autre part, peuvent présenter des écarts considérables entraînant un glissement important entre les éléments roulants et la bague intérieure [18]. Dans des applications exigeantes, comme les arbres à grande vitesse des multiplicateurs d’éoliennes, un fonctionnement au ralenti ou des zones de charge variables peuvent parfois favoriser un glissement important. Il en résulte alors un risque élevé de dommage par grippage [19] [20].
Des essais réalisés sur des multiplicateurs d’éoliennes au ralenti ont démontré l’effet protecteur contre les dommages par grippage du traitement « black oxide » des roulements pour arbres à grande vitesse. La Fig. 6 montre un dommage par grippage apparu sur les surfaces non revêtues des rouleaux et de la bague intérieure après 45 minutes de fonctionnement au ralenti, tandis que des bagues traitées ne présentent aucun dommage significatif après 30 heures de fonctionnement.
Cet effet protecteur du traitement « black oxide » s’explique par un frottement réduit après rodage et une meilleure adhésion du lubrifiant à la surface par rapport à des surfaces non revêtues.
2.2 Fatigue de surface
La fatigue de surface est une altération de la surface des pistes qui se distingue par de petits cratères peu profonds (contact entre les aspérités) suite à des conditions de lubrification inadaptée [21]. Les dentures d’engrenages y sont particulièrement sujettes, mais elle peut également toucher parfois les roulements. Si des roulements sont touchés, les répercussions peuvent être particulièrement dommageables.
Même s’il ne s’agit pas d’un mode de défaillance primaire pour les roulements, il peut favoriser ou accélérer l’apparition d’autres modes de défaillance comme l’indentation par des corps étrangers, l’écaillage initié en surface et le grippage [22]. Il existe plusieurs moyens de réduire le risque de fatigue de surface comme la réduction du frottement, la redistribution des contraintes à proximité de la surface, la réduction des pressions dues à une lubrification mixte et l’optimisation du processus de rodage. Pour y parvenir, l’une des solutions consiste à recourir à des traitements protecteurs comme par exemple le traitement « black oxide ».
Malgré l’étendue des travaux théoriques et expérimentaux disponibles concernant la fatigue de surface en général (cf. par ex. la revue de la littérature de la réf. [21]), peu d’études ont été consacrées jusqu’ici à l’influence des revêtements sur l’altération de la surface. Pour remédier à cette lacune, une série de tests a, par conséquent, été effectuée sur des rouleaux traités « black oxide » [23], à l’aide d’un banc d’essai de fatigue de surface, dans des conditions de laboratoire [14] [21], autrement dit avec un rapport glissement sur roulement, des conditions de lubrification, une température, une charge et une vitesse contrôlés. Le dispositif d’application de la charge du banc d’essai de fatigue de surface est représenté de façon schematique en haut de la Fig. 7) : il se compose d’un rouleau tournant en contact avec trois disques (tous en acier pour roulements trempé). Le banc d’essai intègre un petit rouleau (de 12 mm de diamètre) provenant d’un roulement à rotule sur rouleaux et de trois éléments d’appui de dimension supérieure qui sont en fait des bagues intérieures de roulements à rouleaux cylindriques. Les rouleaux et bagues peuvent subir des opérations de fini de surface par rectification et/ou rodage visant à leur conférer la rugosité souhaitée. Le matériau des rouleaux testés et éléments d’appui est un acier pour roulements conforme à la norme ANSI-52100. Les tests ont été réalisés avec une modification du régime de lubrification (limite à mixte). À l’issue des tests, des signes de fatigue de surface sur rouleaux ont été recherchées. Les résultats ont été comparés entre rouleaux traités et rouleaux sans revêtement soumis à des conditions identiques.
Les résultats expérimentaux obtenus avec le banc d’essai de fatigue de surface montrent que le revêtement « black oxide » offre une certaine protection contre cette altération sur l’ensemble de la plage des conditions d’essai [23], comme on peut l’observer sur la Fig. 7.
Par ailleurs, une analyse paramétrique du modèle de fatigue de surface [22] a été réalisée concernant des surfaces revêtues [23], en tenant compte des effets du frottement, ainsi que de la rigidité et de l’épaisseur du revêtement. Elle a permis d’identifier l’existence d’une épaisseur optimale du revêtement pour une fatigue de surface minimale. Comme le montrent les résultats aussi bien expérimentaux que théoriques, le traitement « black oxide » permet d’élargir la plage de fonctionnement n’induisant aucune fatigue de surface, par rapport aux surfaces en acier pour roulements non revêtues.
3. Test pour roulements et expérience sur le terrain
Des roulements traités « black oxide » ont été soumis à un essai d’endurance dans des conditions de lubrification mixte sévères. L’effet positif de ce traitement concernant le processus de rodage [24] et avec une valeur de к faible pour ce qui est des conditions de lubrification a pu être vérifié par comparaison avec des roulements non revêtus.
Suite à ce test, tous les essais sur des roulements revêtus ont été suspendus. En effet, les résultats obtenus indiquent une durée L10 estimée deux à trois fois supérieure à la durée L10 estimée des roulements non-revêtus.
Outre les résultats des essais ci-dessus réalisés sur des roulements et des composants, l’impact du revêtement « black oxide » sur la réduction du risque de défaillance prématurée a été démontré sur le terrain. Des rapports émanant de fabricants de multiplicateurs et de constructeurs OEM d’éoliennes confirment une réduction significative du taux de défaillance des roulements traités « black oxide » par rapport à des roulements non revêtus [25] [26].
De plus, il a été observé ([8] et [25]) qu’un traitement thermique supplémentaire doux, en-dessous de la température de trempe ou de transformation, peut contribuer à optimiser et renforcer la microstructure sans perte de dureté et, par conséquent, allonger la durée de vie en fatigue des roulements. En partant de ce concept, un traitement « black oxide » effectué à une température similaire peut contribuer à des effets microstructuraux bénéfiques au sein de la surface extérieure en acier. C’est ce qui est apparu à travers une réduction de la valeur maximale de la largeur à mi-hauteur (FWHM ou b/B) des pics XRD de >0,1 degré.
Conclusions
Plusieurs effets bénéfiques du revêtement « black oxide » ont été démontrés par des recherches en laboratoire combinées à des essais sur les roulements et l’expérience sur le terrain. Le revêtement assure une certaine protection contre les attaques tribochimiques, réduit la perméation de l’hydrogène et accroît la résistance aux dommages dus à l’humidité (comme la corrosion « à l’arrêt »). Par ailleurs, le revêtement des surfaces en acier pour roulements par le traitement « black oxide », par rapport à des surfaces en acier pour roulements non revêtues, améliore la marge de sécurité en ce qui concerne des modes de défaillance tels que l’usure par adhérence/les dommages par grippage ou la fatigue de surface. Des expériences positives sur le terrain corroborent ces résultats.
En résumé, le procédé de traitement de thermique « black oxide » employé par SKF offre une protection renforcée des éléments des roulements. Parallèlement aux équipements d’origine, les roulements ainsi traités peuvent également être utilisés en remplacement de roulements conventionnels dans le cadre des opérations de maintenance dans les parcs éoliens. Autrement dit, revêtement « black oxide » peut être appliqué à tous les types de roulements utilisés dans les multiplicateurs d’éoliennes et bénéficier ainsi à l’ensemble de ce secteur d’activité. SKF recommande que les deux bagues, intérieure et extérieure, ainsi que les éléments roulants soient traités pour des performances optimales.
Références
[1] J. Rosinski, D. Smurthwaite : « Troubleshooting wind gearbox problems », Gear Solutions 2010.
[2] K. Stadler : « Comment réduire les coûts d’exploitation et de maintenance des éoliennes grâce aux roulements revêtus d’oxyde noir », Evolution n° 4-2013.
[3] DIN 50938 : « Traitement à l’oxyde noir des matériaux ferreux ».
[4] K. Stadler, A. Stubenrauch : « Défaillances prématurées des roulements dans les boîtes de vitesses industrielles » – Antriebstechnisches Kolloquium Aachen 2013 et Evolution n° 2-2013.
[5] W. Holweger : « Interaction of rolling bearing fatigue life with new material phenomenons » – VDI Kongress « Antriebs-stränge in Windenergieanlagen » 2012.
[6] H. Uyama : « The mechanism of white structure flaking in rolling bearings » – NREL workshop, Broomfield en novembre 2011.
[7] I. Strandell, C. Fajiers, T. Lund : « Corrosion – one root cause for premature bearing failures » – 37th Leeds-Lyon Symposium on Tribology en 2010.
[8] J. Gegner, L. Schlier, W. Nierlich : « Evidence and analysis of thermal static strain aging in the deformed surface zone of finish-machined hardened steel » – PowderDiffraction 24-2009 p 45-50.
[9] M. Reichelt, T.E. Weirich, J. Meyer, T. Wolf, J. Loos, P.W. Gold, M. Fajfrowski : « TEM and nanomechanical studies on tribological surface modifications formed on roller bearings under controlled lubrication conditions » . J. Mater. Sci. 41, 4543-4553 (2006).
[10] H.R. Pasaribu, P.M. Lugt : « The Composition of Reaction Layers on Rolling Bearings Lubricated with Gear Oils and Its Correlation with Rolling Bearing Performance » – Tribology Transactions, Vol. 55, 3, 351-356, 2012.
[11] ASTM G38 « Standard practice for making and using C-ring stress-corrosion test specimens » et ASTM G148 « Standard practice for evaluation of hydrogen uptake, permeation and transport in metals by an electrochemical technique ».
[12] B. Han, B.X. Zhou, R. Pasaribu : « C-ring Hydrogen Induced Stress Corrosion Cracking (HISCC) – Tests in Lubricating Liquid Media » – EuroCorr 2011 Proceeding.
[13] R-H. Song, S-I. Pyung, R.A. Oriani : « The hydrogen permeation through passivating film on iron by modulation method » – Electrochimica Acta Vol 36, N° 5/6, p. 825-831, 1991.
[14] V. Brizmer, R. Pasaribu, G.E. Morales : « Micropitting Performance of Oil Additives in Lubricated Rolling Contacts » – Tribology Transactions, Vol. 56, 5, p. 739-748, 2013.
[15] R.J.K. Wood : « Tribology and corrosion aspects of wind turbines, Wind Energy – Challenges for Materials, Mechanics and Surface Science » – IoP, Londres 2010.
[16] D.A. Jones : « Principles and Prevention of Corrosion » – 2nd Ed., Page 335, ISBN: 0-13-359993-0, 1996.
[17] ASTM B117-09 Standard Practice for Operating Salt Spray (Fog) Apparatus.
[18] M. Volkmuth, K. Stadler, R. Heemskerk : « Slippage measurements in roller bearings » – Antriebstechnisches Kolloquium ATK Aachen en 2009.
[19] R. Hambrecht : « Anschmiererscheinungen in Wälzlagern bei Fettschmierung » – Thèse de doctorat – Erlangen, 1999.
[20] B.J. Scherb, J. Zech : « A study on the smearing and slip behavior of radial cylindrical roller bearings » – Schaeffler Group 2001.
[21] G.E. Morales, K.S tadler, V. Brizmer : « Understanding and preventing surface distress) – Gear Solutions 2012.
[22] G.E. Morales-Espejel, V. Brizmer : « Micropitting Modelling in Rolling-Sliding Contacts: Application to Rolling Bearings » – Trib. Trans., 54, pp. 625-643, 2011.
[23] V. Brizmer, A. Rychahivskyy, B. Han : « Anti-Micropitting Performance of Black Oxide Coating » – Word Tribology Congress, Turin, 2013.
[24] H.v. Lier, C. Hentschke : « Untersuchungen zum Betriebsverhalten brünierter Wälzlager » – VDI-Bericht Nr.2202, 2013.
[25] J. Luyckx : « Hammering Wear Impact Fatigue Hypothesis WEC/irWEA failure mode on roller bearings » – NREL workshop, Broomfield, novembre 2011.
[26] Communiqué privé de SKF aux principaux constructeurs d’éoliennes.