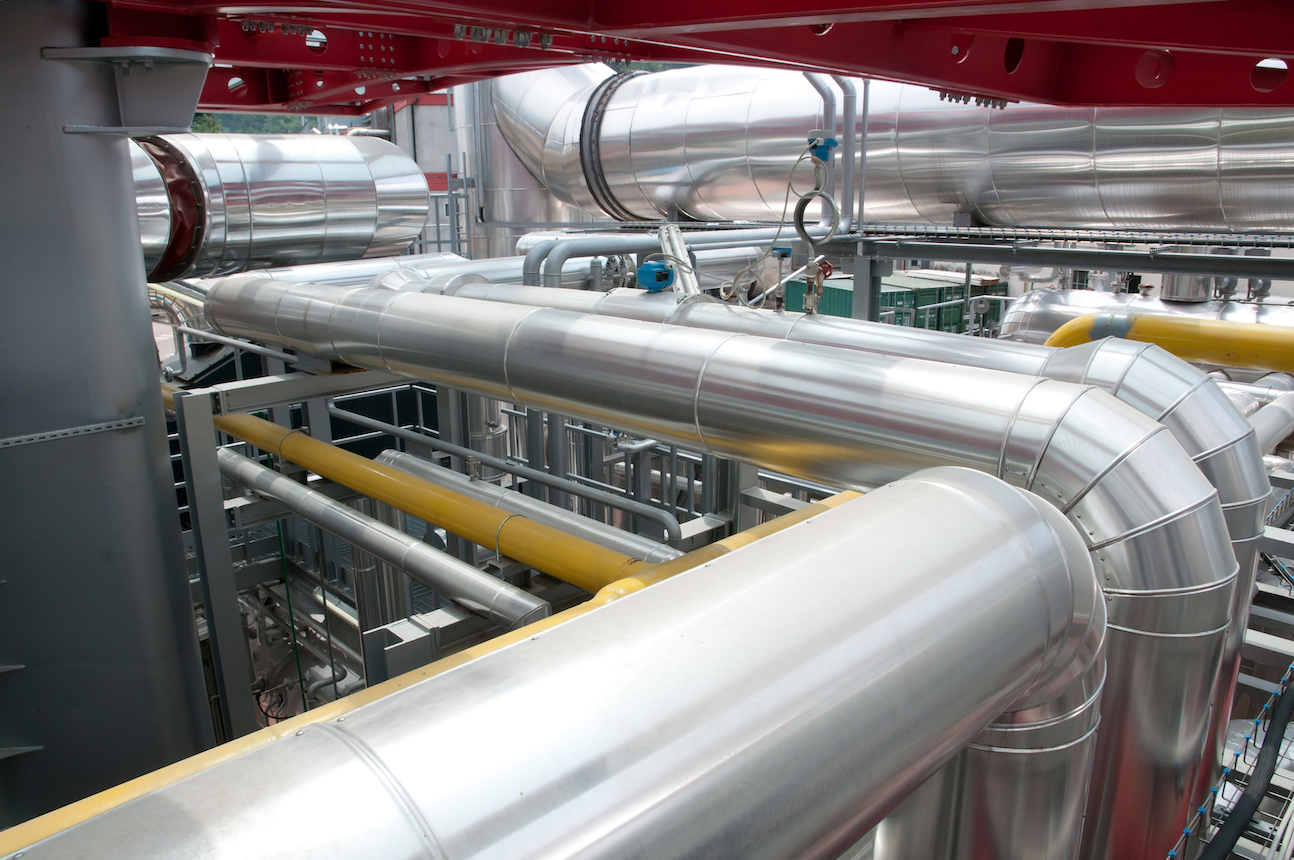
Une détermination d’acier
Filiale du premier groupe sidérurgiste mondial, l’aciériste allemand ArcelorMittal Bremen produit plus de trois millions de tonnes d’acier par an. SKF a fourni le système de maintenance conditionnelle qui surveille son système central de production d’air comprimé.
En bref
ArcelorMittal
– ArcelorMittal est le premier groupe sidérurgique mondial. Il est implanté dans une soixantaine de pays.
– En Allemagne, son volume de production s’élève à environ sept millions de tonnes d’acier brut, ce qui en fait l’un des premiers aciéristes du pays. La construction automobile, le BTP, l’industrie de l’emballage, les fabricants de produits ménagers font partie de sa clientèle.
– Le groupe possède quatre sites de production principaux en Allemagne : deux usines de tôles d’acier intégrées à Brême et à Eisenhüttenstadt, et deux usines de produits longs à Hambourg et à Duisbourg.
Liens apparentés
Contact commercial
Jorerg Lange Stephan Sondermannkf
Installés sur la rive du fleuve Weser, le siège social et le site de production d’ArcelorMittal Bremen occupent une superficie de 7 km2 à la périphérie de la ville de Brême. L’aciérie compte près de 3 500 salariés, ce qui en fait l’un des principaux employeurs industriels de la région.
Elle produit des tôles d’acier laminées à froid et à chaud avec traitement de surface spécial depuis 1957. Ces produits sont vendus à une variété de secteurs d’activité, notamment à la construction automobile.
Grâce à sa production hautement automatisée, ArcelorMittal Bremen fabrique au total 3,2 millions de tonnes d’acier par an. De la fabrication de la fonte au traitement des tôles, toutes les installations de production sont situées sur place.
Les équipements doivent être capables de résister aux conditions les plus extrêmes, qu’ils soient utilisés pour des applications hautes températures dans le cœur incandescent de l’aciérie ou qu’ils remplissent un rôle périphérique, fournir de l’électricité, de l’eau, de l’air, etc., par exemple.
Aux yeux de Ralf Suhling, responsable de la métrologie chez ArcelorMittal Bremen, la fiabilité de toutes les installations est une condition sine qua non à l’optimisation de la production. Celle-ci, tout comme la réduction des coûts de maintenance, ne peut se passer de la maintenance conditionnelle.
Exemple, le système central de production d’air comprimé qui approvisionne les multiples installations de production de l’aciérie par le biais d’un réseau de distribution dédié. Il est composé de quatre turbo-compresseurs affichant une pression de 6,5 bars chacun. « En principe, il y en a toujours trois en marche. Si l’un d’eux est victime d’une avarie grave, celle-ci est généralement due à un problème de roulements dans le moteur. »
Dans ce moteur, rotor et stator sont séparés par un espace. Au fil du temps, le jeu interne des roulements du moteur s’agrandit pour cause d’usure… Et l’espace entre le rotor et le stator rétrécit.
Stephan Sondermann, responsable commercial grands comptes industrie sidérurgique chez SKF Allemagne, explique que si le jeu interne des roulements augmente trop, le rotor peut s’affaisser et venir toucher le stator, provoquant de sérieux dégâts. « Quand cela se produit, le moteur endommagé doit être immédiatement démonté et le réparer coûte très cher. »
Pour éviter de tels incidents, ArcelorMittal Bremen se fie depuis plusieurs années au système en ligne SKF Multilog IMx pour son système central de production d’air comprimé. Ce système de surveillance en ligne permet de détecter les changements à temps et de mieux planifier la maintenance et le remplacement des moteurs.
Le système utilise une méthode simple pour détecter les changements : toute défaillance des roulements provoque, dans des fréquences définies, une augmentation des vibrations mesurable par des capteurs. « En fait, la surveillance en continu nous renseigne également sur le rendement des machines car nous recevons des données en permanence », précise Stephan Sondermann.
Le système a également permis à l’aciériste de réduire sensiblement le nombre de remplacements coûteux de moteurs requis pour le système de production d’air comprimé.
ArcelorMittal Bremen a toujours été un précurseur dans le domaine de la maintenance conditionnelle. Au milieu des années 1990, l’entreprise a imposé une surveillance systématique de ses installations même si, à l’époque, cette procédure était manuelle. Un technicien vérifiait régulièrement les machines du système central de production d’air comprimé à l’aide d’un appareil de mesure portatif. Les données étaient enregistrées puis servaient de base à une analyse, laquelle servait au personnel pour estimer si une pièce d’une machine devait être ou non remplacée.
« C’était déjà un grand progrès par rapport à la méthode traditionnelle qui consistait à remplacer un composant dès qu’on entendait un bruit bizarre dans la machine, explique Ralf Suhling. Avec l’arrivée de la surveillance périodique basée sur les inspections, ArcelorMittal Bremen a été mieux en mesure de planifier le remplacement des roulements et des pièces de moteurs et de compresseurs. »
Dans l’espoir d’optimiser davantage la maintenance conditionnelle, l’aciériste a fait appel à SKF. Il est vite apparu qu’un système de surveillance en ligne contrôlant en continu l’état des équipements de l’aciérie s’imposait.
L’ingénieur SKF Jörg Lange a été nommé chef de projet au moment de l’installation du système permanent en 2008. C’est toujours lui qui s’occupe du compte ArcelorMittal Bremen. L’ancienne méthode d’inspection périodique avait un inconvénient majeur, d’après lui : « Les données de mesure ne sont qu’un instantané. »
Ralf Suhling d’ArcelorMittal Bremen souligne que des variations ont été observées à maintes reprises dans les mesures relevées ponctuellement : « Quand la valeur indiquée était très élevée, on remplaçait immédiatement le composant concerné. Mais des doutes subsistaient quant à la nécessité de l’intervention. »
SKF a fourni le système en ligne SKF Multilog IMx-S, qui a été mis en place, raccordé au réseau électrique et mis en service en deux semaines seulement. Il indique les performances et la disponibilité des machines, et contrôle en continu les capteurs, les câbles et l’électronique. Les messages relatifs à l’état du système sont émis automatiquement.
Ralf Suhling affirme que les dépenses dues à la réparation des moteurs ont considérablement baissé depuis l’installation du système. Contrairement aux mesures manuelles qui ne fournissaient que des instantanés, le système de surveillance permanent peut faire la distinction entre des variations de courte durée et une détérioration avérée et permanente de l’état des machines.
Ces informations précises lui permettent, ainsi qu’à ses collègues, de réagir de manière beaucoup plus pointue. Au lieu de remplacer un grand nombre de pièces quand on soupçonne la présence d’un problème, comme c’était le cas auparavant, ArcelorMittal Bremen sait avec beaucoup plus de précision quand un remplacement est réellement nécessaire. Selon Jörg Lange, les avantages incluent « une meilleure planification des réparations, une augmentation du rendement des machines et, naturellement, un plus haut niveau de sécurité pour le personnel, qui peut accéder aux données depuis un bureau. »
ArcelorMittal Bremen n’a remplacé qu’un seul moteur depuis l’installation du système SKF Multilog IMx-S il y a cinq ans.
Le système en ligne SKF Multilog IMx-S
Le système en ligne SKF Multilog IMx-S peut être équipé, en option, de 16 ou de 32 entrées de signaux analogiques. Chaque entrée peut être configurée. Les informations sur les machines sont transmises automatiquement et avec précision par des capteurs de vibrations fixes vers un ordinateur hôte doté du logiciel SKF @ptitude Observer. Ainsi, un nombre considérable de données compliquées portant sur les machines et les installations peuvent être stockées et traitées avec rapidité, efficacité et fiabilité. Ceci permet au personnel de détecter les défaillances en amont ou de les éviter. Car le système propose automatiquement des recommandations sur la manière d’éliminer des problèmes existants ou à venir.
@ptitude est une marque déposée du Groupe SKF.