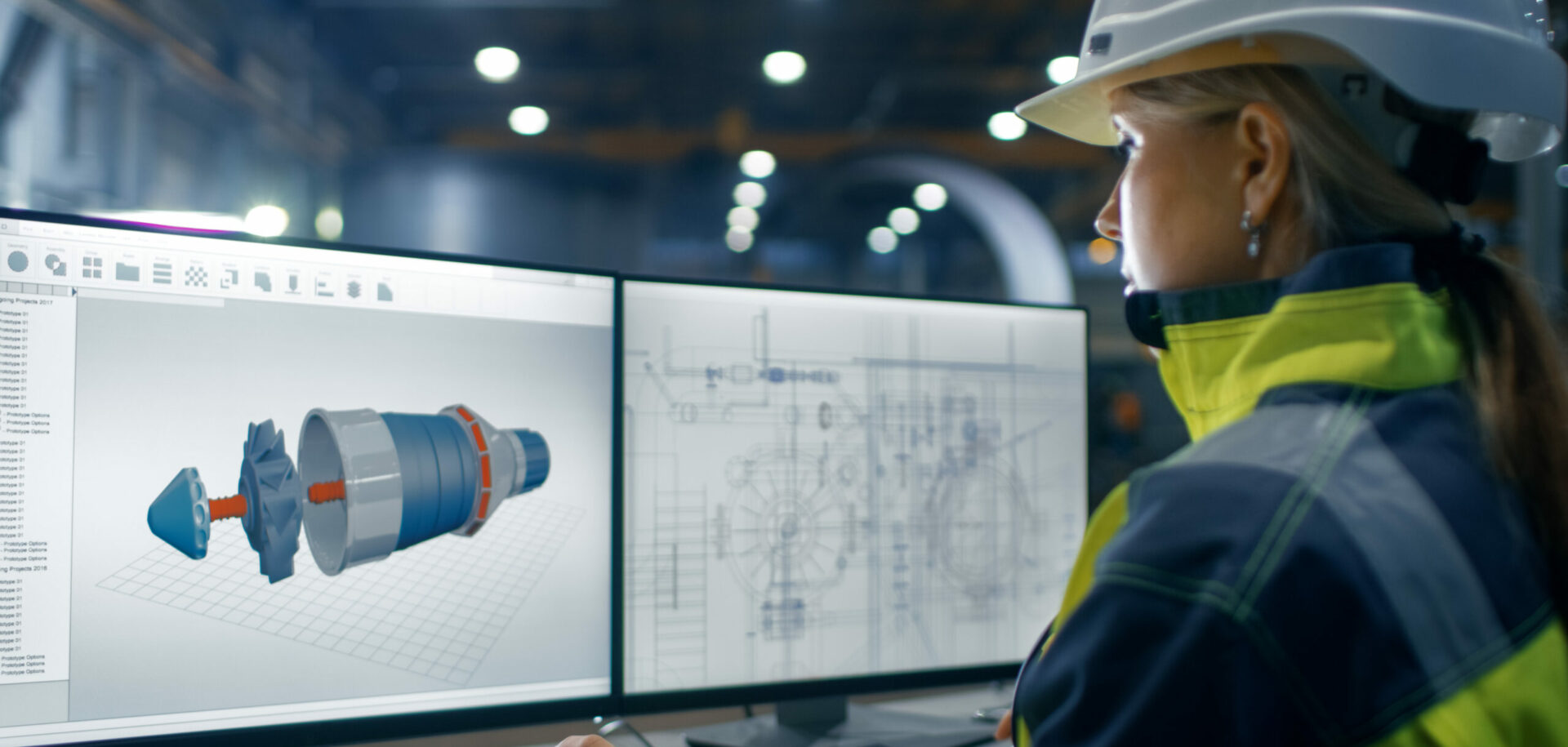
Monitoring critical applications at sea
In the maritime world, some components are more important to a ship’s operation than others. So condition-based maintenance and monitoring tech-niques are becoming increasingly important in improving the operating reliability of a ship’s “critical assets.”
The performanceof certain machine items, such as main gearboxes, turbochargers, thrusters and propulsion steam turbines, are critical for a ship’s availability, reliability and operating efficiency.
Here we look at four case studies where condition monitoring technology and practices have been applied to help secure the highest availability and safe operation of critical ship assets. It also describes how to establish an effective condition-based monitoring approach to maintenance.
Condition-based monitoring refers to the assessment on a continuous or periodic basis of the mechanical and electrical condition of machinery and systems from observations and/or recordings of relevant measurement parameters.
MAIN AND AUXILIARY ENGINE TURBOCHARGERS ON LNG CARRIERS
An increasing number of LNG carriers launched from Korean shipyards are equipped with diesel or dual-fuel engines. A leading ship operator recently introduced several large LNG carriers into its fleet and contacted SKF for advice on a suitable monitoring system for the main and auxiliary engines’ turbochargers (nine per ship). Requirements for the monitoring system included the ability to take continuous measurements and to be connected to the ship’s control system (DCS) to provide immediate warning of unexpected devi-ations in the machine condition.
SKF recommended the SKF Multilog On-line System IMx-S, which is its latest generation of online surveillance systems. The SKF system enables multi-channel (16 or 32) measurements, including synchron-ous channels and flexible conse bild uration to support different operating conditions. The SKF Multilog IMx-S automatically transfers data to a database server and to the SKF analysis software, known as SKF @ptitude Analyst. The SKF Multilog IMx-S is connected to the ship DCS, which also enables operating parameters such as engine speed to be compared. A schematic of the system design is shown in se bild . 1.
In addition to continuous measurements from the SKF Multilog IMx-S units, periodic data collection is made on close to 200 auxiliary machines with portable condition monitoring technology, and the data are sent via the ship’s communication system to an SKF marine remote diagnostic centre for further analysis. The remote analysis service is provided by SKF-certified condition monitoring engineers with marine experience, ensuring that the ship’s staff receives early warning of deterioration in machine condition and information about recommended maintenance actions.
PROPULSION STEAM TURBINE ON LNG CARRIERS
Even though diesel and dual-fuel engines have made their way into the larger LNG carrier tonnage, steam turbines remain a common alternative for small to medium-sized ships.
In order to monitor the condition and performance of these propulsion steam turbines, several new ships launched from Korean yards have been fitted with SKF vibration analysis systems for continuous and/or periodic monitoring.
The monitoring system design can vary, depending on the ship operator’s specific needs and application requirements. Portable monitoring systems are usually adequate for onboard condition monitoring programmes, whereas online monitoring systems are more appropriate for steam turbine monitoring. A simple sketch of a turbine installation can be seen in se bild . 2.
Vibration analysis is a powerful technique in understanding the mechanical condition of steam turbines and reduction gears. Baseline readings taken during the installation and commissioning of the system provide input to properly set alarm levels. Using stored measurement data, trend plots can easily be obtained to assess changes and help plan maintenance
interventions.
MAIN GEARBOXES ON CRUISE SHIPS
Technical requirements for propulsion gear design are becoming more challenging as a result of the ever-increasing power of prime movers, as well as the increasing requirements for lower weight, all without decreasing the gear’s reliability and efficiency.
A cruise ship operator recently contacted SKF for inspection and engineering support for the ship’s main propulsion gears. The operator was interested in monitoring the gears to improve the reliability of operation as well as to strengthen understanding of gearbox condition and maintenance planning.
Thanks to its global presence, SKF was able to easily identify a suitable boarding point with the cruise ship operator, enabling an SKF condition monitoring specialist to board the ship and inspect the gearboxes. By utilizing borescope visual inspection (se bild . 3), in addition to vibration analysis, SKF was able to provide the customer with a good assessment of gearbox condition and future maintenance recommendations. The information collected is also stored in a database for periodic trending of the important parameters.
THRUSTERS ON DRILLING PLATFORMS/RIGS
Drilling platforms and drill ships often use positioning and propulsion thrusters (se bild . 4). These are another example of critical assets that need very high operating reliability.
In a recent case, SKF worked closely with the OEM in the development of a suitable condition monitoring system for thrusters on a newly launched drill platform in the Gulf of Mexico.
Through close cooperation, the thruster design was prepared to suit a complete monitoring system for each bearing and gear within the thruster. The SKF online monitoring system monitors not only the vibration levels at bearings and gears, but also the oil contamination levels and temperature. With the customized logic-gating, data are collected during similar operating conditions, ensuring an accurate comparison of machine condition data.
Similar to the turbocharger monitoring system, the monitoring data are sent via the platform’s communication system to an SKF marine remote diagnostic centre for further analysis by condition monitoring engineers, again resulting in the generation of event reports with appropriate maintenance recommendations. Findings from the SKF analysis are shared with both operator and OEM to maximize efficient operation of the critical assets.