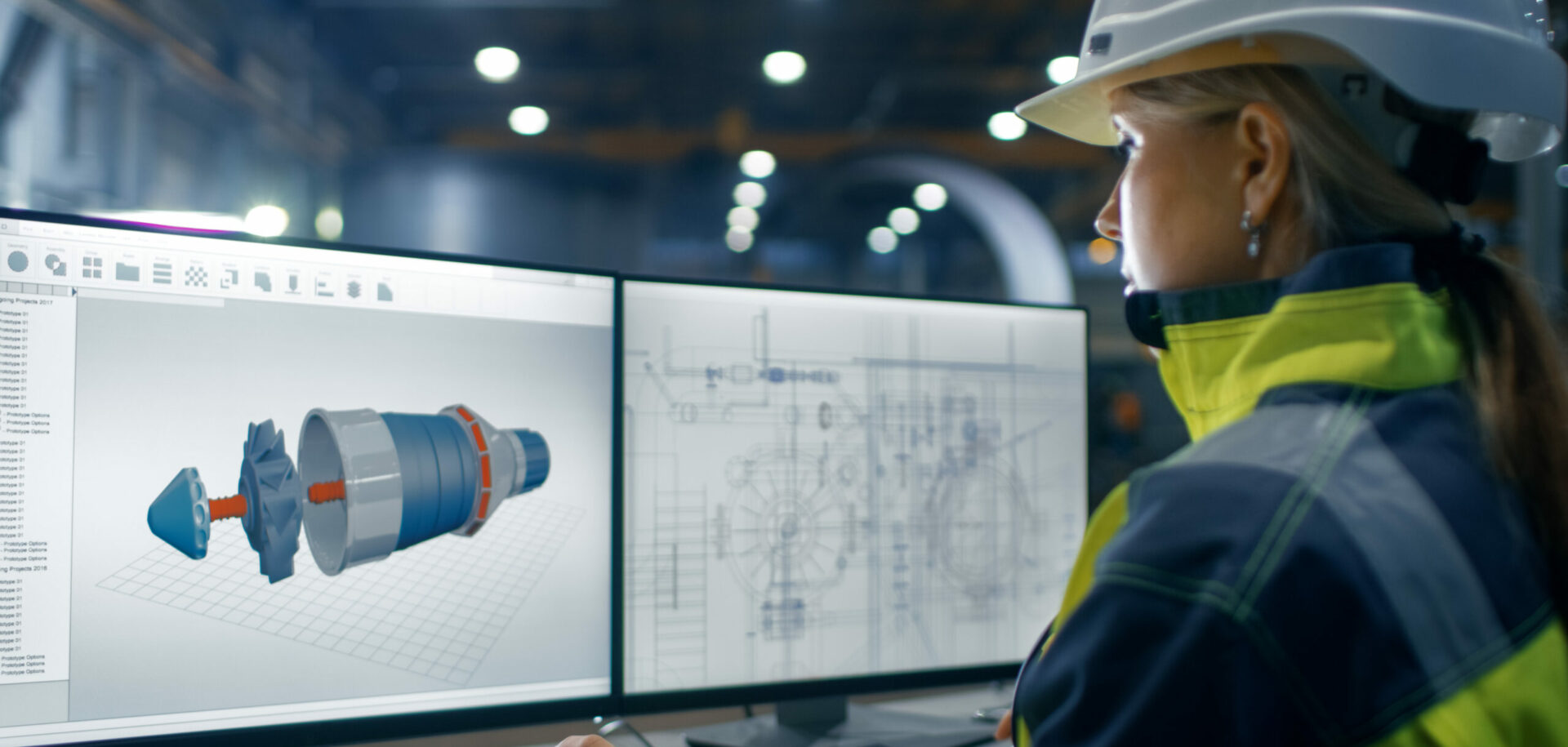
Summary
From looms to aircraft
Shanthi Gears manufactures speciality gears that range in weight from a few grams to more than 20 tonnes. The gears are used in products ranging from looms to power-generating turbines and aircraft.
Roughly 70 percent of the about 70,000 bearings Shanthi Gears buys from SKF per year are taper roller bearings. The majority of these are made in the SKF factory in Pune in western India. Featuring a special logarithmic raceway profile, the rollers in the bearings distribute the weight on the raceways equally, which increases the bearings’ service life.
Shanthi Gears’ engineers and planning teams are also participating in trial projects with SKF to explore the possibilities offered by its toroidal roller bearing CARB®.
Product profile
The product range of Shanthi Gears includes:
- Worm gearboxes from 28.6 mm to 431.8 mm centre distance
- Helical gearboxes with hardened and profile ground gears, ranging from 80 mm to 1,716 mm centre distance
- Bevel / bevel helical gearboxes with a transmitting capacity of up to 2,500 kW
- Geared motors up to 18 kW
- Spur/helical gears up to 3,200 mm diameter, 30 module
- High-precision hardened and profile ground gears up to 1,500 mm in diameter, 32 module
- Straight and spiral bevel gears up to 1,650 mm in diameter and 850 mm in diameter respectively
Equipment profile
Shanthi Gears is equipped with 62 gear hobbing machines with a maximum capacity up to 3,200 mm in diameter – 30 module. There are 32 gear grinders, the latest a Swiss-made Reishauer RZ-820 that can produce DIN class 4 ground gears. The company’s other equipment includes 31 milling machines, 25 straight and spiral bevel cutting machines as well as a variety of boring, milling and drilling machines. The majority of the machines are imported from Europe. Shanthi Gears is certified according to ISO 9001 standards.
Coimbatore, in southern India, has long been known for its colourful cottons. Now it’s also becoming known as home to one of India’s premium gear manufacturers.The headquarters of Shanthi Gears Ltd sits in the heart of a region where agriculture and textile production are the dominating businesses. But step inside the company facilities and you’ll get a different picture – it’s gears, gears, everywhere gears.
In the engineering department engineers are using 3-D modelling techniques and computer graphics to ensure that such factors as gearbox dimensions, gear geometry and rating capacity are all accurate. Next door, in one of the five factory units, CNC boring machines bore through gearbox casings and NC hobbing machines hob the gear blanks to the required contours and dimensions. Finally, precision gear grinders grind the gear profiles to mirror finish and optimum accuracy. Shanthi Gears grew out of the work of one entrepreneurial engineer. In 1969, Managing Director P. Subramanian gave up his teaching job and turned to the business of making gears. He had no start-up money, so he initially sub-contracted out orders for the loose gears used in local textile machinery. Soon he developed a reputation for high quality and timely deliveries, and orders for his gears grew rapidly.
Expanded product range
By 1972 Subramanian had enough capital to open his first factory. Nearly a decade later, building on the company’s growing reputation and customer demands, he expanded to produce worm gearboxes. In the mid-80s, Shanthi Gears took the next step and began manufacturing helical and bevel helical gears. Simultaneously, production of geared motors also began.
To gain better control over production, in 1986 the company built its own foundry. This integration helped the company improve the quality and delivery times of its products. The foundry caters to the needs of grey iron and spheroidal graphite castings, as well as non-ferrous ones such as phosphor bronze, aluminium etc. As a part of backward integration, a forging plant was commissioned simultaneously.
Today Shanthi Gears is no longer making gears just for the textile industry. Other industries have been added to the list, for example process, power, steel, cement, sugar and aviation. The product range extends from gears for simple applications such as hand-driven jacks to high-tech gears for supersonic jet aircraft. Key orders include turbine gearboxes, precision gears for printing machinery and engine gears for aircraft. Heavy-duty gearboxes are delivered to steel mills, sugar mills, cement plants and sponge iron plants.
Shanthi Gears also makes its own hobbing and milling cutters, cutting down the delivery time of special orders, which have become a hallmark of the company. With its in-house design, manufacturing and quality-control facilities, the company is able to fill orders for practically any custom-made gears. Today, nearly 50 percent of the company’s business involves special orders.
Growing exports
With a reputation for building precision gears and filling special orders, sales figures grew exponentially. In addition, the liberalisation efforts of the Indian government and the consequent opening up of export markets gave Shanthi Gears an opportunity to export its products.
The company has a leg up because most of its machinery and quality control equipment are from the best names in the industry. It is also producing gears that met ISO (International), DIN (German) and AGMA (American) standards. Therefore Shanthi Gears is confident its products could compete with products from other manufacturers. The company also showed that with its engineering facilities and factories it could design and make a gearbox, transport it to the port in Madras, load it on the next ship and in three weeks have it to the customer – on time and at a competitive price.
Eventually these efforts started to bring orders. In 1995 Shanthi Gears exported around 4 million rupees (USD 95,000) worth of gears and gearboxes. In the fiscal year that ended March 31, 2000, that figure rose to 17 million (USD 400,000). While this is less than 5 percent of the overall sales of 400 million rupees (USD 9.3 million), the trend is promising and Shanthi Gears aims to double its exports in the next fiscal year.
In terms of the future, perhaps the Japanese industry can serve as an example of what may be coming for its Indian counterparts. Only a few decades ago Japanese products were fairly unknown on the global market and now they are exported all over the world.
Åke R. Malm
managing editor of Evolution, with contributing writers in New Delhi and Coimbatore
photos D. Krishnan