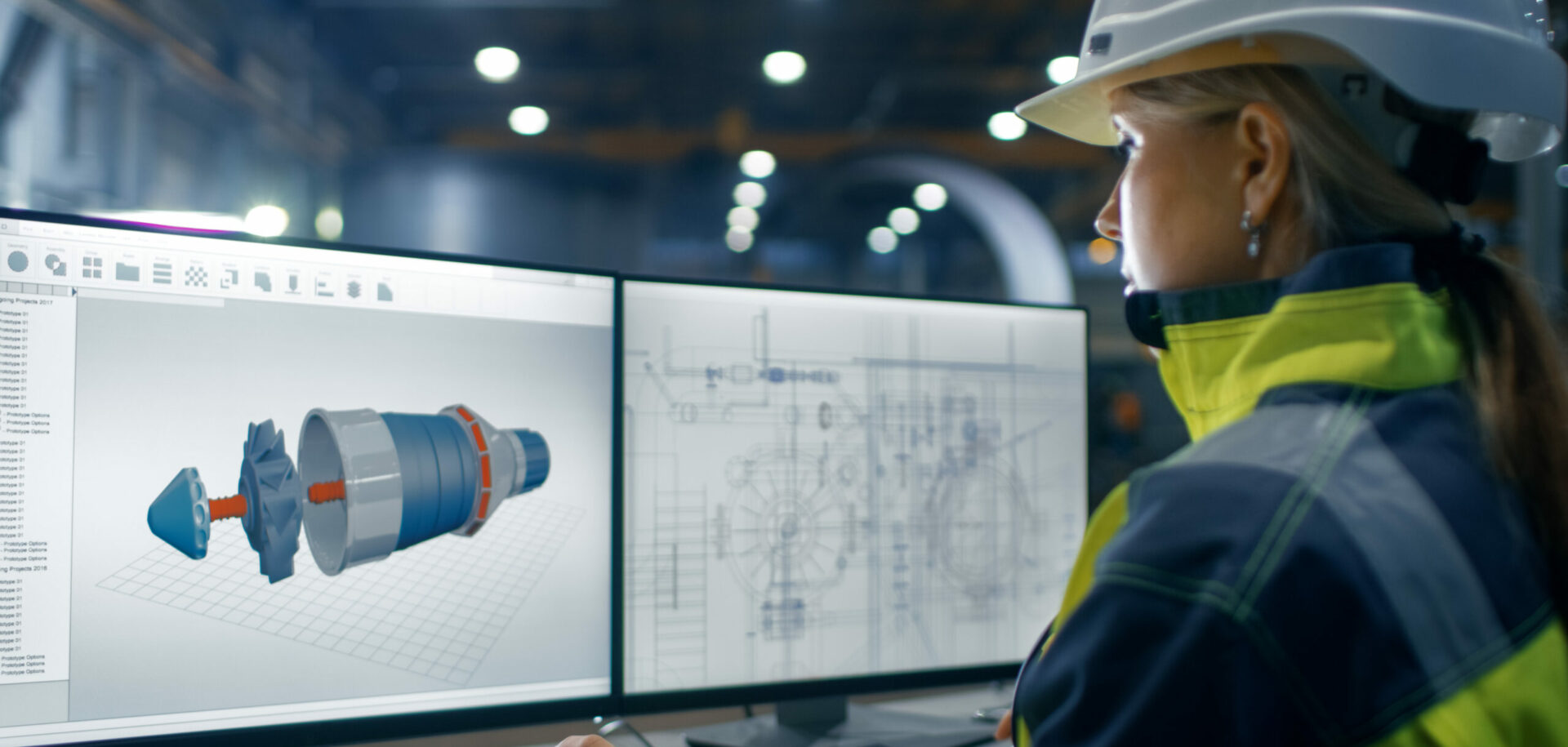
The sound of noise
Designers of domestic appliances are committed to reducing the level of sound which machines contribute to the background cacophony of daily existence. Bearings are an important part of the total process of sound generation.
Our perception and acceptance of sounds depend on their familiarity and the context in which they are heard.
While we actively seek out sounds such as music, accept others like the hum of the refrigerator or the purr of a well-tuned
car engine, a cats’ chorus at three in the morning is considered unacceptable and is classified as noise.
Sound can be defined as ‘the sensation that is perceived by the sense of hearing’. We give sounds a ranking, to be sure to avoid unpleasant sensations. People have an expectation of the sound level for each object or machine they come in contact with.
Sound ranking is very subjective. A sports car has to sound different from a family car, for instance, because the driver’s expectations are different. Sounds can be divided into two categories: sound and noise.
When buying new equipment we always look for a machine with reduced sound levels or something that will not be ‘noisy’. Today, low noise is just as important as washing or cooling performances. For example, low noise is a product feature for SKF customers in the household appliances market and is used as a competitive edge to gain market share.
Main buying criteria
Sound level is becoming one of the main buying criteria when purchasing a new household appliance. The most stringent demands for low noise relate to home and office air-conditioning systems, washing machines, dishwashers, dryers, heating systems and ceiling fans.
When we switch on any of the above machines, we hear a sound in a very subjective way. In general we would like to hear a ‘good sound’, or one that we find acceptable. The domestic appliance manufacturer has the difficult task of translating these perceptions of ‘good sound’ into a quantity that can be measured physically on the production line. This information has to be transferred to SKF, the components supplier, for bearings to help meet these expectations.
Figure 1 gives the levels of typical sounds (measured in dB) generated by different machines and activities.
Today manufacturers are marketing dishwashers that run at noise levels of 47 dB in operation with water circulating and dishes loaded. As the figure shows, this is close to the noise level of a refrigerator and is far below the level of a normal conversation between two people.
Sound and vibrations
Sound or noise level is not the only parameter to define a ‘good sound’. Many other subjective perceptions need to be considered, such as a low level in the audible parts of the frequency spectrum, white noise character with no pure tones and stability of sound with no variations.
The application has to be considered as a total system along with the influence of each component within that system, in order to obtain a good working sound.
The sound we hear is transmitted through the air as a fluctuating pressure wave. Sound is generated by vibrating parts.
Vibrations are different from sounds in that vibrations provide the energy necessary to generate sounds and propel sound waves through the air (fig. 2).
Vibrations of the total structure generate sound. One way of reducing overall sound levels is by reducing the energy the system will transfer to the air that carries the sound waves.
The intensity of the sound is proportional to the velocity of a vibrating surface:
p = r c v
where
p = sound pressure (Pa)
r = air density kg/m3
c = sonic speed (m/s)
v = velocity of point on surface (m/s)
Figure 3 shows the difference in vibrations of two systems with the same amplitude, but at two different velocities.
Good vibrations are defined as small in amplitude and of low frequency.
Quiet applications
Bearings are an important part of the total process of sound generation, when considering vibrations of the total application as the source of sound levels.
Looking more closely at the bearing and its application, five important factors acting on vibration generation and subsequent sound levels can be identified:
Some are the responsibility of the bearing supplier while others are controlled by the manufacturers. All factors emphasise the need for a close relationship between manufacturer and supplier.
1. Choosing the right bearing
Bearing application engineers should be involved from the earliest stages of a customer’s project. They can provide specific expertise and system knowledge necessary to choose the right bearing type. SKF, for example, can calculate and help choose proper clearances and internal designs while SKF laboratories continue to work closely with the customer.
2. Manufacturing of bearings at world class standards
SKF is fully committed to continuously improving its product, with the Total
Quality Management system. New customer development are also vital sources
of innovation.
3. Assembly
When assembling bearings into the application, bearings have to be in the original state, and considerable care taken to avoid pollution and damage during assembly.
4. Mounting conditions
include roundness of shafts and housings, selection of fits and misalignments.
5. Working conditions
include resonance, alternating loads and loads and speeds.
household appliances
Household appliances and their related components (such as electrical motors) are the most sensitive applications regarding noise levels. Washing machines, dishwashers, air-conditioning systems and everyday kitchen equipment are sold with different designs and performances, which tend to follow geographical differences: smaller and faster machines in Europe and Asia, bigger and slower machines in America. Requests for low noise machines, however, are universal.
Performance and machine features have led designers of most well-known household appliances to choose SKF deep groove ball bearings.
Due to these sensitive applications, product and process development of
deep groove ball bearings has always been focused on studying and implementing new systems for vibration control,
both on the production line and in laboratories.
Figure 4 illustrates the important parameters influencing ball bearing vibrations.
Bearing manufacture and vibration control
Vibration checking is vital to bearing manufacture. For example, operators on the manufacturing lines at SKF plants who control the overall process also check vibration. Post process machines are in place to assure quality of the product and contribute to process control.
Cleanliness of the components and of the assembly lines is one of the basic factors in achieving the requested low vibration levels. In addition the manufacturing process is continuously monitored and improved to maintain very low contamination levels. Filtering and washing are essential parts of the process.
It is important that customers try to keep the same low contamination levels during the assembly operations for bearings.
Vibration Analyser
For application testing and analysis of vibration, SKF has developed a new system that is called AVA, Advanced Vibration Analyser.
The system is based on a personal computer. The software, in effect, transforms the PC into a vibration detector (velocity or acceleration) and a recording device for sound and noise (fig. 5).
The recorded vibrations or sounds are then processed, the data allowing application engineers to suggest improvements either to the customer’s design or in bearing selection. The vibration spectrum of
an electrical motor, in which the peak frequencies are identified in operation, can
be detected, processed and recorded.
Luigi Cavallero,
SKF Industrie S.p.A.,
Airasca, Italy