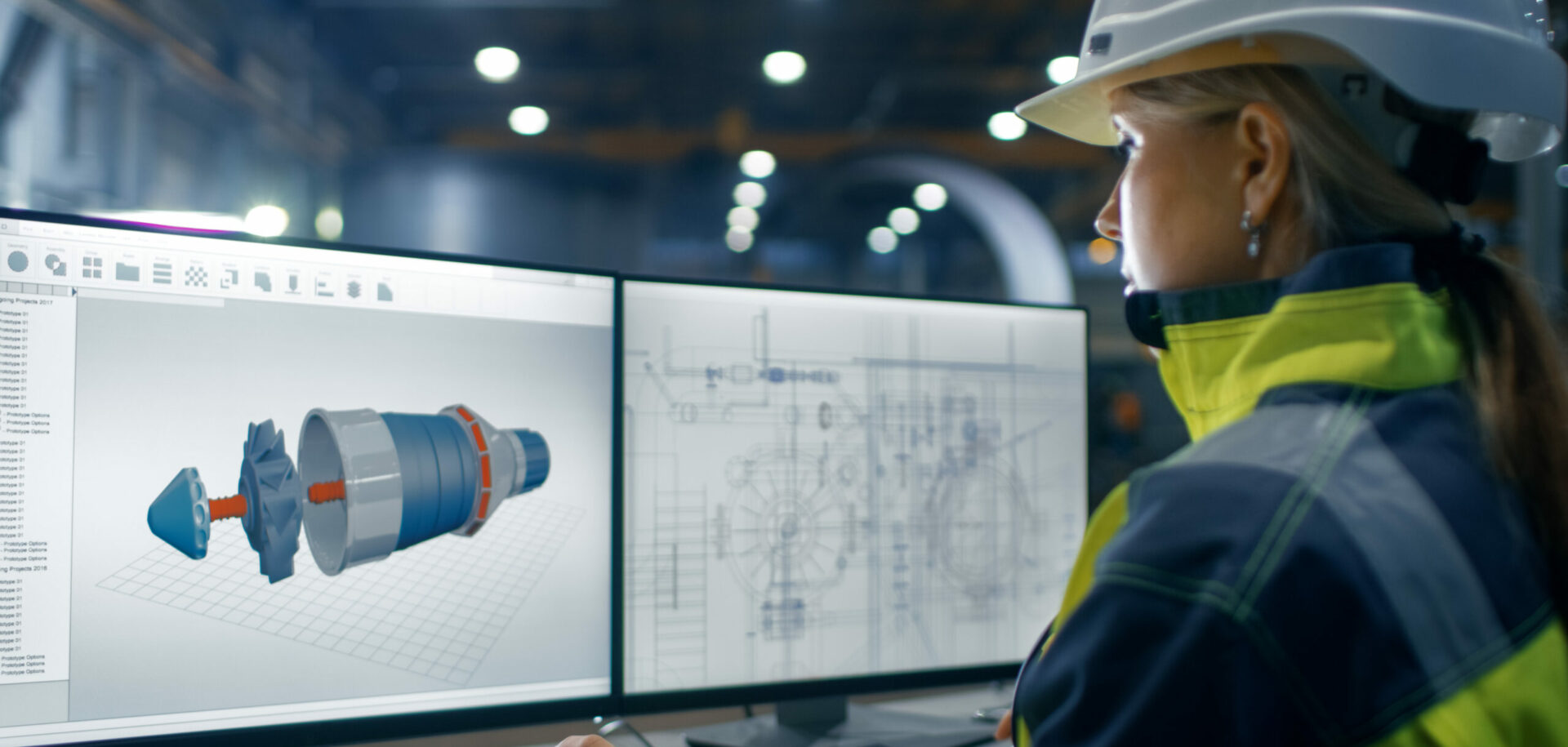
Working close to the melting pot
Today molten steel is continuously cast to slabs, billets or blooms which are then rolled to plate, rods, rails etc. The molten steel is poured in at one end of the machine, and the semi-finished product comes out the other.Apart from being a fascinating machine, it is a very demanding environment for the machine components, not least for the bearings.
Today molten steel is continuously cast to slabs, billets or blooms which are then rolled to plate, rods, rails etc. The molten steel is poured in at one end of the machine, and the semi-finished product comes out the other.Apart from being a fascinating machine, it is a very demanding environment for the machine components, not least for the bearings.
The principle of a slab caster is shown in figure 1.
On its way down through the caster, the strand passes some 200-300 support rolls and at the end it is cut into manageable lengths of about 15 m. In a conventional slab caster, the strand has a thickness of 200 mm and a width of 1,500-2,000 mm.
In the top section, the many support rolls which have a relatively small diameter provide good support for the strand which is still weak. The loads are light and the bearings used preferably have a low section height. Further down, just above the middle of the bow, the loads increase rapidly.
High demands on bearings
Bearings for support rolls in continuous casters have a tough life with very heavy loads, high temperatures, low speeds, heavy contamination and wear. These are conditions that are unfavourable to any kind of bearing. For the bearings to survive the ingress of water, dirt, steel particles and cooling water additives, grease is normally pumped through the caster continuously.
Grease consumption may be 10 to 50 tonnes of grease per year, resulting in high costs not only because of the vast quantity of but also maintenance of the relubrication systems, cleaning the cooling water, production disturbances etc. In addition, there are the environmental aspects. Since grease is toxic, disposal of used grease is a problem, and future environmental cost considerations and legislation will impose constraints.
A maintenance-free solution for this application has been sought after by steel mills for quite some time.
Reduced maintenance
To meet the demand for reduced maintenance in continuous casters, SKF has developed a sealed spherical roller bearing for this harsh environment.
Its foundation is the well known spherical roller bearing, a robust heavy duty bearing allowing combined loads and misalignment between housing and shaft. Without reducing the carrying capacity, the new bearing has fully integral rubbing seals, see figure 2. The rubber material is a fluoro elastomer allowing peak temperatures of 200 °C; the bearings are filled with a heavy duty grease matching the same temperature range.
The basic idea is to avoid having to relubricate the bearing during its service life. In this sense, the bearing is a ‘bolt on, ready to use’unit. However, the benefits are not obtainable until the bearing is built into a proper housing with outer sealing arrangement. To complete the solution, SKF has developed additional housing and outer sealing designs (see figure 3). Depending on the design and condition of the machine, relubrication can be completely dispensed with or limited to relubrication of the outer sealing arrangement.
The bearing is normally mounted with a loose fit on the shaft and in the housing, allowing axial displacement along the shaft. Roll length changes during a production cycle because of changing temperature. As the final sealing agent, the housings are 100% filled with grease.
Many steel mills in Europe and USA are now testing SKF’s ideas. Some mills are even running them fully implemented on a commercial basis. The experience so far is very good. As expected, there is less grease consumption and fewer grease-related production disturbances, less maintenance to relubrication systems, less cleaning and less used grease to get rid of. Machine manufacturers benefit from the partial elimination of complex and expensive relubrication systems.
All over the world, there are more than 1,200 continuous casting machines, and there are many opportunities for the saving of costs and protection of the environment. The sealed spherical roller bearings are today’s state of the art solution for casters and more and more steel mills are expected to adopt this solution.
Klas Ålander,
SKF Spherical Roller Bearing Division,
Gothenburg, Sweden