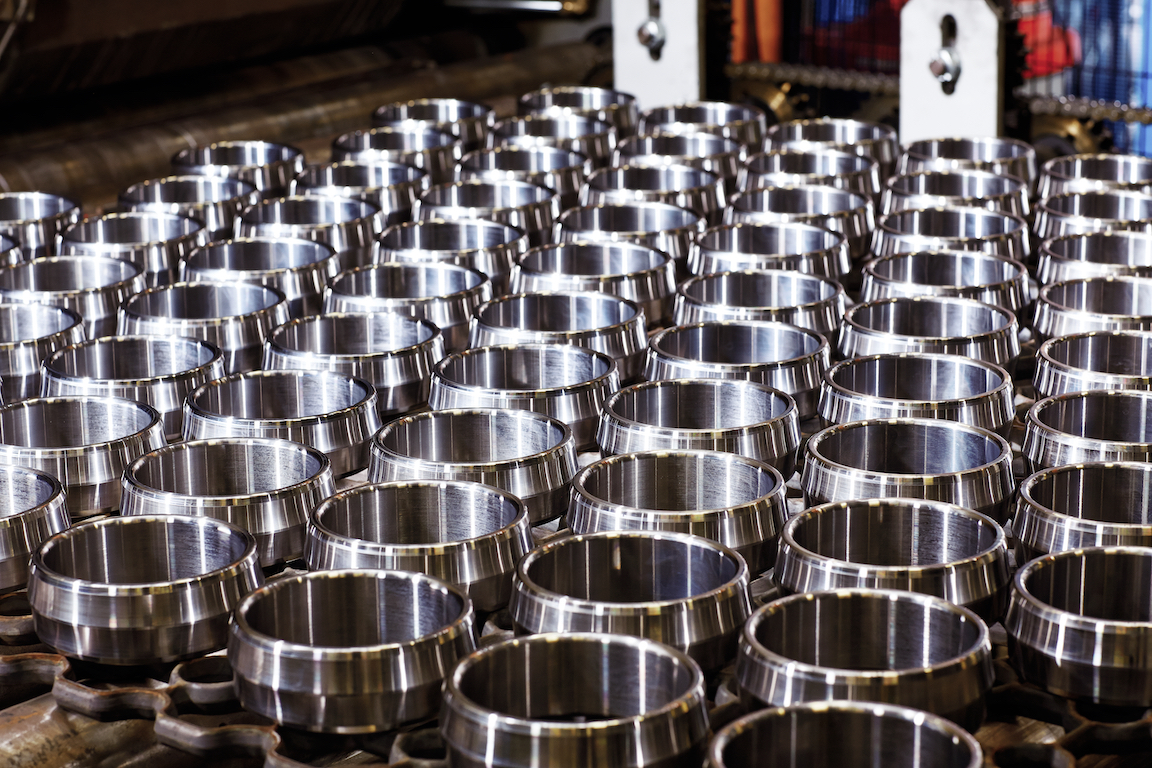
A distaste for waste
Michael Biddle has built an award-winning business around plastics recovery and recycling from discarded products.
A self-described “above-ground miner”, Michael Biddle has built a global, large-scale industrial business on material extraction from post-consumer waste. His success is based on the idea that plastics from complex waste streams can be recycled into high-quality raw material. “I think most people have a love-hate relationship with plastics,” says Biddle. “I just hate waste of any kind – resources, time, people – so closing the loop is my way of dealing with that.” The recycling industry’s volumes are growing rapidly, but in comparison with metal and paper, plastics only represent a small part of the total; less than 10 percent of all plastics used in the world are recycled. “The fundamental problem with plastics is that every device – such as computers, phones or coffee makers – can contain five or more different plastics, each with different properties, as well as many other materials,” says Biddle. “First you have to separate the non-plastics from the plastics, and then you have to separate the plastics from one another. The last part is particularly difficult.” Biddle’s company, MBA Polymers, has its headquarters and research facility in Richmond, California, and plants in Austria, the UK and China that sell recycled plastics to Fortune 100 companies such as Electrolux, Philips and Nestlé. MBA Polymers has an origin story that reads like a cliché: It all started 20 years ago in an American garage, in the San Francisco Bay Area of California. That’s where Biddle, armed with a business plan and enough research funding from the American Plastics Council to give him sufficient courage, began experimenting with his first huge pile of junk. First, he needed to find an efficient method for shredding computers, car parts or vacuum cleaners in order to liberate their various constituent materials. Next, he needed to devise a way to separate the rubber, wood, fibres, foam, carpeting, glass, stones, foil or metal from the plastics. (Some of these materials, such as metal and rubber, can be sorted as commodities and sold to other recyclers. Most of the rest becomes solid waste or can be turned into energy.) “This is when it all starts to resemble mining,” Biddle says. “To extract what you want from a pile of shredded waste that used to be a vacuum cleaner is not so different from extracting one mineral from among others in a stone.” Thinking like a miner helped him, after much trial and error in his garage, to make a number of breakthroughs, followed by a small pilot line pieced together with a hotchpotch of “recovered” equipment in Berkeley, California. The really big challenge was devising a method for separating the different plastics by type and grade. “At this stage in the process I had piles of this-sized pieces of plastic,” Biddle says, pointing at one of his fingernails. Different kinds of plastics have overlapping characteristics (densities, colours, electrical and magnetic properties) that make sorting seemingly impossible. Nevertheless, MBA Polymers has succeeded in developing a highly automated process – covered by a combination of patents and trade secrets – to sort the plastics mixtures by type and grade, followed by an optical sorting process to sort them by colour. At MBA’s newest facility in Nottinghamshire, UK, it takes less than an hour for the remnants of a vacuum cleaner to go from waste to small particles of various valuable materials. Biddle is proud that MBA’s techniques do not require the addition of virgin or other relatively pure materials to its plastics, which is the most common way to raise purity levels in recycled plastics products today. “To separate the plastics from other materials to 75 percent purity is not that difficult,” he says. “To reach over 90 percent is really hard, and to get sufficient purity to replace virgin plastic is nearly impossible. But we have managed to do that.” Biddle acknowledges that it is hard for MBA to compete with plastic manufacturers strictly on the basis of cost. “Our products at present can sometimes be more expensive, depending on customer requirements – especially difficult-to-match colours. But our customers see the importance of minimizing their carbon footprint and developing a more sustainable supply chain.” Biddle’s sustainability accolades are many. He serves on the boards of the Worldwatch Institute and EPEAT (the Electronic Product Environmental Assessment Tool), a rating tool for greener electronics. He is also a recipient of the 2012 Gothenburg Award for Sustainable Development. One of the things about Biddle that does not seem sustainable, though, is his work schedule. He divides his time between the MBA Polymers recycling facilities in China, Austria and the UK and the research and development plant in California, near where he lives with his family. “Travelling across the globe is not very sustainable, but I try to compensate for that in other ways,” he says. “I bike to work, meetings and shopping as often as I can, and we are one of the few parents who force our kids to cycle to school – and probably the only ones in the neighbourhood who hang our laundry outside to dry.” The Gothenburg Award is an international prize of 1 million Swedish kronor (117,000 euros) that recognizes and supports works to achieve sustainable development. The award is decided by an independent jury and administered and funded by a coalition of the City of Gothenburg and 12 companies, including SKF. Michael Biddle shares the award for 2012 with Björn Söderberg, whose entrepreneurship in Nepal has created jobs and contributed to an increased eco-cycle approach.Prizewinner