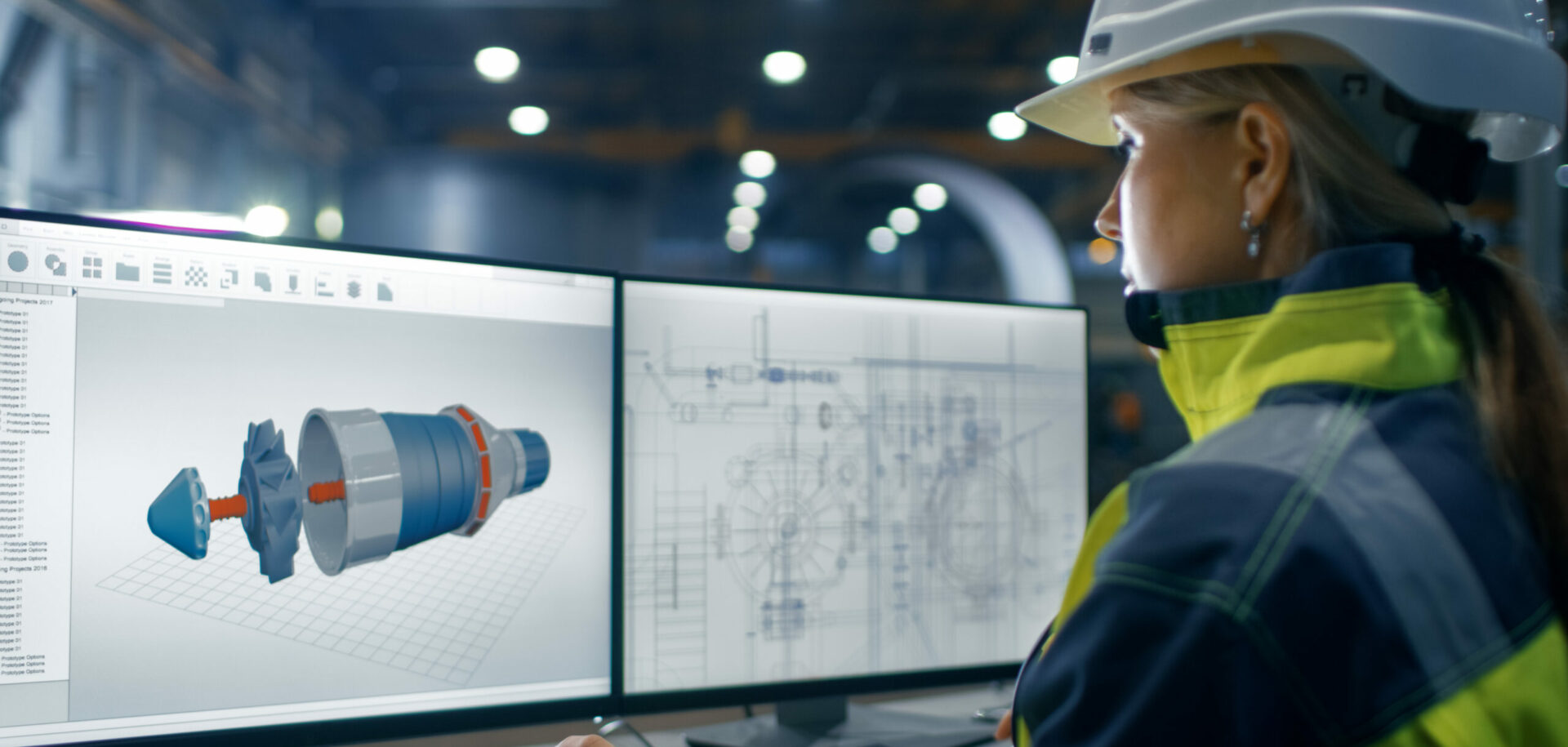
A new standard
A modular concept from ABB is now available on the market for railway traction motors. Based on standard modules, the new motors are optimized and can be made to specification more quickly than with traditional designs.
Traction motors in different railway applications have a tough job. Not only must they endure demanding operating conditions such as intermittent operating cycles, variable loads, changing weather conditions, dust and dirt, but they must continue to do so in an energy-efficient manner for as long as 40 years.
This results in specifications with somewhat conflicting requirements that can be difficult to match. It’s no wonder then that manufacturers of locomotives, multiple units, trams, metros and other railway rolling stock have traditionally ended up with unique designs for their respective traction motors.
ABB, a manufacturer of traction motors since 1909, saw an opportunity that involved breaking with tradition. “We saw that we could be competitive and grow in this market,” says Peter Isberg, technical manager for ABB traction motors.
“The challenge was to set a higher level, creating standardization and flexibility in traction motor design that had never been seen before.”
Isberg speaks about this ambitious goal in a matter-of-fact manner that conveys a deep sense of confidence in his and his ABB colleagues’ engin-eering know-how. The project got the go-ahead in 2007. The main question was: How do we meet a whole range of customer demands with standardized induction traction motors?
“Every customer has its own bogie design with a pre-defined space for the traction motor,” says Isberg. “Suppliers must fit their motors into the available space and follow the rest of the specification too.”
Isberg and his team sought to develop an elec-trical design that was as energy-efficient as possible. “This would enable us to make a compact motor that could deliver high power and torque with good efficiency,” says Isberg.
The more power you extract from an electrical motor, the lower the efficiency, due to the temperature rise in the active parts. One remedy was to increase the size of the motor, but this would negate the goal of the project, so instead the team worked to optimize the electrical design.
One important issue was the thermal behaviour of the motor when fed by a traction frequency converter, a device that converts alternating or direct current to rectangular pulses of variable frequency, enabling control of the motor output. The converter and motor must be designed as a system based on the operating characteristics for a certain railway application. ABB has its own FEM-based design software that, when combined with separate thermal design software, can accurately predict the in-service motor
temperature.
A converter can also create voltage at the point where the phases are connected together in the motor winding (common mode voltage), which results in another technical challenge: bearing current (when a damaging electrical current passes through a bearing).
“Our job is to inform the customer about the risk of bearing currents with different technical solutions and to suggest one that is safe,” says project manager Henrik Carlsson. “In this case we chose hybrid bearings.”
Hybrid bearings have steel rings and ceramic rolling elements that act as insulators. This makes it virtually impossible for a current to pass through a bearing under normal operating conditions. In addition, the relubrication intervals are significantly longer than for all-steel bearings.
“These two benefits were enough to motivate us to choose this bearing solution,” says Carlsson.
While hybrid bearings are more expensive, they translate directly to reduced costs for the railway operator, due to increased reliability and reduced downtime. A traction motor often sits in the bogie, and dismantling it for maintenance could require the service technicians to first separate the body from the undercarriage.
As we pass through the well-organized workshop, Carlsson has a small but friendly argument with one of the truck drivers. The atmosphere is professional and at the same time informal, a feeling that is reinforced by the size of the facility. It looks small for a production output of more than 3,000 units per year.
We stop at a traction motor that is being assembled to take a look at the standardized modules: terminal box positions, sensor and cooling arrangements, bracket attachment and, not least, a scalable design. ABB can meet a variety of customer specifications with one basic design.
“It will be really exciting to see the first trains in operation with motors from the new platform,” says Lars Fredrikson, who works with marketing and sales for ABB.
The commissioning of the new motor will take place 2011 in Caracas, Venezuela. The customer is Spanish manufacturer CAF/Trainelec, which will deploy 1,100 modular traction motors there, fitted in metro trains supplied to Caracas Metro.
“We have been selected by them as a new supplier of traction motors,” says Fredrikson. “There are a number of other motor manufacturers, and the competition is tough. In this case, a reliable design and the short delivery time offered by the modular design were determining factors.”
More rail time with hybrid bearings
When ABB decided to develop a modular traction motor concept the company turned to SKF for bearing solutions.
Two important objectives in the project were to minimize downtime by limiting damaging currents to pass through the bearings, and to minimize maintenance costs through prolonged relubrication intervals. ABB also wanted to minimize the bearing range in order to benefit price-wise from increased long-term sales volumes.
The two companies went for a flexible bearing arrangement approach that resulted in a preferred selection of SKF’s hybrid bearings for the ABB range of traction motors.