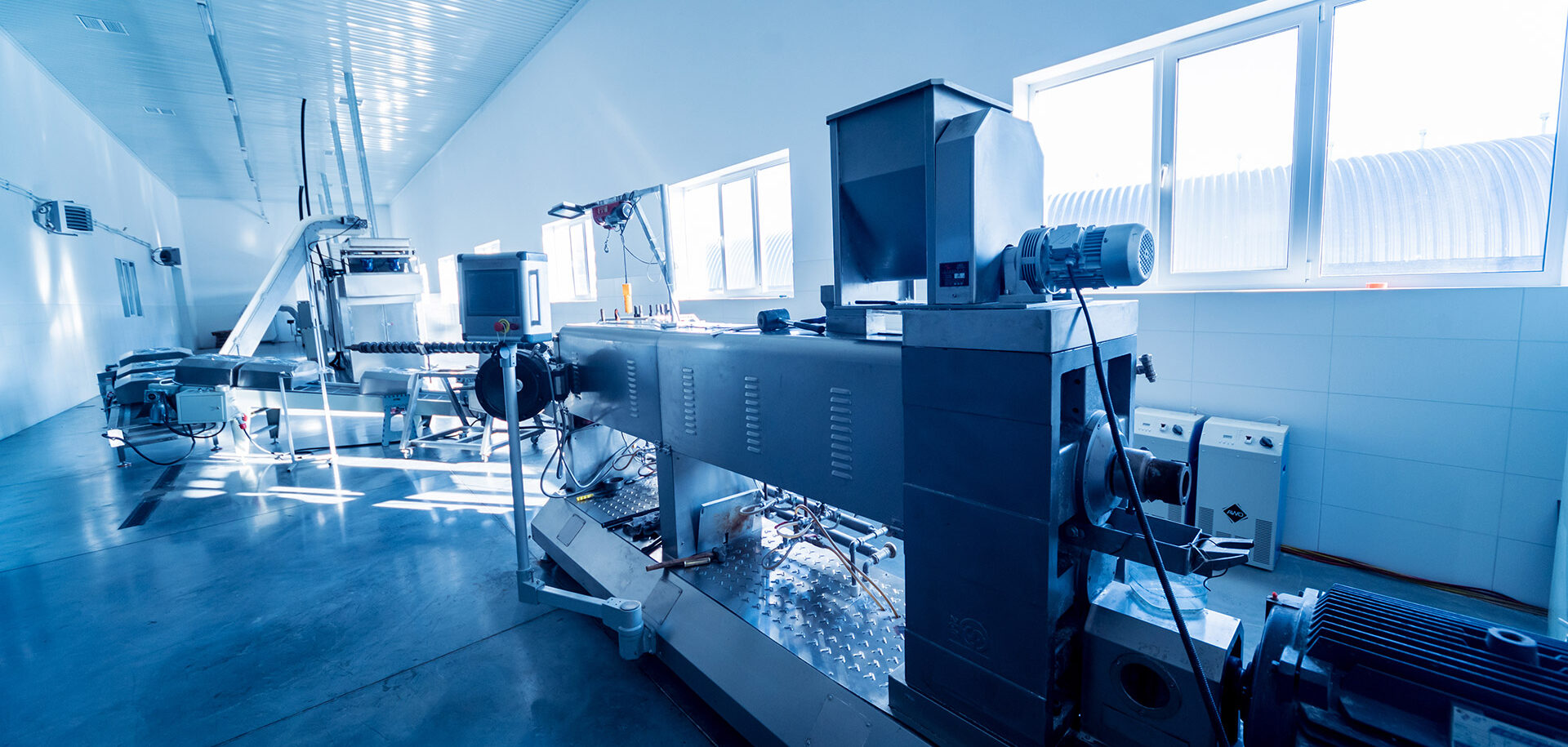
A well-oiled operation
It’s time to rethink relubrication. Thanks to an innovation from SKF, a leading snack food producer is using fryer oil to lubricate the bearings in its commercial fryers, allowing for safe operation for up to 16,000 hours without the need for relubrication or unplanned stoppages.
Bearing the burden
Even if bearings are cared for in this way, the severe operating conditions of fryers limit bearing service life to around 3,000 operating hours – or a service life of around three to six months. During this time, it is imperative that the condition of bearings and seals is monitored closely, as failure can lead to catastrophic outcomes. A fryer containing hot oil cannot just be switched off and repaired. Unplanned maintenance takes the equipment out of service for at least 24 hours and negatively impacts productivity. Operators and engineers have to take responsibility to ensure sealing and bearing integrity.
If a bearing becomes damaged it can leak lubricating grease, and pieces of the bearing itself can spill out into the fryer. With a failure of this type the oil must be drained and then strained and possibly even replaced to recover any wayward material. There is also the issue of contamination of the product. Food recalls and standards are on the rise, and any incident like this could render a product unfit for the market. The company suffers in terms of not only money and productivity but also reputation.
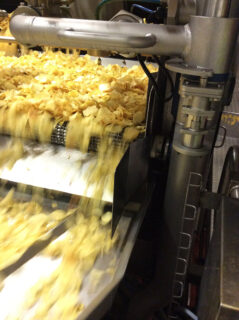
We reduced planned and unplanned downtime, providing better line availability and reduced costs – both by eliminating relubrication and associated costs and because fewer replacement bearing units are needed.
David Oliver
Global portfolio development manager, Food and Beverage, SKF
Cooking up a solution
To help food and beverage stakeholders – specifically operators of commercial fryers – combat these challenges, SKF engineers have developed a unique solution that facilitates a symbiotic relationship between the fryer and the bearing itself.
SKF’s team of experts concluded that fryer bearings’ load and speed requirements were low enough that the cooking oil itself could provide the necessary lubrication, so they set about developing a bearing with characteristics that allowed reliable operation despite the extreme temperatures and aggressive chemicals found in the customer’s equipment. The solution was a high-temperature plastic cage, specially designed to perform well in poorly lubricated environments with stainless steel rings and rolling elements.
The innovative SKF fryer bearings required no relubrication and met materials requirements for food and beverage manufacturing in corrosive environments. As a result, the snack food producer can use the same bearing for up to 17,500 hours – significantly increasing the existing bearing’s lifespan and eradicating unplanned stoppages.
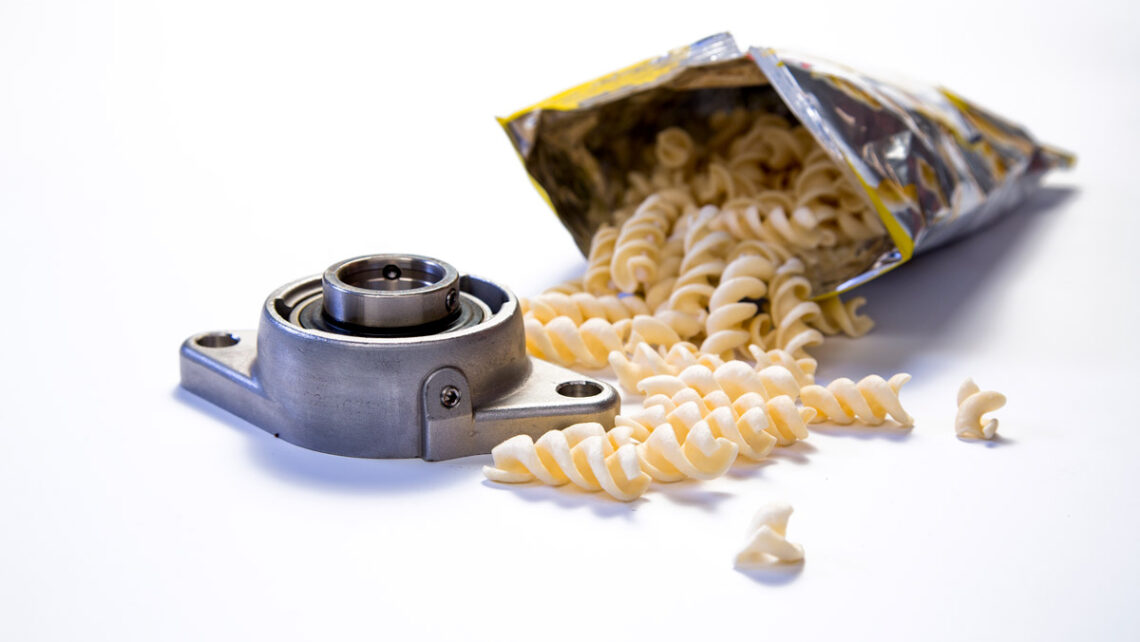
The result
In addition to reducing maintenance requirements and costs and vastly reducing the risk of catastrophic bearing failure, SKF’s relubrication-free bearings also produce a smaller environmental footprint than traditional bearings. No lubricating grease is released into the environment, nor is replacement grease required. In addition, the far longer lifespan of the SKF bearings cuts the number of bearings sent to recycling by at least half as well as reducing CO2 emissions involved in the production of new bearings.
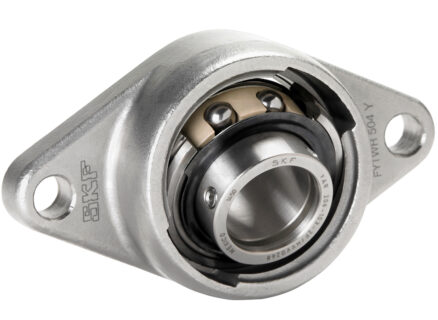
SKF FRYER BEARING UNITS
SKF’s unique fryer bearing unit design allows cooking oil to enter the bearing and act as an effective lubricant. With this solution, customers can:
- Run bearings for up to 16,000 hours
- Eliminate the need to relubricate bearings after each boil out
- Avoid process oil contamination through grease washout
- Improve corrosion resistance in an extreme operating environment.