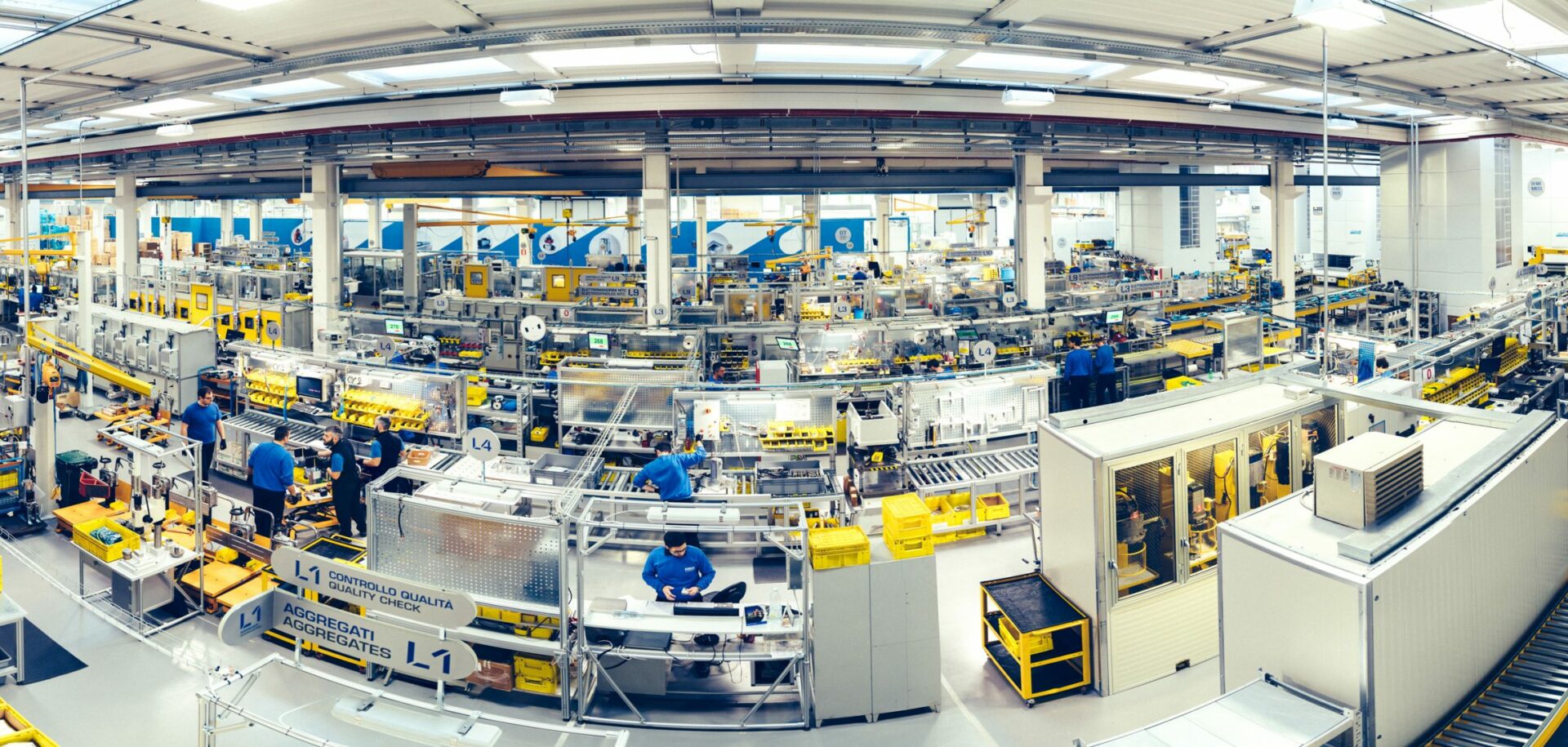
At the E-core® of the Internet of Things
The Internet of Things is becoming a core element in manufacturing and industry, including the electrospindles at the heart of the machine tooling equipment manufactured by Italian company HSD.
HSD is the world’s leading producer of electrospindles for woodworking and other light applications. The company was founded in Pesaro, Italy, in 1992, specifically to supply these spindles to its parent corporation, Biesse Group of Pesaro. HSD means “high-speed development”. Although at its inception, founder Giancarlo Selci could not have imagined a data-collecting CPU (central processing unit) inside every spindle, he foresaw that fast and flexible development would be crucial to the success of his company.
Current general manager Fabrizio Pierini joined HSD in 1995, when sales totalled about 1 million euros and the company had fewer than 20 employees. At that point, HSD produced spindles for wood-tooling applications because its primary client was Biesse, which produced machinery in that sector. But from the outset, HSD began selling to Biesse’s competitors as well, with the blessing of the parent company. “It’s a compliment to us if other producers of woodworking equipment think our products are so good that they are willing to buy them from us – a company owned by their competitor,” says Pierini.
Today, HSD represents 60 percent of the world market for electrospindles for light applications. It sells 15 percent of its output to Biesse and the rest worldwide, with a special focus on Asia, Germany and the United States.
In 2000, the company decided that over-reliance on the woodworking sector was an unwise strategy in the long term. The housing market is cyclical, and companies tied exclusively to its fortunes are similarly volatile. HSD expanded into other light applications for spindles, such as plastic, composites and marble, echoing – but independent of – similar strategic decisions by Biesse.
The more challenging market for heavy applications such as spindles for metalworking also beckoned. “Woodworking machinery is limited to the housing market, while metalworking is everywhere – automotive, aerospace, electronics,” Pierini says.
There are significant differences between light and heavy applications markets, aside from the materials themselves. Light applications are synonymous with very high speed and high volume.
Heavy applications are high torque, involving far fewer spindles per unit of machinery, but with much higher value per unit. In addition, the market for metalworking machinery is extremely closed. Pierini notes that producers are protective of their particular machinery. “Each one wants a spindle with specific characteristics customized for his equipment,” he explains. “Everything is more sophisticated, with more ‘value-added’. It’s the difference between tooling machinery for an iPhone and for an aeroplane.”
When HSD first entered the heavy sector, the market regarded the company with some scepticism. After 15 years that is no longer the case, and HSD devices for heavy applications represent 65 percent of its sales by value. “We have arrived at the point where our growth depends on the growth of our clients,” says Giuseppe Benelli, HSD sales manager. “If they have orders to build machines, they turn to us for spindles.”
The orders are coming, especially from Asia. In 2015, the company doubled its production capacity, moving from a 4,000-square-metre facility to one that’s 8,000 squares metres. An increase to 12,000 square metres is in the offing, with an eye to doubling capacity again in the not-too-distant future.
In that future, electrospindles will become increasingly intelligent, and HSD intends to continue its leadership position by embedding intelligence into its devices, which include boring heads, 5-axis heads and aggregates as well as spindles. It has registered the name E-core® to underscore this concept.
Facilitating the analytics of one’s own equipment will become HSD’s new core business, says Pierini. The ability to communicate preventive maintenance, intervene before a production line is interrupted and collect information to improve future machines is the goal.
“We are only at the beginning,” he says. “To have machines connected to headquarters is the essence of the Internet of Things.”
SKF’s partnership with HSD
SKF has been partnering with HSD since 1992. HSD’s spindles for woodworking applications call for bearings with high-speed capability, low noise levels, very low frictional moment, close tolerances and sealing options to keep lubricants in and contaminants out of bearings.
In 2012, SKF developed the S70 .. W series – a new sealed super-precision hybrid angular contact ball bearing series. A new PEEK cage was designed to reduce noise and vibration levels (especially at low to medium speeds) with the ability to accommodate very high speeds (speed factor A = 1.6 million n × dm). Incorporating these unique bearings resulted in increased productivity.
In addition, HSD benefits from increased efficiency through just-in-time delivery of the bearings, SKF technology, after-sales service and industry focus. SKF continues to work alongside HSD to improve machine performance as HSD provides solutions for light and heavy applications such as automotive, aerospace and medical.