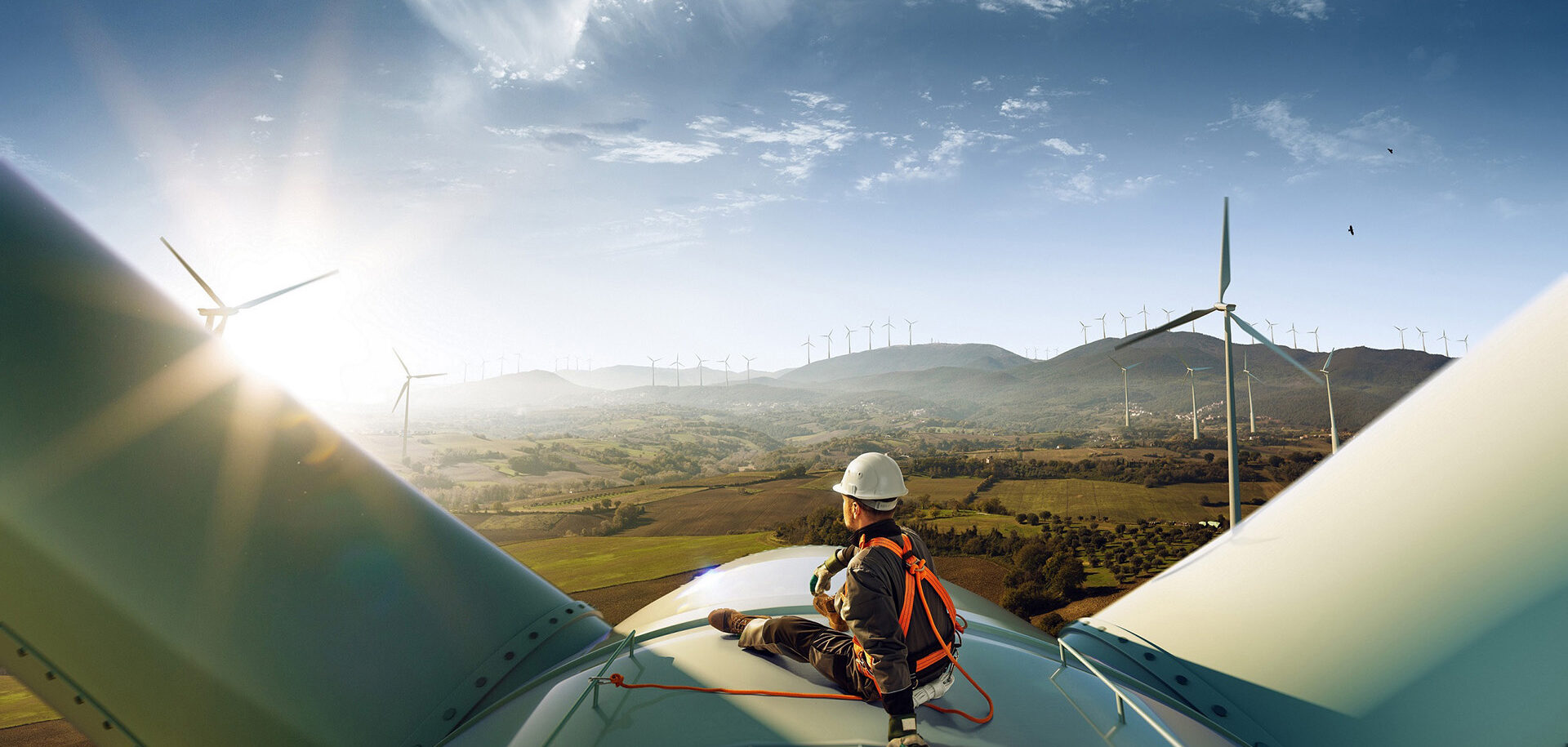
Data to reduce the levelized cost of energy
Gearboxes and main bearings are critical components in wind turbines. Failure of these components can lead to lost revenue, high emergency repair costs and, ultimately, higher energy production costs. SKF and gearbox manufacturer ZF have joined forces to take predictive maintenance of wind turbine gearboxes to the next level with the goal of supporting wind farm owners, reducing their levelized cost of energy and making renewable energy a more profitable business.
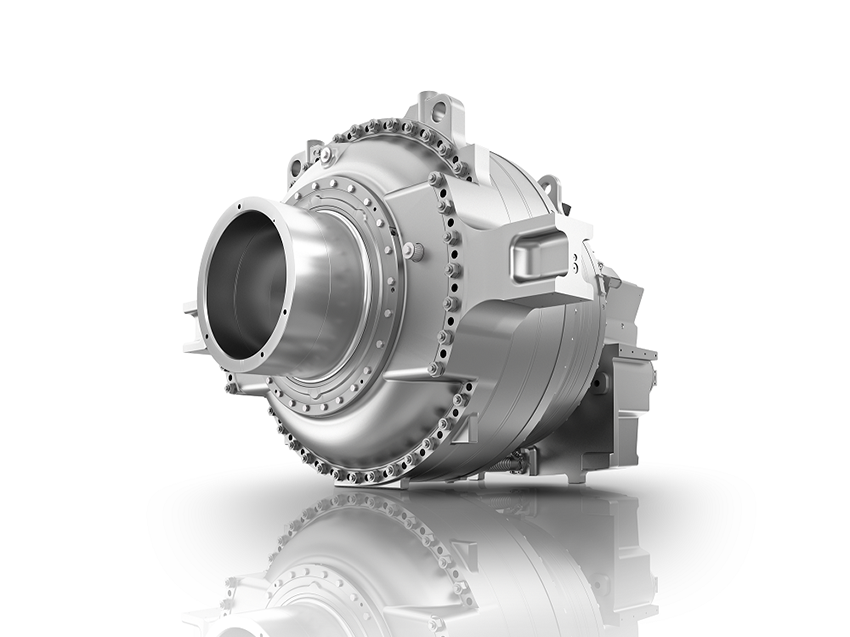
To secure a competitive price for the electricity produced by wind turbines, it is crucial that the turbines keep rotating. One way to achieve this is to focus on reducing the levelized cost of energy (LCoE) using predictive maintenance. LCoE is a concept that considers the cost of energy production over the lifetime of an energy-generating turbine. Reducing unplanned maintenance effectively increases an energy company’s profits, but it does not necessarily increase production or provide more stable production. However, addressing recurring failures both reduces the life-cycle cost of the turbine and helps to produce a larger absolute amount of energy over its lifetime.
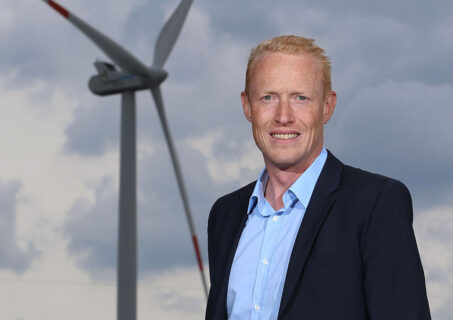
We’ve seen a customer requirement and realized that together we could create added value for the customer.
Joris Peeters, head of digitalization at ZF’s Wind Power Technology Business Unit
Simplifying processes to create added value
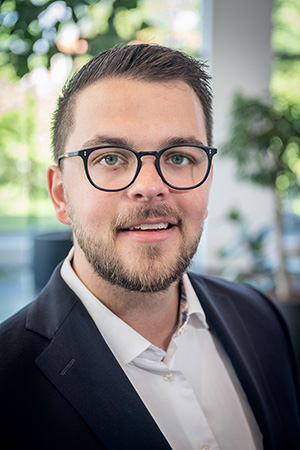
Remote condition monitoring is particularly suitable for the wind industry, as it allows turbine operators to assess the machinery while the turbine is producing energy. Now SKF and gearbox manufacturer ZF have taken predictive maintenance to a new level. Their approach significantly simplifies the process for all involved parties and cuts lead time to repair for the operator by more than 85 percent. The project has been using the ability of sensors to detect anomalies, not just in the bearings but also in the entire gearbox.
“One challenge has always been that big companies don’t share data,” says Dennis Nordmark, digitalization manager Energy Industries at SKF. “But we have 150 years of core knowledge between us. It’s a real jump that we integrate our knowledge.”
Joris Peeters, head of digitalization at ZF’s Wind Power Technology Business Unit, comments: “SKF and ZF have used a real one-year pilot project to show customers what we can do together. We’ve seen a customer requirement and realized that together we could create added value for the customer.”
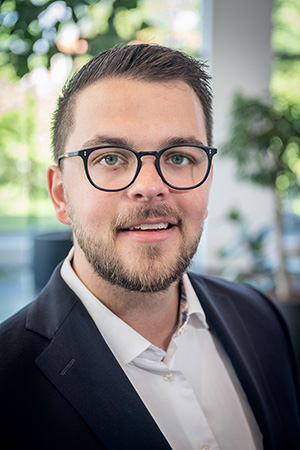
Simplifying processes to create added value
Remote condition monitoring is particularly suitable for the wind industry, as it allows turbine operators to assess the machinery while the turbine is producing energy. Now SKF and gearbox manufacturer ZF have taken predictive maintenance to a new level. Their approach significantly simplifies the process for all involved parties and cuts lead time to repair for the operator by more than 85 percent. The project has been using the ability of sensors to detect anomalies, not just in the bearings but also in the entire gearbox.
“One challenge has always been that big companies don’t share data,” says Dennis Nordmark, digitalization manager Energy Industries at SKF. “But we have 150 years of core knowledge between us. It’s a real jump that we integrate our knowledge.”
Joris Peeters, head of digitalization at ZF’s Wind Power Technology Business Unit, comments: “SKF and ZF have used a real one-year pilot project to show customers what we can do together. We’ve seen a customer requirement and realized that together we could create added value for the customer.”
SEE-THINK-ACT
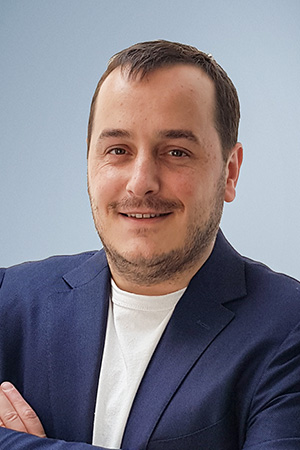
ZF Data Analytics Engineer Joris Boeye notes that the system operates according to the “See-Think-Act” principle. He explains: “The CMS detects a deviation, SKF’s analysis leads them to alert us, and we have the manufacturing data and the system knowledge to process the alert: that’s ‘See’. Then we work out what the failure is, where the turbine is located and how long until the turbine would fail: that’s ‘Think’. And finally, we organize the right work order, the right technicians and the right spare parts: that’s ‘Act’.”
“The challenge,” says Nordmark, “was to combine our core knowledge about bearing vibration with the core knowledge of the data scientists at ZF. They need to put the data into context; otherwise the data will just be data and not information.”
Analysis of deviations is part of the core domain knowledge of SKF and ZF in their different fields, he continues. “Like a car going over a pothole, the CMS sensors notice a ‘bump’ when there’s a problem in a part of the gearbox,” he says. “Obviously, detecting tiny bearing vibration differences is a lot more difficult than feeling a car bump in the road, but the principle is similar. Through the wheels and suspension of the car we can detect an anomaly. Our experience as drivers helps us identify that the likely cause is damage on the road surface. Similarly, the vibration patterns of bearings change when there is, for example, a misalignment in the shaft. The analysts at SKF and ZF, with their specialist knowledge, can together work out what vibration changes mean, which gearbox component is likely causing them, what type of repair is needed and when it should be done.
“The aim is to spot potential failures before they lead to an unplanned stoppage,” says Nordmark. “And every hour counts. Based on an electricity price of 60 euros per megawatt-hour, the daily loss for a 3.5 megawatt turbine can amount to 1,800 euros. For a stand-still time of four weeks, such an unplanned stop can amount to 55,000 euros in lost revenue.”
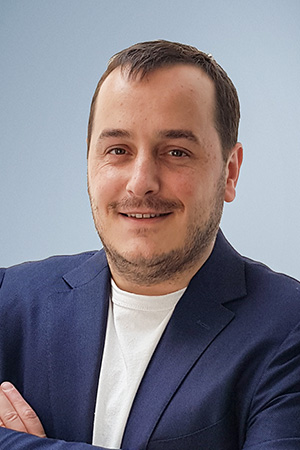
SEE-THINK-ACT
ZF Data Analytics Engineer Joris Boeye notes that the system operates according to the “See-Think-Act” principle. He explains: “The CMS detects a deviation, SKF’s analysis leads them to alert us, and we have the manufacturing data and the system knowledge to process the alert: that’s ‘See’. Then we work out what the failure is, where the turbine is located and how long until the turbine would fail: that’s ‘Think’. And finally, we organize the right work order, the right technicians and the right spare parts: that’s ‘Act’.”
“The challenge,” says Nordmark, “was to combine our core knowledge about bearing vibration with the core knowledge of the data scientists at ZF. They need to put the data into context; otherwise the data will just be data and not information.”
Analysis of deviations is part of the core domain knowledge of SKF and ZF in their different fields, he continues. “Like a car going over a pothole, the CMS sensors notice a ‘bump’ when there’s a problem in a part of the gearbox,” he says. “Obviously, detecting tiny bearing vibration differences is a lot more difficult than feeling a car bump in the road, but the principle is similar. Through the wheels and suspension of the car we can detect an anomaly. Our experience as drivers helps us identify that the likely cause is damage on the road surface. Similarly, the vibration patterns of bearings change when there is, for example, a misalignment in the shaft. The analysts at SKF and ZF, with their specialist knowledge, can together work out what vibration changes mean, which gearbox component is likely causing them, what type of repair is needed and when it should be done.
“The aim is to spot potential failures before they lead to an unplanned stoppage,” says Nordmark. “And every hour counts. Based on an electricity price of 60 euros per megawatt-hour, the daily loss for a 3.5 megawatt turbine can amount to 1,800 euros. For a stand-still time of four weeks, such an unplanned stop can amount to 55,000 euros in lost revenue.”
Improved levelized cost of energy
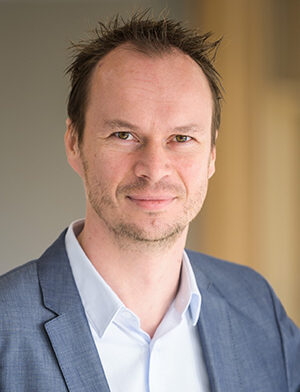
The pilot project, in a wind park with about 100 wind turbines, has shown that it’s possible. The result has been a 60 percent decrease in unplanned field inspections, an 85 percent decrease in lead time to repair and a 0.4 percent increase in annual energy production. The plan now is for a commercial roll-out of the programme during 2021.
Raf Kerkhofs, business development manager Wind Operation and Maintenance at SKF, says there’s plenty of potential. “Both SKF and ZF get insights into the operation of their products and can help customers think proactively about solutions and upgrades,” he says.
And ZF’s Peeters comments, “Currently, we are applying the new solution to existing CMS systems. Next, we can include it in new installations. We can improve the alarm settings, and in the end we could even have autonomous powertrains, which would leave the factory able to trigger their own repairs.”
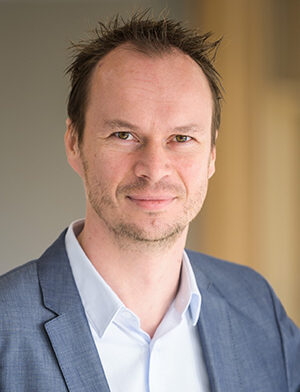
Improved levelized cost of energy
The pilot project, in a wind park with about 100 wind turbines, has shown that it’s possible. The result has been a 60 percent decrease in unplanned field inspections, an 85 percent decrease in lead time to repair and a 0.4 percent increase in annual energy production. The plan now is for a commercial roll-out of the programme during 2021.
Raf Kerkhofs, business development manager Wind Operation and Maintenance at SKF, says there’s plenty of potential. “Both SKF and ZF get insights into the operation of their products and can help customers think proactively about solutions and upgrades,” he says.
And ZF’s Peeters comments, “Currently, we are applying the new solution to existing CMS systems. Next, we can include it in new installations. We can improve the alarm settings, and in the end we could even have autonomous powertrains, which would leave the factory able to trigger their own repairs.”
SKF IMx Condition Monitoring System
The dynamic signal inputs from the system are configurable for a variety of sensors. Together with the SKF @ptitude Observer software, SKF IMx provides a complete system for early fault detection and prevention, automatic advice for correcting existing or impending conditions and advanced condition-based maintenance to improve reliability, availability and performance.
Click here to get more information how SKF can support turbine manufacturers and operators.