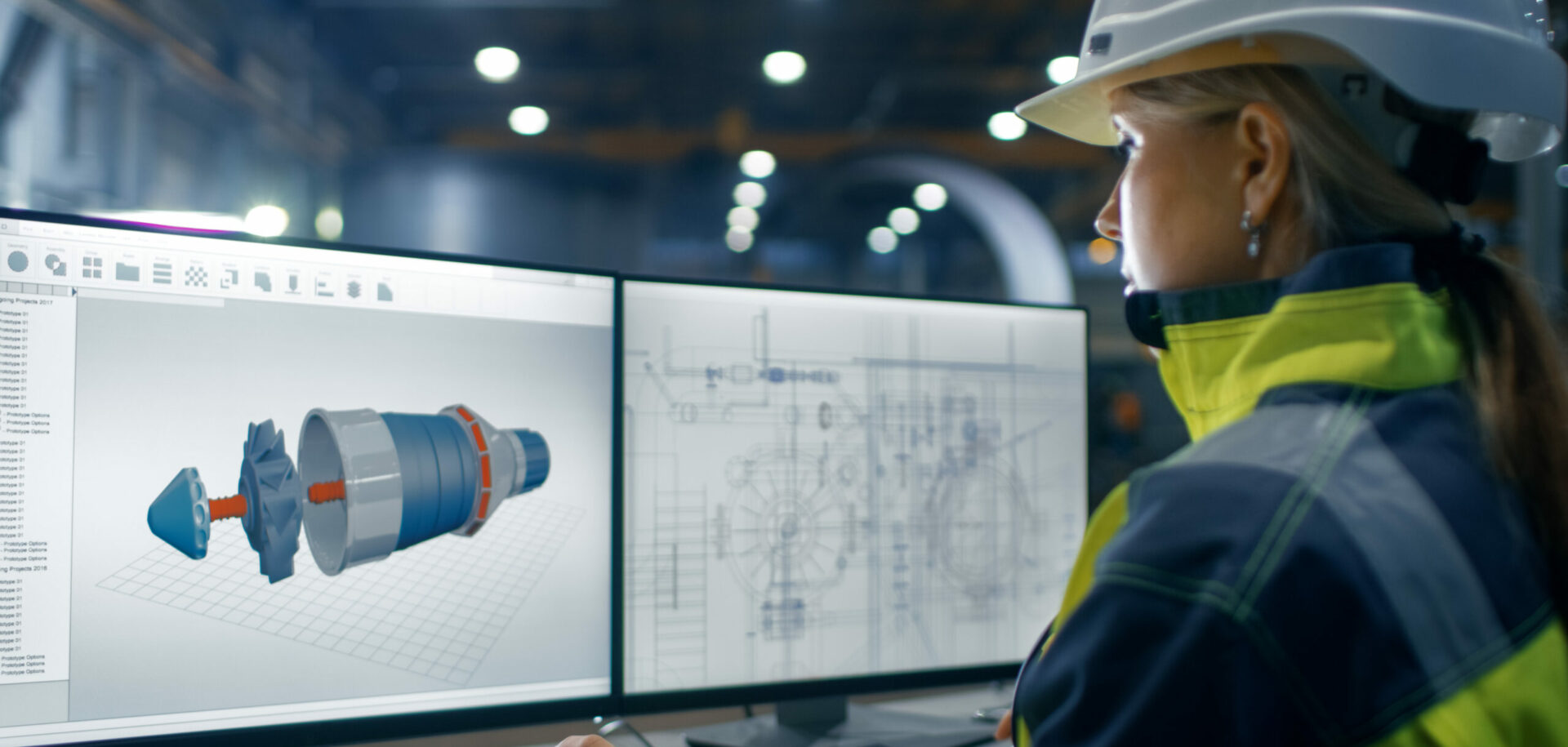
Lagerschäden vermeiden und dadurch viel Geld sparen
Die Vermeidung eines Lagerschadens oder seines erneuten Auftretens kann einen viel höheren Wert haben als das eigentliche Lager.
Fakten
Die Kenntnis der primären Schadensursache bei Lagerausfällen führt nicht nur zu einem zuverlässigen Lagerbetrieb, sondern hilft auch teure Ausfallzeiten zu vermeiden. Auch wenn die meisten Lager in ihren jeweiligen Anwendungen außerordentlich gut funktionieren, können die Ausfälle der übrigen Lager doch teure Konsequenzen haben. Nun wurde in einer ISO-Norm eine Klassifikation der verschiedenen Lagerausfallarten aufgestellt. Auf dieser Grundlage kann gewährleistet werden, dass ein Lager seine Funktion einwandfrei erfüllt. Die ISO-Klassifikation trägt zur besseren Kommunikation bei und vermeidet dadurch Missverständnisse. Die richtige Schadensklassifizierung hilft festzustellen, was die Hauptursache, aber auch die Lösung für das Problem (des Kunden) ist.
Die Vermeidung eines Lagerschadens oder seines erneuten Auftretens kann einen viel höheren Wert haben als das eigentliche Lager.
Technik
Jedes Jahr werden weltweit mehr als 10 Milliarden Wälzlager hergestellt. Die meisten überdauern die Maschinen, in die sie eingebaut sind (etwa 90 %). Manche werden ersetzt, bevor sie ausfallen (9,5 %). Aber die Lager, die ausfallen (0,5 %), können katastrophale Auswirkungen haben. Wenn ein Lager in der Hauptfertigungsstraße eines großen Werks oder in einer kritischen Anwendung ausfällt, können die Produktionsausfallkosten einige Millionen Euro betragen. Manchmal ist die eigentliche Ursache eines Lagerausfalls ganz einfach.
Betrachten wir uns beispielsweise die Entgleisung eines Güterzugs vor einigen Jahren. Ein Radsatzlager war heiß gelaufen (Bild 1). Die Achse brach und acht Waggons entgleisten, wobei Schienen und Fahrleitungen zerstört wurden. Was war die Hauptursache des Problems? Sie war schwer zu bestimmen, da beinahe alles zerstört war, aber schließlich fand man heraus, dass während eines Wartungsvorgangs ein ganz gewöhnlicher Abstandsring mit zu geringer Breite eingesetzt worden war. Die Lager konnten sich auf der Welle verschieben und infolgedessen Wärme entwickeln; schließlich brach die Welle (mitsamt der Lager).
Schadensanalyse
Wälzlager zählen bei den meisten Maschinen und Fahrzeugen zu den wichtigsten Bauteilen. Wenn das Lager jedoch versagt, stoppt die Maschine oder das Fahrzeug.
Bei den meisten Lagern treten mit der Zeit im Betrieb Änderungen im Erscheinungsbild auf. Diese Veränderungen, so genannte Laufbilder, können Aufschluss über die Betriebsbedingungen geben und darüber, was im Laufe der Lagerlebensdauer vorgefallen ist.
Bild 2 zeigt das Beispiel eines fortschreitenden Lagerschadens.
Fremdkörper (Verunreinigungen) waren in das Lager eingetreten und überrollt worden. Dies hatte eine Oberflächeneindrückung zur Folge (Verunreinigung wurde in die Laufbahn gedrückt), aber auch einen erhöhten Wulst um die Eindrückung herum, der einem Krater ähnelt. Die Laufbahngeometrie wurde örtlich verändert und folglich wurde dieser Bereich nicht mehr optimal mit einem ausreichenden Schmierfilm zur Trennung der Berührungsflächen versorgt. Das Ergebnis war eine von der Oberfläche ausgehende Werkstoffermüdung mit Rissbildung und schließlich eine Schälung hinter dem beschädigten Bereich (Bild 2a). Mit weiterem Betrieb schritt die Schälung weiter fort (Bilder 2b und 2c). Im weiteren Verlauf wurde der beschädigte Bereich so groß, dass der Entstehungspunkt, d. h. die Eindrückung, verschwand (Bild 2d).
Heute ist allgemein bekannt, dass
-
eine Ausfallursache bestimmte Eigenschaften hervorruft.
-
ein bestimmter Ausfallmechanismus eine bestimmte Ausfallart (Laufbild) bedingt.
-
sich die Hauptursache für den Lagerausfall möglicherweise aufgrund des festgestellten Schadens bestimmen lässt.
Die Internationale Organisation für Normung ISO hat viel Arbeit in die Bestimmung und Klassifizierung der unterschiedlichen Ausfallarten investiert (Bild 3). Dies führte zur Veröffentlichung der ISO-Norm 15243 im Jahr 2004. Bei den Lagerschäden werden insgesamt sechs Hauptausfallarten festgestellt, die wiederum in verschiedene Unterarten eingeteilt werden können.
Die Klassifikation basiert auf drei maßgeblichen Faktoren:
-
Schäden und Veränderungen, die im Betrieb aufgetreten sind (nachdem ein Lager das Werk verlassen hat)
-
charakteristische Veränderungen im Erscheinungsbild, die bestimmten Ursachen zugeschrieben werden können
-
Einteilung nach sichtbaren Veränderungen (einschließlich der Hilfe von Vergrößerungsgeräten, wie Mikroskopen).
Betrachten wir nun die verschiedenen Ausfallarten:
Werkstoffermüdung
Die vom oberflächennahen Bereich ausgehende Ermüdung stellt eine Verschlechterung des Werkstoffs dar. Sie wird durch zyklische Beanspruchung dicht unterhalb der Laufbahnoberfläche verursacht und führt schließlich zum Zerfall des Werkstoffs. Es entstehen Risse, die unterhalb der Oberfläche fortschreiten, und bei Erreichen der Oberfläche zu Schälungen führen (Bild 4).
Die von der Oberfläche ausgehende Ermüdung ist die Folge unzureichender Schmierbedingungen. Aufgabe des Schmierstoffs ist der Aufbau eines Schmierfilms, der die bewegten Teile voneinander trennt. Unter schlechten Schmierbedingungen, beispielsweise aufgrund von Verunreinigungen oder ungeeigneter Viskosität kommt es zu metallischem Kontakt zwischen den Oberflächen. Die Oberflächenrauheiten (Spitzen) reiben übereinander und verursachen an der Oberfläche Schubspannungen. Aufgrund von Werkstoffermüdung treten kleine Risse und anschließend so genannte Mikroschälungen auf. Anfangs kann die Oberfläche glänzend sein, da die Oberflächenrauheit verringert wird, aber dann geht der Prozess weiter und die Oberfläche wird matt und bricht immer mehr auf (Bild 5).
Verschleiß
Verschleiß ist eine typische Erscheinung, die sich in der Berührungszone bewegter Körper zeigt. Verschleiß ist in den meisten Fällen unvermeidbar. Allerdings können bestimmte Umstände Verschleiß bereits in einem frühen Stadium des Lagerbetriebs herbeiführen. Es gibt zwei Arten von Verschleiß: „abrasiver“ (spanender) Verschleiß und „adhäsiver“ Verschleiß. Sie treten aufgrund von Geschwindigkeitsunterschieden der Wälzkontaktflächen auf. Die Ursache dieser Geschwindigkeitsunterschiede können kinematisches Gleiten sowie Beschleunigungen und/oder Verzögerungen sein.
Abrasiver Verschleiß findet aufgrund von schmirgelnden Teilchen im Schmierstoff statt. Dabei kann es sich um Verunreinigungen von außerhalb oder innerhalb des Lagers handeln, beispielsweise um Abrieb von Zahnrädern und Getrieben. Diese schmirgelnden Teilchen verschleißen die Oberfläche der Laufbahnen (Bild 6) und Wälzkörper. Die Folge davon sind meist matte Oberflächen. Wenn die schmirgelnden Teilchen jedoch sehr fein und hart sind wie beispielsweise Zementstaub, kann eine polierende Wirkung eintreten und für spiegelblanke Oberflächen sorgen. Oft führen unzureichende (oder fehlende) Dichtungen dazu, dass Verunreinigungen in den Lagerhohlraum eintreten. Mit einer Schmierstoffanalyse lässt sich der Ursprung der Verunreinigungen bestimmen, was zur Lösung des Problems beitragen kann.
Adhäsiver Verschleiß tritt hauptsächlich in Berührungsflächen auf bei geringer Belastung, schlechten Schmierbedingungen und großen Geschwindigkeitsunterschieden mit hieraus resultierendem Gleiten der Wälzkörper. Ein Beispiel dafür ist der Übergang eines Wälzkörpers aus der unbelasteten Zone in die belastete Zone (Bild 7). Der Wälzkörper kann in der unbelasteten Zone an Geschwindigkeit verlieren und sich bei Rückkehr in die belastete Zone wieder beschleunigen. Dies kann zur Unterbrechnung des Schmierfilms, zum Gleiten, zu einer Wärmeentwicklung und möglicherweise zu einem Werkstofftransfer vom Wälzkörper zur Laufbahn und umgekehrt führen. In einem frühen Stadium sind die Oberflächen noch glänzend, aber sie werden schnell matt und weisen (mehr oder weniger ausgeprägte) Anschmierungen auf.
Korrosion
Feuchtigkeitskorrosion kann schwere Lagerschäden hervorrufen. Im Gegensatz zu anderen Schadensvorgängen kann Korrosion schnell auftreten und tief in den Werkstoff eindringen. Korrosion entsteht in Gegenwart von Wasser, aggressiven Medien und Feuchtigkeit. Auch eine hohe Luftfeuchtigkeit und die Berührung der Laufflächen mit den Fingern können diese Art von Korrosion hervorrufen. Ein guter Schutz ist daher wichtig. Korrosion tritt oft bei Stillstand auf und ist dann in Form von Korrosionsmarkierungen im Wälzkörperabstand sichtbar (Bild 8). Tief sitzender Rost führt zu Lagerfrühausfällen.
Passungsrost kann sehr schädlich sein. Die Hauptursache hierfür sind Mikrogleitbewegungen zwischen zwei belasteten Oberflächen. Meistens tritt diese Art von Reibkorrosion zwischen dem Lageraußendurchmesser und dem Gehäuse und/oder zwischen der Lagerbohrung und der Welle auf. Die Mikrogleitbewegungen werden hauptsächlich durch zyklische Belastungen verursacht, wenn die Wälzkörper passieren. Inadäquater Lagersitz, Wellendurchbiegung und/oder Schwachstellen an den Berührungsflächen können die Ursache hierfür sein und/oder das Auftreten von Passungsrost beschleunigen. Luft kann in die ungeschützten Oberflächen eindringen und das Fortschreiten der Korrosion beschleunigen. Das gebildete Eisenoxid nimmt ein größeres Volumen ein als reiner Stahl. Hierdurch können Werkstoffwachstum und hohe Spannungen selbst bis zur Lagerlaufbahn entstehen und zu einer vorzeitigen, vom oberflächennahen Bereich ausgehenden Ermüdung führen. Passungsrost kann leicht zu Ringbruch führen (Bild 9).
Das so genannte False Brinelling, ebenfalls eine Art von Reibkorrosion, tritt in den Berührungszonen von Wälzkörpern und Laufbahn aufgrund von Mikrogleitbewegungen und Elastizität des elastischen Kontakts unter zyklischen Schwingungen auf. Da das False Brinelling bei Lagerstillstand und unter Belastung entsteht, ist der Schaden im Wälzkörperabstand sichtbar. In Abhängigkeit von der Stärke der Schwingungen, den Schmierbedingungen und der Belastung tritt eine Kombination von Korrosion und Verschleiß ein, wobei flache Vertiefungen in den Laufbahnen gebildet werden. Normalerweise verursachen die Schwingungen eine örtliche Beseitigung des (schützenden) Schmierfilms mit metallischem Kontakt und abrasivem Verschleiß. Das Erscheinungsbild ist daher gewöhnlich matt, oft verfärbt und manchmal rötlich aufgrund des gleichzeitigen Auftretens von Feuchtigkeitskorrosion. Gelegentlich können die Vertiefungen glänzend sein, höchstwahrscheinlich dadurch bedingt, dass immer noch Schmierstoff vorhanden ist und folglich kein abrasiver Verschleiß stattgefunden hat. Schäden durch Falsches Brinelling zeigen sich bei Kugellagern in Form von sphärischen Mulden (Bild 10) und bei Rollenlagern in Linien bzw. Riffeln auf den Laufbahnen.
Elektroerosion
Jeder Strom, der durch ein Lager fließt, kann Schäden verursachen. Schäden durch Überspannung können auftreten, wenn ein elektrischer Strom ein Lager passiert, d. h. sich von einem Ring zum anderen über die Wälzkörper fortpflanzt. An den Berührungsflächen ist der Vorgang mit dem elektrischen Lichtbogenschweißen vergleichbar (hohe Stromdichte bei kleiner Berührungsfläche). Der Werkstoff wird auf ein Temperaturniveau zwischen Anlasstemperatur und Schmelztemperatur erwärmt. Dabei entstehen verfärbte, unterschiedlich große Bereiche, in denen der Werkstoff angelassen, wiedergehärtet oder geschmolzen ist. Dort, wo der Werkstoff geschmolzen ist, bilden sich Krater (in unterschiedlicher Größe von etwa 0,1 mm bis 0,5 mm) (Bild 11).
Schäden durch Kriechströme entstehen durch elektrische Streuströme, die durch ein Lager fließen; diese werden oft durch Frequenzschwankungen verursacht. Der sichtbare Hauptschaden ist eine andere Form der Riffelbildung, auch Waschbrettmuster genannt (Bild 12). Die Riffeln haben die Form von Kontaktellipsen in Kugellagern und von Berührungslinien in Rollenlagern. Die Wälzkörper sind meist gleichmäßig verfärbt. Im Vergleich zu Schäden durch Überspannung passiert der Strom hier eine größere Fläche und folglich ist die Stromstärke geringer und die schädigende Temperatur niedriger. Deshalb ist der sichtbare Hauptschaden ein Anlasseffekt, d. h. eine Herabsetzung der Härte des Stahls.
Plastische verformung
Bleibende Verformungen treten auf, wenn die Streckgrenze des Werkstoffs überschritten wird.
Überlast entsteht durch statische Belastung oder Stoßbelastung und führt zu plastischen Verformungen. Sie zeigt sich in Form von Vertiefungen im Wälzkörperabstand. Ursache des Problems sind häufig Fehler bei der Montage, d. h. Einbaukräfte werden am falschen Ring aufgebracht, wodurch eine Stoßbelastung auf die Wälzkörper ausgeübt wird (Bild 13).
Eindrückungen durch Fremdkörper werden durch Teilchen (Verunreinigungen) verursacht, die in das Lager eingedrungen und durch die Wälzkörper in die Laufbahnen eingewalzt worden sind. Größe und Form der Eindrückungen hängen von der Art der Teilchen ab. An der Eindrückung wird die Laufbahngeometrie zerstört und die Schmierung beeinträchtigt. Es entstehen Oberflächenspannungen. Werkstoffermüdung führt zu vorzeitigen Abblätterungen an der Oberfläche (Bild 14).
Eindrückungen durch unsachgemäße Handhabung können auftreten, wenn die Lageroberflächen durch harte, scharfe Objekte „ausgemeißelt“ werden. Lager müssen sorgfältig behandelt werden. Auch wenn sie aus Stahl höchster Qualität hergestellt sind, kann eine örtliche Überlastung, z. B. durch Fallenlassen, die Oberflächen eindrücken und das Lager unbrauchbar machen.
Bruch und Rissbildung
Bruch (oder Rissbildung) tritt bei Überschreitung der Zugfestigkeit (bzw. Schwingfestigkeit) des Werkstoffs auf.
Gewaltbruch wird durch Spannungskonzentrationen verursacht, die infolge örtlicher Überlastung die Zugfestigkeit des Werkstoffs überschreiten. Hierfür gibt es zwei häufige Ursachen:
-
Grobe Behandlung (Schläge) beim Ein- bzw. Ausbau eines Lagers. Hammerschläge auf einen gehärteten Meißel direkt gegen den Ring können die Bildung feiner Risse verursachen mit der Folge, dass Teile des Rings bei Inbetriebnahme des Lagers abbrechen.
-
Zu starkes Aufpressen auf einen kegeligen Sitz oder eine Spannhülse mit der Folge, dass die im Ring entstehenden Zugspannungen (Umfangsspannungen) bei Inbetriebnahme des Lagers Risse verursachen (Bild 15).
Ermüdungsbruch beginnt bei Überschreitung der Schwingfestigkeit unter zyklischer Beanspruchung. Es entsteht ein Riss, der dann wächst. Schließlich bricht der gesamte Ring oder Käfig entzwei. Ermüdungsbrüche können bei einem Presssitz mit hohen Umfangsspannungen entstehen. Dann kann die Kombination aus Hertz’scher Pressung und Umfangsspannungen zu vorzeitiger Ermüdung und durchgehenden Rissen am Ring führen.
Wärmerisse können auftreten, wenn zwei Oberflächen heftig aufeinander gleiten. Die dabei entstehende Reibungswärme verursacht Risse, die im Allgemeinen im rechten Winkel zur Gleitrichtung verlaufen (Bild 16).
Schlussfolgerung
Ein Großteil der Lagerausfälle ist vermeidbar. Mit einer sorgfältigen Schadensanalyse lässt sich meist die primäre Ursache eines Lagerschadens feststellen und bei Durchführung geeigneter Abhilfemaßnahmen kann ein erneutes Auftreten vermieden werden.
Wartungstipps
Durch Beachtung einiger Grundregeln bei der Wartung kann die Lagergebrauchsdauer oft verlängert werden.
-
Einhaltung der Spezifikationen: Ein Lager ist für eine bestimmte Belastung, bestimmte Drehzahlen etc. ausgelegt.
-
Lager nicht zu hoch belasten (aber auch nicht zu gering) und zu hohe Drehzahlen vermeiden. Die Lagerauswahl ist so groß, dass für jeden Anwendungsfall das optimal passende Lager gefunden werden kann. Sicherstellen, dass Toleranzklasse und Lagersitze richtig sind.
-
Gegebenenfalls sicherstellen, dass die Ausrichtung innerhalb angemessener Grenzwerte liegt.
-
Sauberkeit: Eine saubere Umgebung bei der Lagermontage ist eine gute Voraussetzung für eine lange Lagergebrauchsdauer.
-
Werkzeug: Für die Montage oder Demontage eines Lagers stets das geeignete Werkzeug verwenden. Ungeeignetes Werkzeug kann zu frühzeitigen Lagerschäden führen.
-
Dichtungen: Sicherstellen, dass die richtige Dichtungslösung gewählt wurde und die Dichtungen effizient funktionieren.
- Schmierung: Eine effiziente Schmierung ist äußerst wichtig. Zu wenig, zu viel oder ungeeignete Schmierung kann zu frühzeitigen Lagerschäden führen. Sicherstellen, dass der richtige Schmierstoff in der richtigen Menge zur richtigen Zeit zur Verfügung steht.