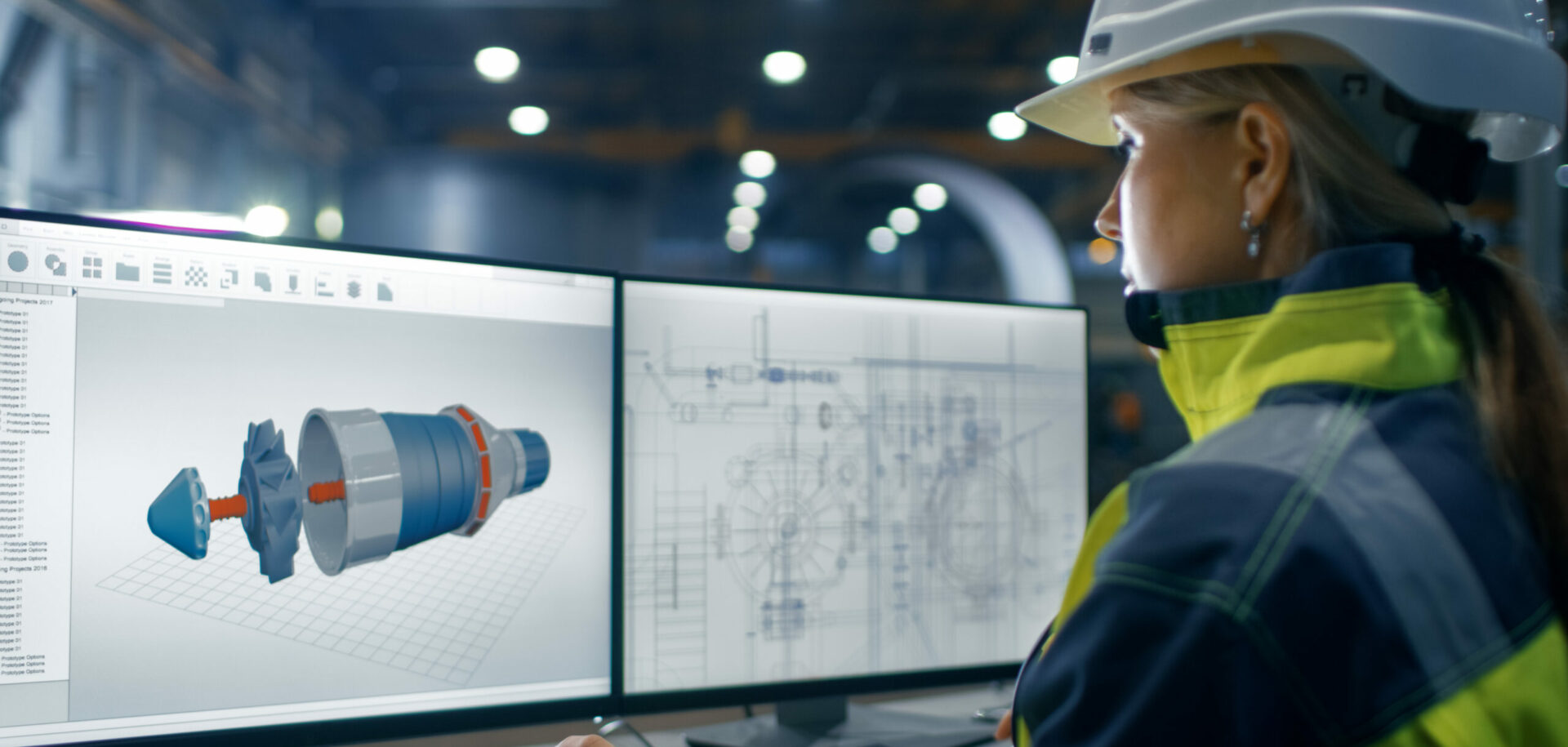
Modellierungs- und Simulationsverfahren der nächsten Generation
Dank neuer Modellierungs- und Simulationsverfahren eignet sich Software zunehmend als Analysewerkzeug. Damit kann SKF Analysen für eine spezielle Kundenanwendung leichter und mit einem viel größeren Gestaltungsspielraum durchführen und verschiedene Faktoren unter unterschiedlichen Betriebsbedingungen untersuchen.
Zusammenfassung
SKF stellt die nächste Generation von Modellierungs- und Simulationsverfahren zur Analyse von Lagerteilen und -systemen in Kundenanwendungen vor. Die leistungsstarken und leicht bedienbaren Programme sollen SKF Anwendungstechnikern die Durchführung anspruchsvollerer Analyseaufgaben ermöglichen. So wird durch Auswahl der optimalen Lösung der größtmögliche Nutzen für Kundenanwendungen erreicht.
SKF verfügt über eine langjährige Erfahrung mit Simulationsprogrammen. Diese werden ständig weiterentwickelt und mit neuen Funktionen und besserer Funktionalität versehen, um sämtliche relevanten Komponenten – Lager, Wellen, Dichtungen, Verzahnungen und Gehäuse – als vollständiges System realitätsnah zu simulieren. Heute setzt SKF in großem Umfang Berechnungssoftware in der Anwendungstechnik ein, um Kundenanwendungen unter speziellen Betriebsbedingungen zu untersuchen.
Mit den neusten Entwicklungen auf dem Gebiet Modellierung und Simulation sollen die großen Herausforderungen gemeistert werden, die sich insbesondere dann stellen, wenn Trends und Anforderungen seitens der Kunden sich ändern.
Zunächst einmal wird immer häufiger gewünscht, dass mehrere Designvarianten einer bestimmten Anwendung untersucht werden. Damit wird die Simulationsaufgabe natürlich komplexer. Bei einer Lagerung für eine Windkraftanlage hat SKF beispielsweise mehrere Konstruktionsvorschläge erarbeitet, bevor lediglich ein paar ausgewählte Alternativen dem Kunden präsentiert wurden. Dank der neuen, in die SKF Berechnungswerkzeuge integrierten Verfahren können nun Hunderte von Simulationen für die vorgeschlagenen Lagerlösungen durchgeführt werden, um die für die jeweilige Kundenanwendung am besten geeignete Ausführung zu finden.
Zweitens gilt es, die Frage von Robustheit und Sensibilität zu beantworten. Hier geht es darum, wie Lager und andere Bauteile mit den realen Bedingungen einer Anwendung zurechtkommen, die womöglich stark von den Auslegungskriterien abweichen. In manchen Fällen möchte der Kunde mehr über das Verhalten der vorgeschlagenen Lösung unter verschiedenen Betriebsbedingungen erfahren. Inwieweit wird die Leistungsfähigkeit eines Lagers davon beeinflusst, wenn ein paar Variablen, die schwer zu steuern sind, eine sehr große Streubreite haben? Um sicherzustellen, dass ein Lager stabil in der Maschine eines Kunden läuft, ist es wichtig, zu wissen, welche Betriebsbedingung mit der geringsten Variation eingehalten werden muss.
Drittens geht es darum, mehrere Variable zeitgleich zu modellieren. Auch wenn es durchaus üblich ist, bei der Modellierung und Simulation viele Faktoren als Variablen einzubeziehen, ist es nicht einfach, das gleichzeitige Zusammenwirken mehrerer Faktoren zu analysieren. Bei einer einzigen Variablen kann der Ingenieur ganz leicht ein paar Simulationen zwischen dem Min.- und Max.-Wert eines Bereiches vornehmen und anschließend ein einfaches Diagramm erstellen. Sobald aber drei oder vier Faktoren im Spiel sind, ergeben sich zwei Hauptschwierigkeiten. Eine davon betrifft die Auswahl der Simulationsparameter und deren Priorisierung, während es bei der anderen um die Analyse der Berechnungsergebnisse oder zumindest um die Visualisierung der Ergebnisse geht. Eine Möglichkeit zur Vermeidung dieser Problematik ist, jeweils nur einen Parameter zu ändern und alle anderen Parameter unverändert zu lassen, und dann nach der Durchführung der entsprechenden Simulationen die anderen Faktoren einen nach dem anderen zu ändern. Auf diese Weise erhält man Informationen über das unter bestimmten Bedingungen laufende System – das ist besser als nichts. Allerdings hat man dann noch nicht den Überblick über das Systemverhalten, insbesondere hinsichtlich des Zusammenwirkens all dieser Faktoren.
Die Lösung
Die neuste Generation der von SKF selbst entwickelten Modellierungs- und Simulationsprogramme folgt diesen Trends und sorgt für eine leichter zu handhabende Konstruktionsumgebung, in der beispielsweise Parameter einfacher änderbar sind und eine Reihe von Simulationen sich leichter durchführen lassen.
Ein wichtiges Merkmal dieser neuen Softwaregeneration ist, dass Six Sigma-Methoden in die SKF Modellierungs- und Simulationsprogramme integriert wurden. Kernstück ist dabei eine Auswahl von Methoden und Werkzeugen, die viele technische Aufgabenstellungen wie z. B. Untersuchung der Parameterabhängigkeit, Robustheitsanalyse und Ergebnisoptimierung unterstützt. Solche Methoden sind ebenfalls bei der Modellierung und Simulation wichtig. Bei SKF sind diese Funktionen in den Modellierungs- und Simulationsprogrammen der nächsten Generation enthalten. Sie können über eine sehr übersichtliche und einfache interaktive Benutzeroberfläche aufgerufen werden; die komplexen mathematischen Vorgänge und andere Six Sigma-Elemente sind hinter der Oberfläche verborgen. Auch stellen die neuen Softwareprogramme die Ergebnisse visuell auf eine intuitivere Art und Weise dar.
In der Praxis profitieren von dieser Art der Integration von Six Sigma-Methoden nicht nur die SKF Techniker und Ingenieure, sondern auch die Kunden. Seitens SKF bedeutet dies, dass jetzt mehr Mitarbeiter in der Lage sind, diese komplexen Analysen durchzuführen, die zuvor nur von erfahrenen Spezialisten mit besonderem Know-how erledigt werden konnten.
Die Kunden schätzen daran, dass sie nun eher verschiedene Designvarianten zur Auswahl vorgeschlagen bekommen und nicht nur eine. Zudem können sie zu den einzelnen Varianten mehr Informationen erhalten, wie beispielsweise, ob die jeweilige Variante bestimmten Einflüssen gegenüber empfindlicher oder aber robuster als eine andere Variante ist.
Ein weiterer Vorteil der integrierten Six Sigma-Tools besteht darin, dass die Benutzer nicht ein Programm zur Planung von Simulationen benötigen, ein weiteres Programm zur Durchführung von Hunderten von Simulationen und ein drittes dann zur Auswertung, sondern, dass die neue Software all diese Programme in einer einzigen einheitlichen Umgebung zusammenfasst und bereits nach kurzer Einweisung über eine übersichtliche und einfache interaktive Benutzerschnittstelle bedient werden kann.
Anwendernutzen
Am Beispiel eines Industriegetriebes galt es, die Gesamtsystemleistung durch Steuerung der Wärmeentwicklung zu verbessern. Neben der Modellierungssoftware wurde auch ein physikalisches Modell benutzt. Die Tests erfolgten auf einem FZG-Prüfstand mit zwei einstufigen Stirnradgetrieben gleicher Übersetzung, die mit beiden Wellen verbunden und zueinander verspannt sind (Bild 1). Zur Lagerung der Wellen wurden Radial-Rillenkugellager verwendet. Bei dieser Prüfanordnung wird die Lageraußenringtemperatur zur Beurteilung der Wärmeentwicklung insgesamt herangezogen (Bild 2).
Zur Steuerung der Außenringtemperatur wurden vier Faktoren bestimmt (siehe Tabelle 1).
Jeder dieser vier Faktoren – Emissionsgrad, Wärmeleitfähigkeit, Umgebungsluftgeschwindigkeit und rheologische Kenngrößen – wurde dann zur Bestimmung seines Einflusses auf die Außenringtemperatur modelliert. Bild 3 zeigt die Ausgangssituation der Simulation mit der für die Anwendung aktuell bekannten Einstellung im Verhältnis zur Außenringtemperatur und zu den vier Faktoren, die in Form eines Parallelkoordinaten-Diagramms abgebildet sind. Nach 100 Simulationen mit unterschiedlichen Eingabedaten (Bild 4) zeigt die Außenringtemperatur große Ergebnisschwankungen. Ein wichtiger Aspekt bei den neuen Modellierungs- und Simulationsprogrammen ist, dass Hunderte von Simulationen durchgeführt werden können; hier nach dem Monte-Carlo-Verfahren. Das Filtern und Analysieren der Wirkung eines jeden einzelnen Faktors kann mithilfe von einfachen Min.- und Max.-Schiebereglern in der grafischen Benutzeroberfläche der Software erfolgen.
Bild 5 zeigt die theoretisch optimale Lösung, die durch Filtern und eine Reihe neuer Simulationen erzielt wird. Es wird deutlich, dass es bei dem Emissionsgrad kaum eine Verbesserungsmöglichkeit zwischen der Ausgangssituation und der optimalen Situation gibt. Die Außenringtemperatur ist empfindlich gegenüber der Umgebungsluftgeschwindigkeit und eine Erhöhung dieses Wertes führt dazu, dass die Außenringtemperatur absinkt, während es gegenüber den Faktoren Wärmeleitfähigkeit und rheologische Kenngrößen so gut wie keine Empfindlichkeit gibt.
Sobald die neue Lösung mit verbesserter Umgebungsluftgeschwindigkeit modelliert ist, werden die Vorteile der verringerten Außenringtemperatur deutlich (Bild 6). Die Simulationsanalyse hat bestätigt, dass die Steuerung der Umgebungsluftgeschwindigkeit die beste Möglichkeit zur Verringerung der Lageraußenringtemperatur in dieser speziellen Anwendung ist. Entsprechend den Simulationen würde die Lageraußenringtemperatur in einem Temperaturbereich von 74 °C – 81 °C auf 69 °C – 75 °C absinken.
Für den Kunden resultiert daraus konkret, dass durch einfaches Hinzufügen eines Ventilators signifikante Leistungsverbesserungen erzielt werden. Für SKF zeigt sich, dass die Kunden von der Leistungsfähigkeit und Nutzung der verbesserten Software und Modellierungsprogramme nur profitieren können. Einerseits werden die Kunden nun in zunehmendem Maße versuchen, die Faktoren besser zu verstehen, welche die Leistung und Lebensdauer ihrer Maschinen und Anlagen beeinflussen, und andererseits zeigt SKF, dass sie sowohl über die Programme als auch das Wissen zur Bereitstellung solcher Analysen verfügt und dadurch bessere Lösungen anbieten kann.