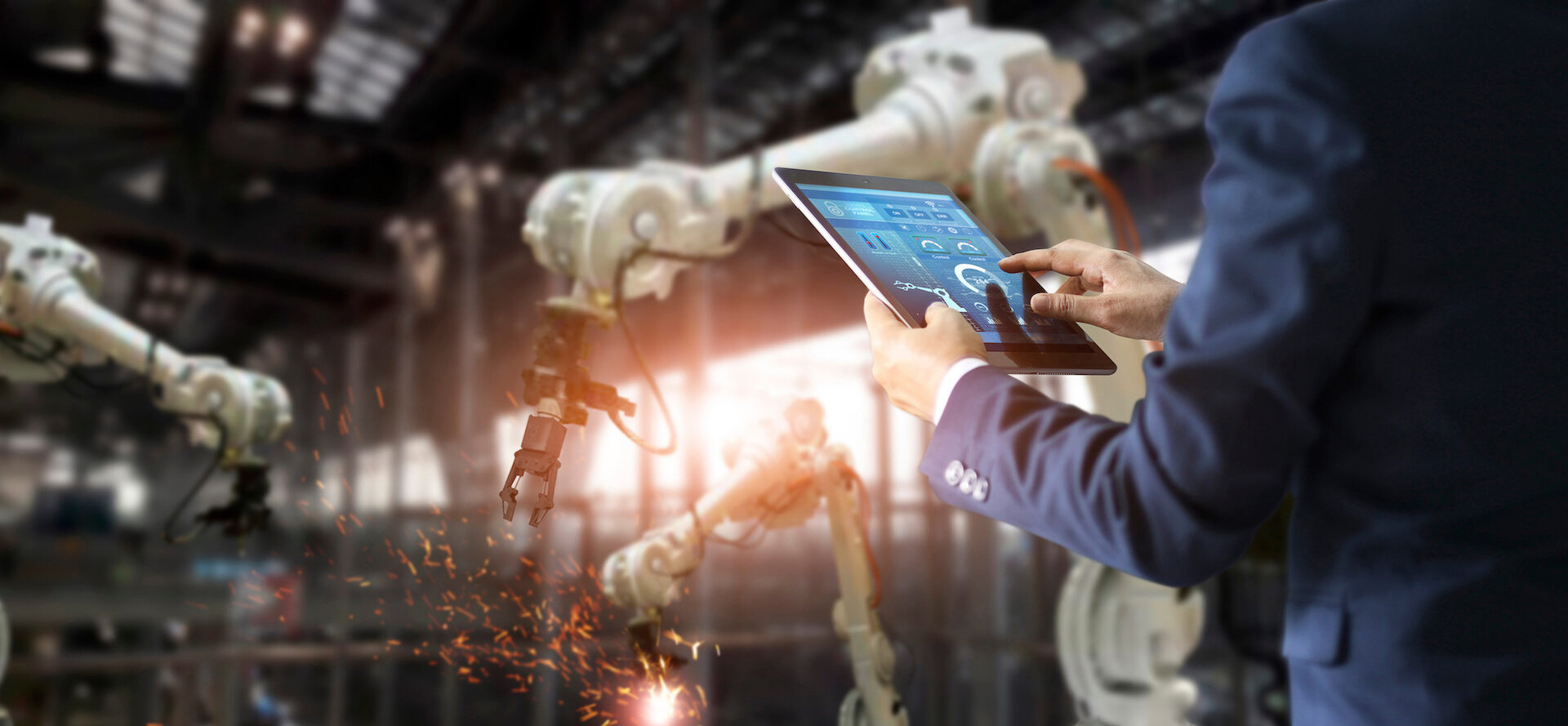
Smooth operator
Als der belgische Blähtonhersteller Argex die Laufrolleneinheiten seines Drehrohrofens austauschen wollte, wandte er sich direkt an SKF.
Als der belgische Blähtonhersteller Argex die Laufrolleneinheiten seines Drehrohrofens austauschen wollte, wandte er sich direkt an SKF.
Wirtschaft
Im naturschönen Flandern nur zehn Kilometer südlich der belgischen Stadt Antwerpen liegt das Argex-Werk direkt am Ufer der Scheldt. Eine auf der gegenüberliegenden Flussseite gelegene Zementfabrik gründete das Werk 1965, um mit der Produktion von Blähtongranulat aus dem Ton eines nahegelegenen Abbaugebietes zu experimentieren. Die Zementfabrik ist inzwischen geschlossen, aber Argex gibt es immer noch. Hier werden täglich 1.000 Tonnen Ton gewonnen, aus denen bis zu 500.000 Kubikmeter Blähton pro Jahr hergestellt werden.
„Das Blähtongranulat von Argex ist ein leichter Mehrzweck-Baustoff mit einem breiten Anwendungsspektrum“, erklärt Werksleiter Johny Bultheel. „Es kann als Füllmaterial im Tiefbau eingesetzt werden, etwa für den Bau von Straßen, Eisenbahntrassen und Wasserstraßen oder für die Herstellung von Leichtbausteinen. Das Material eignet sich aber auch hervorragend für den Bau von Sportplätzen und Gartenanlagen sowie für Fußbodenisolierungen und Industrieprodukte.“
Argex ist im B2B-Geschäft tätig. 95 Prozent der Produktion gehen an den Hoch- und Tiefbau. Die restlichen fünf Prozent werden für Landschaftsgestaltung und Hydrokultur verwendet.
Der aus einem nahe gelegenen Tagebau gewonnene Ton wird in einem zweiteiligen Drehrohrofen mit einer Produktionskapazität von 1.800 Kubikmetern pro Tag gebrannt. Das riesige Rohr von 76 Metern Länge dreht sich Tag und Nacht und verarbeitet stündlich rund 50 Tonnen Granulat. Es ist der größte Drehrohrofen seiner Art in Europa. Er wird mit Braunkohle befeuert und ist zwei bis drei Monate ununterbrochen in Betrieb. Danach wird er abgeschaltet und einer Wartung unterzogen, die zwei bis vier Wochen in Anspruch nimmt.
Der Ton wird zunächst der Trocknungsanlage des Drehrohrofens zugeführt, die sich mit einer Geschwindigkeit von einer U/min dreht. Dort wird er circa 2,5 Stunden lang bei einer Temperatur von 300 bis 800 Grad Celsius getrocknet und zerkleinert. Anschließend wird das Granulat im Brennofenteil des Drehrohrofens, der mit 5,2 U/min rotiert, weitere 30 Minuten bei 1.100 Grad erhitzt. Hierbei erfolgt der eigentliche Blähprozess. Als letzter Schritt wird der Blähton in einem Wirbelschichtkühler mit Luft gekühlt und auf eine Temperatur von 80 bis 100 Grad Celsius gebracht.
Bei der Zerkleinerung des Tons während des Trocknungsprozesses können unterschiedliche Körnungen von einem bis 25 Millimeter Größe hergestellt werden, wobei jede Körnung ihren ganz speziellen Verwendungszweck hat. Das Granulat wird schließlich nach Körnungsgröße sortiert und auf Halde gelegt.
Der Drehrohrofen ruht auf acht Laufrolleneinheiten, die jeweils zwei Lager enthalten, üblicherweise Laufbuchsen oder Gleitlager. Vor drei Jahren beschloss Argex jedoch, die Einheiten nach und nach auszutauschen und begann mit den ersten zwei.
„Es war eine Frage der Sicherheit, die durch die Unzuverlässigkeit der Gleitlager nicht gewährleistet war“, sagt Bultheel. „Wenn wir den Drehrohrofen nach dem Austausch der Lager wieder anlaufen lassen, müssen sie absolut perfekt ausgerichtet sein. Anderenfalls funktioniert die Schmierung nicht korrekt. Die Lager könnten den Schmierstoff erhitzen und entzünden.“ Argex hat das bereits zweimal erlebt. Wegen Schiefstellung der Gleitlager kam es zum Brand in den Laufrolleneinheiten. Manchmal tritt die Überhitzung sofort ein, in anderen Fällen können Wochen vergehen, bis das Problem zutage tritt. Dann muss die Produktion unterbrochen werden, um die notwendigen Einstellungen vorzunehmen. Hinzu kommt, dass die für die Einstellung der älteren Lager benötigte Kompetenz durch Personalwechsel allmählich verloren geht.
„Ein weiterer Anreiz für Wechsel zu Pendelrollenlager war der Energieverbrauch. Darauf achten wir hier immer“, erzählt Bultheel. „Wir wollten unsere Kosten senken und suchten deshalb nach einer moderneren Lösung mit einem besseren Schmiersystem und folglich einer geringeren Reibung.“
Argex wandte sich an SKF. „Eine Lagerlösung von SKF lag für uns auf der Hand, weil wir schon Kunde bei SKF waren und SKF eben die besten Produkte hat“, so Bultheel. „Wir hatten nicht das Gefühl, wir müssten uns noch nach anderen Alternativen umschauen.“
Das Projekt begann 2008 unter Aufsicht des Wartungstechnikers George Cant. Die Untersuchungen dauerten eine Weile, weil SKF gebeten wurde, nicht nur die Lager, sondern auch die Laufrolleneinheiten sowie die Welle, das Gehäuse und die Bodenplatten bereitzustellen. Dabei sollten exakt die gleichen Abmessungen wie bei der alten Lösung eingehalten werden, um die Installation zu erleichtern und die Montagekosten möglichst niedrig zu halten. Die neuen Laufrolleneinheiten, die im August 2010 installiert wurden, wiegen jeweils 23 Tonnen und sind mit einem automatischen SKF Schmiersystem ausgestattet.
„Von dem Moment, als wir das Geschäft abgeschlossen hatten, lief alles reibungslos. Seit wir die neuen Lager installiert haben, ist es zu keiner Störung mehr gekommen“, meint Bultheel. „Was wir von SKF wollten, war eine einfachere und zuverlässigere Lösung, und bekommen haben wir ein Lagersystem, das unseren Energieverbrauch um bis zu zehn Prozent reduziert. Die Investition war zweifellos beträchtlich, weswegen wir auf eine möglichst lange Lebensdauer der Pendelrollenlager hoffen.“ Argex plant zurzeit, die nächsten zwei Laufrolleneinheiten seines Drehrohrofens auszuwechseln und will, dass SKF den Auftrag möglichst bald ausführt
ARGEX
-
Gegründet 1965
-
84 Beschäftigte
-
Dauerbetrieb (24 Stunden – 7 Tage pro Woche)
-
Produktionskapazität: 500.000 m³/Tag
-
Tagesproduktion 1.800 m³ Granulat
-
Tonabbau: 1.000 Tonnen pro Tag
ProduktfaktenDas Blähtongranulat von Argex ist
-
ökologisch: 100 Prozent Ton
-
leicht: Dichte von 320 – 750 kg/m³
-
isolierend: wärme- und schalldämmend inert: chemisch neutral äußerst tragfähig nicht brennbar frost- und hitzebeständig drainierend
Argex in Zahlen
Tonnen Granulat/Stunde 50
Länge des Drehrohrofens in Metern 76
Tonnen Blähton/Tag 1.000
m3 Granulat/Tag 1.800
Maximale Temperatur im Ofen (oC) 1.200