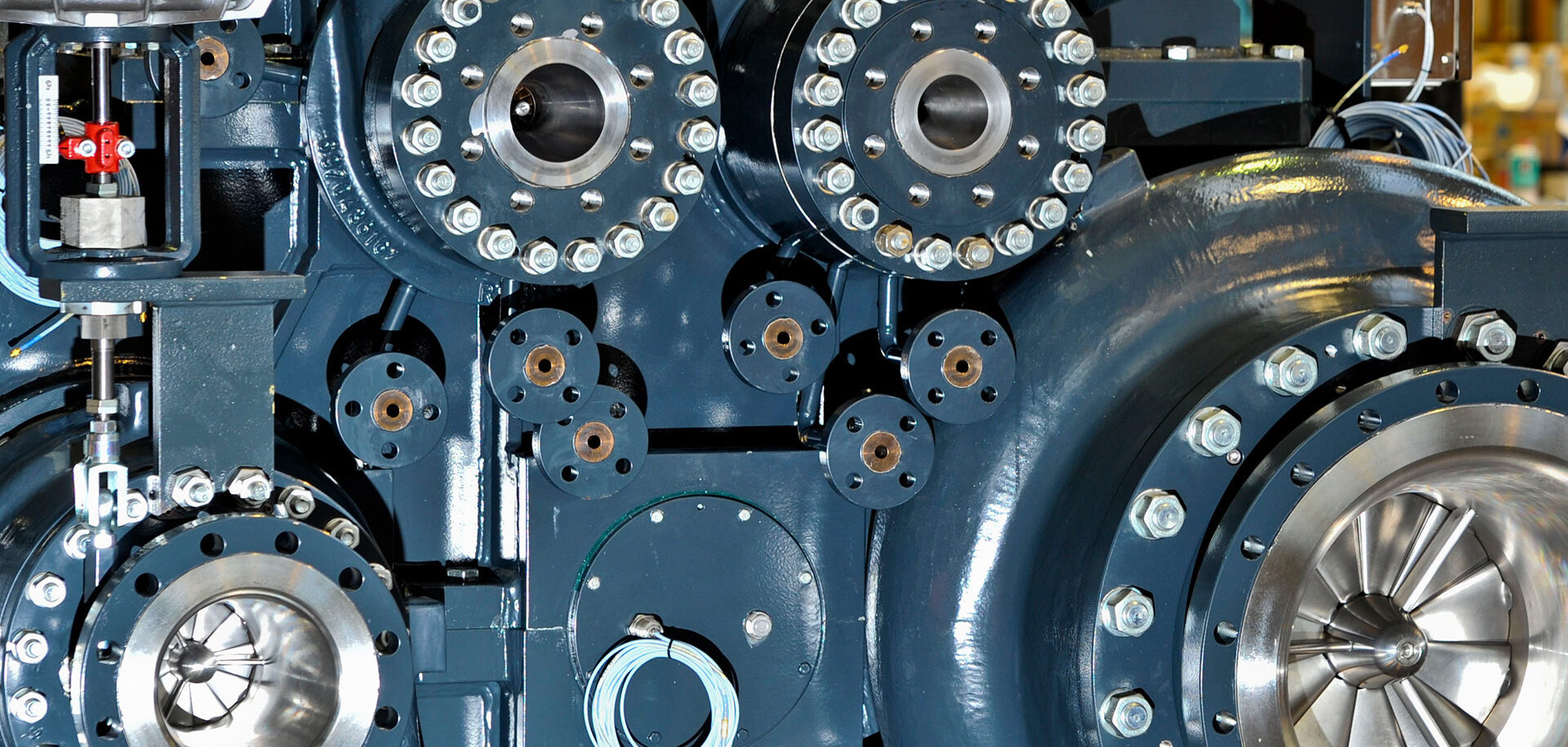
Vorteilhafter Wechsel von hydrodynamischen Gleitlagern zu Wälzlagern
Lösungen und Engineering-Kompetenzen von SKF ermöglichen den Umstieg von hydrodynamischen Gleitlagern auf effizientere Wälzlagersysteme.
Die Bedeutung der Energie- und Ressourceneffizienz, insbesondere in der Industrieproduktion und Stromversorgung, ist weltweit so wichtig wie nie zuvor. Ungeachtet des technologischen Fortschritts geht weltweit immer noch viel Energie durch mechanische Reibung und fluiddynamische Verluste in rotierenden Maschinen wie Kompressoren, Turbinen, Gebläsen und Pumpen verloren. Im Folgenden wird erklärt und anhand von Beispielen aus der Praxis dargelegt, wie durch den Ersatz von hydrodynamischen Gleitlagern durch moderne Wälzlager erhebliche Energie- und Kosteneinsparungen erzielt werden können.
Bei Industrieanlagen wie Pumpen, Kompressoren und Gebläsen sind jährliche Laufzeiten von 4.000 bis 8.000 Stunden durchaus üblich, was bedeutet, dass die elektrische Energie für den Antrieb dieser Maschinen meist den weitaus größten Anteil an den Lebenszykluskosten (LCC) und Emissionen darstellt. Ein wirksames Mittel zur Verbesserung der Energieeffizienz ist in vielen Fällen der Einsatz von Direktantrieben mit variabler Drehzahlregelung (VFD-Antriebe) sowie die Auswahl und sorgfältige Auslegung des Rotors bzw. des Laufrads, der Lager und des Dichtungssystems.
Seit Jahrtausenden werden Wälzkörper (Stäbe, Rollen und Kugeln) eingesetzt, um die Reibung und den Wärmeverlust beim Transport und bei rotierenden Maschinen zu verringern und eine genaue und zuverlässige Positionierung von rotierenden Wellen zu erreichen. Aus diesem Grund werden Wälzlager im Englischen manchmal auch als „anti-friction bearings“ oder „precision bearings“ bezeichnet. Aus verschiedenen technischen und historischen Gründen werden jedoch weltweit immer noch viele Gleitlager, also „friction bearings“, verwendet, insbesondere hydrodynamische oder hydrostatische Gleitlager.
Hydrodynamische Gleitlager im Vergleich zu Wälzlagern
Bei hydrodynamischen Gleitlagern wird die Stahloberfläche der rotierenden Welle mittels eines Ölfilms von der stillstehenden Gehäusebuchse getrennt, wobei die seit langem bekannten Grundsätze der hydrodynamischen Schmierung genutzt werden. Gut geschmierte hydrodynamische Gleitlager weisen so gut wie keine Ermüdung und keinen mechanischen Verschleiß auf und besitzen eine höhere Ölfilmdämpfung als Kugel- oder Rollenlager. Aufgrund des relativ dicken Ölfilms haben Schmutz und andere Teilchen einen geringeren Einfluss auf die Lebensdauer, da die harten Teilchen teilweise in die weicheren Buchsen- oder Kippsegment-Materialien eingebettet werden und somit die Gegenlaufflächen nicht beschädigen können.
Hydrodynamische Gleitlager haben jedoch ein relativ großes Spiel und zeigen Verschleiß und Fressschäden bei häufigen Start-Stopp-Vorgängen oder sehr niedrigen Drehzahlen, was bei VFD-Anwendungen der Fall sein kann. Wenn die Viskosität des Schmieröls niedrig ist oder das Öl durch die Prozessmedien stark verdünnt wird, reicht der Schmierfilmaufbau unter Umständen nicht mehr aus, um eine gute Leistung der hydrodynamischen Gleitlager zu gewährleisten, vor allem bei Axial-Kippsegmentlagern. Hier stellen Wälzlager eine gute Alternative dar, da sie mit Schmierstoffen geringerer Viskosität und höherer Verdünnung betrieben werden können, insbesondere wenn Keramikwälzkörper verwendet werden.
Auch im intermittierenden Betrieb und in kalten Umgebungen sind Wälzlager wegen ihrer geringen Anlaufreibung oft die erste Wahl, insbesondere beim Einsatz von Hybridlagern mit Keramikwälzkörpern. Noch bedeutender für die Energieeffizienz ist, dass die Rollreibung bei Wälzlagern in der Regel viel geringer ist, zumindest im niedrigen und mittleren Drehzahlbereich. Nach Angaben von J/E Bearing & Machine Ltd [1] benötigt der gesamte Schmierfilm in hydrodynamischen Gleitlagern bis zu dreimal mehr Energie für den Betrieb, selbst wenn die Anlaufverluste unberücksichtigt bleiben. Die nachstehende schematische Darstellung zeigt ein typisches Ergebnis beim Vergleich von Reib(leistungs)verlusten bei Gleitlagern gegenüber Kugel- oder Rollenlagern.
Auf Erfolgskurs: Wälzlager in Turboladern und Kurbelwellen
Technikexperten und Anhänger von PS-starken Fahrzeugen wissen, dass kugelgelagerte Turbolader die Motorsportszene beherrschen, seit die ersten Kugellager bei den 24-Stunden-Rennen von Le Mans in den 1990er-Jahren die Gleitlager in Turboladern ersetzten. Dafür gab es zwei Hauptgründe. Erstens wiesen die Kugellagersysteme eine geringere Laufreibung auf. Und zweitens brauchte man keine Hochdruck-Ölpumpen mehr, die bei Gleitlagersystemen, bei denen viel Öl durch kleine Löcher in den Gleitlagerhülsen gepumpt werden muss, Leistungsverluste verursachen. In neueren Konstruktionen werden platzsparende Cartridge-Einheiten mit Hybrid-Keramikkugellagern verwendet, mit denen eine noch höhere Leistung erzielt werden kann.
Hohe Einsparungen bei der Ökostromerzeugung
Ein unlängst errichtetes 250-MW-Geothermiekraftwerk in Asien nutzt die ORC (Organic Rankine Cycle)-Technologie zur Erzeugung von Ökostrom aus Erdwärme. Fast 200 sogenannte Schraubenexpander werden zum Antrieb der Stromgeneratoren eingesetzt. Schraubenexpander arbeiten nach dem gleichen mechanischen Prinzip wie Schraubenverdichter, jedoch in umgekehrter Richtung, um Energie aus expandierendem Dampf zu erzeugen – ähnlich wie eine Dampfturbine. Eine besondere technische Herausforderung bestand darin, die vom Anlagenbesitzer gesetzten Effizienzziele zu erreichen. Erste Tests zeigten, dass dies bei Verwendung von hydrodynamischen Gleitlagern nicht möglich war. Man beachte dabei, dass in jedem der großen Schraubenexpander fünf oder sechs hydrodynamische Gleitlager eingesetzt werden.
Aus diesem Grund schlugen die Ingenieure von SKF die Überarbeitung des Schraubenexpanders für den Einsatz von Wälzlagern vor. Neben der geringeren Laufreibung ermöglichen die engen Toleranzen der Wälzlager, dass die Schraubenexpander mit sehr kleinen Endspaltmaßen zwischen Verdichterwellen und -gehäuse betrieben werden können, was die Effizienz weiter erhöht. Berechnungen und Tests zeigten, dass die jeweiligen Energieverluste erheblich reduziert werden konnten, normalerweise von 30 kW auf 12 kW, was bedeutet, dass ein einziger Expander 18 kW mehr Strom erzeugen kann, wenn ein Wälzlagersystem zum Einsatz kommt.
Die Einsparung von 18 kW an Leistungsverlusten kann mehr als 100.000 kWh an zusätzlicher elektrischer Energie bedeuten – pro Maschine und pro Jahr. Hochgerechnet auf die große Anzahl von Schraubenexpandern, die in dieser Geothermie-Anlage eingesetzt werden, ergibt dies einen zusätzlichen Gewinn von rund 1 Million Euro pro Jahr.
Industrielle Kälteanlagen und Wärmepumpen
Große gewerbliche oder industrielle Kälteanlagen oder Wärmepumpen arbeiten in der Regel mit Radial- oder Kolbenverdichtern, die ein Kältemittelgas verdichten, um eine Wärmeübertragung von einer Quelle mit niedrigerer Temperatur zu einer Empfängereinheit mit höherer Temperatur zu ermöglichen. Bisher wurden bzw. werden viele Kältemittelverdichter über ein Getriebe mit oftmals hydrodynamischen, mit einem Öl-Kältemittel-Gemisch geschmierten Gleitlagern angetrieben.
Die Einführung neuer umweltfreundlicher Kältemittel (z. B. Hydrofluorolefine (HFO) mit geringem Treibhauseffekt- und Ozonabbaupotenzial) und die viel höheren Temperaturwerte, die in Wärmepumpen oder Kälteanlagen für Rechenzentren benötigt werden, haben oft einen unerwünschten Effekt: Das Öl wird durch die Kältemittel stark verdünnt, manchmal bis zu einem Verdünnungsverhältnis von 50 % oder darüber. In manchen Fällen reicht die Ölviskosität für hydrodynamische Gleitlager dann nicht mehr aus und die Lagerung der Kompressoren muss auf Wälzlager umgestellt werden, was zusätzliche Vorteile wie geringere Reibverluste und eine höhere Positioniergenauigkeit des Laufrads mit sich bringt.
Die Daten zeigen, dass Wälzlager geringere Lagerreibverluste verursachen und aufgrund der höheren Laufgenauigkeit auch geringere volumetrische Dichtspaltverluste aufweisen. Ein positiver Effekt hinsichtlich des Wirkungsgrads wird auch der Tatsache zugeschrieben, dass Wälzlager viel weniger Öl (normalerweise weniger als 10 %) zur Schmierung benötigen als hydrodynamische Gleitlager, so dass sich weniger Öl mit dem Kältemittel vermischt, was zu einer geringeren Ölverschmutzung der Wärmetauscher führt. Durch den Einbau von ölgeschmierten Wälzlagern anstelle von hydrodynamischen Gleitlagern können somit Effizienzsteigerungen von 3 % bis 4 % erzielt werden. Ein weiterer wichtiger Schritt in Richtung Effizienzsteigerung wäre die Konstruktion ölfreier Kältemaschinen, bei denen entweder SKF Magnetlager oder keramische SKF PRL (Pure Refrigerant Lubricated)-Wälzlager zum Einsatz kommen (siehe die SKF Broschüre Evolving Chiller Performance und diesen Evolution-Artikel).
Großer Ammoniak-Schraubenkompressor
Vor einiger Zeit war SKF maßgeblich an der Entwicklung einer neuen Generation von großen Ammoniak-Schraubenkompressoren für Kältemaschinen und Kühlanwendungen beteiligt. Der Kunde, ein führendes Unternehmen auf diesem Gebiet, hat normalerweise hydrodynamische Gleitlager mit relativ viel Lagerluft zur Aufnahme der Radiallasten und Schrägkugellager für die Axiallasten verwendet. Derzeit werden Zylinderrollenlager mit kleinen Radiallufttoleranzen als Alternative zu hydrodynamischen Gleitlagern erprobt. Dadurch verbessert sich nicht nur der volumetrische Wirkungsgrad des Kompressors, auch der Ölverbrauch der Kompressoranlage lässt sich so reduzieren.
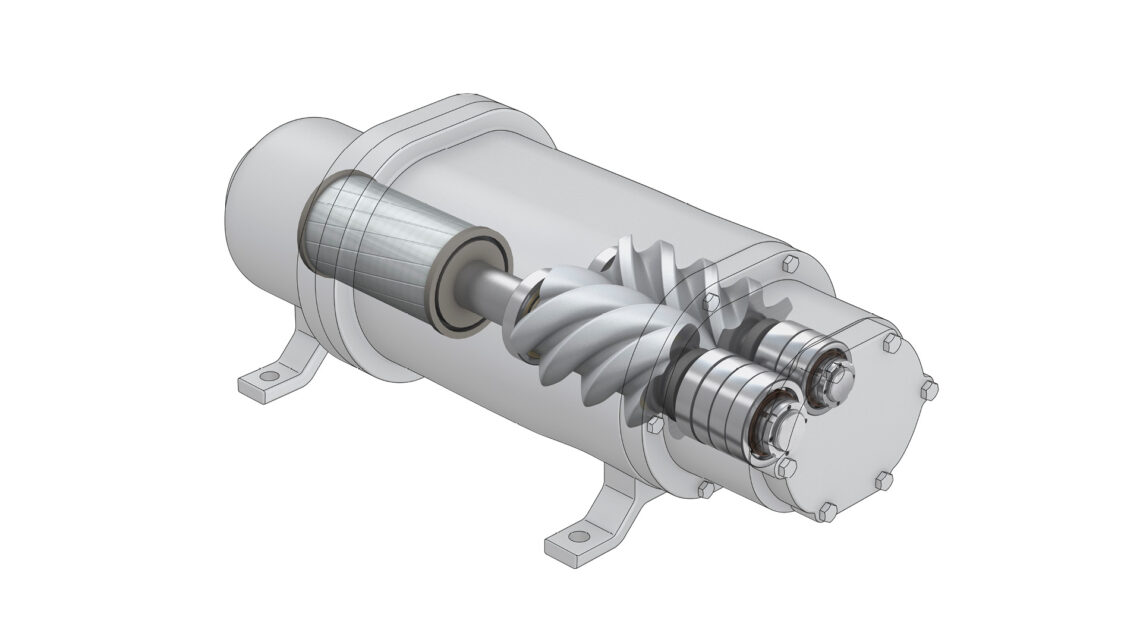
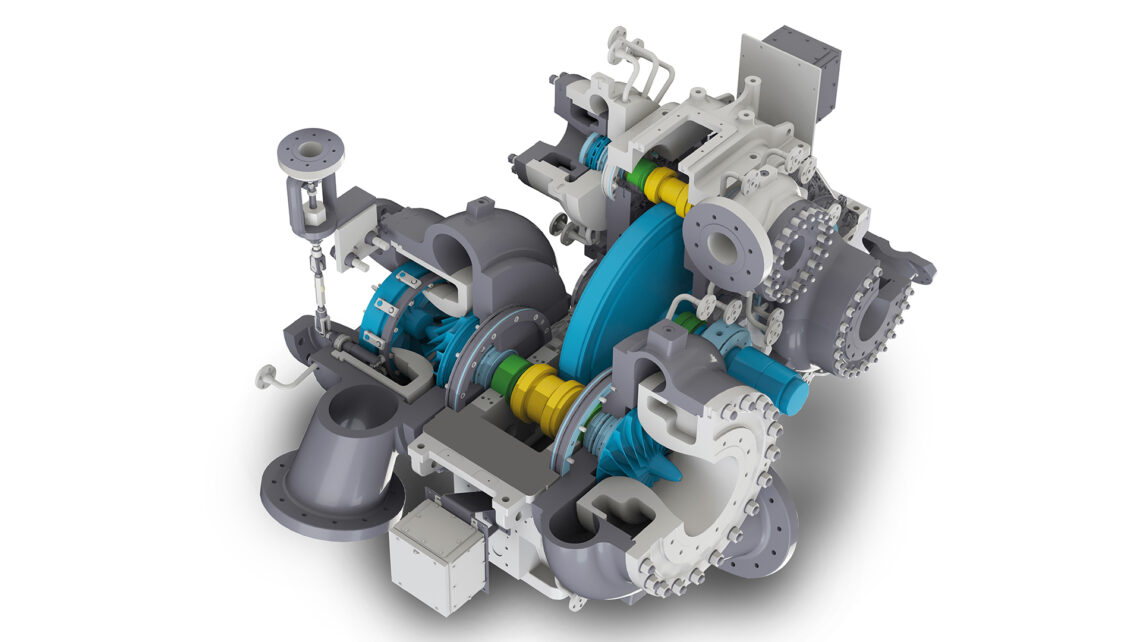
Dieses Bild und das Titelbild stammen von Atlas Copco Gas and Process.
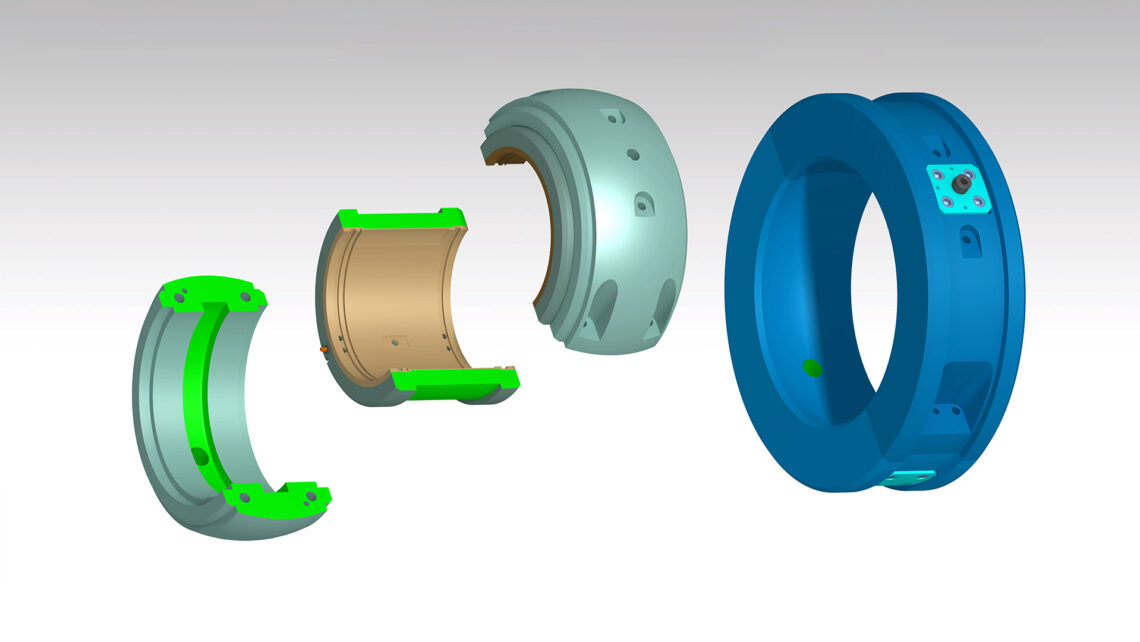
Vorteile von Wälzlagern gegenüber hydrodynamischen Gleitlagern:
- Durch die hohe Positioniergenauigkeit sind geringe Spaltmaße bei Dichtungen und Laufrädern möglich, wodurch Strömungsverluste reduziert werden (Volumenverluste).
- Geringere Laufreibung
- Besser geeignet für häufigen Start-Stopp-Betrieb oder sehr niedrige Drehzahlen (z. B. für VFD-Antriebe)
- Verträglich mit niedrigen Viskosewerten und hohen Ölverdünnungsgraden
- Normalerweise werden 90 % weniger Schmieröl benötigt und das Ölversorgungssystem braucht weniger Wartung.
- Niedrigere Systemkomplexität und geringere Kosten des Gesamtsystems
- Einfachere Lagerungen für Axial- und kombinierte Lasten oder bei hohen Wellenschiefstellungen
[1] J/E Bearing & Machine Ltd., “Plain or Rolling Bearings – Which is Best?”
[2] Vanhaelst R, Kheir A, Czajka J, “A Systematic Analysis of the Friction Losses on Bearings of Modern Turbocharger”, Combustion Engines 1/2016 (164), pages 22–31.
[3] Morales G E, Hauleitner R, Wallin H H, “Pure Refrigerant Lubrication Technology in Oil-Free Centrifugal Compressors”, Evolution 2 March 2017.
[4] “SKF GBLM – A New Rating Life Model Applied to Hybrid Bearings”, Evolution 4 February 2021.