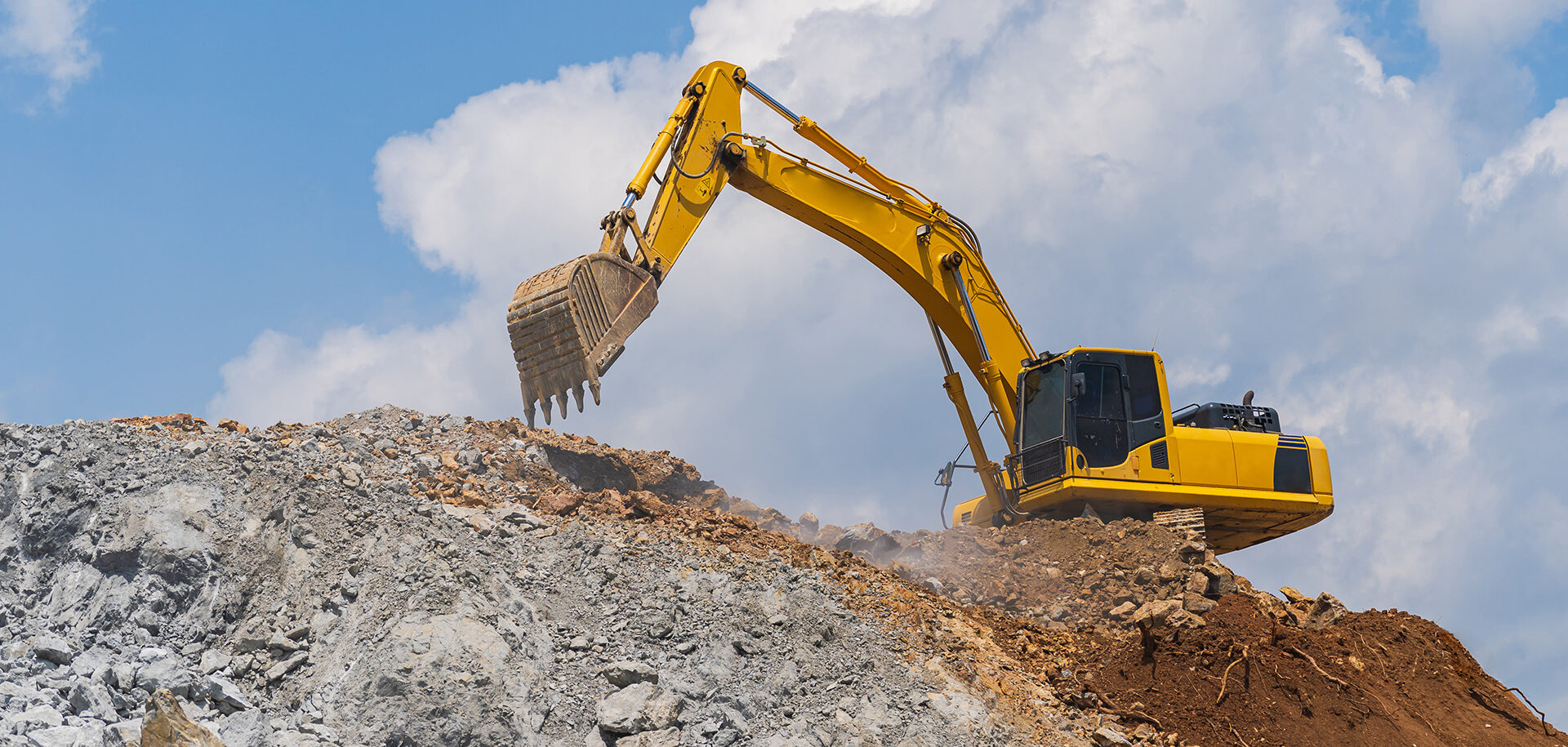
Mayor vida útil de los cilindros hidráulicos usando sellos de amortiguación (buffer) de fricción optimizada
En los sistemas hidráulicos, los fluidos se presurizan para generar, controlar y convertir la potencia del fluido en movimiento alternativo. Su eficacia la define la energía generada respecto de la entrada de energía. Los sellos pueden influir poderosamente sobre esta eficacia energética.
La sostenibilidad –un concepto que cada vez adquiere mayor importancia– ha llegado a alcanzar casi cada sector del mundo. Un sistema hidráulico sostenible debe estar exento de fugas pero, asimismo, el intervalo entre las paradas de mantenimiento debe poder prolongarse lo más posible. Desde el punto de vista de los sellos, esto puede lograrse seleccionando el mejor sistema de sellado posible –que conste de sellos de vástago y pistón así como elementos guía y sellos estáticos– para conseguir la máxima eficacia. Por ello, hay que conocer los tipos de sello propiamente dichos, pero también las in-teracciones entre estos tipos de sello diferentes, a fin de lograr el objetivo de un sistema de sellado altamente eficaz.
Este artículo aborda los sistemas de sellado de vástagos usados en aplicaciones hidráulicas (por ejem-plo, excavadoras). Especialmente en investigaciones internas en bancos de pruebas y en estudios de FEA se han analizado profundamente las interacciones entre el sello de amortiguación y el de vástago primario. El resultado de esta labor son dos nuevos sellos de amortiguación de fricción optimizada de SKF.
Sistemas de sellado de vástagos hidráulicos y funciones de sellado principales
El sistema de sellado en un cilindro hidráulico consta, por lo general, de un sello de amortiguación, un sello de vástago primario y un rascador (figura 1).
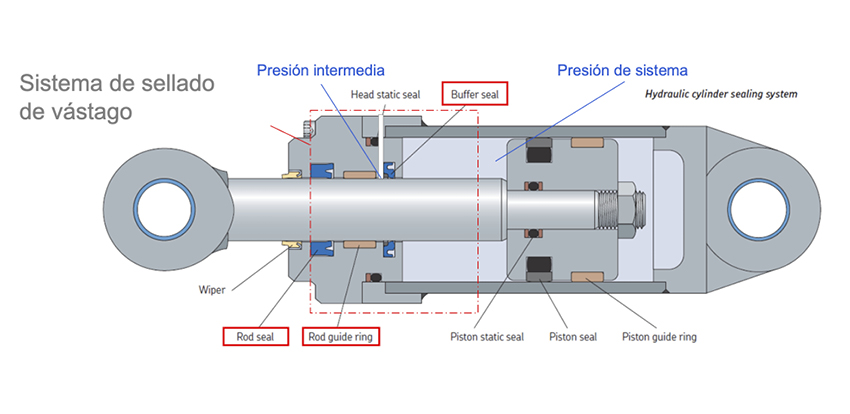
- Absorber los picos de presión del sistema (ppico) que puedan dañar el sello de vástago primario
- Permitir que el aceite pase más allá del labio de sellado para proporcionar lubricación al sello de vástago primario y al rascador (ver la figura 2)
- Aliviar la presión intermedia (ver la figura 1) entre el sello de amortiguación y el sello de vástago primario cuando la presión del sistema sea inferior a la presión intermedia, para evitar una re-tención de presión
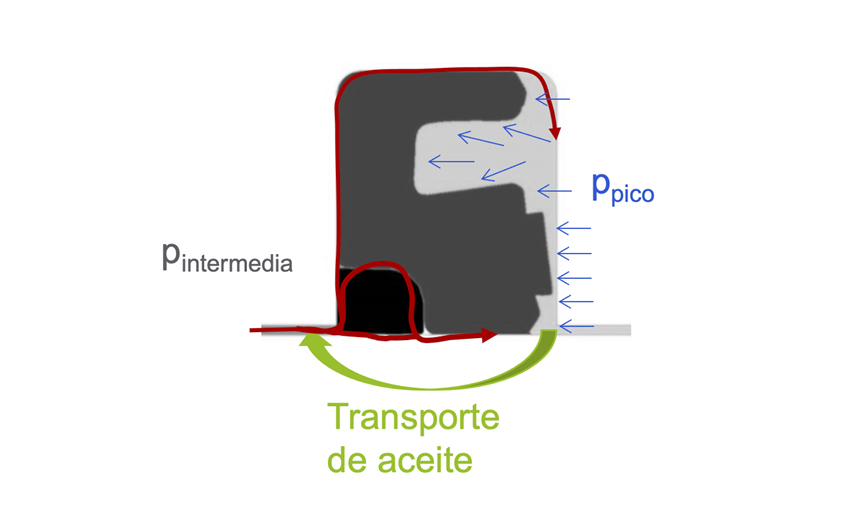
- Evitar fugas reduciendo el espesor de la película de lubricación y permitir el retrobombeo en el sistema
- Equilibrar el espesor de la película de lubricación para mantener, por un lado, las mínimas fugas posibles y, por el otro, una baja fricción
- Absorber la presión intermedia que podría originarse
El rascador debe ofrecer las siguientes funciones principales:
- Excluir toda clase de contaminación procedente del entorno
- Evitar fugas teniendo capacidad de retrobombear el lubricante en el sistema
- Aliviar la presión intermedia que podría generarse entre el sello de vástago y el rascador
Tipos de sello de amortiguación
Para cumplir con las funciones de sello de amortiguación antedichas y el objetivo general de un sistema de sellado de vástago altamente eficaz, el sello de amortiguación precisa estar diseñado de tal forma que asegure una cierta película de lubricación al sello de vástago primario y al rascador.
En general existen dos tipos diferentes de sello de amortiguación disponibles en el mercado, que fun-cionan de diferentes maneras según sus características especiales de diseño. El primero se denomina “sello de amortiguación con alta capacidad de sellado”. Se centra en reducir la película de lubricación al mínimo y, por lo tanto, evitar que el sello de vástago primario se presurice.. Por un lado, la misión de este concepto es evitar la extrusión y/o el desgaste del sello de vástago primario causados por la presu-rización pero, por otro lado, ocasiona una lubricación insuficiente del sello de vástago, que genera un aumento de la fricción y posiblemente adherencia-deslizamiento y temperaturas más elevadas en el sistema.
El segundo tipo se denomina “sello de amortiguación de fricción optimizada”. Permite que una cierta película de lubricación pase más allá del labio de sellado y asegura suficiente lubricación al sello de vástago primario. Por un lado, este concepto puede conducir a que posiblemente se produzca presión intermedia detrás del sello de amortiguación, que debe sostenerla el sello de vástago primario pero, por otro, asegura una menor fricción de todo el paquete de sellado del vástago. El resultado es una mayor vida útil y mayor eficacia energética.
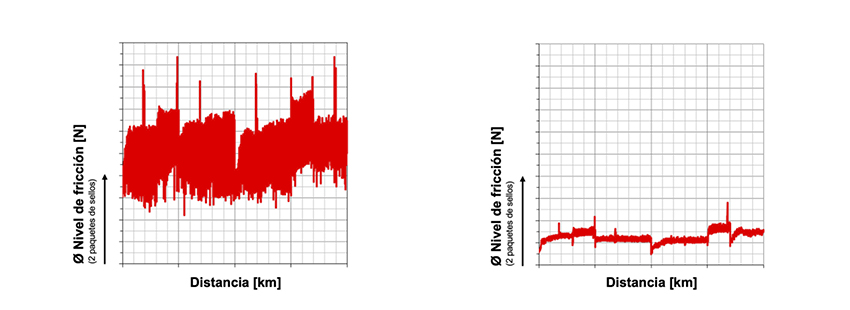
1.1 Sellos de amortiguación de fricción optimizada de SKF
SKF ha desarrollado dos nuevos sellos de amortiguación de fricción optimizada.. El HDB está optimiza-do para aplicaciones pesadas, con un anillo de respaldo de termoplástico para evitar la extrusión. El RDB está diseñado para emplearse en aplicaciones semipesadas, con material de poliuretano de gran dureza y alto rendimiento. Las pruebas de verificación se han completado con éxito en ambos tipos de sello de amortiguación. Todavía se están llevando a cabo las pruebas de validación en campo de los diferentes tamaños (que pueden prolongarse hasta un año).
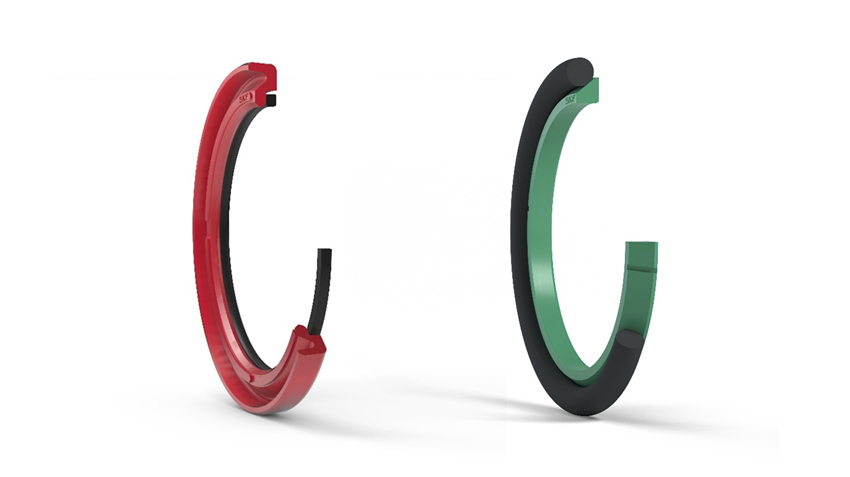
Varios factores influyen en la eficacia energética de un paquete de sello de vástago en un sistema hi-dráulico. Para llegar al objetivo de alta eficacia, la fricción creada por los sellos debe mantenerse al mí-nimo. Sin embargo, ¿qué influye en la fricción de los sellos?
Para averiguar esto, necesitamos examinar con mayor detenimiento la superficie de contacto entre el sello y la contraparte móvil. Los factores que influyen pueden explicarse enteramente por la ecuación de Reynolds. Expresa que el flujo de una película lubricante delgada entre dos superficies está influido por la velocidad, el gradiente de la distribución de la presión de contacto y la viscosidad del lubricante. Cuanto más bajo sea el nivel de espesor de la película de lubricación, mayor será la probabilidad de un aumento de la fricción. También puede encontrarse información más detallada en /3/ y /4/.
La influencia de una diferente velocidad de la carrera de vuelta y de ida del vástago del pistón se ha analizado para un sello de vástago común con copa en U. La figura 5 muestra que las fugas y el espe-sor de la película de lubricación aumentan, con una proporción más elevada entre la velocidad de la carrera de ida y de vuelta. Entonces, si la velocidad de la carrera de ida es muy superior a la de vuelta, hay mayor probabilidad de lubricación insuficiente, lo que genera un aumento de la fricción cuando la carrera de vuelta es alta.
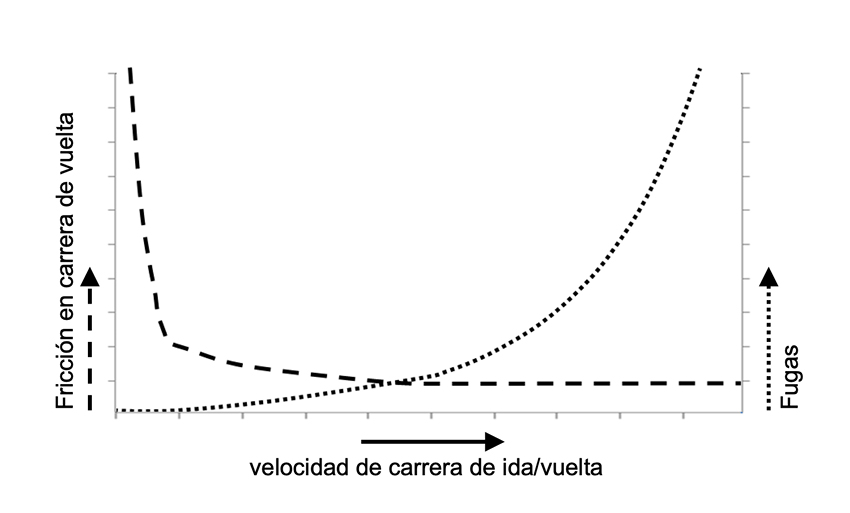
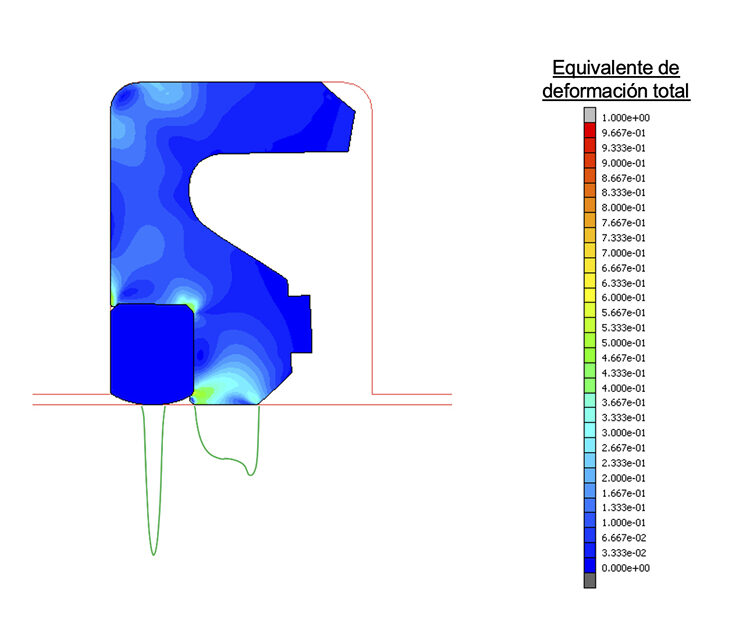

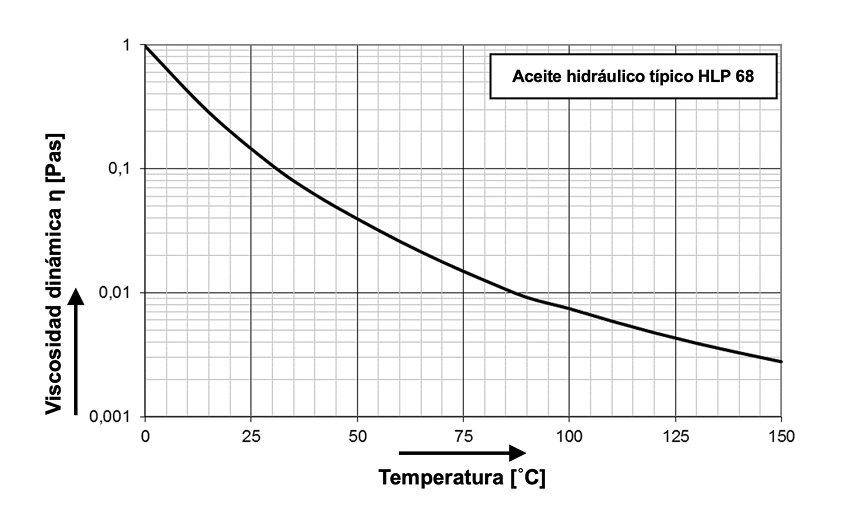
Investigación en banco de pruebas
1.3 Configuración de banco de pruebas
La figura 9 muestra una ilustración esquemática del banco de pruebas que se utilizó en la labor de in-vestigación, y una tabla con los parámetros de prueba usados. Consiste en una cámara de prueba presurizada que incluye sellos de amortiguación y de vástago primarios, así como sellos estáticos y elementos guía. El banco de pruebas también está equipado con un vástago del pistón móvil (accio-namiento eléctrico), una unidad de presurización hidráulica y un sistema de detección de la fuerza de fricción basado en un transductor de fuerza de tensión/presión.
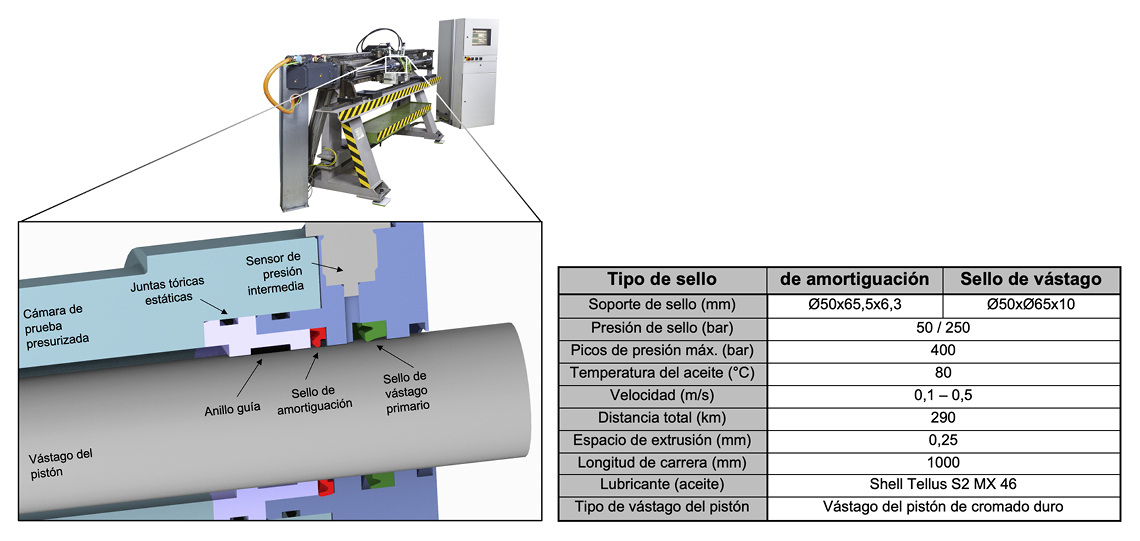
La figura 10 expone esquemáticamente la prueba de resistencia utilizada para evaluar la capacidad de truncar picos de presión y aliviar la presión intermedia a medida que el sello envejece. Al definir el ciclo de prueba, el objetivo era comprobar todas las funciones del sello de amortiguación, pero que también fuera lo más cercano posible a la aplicación real. El programa de pruebas comprende las siguientes fases de prueba:
- Fase de rodaje para establecer condiciones iniciales constantes en cada paquete, a fin de garanti-zar una comparación correcta
- Fase previa a la ejecución para evaluar características como la absorción de picos de presión o el tiempo para acumular presión intermedia
- Fase a largo plazo para evaluar características como el desgaste o la resistencia a la extrusión
- Fase de posterior a la ejecución para evaluar características como el envejecimiento de los sellos
Resultados y análisis
1.5 Sellos de amortiguación para aplicaciones pesadas (p. ej., excavadoras): el nuevo HDB de SKF
En el programa de pruebas de resistencia, se evaluó el nuevo sello de amortiguación HDB combinado con el sello de vástago primario S1S, y se comparó con el paquete de sello de vástago de referencia, compuesto de un sello de amortiguación con alta capacidad de sellado combinado con una copa en U de caucho con anillo de respaldo integrado como sello de vástago primario.
La figura 11 muestra la fuerza de fricción y el análisis visual del ciclo de pruebas previo a la ejecución y posterior a la ejecución. La diferencia entre un sello de amortiguación de “fricción optimizada” (HDB de SKF) y un sello de amortiguación con alta capacidad de sellado (referencia) pudo verse claramente al comparar los niveles de fricción. Además, el paquete de referencia muestra un aumento significativo de la fricción durante la prueba posterior a la ejecución en comparación con la prueba previa. Esto significa que el paquete de referencia se vio perjudicado durante el ciclo de prueba a largo plazo debido a pa-rámetros operativos más altos causados por el aumento de la fricción. El paquete de SKF muestra una fuerza de fricción bastante estable y baja, lo que es un indicador de un sistema de sellado que funcio-na correctamente a largo plazo.
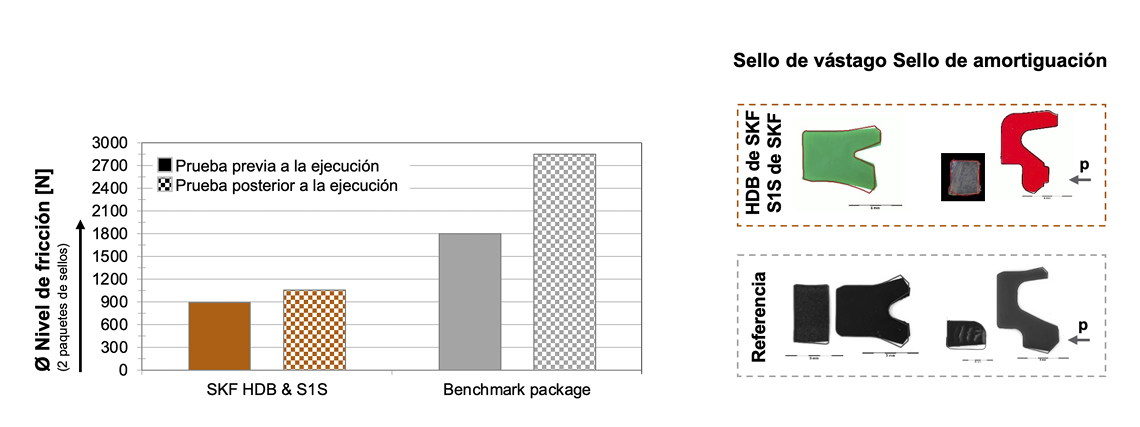
El aumento de la fricción del paquete de referencia provocó una temperatura más elevada en todo el sistema, lo que ocasionó un mayor desgaste del anillo de respaldo de termoplástico. Además de esto, el análisis visual del sello de vástago primario muestra una mayor pérdida de precarga del labio de se-llado, causada por una temperatura más alta y lubricación inadecuada.
No había presión intermedia entre el sello de amortiguación y el de vástago en el paquete de referen-cia. El paquete de SKF mostraba una presión intermedia relativamente baja, lo que es una consecuen-cia del concepto de diseño del HDB. En cualquier caso, la sección del perfil del S1S en la figura 11 indica que la presión intermedia no ha dañado el sello de vástago primario. La deformación del anillo de respaldo del HDB proporcionó una mayor capacidad de sellado a medida que el sello envejecía, lo que finalizó con una menor probabilidad de acumulación de presión intermedia y menores niveles de lubri-cación. Ninguno de los paquetes mostró fugas después de toda la prueba de resistencia.
La labor de investigación muestra que el paquete de SKF es más eficaz ya que precisa menos entrada de energía debido a una menor fricción. El resultado es una vida útil más prolongada de los sellos y el lubricante, e intervalos más prolongados entre mantenimientos.
1.6 Sellos de amortiguación para aplicaciones semipesadas (p. ej., carretillas elevadoras): el nuevo RDB de SKF
La figura 12 muestra el nivel de fricción del RDB de SKF y un sello de amortiguación de PTFE energi-zado con caucho en las pruebas previa y posterior a la ejecución, así como un análisis de sección del perfil después de toda la prueba de resistencia. Ambas unidades de amortiguación se combinaron con el mismo sello de vástago.
La amortiguación de PTFE muestra un nivel de fricción relativamente bajo. El elemento de PTFE pre-senta extrusión en ambas direcciones debido a que está sellado en las dos y no alivia la presión inter-media como se desea. Como consecuencia de esto, el sello de vástago primario también mostraba una cierta extrusión, lo que confirma que el sello de amortiguación de PTFE no era efectivo para reducir los picos de presión durante la prueba de resistencia.
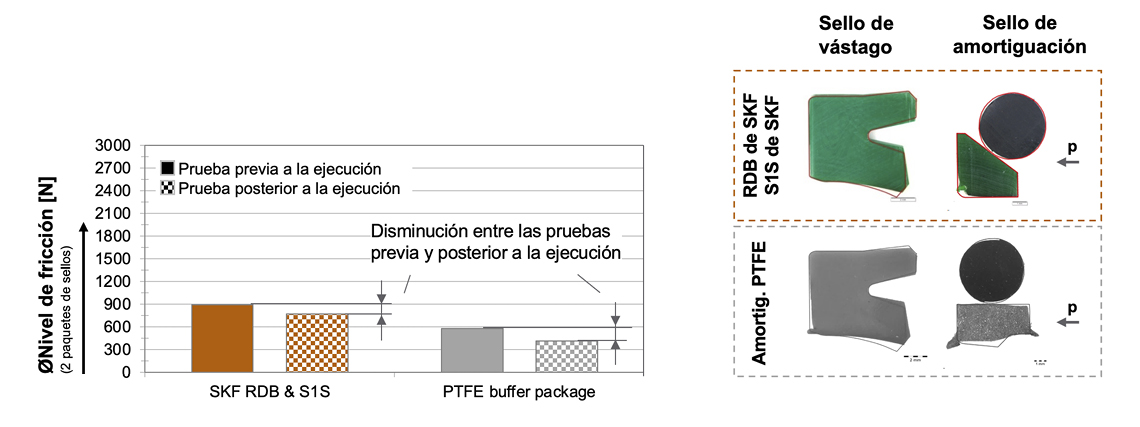
La figura 13 muestra la presión intermedia a una presión de sistema de carrera de vuelta de 50 bar en la prueba a largo plazo de ambos sellos de anillo de deslizamiento. Podía verse que la amortiguación de PTFE acumulaba inmediatamente presión intermedia a un nivel de presión de sistema múltiple, que es el resultado de la falta de capacidad de alivio. El RDB de SKF presenta una acumulación de presión intermedia desde sin presión hasta presión baja a varias etapas de presión entre 50 y 400 bar.
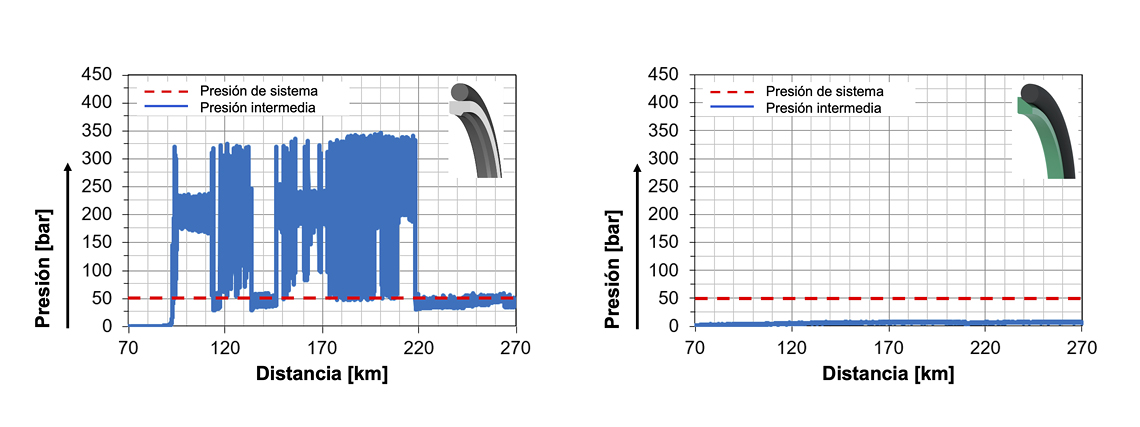
Resumen y conclusión
Este artículo presenta las funciones principales de los sellos de vástago y los diferentes principios de funcionamiento de los sellos de amortiguación. La influencia de los sellos de amortiguación y de vásta-go en la eficacia de un sistema hidráulico puede explicarse a fondo con los resultados de la labor de investigación interna realizada en bancos de pruebas.
Los resultados demuestran claramente que es muy importante seleccionar el tipo de sello de amorti-guación adecuado en relación con los parámetros operativos. Cuando puedan usarse amortiguadores del tipo de labio con anillo de respaldo de termoplástico (HDB) a presiones muy altas, los sellos de anillo de deslizamiento (RBD) energizados por juntas tóricas tienen limitaciones en la resistencia a la extru-sión; especialmente los materiales de PTFE de baja calidad pueden conducir a una extrusión inacepta-ble. En consecuencia, estos tipos de sello solo deberían emplearse en aplicaciones semipesadas.
No obstante no solo es importante la selección adecuada del tipo de sello de amortiguación. El sello de vástago primario y el rascador tienen que ajustarse, según el tipo de sello de amortiguación selecciona-do. Consulten más folletos y artículos de SKF para obtener más información sobre la selección de los paquetes de sello de vástago.
1.1 Características y beneficios de los sellos de amortiguación HDB
El sello de amortiguación HDB se adapta a las ranuras de sello de amortiguación estándares (ISO y JIS) y garantiza la fricción mínima posible para asegurar una larga vida útil del sello. La figura 14 mues-tra los beneficios y las características del producto.
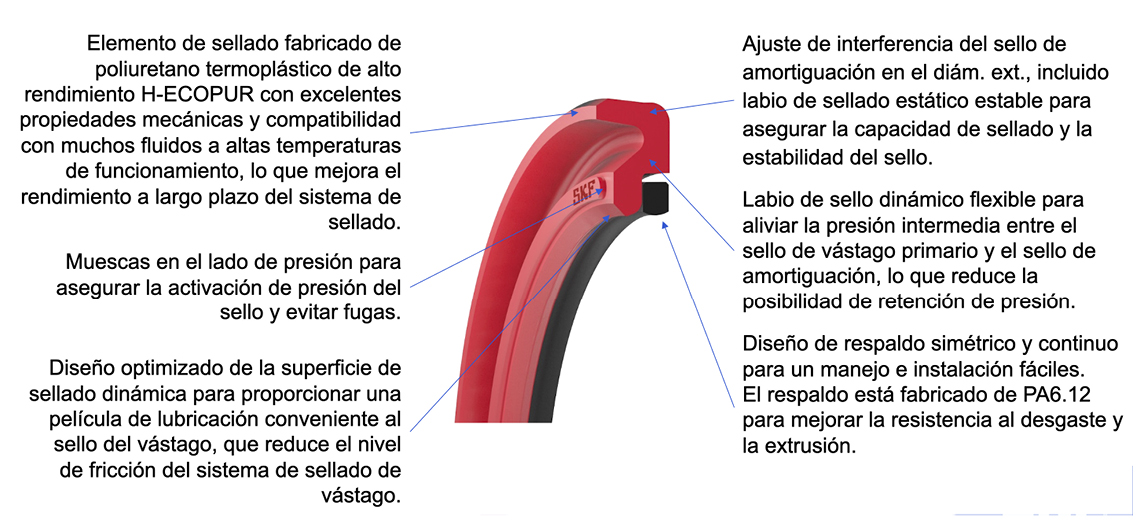
El sello de amortiguación RDB se adapta a las ranuras de sello de amortiguación estándares (ISO y JIS) y proporciona un rendimiento extraordinario a un menor costo que otros sellos de amortiguación comúnmente usados en aplicaciones semipesadas. La figura 15 muestra los beneficios y las caracterís-ticas del producto.
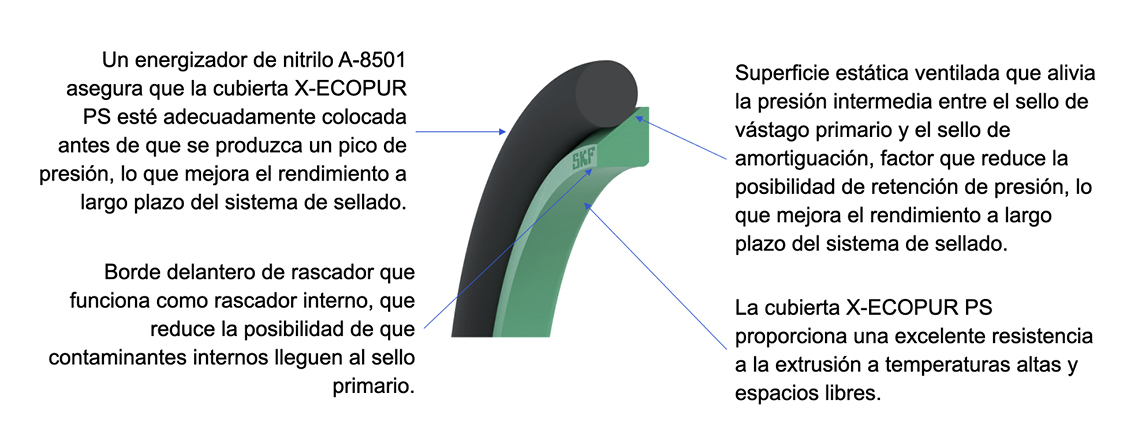
2 Referencias
/1/ SKF Industrial Seals, Hydraulic seals catalogue, 2014-06-18, page 15
/2/ M.Sc. Pat.-Ing Mario Stoll, Reibkraft S1S Prüfprogramm, Institut für Ma-schinenelemente, Universität Stuttgart, März 2017
/3/ Müller, H.K., Nau, B.S.: Fachwissen-Dichtungstechnik, http://www.fachwissen-dichtungstechnik.de
/4/ Dipl.-Ing. Ulrich Nißler, Prof. Dr.-Ing. habil. Werner Haas, Simulation und Versuch bei Hydraulikdichtungen, 14th ISC Tagungsband, S. 497-511