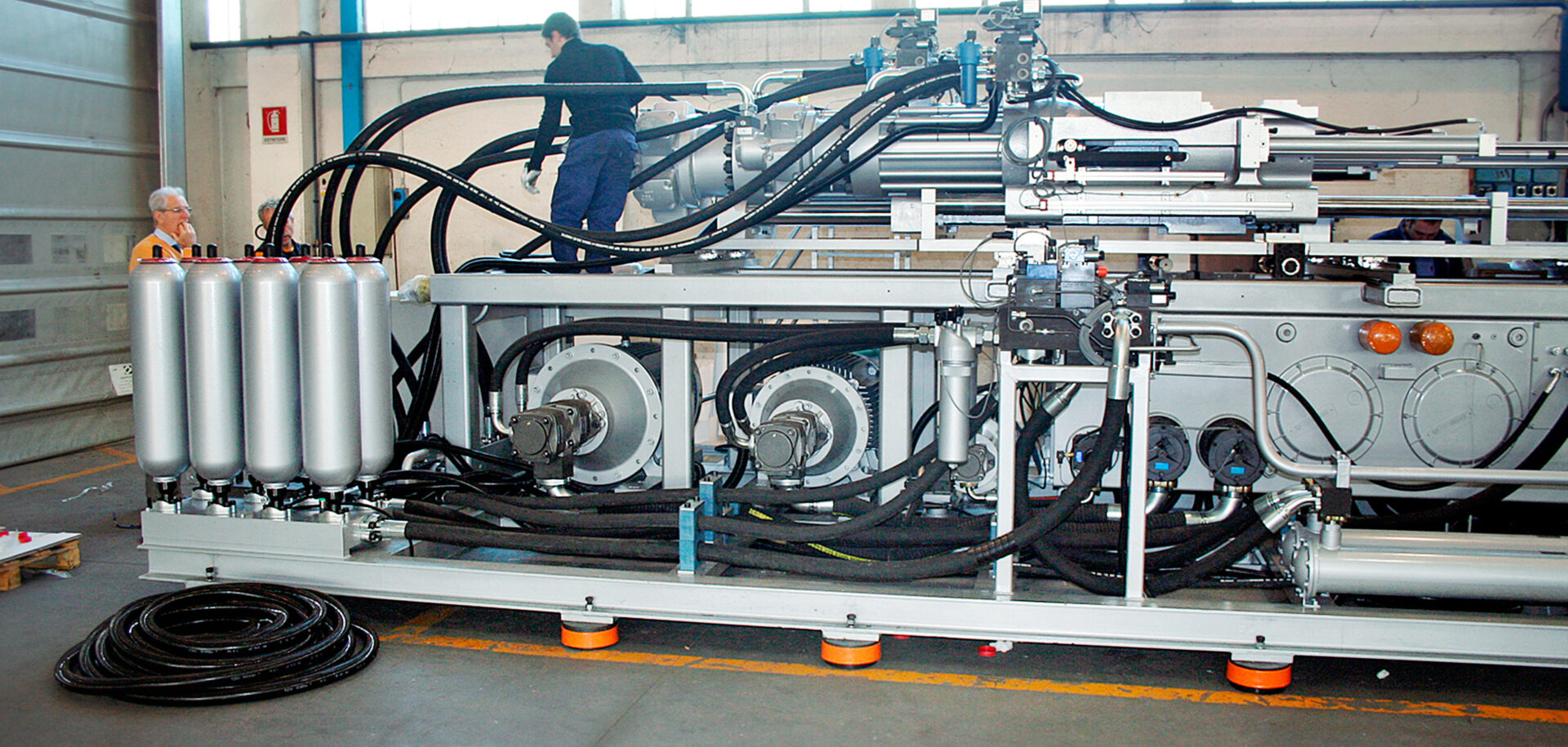
Plásticos electrizantes
Un negocio familiar italiano moldea el futuro de la tecnología de inyección de plásticos.
Datos
BMB SPA
- Constitución: 1967 en Brescia, Italia.
- Dirección: Egidio Bugatti, presidente; Marco Bugatti, director general.
- Ubicación: sede en Brescia, Italia; oficinas comerciales en 30 países.
- No cotiza en Bolsa.
- Línea de productos: máquinas de moldeo por inyección (híbridas, eléctricas e hidráulicas).
- Volumen de ventas: 70 millones de euros en 2011.
- Número de empleados: 180 en todo el mundo.
Enlaces relacionados
Contacto de venta
Giuseppe Saroglia, giuseppe.saroglia@skf.com
En 1967, la película El Graduado hizo famoso un término capaz de describir el futuro por sí mismo: el “plástico”. Ese mismo año, en una ciudad próxima a Milán llamada Brescia, tres italianos que confiaban en el futuro de los plásticos fundaron una empresa. Egidio Bugatti, su hermano Domenico y su cuñado Giuseppe Moreschi dieron a la compañía el nombre de BMB y empezaron a fabricar maquinaria para el moldeo de plásticos.
Egidio Bugatti ya tenía más de una década de experiencia en máquinas de moldeo de plásticos por inyección y en diseño de geometrías de movimiento oscilante. Él y sus socios estaban convencidos de que el “plástico” era un sector en crecimiento, y de que ellos, desarrollando máquinas más eficientes, precisas y fiables que sus competidores, crecerían con él.
“Teníamos que ser mejores que ellos”, dice Bugatti recordando aquella competencia feroz. Con esta misión, la joven empresa recibió pedidos de algunas compañías de primera línea como Olivetti, Bic y Coster, cuyos productos exigían velocidad, precisión y un control de calidad incorporado. “Contribuyeron a nuestro crecimiento y nos ayudaron a posicionarnos en lo más alto de nuestro mercado”, dice Bugatti.
BMB siguió creciendo durante la década de los 70 con una filosofía centrada en tres pilares: producto de calidad, maquinaria precisa y honradez en el trato con el cliente. La empresa solicitó su primera patente en 1980, convirtiéndose en el primer fabricante de maquinaria de moldeo que integraba la electrónica en sus productos.
En 1980 la empresa se trasladó a su sede actual, más espaciosa y ubicada en la principal zona industrial a las afueras de Brescia. Con el tiempo, las instalaciones fueron ampliándose, y hoy consisten en tres edificios contiguos que albergan la administración, el departamento técnico, y tres zonas de producción (para máquinas de hasta 400 toneladas, 450-3.500 toneladas y más de 3.500 toneladas, respectivamente). Estas instalaciones, con una superficie total de 30.000 metros cuadrados, son de última generación y gozan de un mantenimiento impecable.
A lo largo de los años 80, BMB siguió creciendo y produciendo máquinas tradicionales de moldeo por inyección de alto rendimiento y gran fiabilidad. Sin embargo, y a pesar de que la empresa vendía algunas máquinas en el extranjero, su mercado y su fama raras veces traspasaban las fronteras italianas.
Todo esto empezó a cambiar en los años 90. Marco, hijo de Bugatti, se incorporó a la empresa en 1994 después de licenciarse en la Universidad Politécnica de Milán y tras haber pasado una temporada trabajando para BMB en el Reino Unido. Quería remodelar la estructura comercial de la empresa y abogaba por poner un mayor énfasis en los mercados extranjeros. Hoy, el 85% de las ventas de BMB se realizan fuera de Italia, con una fuerte demanda desde América Latina y un foco reciente en Norteamérica.
También se ha revolucionado la línea de productos. Hasta hace tan solo 8 años, todas las máquinas de moldeo por inyección de BMB eran hidráulicas. Hoy, solo el 20% lo son. Las máquinas totalmente eléctricas, desarrolladas por primera vez por BMB en 2005, representan el 35-40% de la producción anual, y las máquinas híbridas, introducidas en 2007, suponen el 40-45%.
Las máquinas de moldeo eléctricas se utilizan en Japón desde 1983. Pero, a pesar de sus ventajas (menor consumo energético y menor impacto medioambiental, menores costes durante su vida útil, mayor precisión y dimensiones relativamente compactas), son más caras y los clientes fuera de Japón se resistían a probarlas. Todo eso cambió cuando se disparó el coste de la energía. Una máquina eléctrica puede costar un 30-40% más a la hora de comprarla, pero ahorra un 40% en costes totales de ciclo vital, además de ofrecer otras ventajas importantes.
BMB construyó su primer prototipo eléctrico en 2002. Luego, sus clientes pidieron máquinas más grandes y capaces de operar a mayores velocidades para productos de paredes delgadas y difíciles de manejar, y desarrolló máquinas híbridas. Por ejemplo, la máquina híbrida eKW70PI/7000 de BMB, introducida en 2008, produce botes de yogur en un molde de 16+16 cavidades. Utiliza tecnología de transmisión eléctrica para todas las funciones, excepto la inyección propiamente dicha del plástico, que es accionada por un sistema de acumuladores hidráulicos para lograr las velocidades de llenado requeridas.
Tanto Egidio como Marco Bugatti están convencidos de que en el futuro todas las máquinas serán eléctricas. “Aún queda mucho margen de crecimiento en el sector del moldeo de plásticos –dice Egidio Bugatti– y nuestra intención es liderar su evolución”.
Gigante electromecánico
Cuando BMB comenzó a centrarse en las máquinas eléctricas en 2004, recurrió a SKF. “Sabíamos que SKF era un experto en husillos de rodillos y máquinas de moldeo eléctricas”, explica Egidio Bugatti, presidente de BMB. “Queríamos que nos ayudara a desarrollar una máquina eléctrica capaz de realizar un ciclo de cuatro segundos a velocidades altas”.
La gama de husillos de rodillos planetarios de SKF, con capacidad de carga muy elevada, fue creada específicamente para cumplir estas exigencias. Un ejemplo es la nueva máquina híbrida de moldeo por inyección de 1.700 toneladas. Su movimiento oscilante es el mayor realizado con tecnología electromecánica, exigiendo presiones elevadas que comportan un alto riesgo de desalineación. Los husillos de rodillos planetarios de SKF han sido diseñados específicamente para evitar estos problemas y el tiempo improductivo resultante. “Además –señala Giuseppe Saroglia, Business Manager de SKF Mechatronic, reducen sustancialmente la cantidad de aceite hidráulico necesario y, con ello, la demanda de refrigeración”.