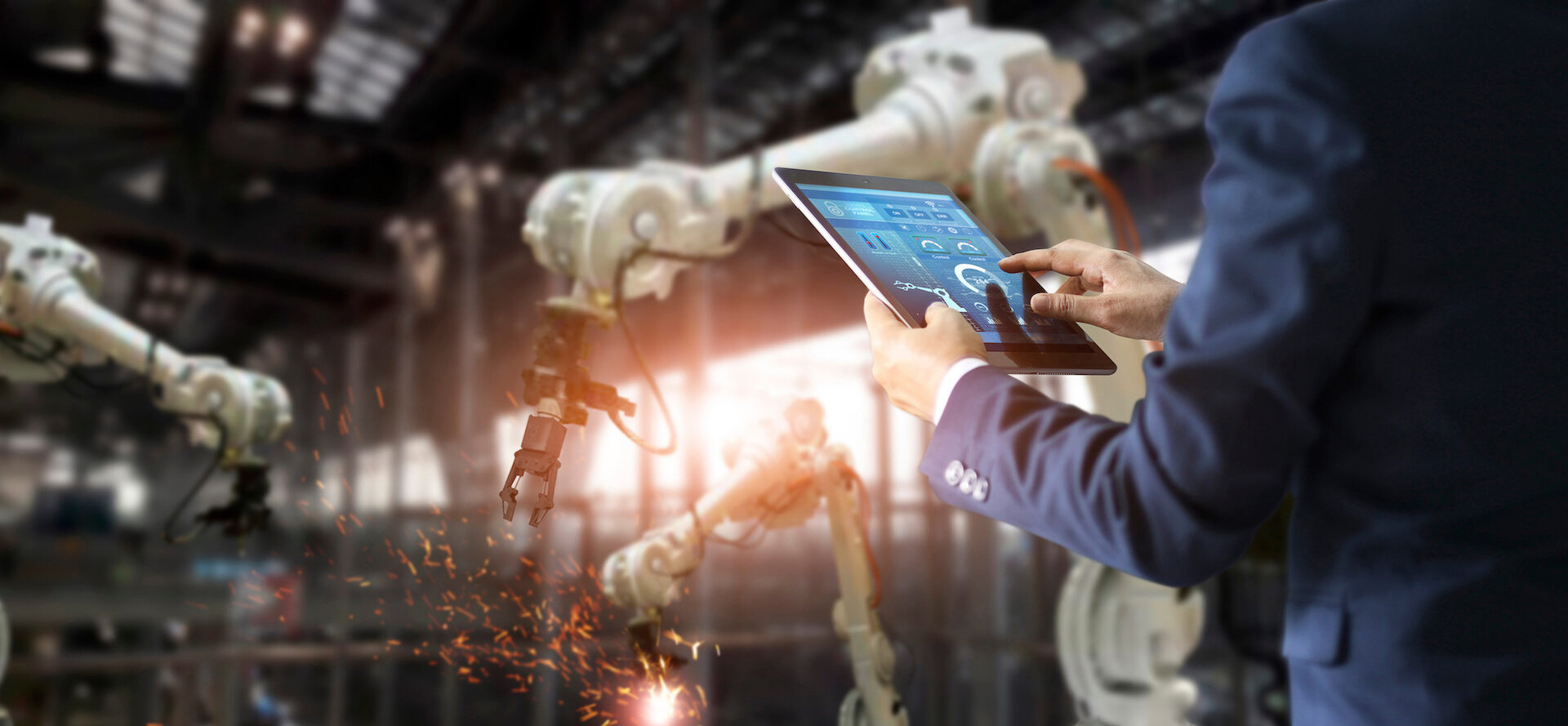
Forging asset efficiency
Due to the economic slowdown in China and the consequent fall in steel demand, the country’s steel industry is seeking new ways to reduce production costs. Evolution pays Rizhao Steel a visit.
According to the World Steel Association, about 50 percent of global steel production is used in the housing and construction sector, making it the biggest consumer of steel today. China is the largest producer and consumer of steel in the world. But 2012 was a tough year for the Chinese steel industry, which saw its profits plummet by nearly 96 percent in the first half of the year compared with the same period the previous year. Chinese steel company Rizhao Steel, on the east coast of China, knows that in times of waning demand there is money to be saved by increasing efficiency in its plants. As early as 2007, Rizhao began asset efficiency work by partnering with SKF through an SKF Integrated Maintenance Solution, or IMS contract, for its most critical mill, the H-beam rolling mill. Liang Dong, manager Asset Management Services at SKF China, explains: “By the first assessment, we saw that Rizhao was quite strong in execution but lacking in overall planning, especially strategy. Phase one of a project is the most difficult part because the customer does not yet have the trust and is sceptical that you will be able to deliver the significant results that you present.” SKF tied the project to key performance indicators (KPIs) related to Rizhao’s own business strategies. “This is the first project in the metals industry where we based a project on KPIs,” says Dong. “Through KPIs we can persuade the customer that there is no risk in signing a contract with us. From the beginning to the end of the project we drive it, measure it, control it and then bring the results.” Wei Li-hua, assistant president in charge of asset management at Rizhao, comments: “The SKF IMS project is a pilot for our company, and it requires both sides to work closely to explore a new management mindset and concepts in order to achieve the optimal results and benefits for our company’s business.” The four-year contract included a Computerized Maintenance Management System (CMMS), the installation of 450 permanent sensors, root cause failure analysis (RCFA) process and training, machine reliability improvement support and more. Rizhao got a large return on its investment. Unplanned downtime went from 911 minutes per month in 2007 to 77 minutes per month in 2011. Spare parts cost per tonne of product was reduced by 48 percent. “The reason we can achieve such marvellous results is that we work and innovate together with the customer,” says Dong. “Without the customer’s contribution, of course, we cannot achieve this.” Rizhao has renewed the contract for another two years and is replicating the H-beam rolling mill success to other areas of the plant. For example, SKF is now working on original machine designs with Rizhao and helping to transfer the knowledge gained from the IMS project into setting up a brand new production line. Dong sees the achievements of the project as just the beginning. “We gradually replicate this success to other customers and other segments, such as power generation,” he says. “So we have several successful cases resulting from this replication.”