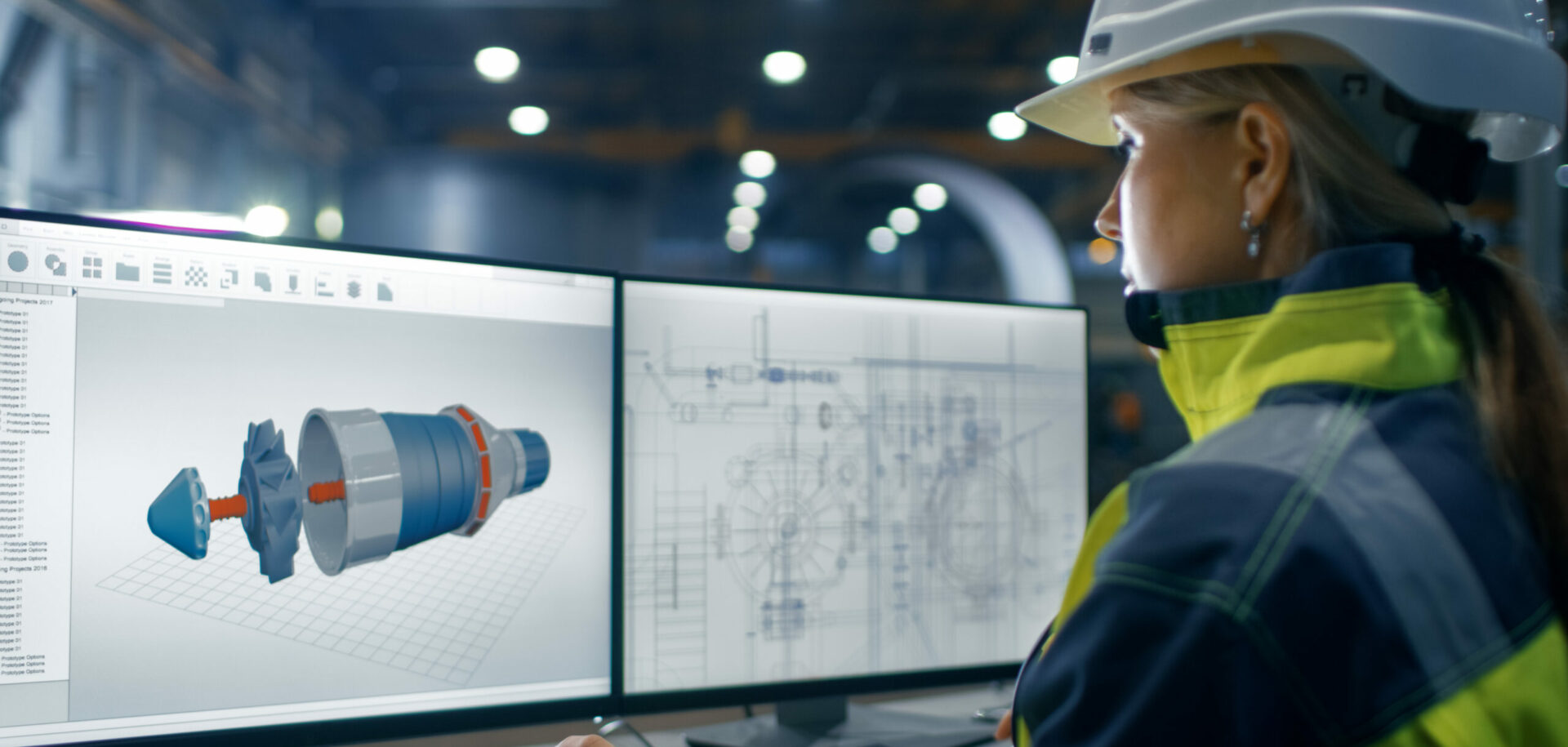
Des opportunités qui pèsent dans la balance
Éviter une défaillance de roulement ou sa réapparition peut très bien rapporter plus que le pesant d’or du roulement.
Éviter une défaillance de roulement ou sa réapparition peut très bien rapporter plus que le pesant d’or du roulement.
Technologie
Chaque année, plus de dix milliards de roulements sont produits dans le monde. Ils survivent pour la plupart (environ 90 %) à l’équipement dans lequel ils sont installés. Certains sont remplacés avant toute défaillance (9,5 %). En revanche, leurs défaillances (0,5 %) peuvent avoir des conséquences désastreuses. En cas de défaillance d’un roulement sur une ligne de production majeure d’une grosse usine ou dans une application critique, les pertes de production peuvent se chiffrer en millions d’euros. La cause sous-jacente est parfois très simple.
Prenez, par exemple, le cas du déraillement d’un train de marchandises il y a quelques années. Un roulement dans une boîte d’essieu est entré en surchauffe (Fig. 1), l’essieu s’est rompu et huit wagons sont devenus incontrôlables. La cause du problème fut difficile à déterminer car presque tout avait été détruit. Il est finalement apparu qu’une simple entretoise, montée lors d’une révision, présentait une largeur insuffisante. Les roulements pouvaient se déplacer librement sur l’essieu, ce qui avait entraîné la surchauffe et la rupture de l’arbre (et des roulements).
Analyse des causes de défaillance
On trouve des roulements dans la plupart des machines et véhicules. Lorsque le roulement ne remplit plus sa fonction, la machine ou le véhicule s’arrête. La présence dans l’équipement d’un élément perturbateur nuit au bon fonctionnement du roulement. Il s’agit alors d’identifier la cause racine pour empêcher la réapparition de l’anomalie car le seul remplacement du roulement ne pourra résoudre le problème.
Après une certaine durée de service, des changements apparaissent dans l’aspect de la plupart des roulements. Ces changements sont une mine d’informations sur les conditions de service et les événements intervenus au cours de la durée de vie du roulement.
Pour permettre une inspection satisfaisante d’un roulement endommagé, l’équipement doit être arrêté à temps car l’état du roulement en question continue de se dégrader. Il finit par devenir inutilisable, et toutes les preuves des mécanismes de défaillance sont détruites (Fig. 2).
Des corps étrangers (particules) ont pénétré à l’intérieur du roulement où ils ont été broyés. Des empreintes se sont ainsi formées (particules écrasées contre les pistes) avec des bords surélevés faisant penser à des cratères. La géométrie de la piste a été localement modifiée et, dans la zone concernée, les conditions de formation d’un film d’huile adéquat pour séparer les surfaces de contact ont disparu. Il s’en est suivi une fatigue du matériau, initiée en surface, avec apparition de fissures, puis d’un écaillage de la zone endommagée (Fig. 2a). L’équipement ayant continué de fonctionner, l’écaillage s’est étendu (Fig. 2b et 2c). La zone endommagée est devenue si vaste que le point de départ, autrement dit l’empreinte, a disparu (Fig. 2d). À ce stade, l’inspection du roulement endommagé ne permet plus d’identifier, comme cause de la défaillance, la pénétration de particules à l’intérieur du roulement due à de probables problèmes d’étanchéité.
Aujourd’hui, ondispose des éléments de compréhension suivants :
-
les causes d’une défaillance présentent certaines caractéristiques ;
-
un mécanisme de défaillance donné se traduit par un mode de défaillance spécifique ;
-
il est possible de déterminer la cause de la défaillance à partir des dommages observés.
L’ISO a accompli un travail important pour définir les différents modes de défaillance de roulements selon différentes catégories (Fig. 3). Ces travaux ont donné lieu à la norme ISO 15243, publiée en 2004. Six grands modes de défaillance peuvent être observés et classés selon un certain nombre de sous-catégories.
La classification est basée sur trois facteurs principaux :
-
les dommages et modifications survenus pendant la durée de service (à partir du moment où le roulement a quitté l’usine) ;
-
les formes caractéristiques des changements d’aspect pouvant être attribuées à des causes spécifiques ;
-
la classification selon des caractéristiques visibles (y compris avec des outils de grossissement comme les microscopes).
Intéressons-nous aux différents modes :
La fatigue du matériau
La fatigue initiée en sous-couche est une détérioration du matériau. Elle est due à des contraintes cycliques qui s’exercent sous la surface des pistes et finissent par entraîner une détérioration du matériau. Les fissures se forment et se propagent sous la surface. Lorsqu’elles atteignent la surface, c’est l’écaillage (Fig. 4).
La fatigue de surface est due à de mauvaises conditions de lubrification. Le rôle du lubrifiant est de former une pellicule d’huile pour séparer les éléments en mouvement. Si les conditions de lubrification sont mauvaises, par exemple en raison d’une contamination ou d’une viscosité inappropriée, un contact métal sur métal se produit. Au contact les unes des autres, les aspérités de surface (pics) génèrent des contraintes de cisaillement en surface. Compte tenu de la fatigue du matériau, des petites fissures, puis un micro-écaillage apparaissent. Au début, la surface peut prendre un aspect brillant car sa rugosité est gommée, mais le processus se poursuit et la surface devient mate et de plus en plus cassante (Fig. 5).
L’usure
L’usure est unaspect typique que prennent des éléments en mouvement au niveau de leurs zones de contact. Toutefois, il arrive qu’elle apparaisse à un stade précoce de la période de service du roulement.
Elle se décline en deux variantes : l’usure abrasive et l’usure adhésive. Elles apparaissent du fait des variations de vitesse entre les surfaces en contact. Ces variations de vitesse peuvent elles-mêmes provenir d’un glissement cinématique, d’une accélération et/ou d’une décélération.
L’usure abrasive est due à des particules abrasives présentes dans le lubrifiant. Il peut s’agir d’impuretés provenant de l’extérieur ou de l’intérieur : par exemple, des particules d’usure d’engrenages. Les particules abrasives entraînent une usure de la surface des pistes (Fig. 6) et des éléments roulants. Cela se traduit d’ordinaire par des surfaces mates. Toutefois, si les particules abrasives sont très fines et dures, comme la poussière de ciment, elles ont plutôt un effet de polissage des surfaces qui se traduit par un aspect poli miroir. Des dispositifs d’étanchéité souvent inadaptés, voire absents, laissent les impuretés pénétrer dans la cavité du roulement. Une analyse du lubrifiant peut révéler l’origine des impuretés.
L’usure adhésive est généralement le lot des surfaces de contact soumises à de faibles charges, de mauvaises conditions de lubrification et des variations de vitesse importantes dues au glissement des éléments roulants. Prenons l’exemple du passage d’un élément roulant de la zone non chargée à la zone chargée (Fig. 7). L’élément roulant peut perdre de la vitesse dans la zone non chargée et accélérer lors du retour dans la zone chargée. Cela peut entraîner une rupture du film lubrifiant, un glissement, un échauffement et un transfert de matière de l’élément roulant à la piste ou inversement. À un stade précoce, les surfaces sont brillantes, mais rapidement, elles deviennent mates avec, dans une mesure plus ou moins grande, des zones de grippage.
La corrosion
La corrosion due à l’humidité peut causer de sérieux dommages aux roulements. Elle se développe rapidement et peut pénétrer profondément dans le matériau. Elle apparaît en présence d’eau, de liquides corrosifs ou d’humidité. Une forte humidité de l’air et une manipulation des pistes avec les doigts peuvent également conduire à ce type de corrosion. Celle-ci apparaît souvent à l’arrêt et se traduit visuellement par des marques de corrosion à distance des éléments roulants (Fig. 8). Bien installée, elle conduit à un endommagement prématuré du roulement.
La rouille de contact peut avoir des conséquences très sévères. Elle est due à des micro-mouvements entre deux surfaces chargées. La plupart du temps, elle apparaît entre le diamètre extérieur du roulement et le logement et/ou entre l’alésage du roulement et l’arbre. Les micro-mouvements sont causés principalement par les charges cycliques exercées au passage des éléments roulants. Des ajustements inappropriés, une flexion de l’arbre et/ou des imperfections sur les surfaces de contact peuvent être à l’origine du phénomène ou accélérer son apparition. De l’air peut pénétrer dans les surfaces non protégées et accélérer sa progression. L’oxyde de fer ainsi formé présente un volume supérieur à celui de l’acier pur. Une expansion du matériau et des contraintes élevées sont alors possibles, y compris au niveau des pistes de roulement, et susceptibles d’entraîner une fatigue interne prématurée. La rouille de contact peut facilement conduire à une fissuration des bagues (Fig. 9).
Le faux effet Brinell, autre forme de corrosion de contact, se produit dans les zones de contact entre éléments roulants et pistes en raison de micro-mouvements et de la résilience du contact élastique sous des vibrations cycliques. Comme cela se produit lorsque le roulement est à l’arrêt et chargé, les dommages apparaissent entre les éléments roulants. Selon l’intensité des vibrations, les conditions de lubrification et la charge, une corrosion mêlée à de l’usure apparaît, entraînant la formation de creux superficiels dans les pistes. En général, les vibrations se traduisent par une pénurie locale de lubrifiant, un contact métal contre métal et une usure abrasive. La surface prend alors un aspect mat, avec bien souvent une décoloration, voire parfois une coloration rouge sous l’effet d’une corrosion simultanée due à l’humidité. Elle peut être brillante dans les creux, la raison la plus probable étant la présence d’un reste de lubrifiant offrant une protection contre l’usure abrasive. Le faux effet Brinell se traduit par des cavités sphériques sur les roulements à billes (Fig. 10) et des stries sur les roulements à rouleaux.
L’érosion électrique
Tout courant qui traverse un roulement est potentiellement néfaste.
Des dommages dus à un survoltage peuvent se produire lorsqu’un courant électrique traverse un roulement, autrement dit passe d’une bague à l’autre via les éléments roulants. Au niveau des surfaces de contact, le processus est similaire à celui exploité pour le soudage à l’arc électrique (densité de courant élevée sur une petite surface de contact). La température du matériau s’élève à des niveaux compris entre le niveau de trempe et le niveau de fusion. Apparaissent alors des zones décolorées, de dimensions variables, dans lesquelles le matériau a été trempé, re-durci ou a fondu. Des cratères (d’environ 0,1 à 0,5 mm) se forment aux endroits où le matériau a fondu (Fig. 11).
Les dommages liés à un passage du courant proviennent de courants électriques vagabonds qui traversent un roulement, souvent sous l’effet de variations de fréquence. Les principales marques visibles sont des cannelures (Fig. 12). Celles-ci se présentent sous forme d’ellipse de contact sur les roulements à billes et de lignes de contact sur les roulements à rouleaux. Les éléments roulants présentent la plupart du temps une décoloration uniforme. Par rapport aux dommages dus à une tension excessive, le courant parcourt dans ce cas une zone plus grande, l’intensité du courant est donc plus faible, de même que la température. Par conséquent, le principal dommage visible est un effet de trempe, autrement dit un ramollissement de l’acier. Toutefois, l’observation de la détérioration avec un grossissement supérieur révèle la plupart du temps la présence également de cratères à l’échelle microscopique.
La déformation plastique
Une déformation permanente se produit chaque fois que la limite d’élasticité du matériau est dépassée.
Une surcharge provient de charges tactiques ou charges par choc et entraîne une déformation plastique. Elle est reconnaissable aux creux formés à distance des éléments roulants. Des procédures de montage incorrectes sont souvent à l’origine du problème : par ex., la force de montage est appliquée sur la mauvaise bague, ce qui entraîne une charge par choc exercée sur les éléments roulants (Fig. 13).
Les empreintes de particules sont dues à des corps étrangers (impuretés) qui ont pénétré à l’intérieur du roulement et sont écrasés contre les pistes au passage des éléments roulants. La taille et la forme des empreintes dépendent de la nature des particules. La géométrie de la piste au niveau de l’empreinte est altérée, ainsi que la lubrification. Des contraintes sont générées à la surface et la fatigue conduit à un écaillage prématuré de celle-ci (Fig. 14).
La présenced’empreintes de manutention est due à l’utilisation d’objets durs, pointus qui ont endommagé les surfaces du roulement. C’est la raison pour laquelle les roulements doivent toujours être manipulés avec soin. Même si le roulement est fabriqué dans un acier de la plus grande qualité, des surcharges localisées, par exemple en cas de chute d’un roulement, peuvent endommager ses surfaces et le rendre inutilisable.
Fracture et fissuration
Une fracture (ou fissuration) se produit lorsque la limite de résistance à la traction du matériau est dépassée.
Une rupture forcée est causée par une concentration de contraintes qui dépasse la résistance à la traction du matériau en cas de surcharge locale ou de contrainte excessive.
Les deux causes courantes sont :
-
une manœuvre brutale (impact) lors du montage ou du démontage du roulement. Des coups de marteaux appliqués sur un burin durci directement en contact avec la bague peuvent entraîner des fissures minces conduisant au détachement de morceaux de la bague lors de la mise en service du roulement ;
-
enfoncement excessif sur une portée conique ou un manchon. Les contraintes de traction (contraintes circonférentielles) ainsi générées au niveau des bagues entraînent une fissuration au moment de la mise en service du roulement (Fig. 15).
La rupture de fatigue apparaît en cas de flexion induisant un dépassement de la résistance à la fatigue. Une fissure apparaît avant de se propager et l’ensemble de la bague ou de la cage se fissure. Une rupture de fatigue peut se produire lorsqu’un ajustement serré est utilisé, conduisant à des contraintes circonférentielles élevées. Les contraintes hertziennes et circonférentielles combinées peuvent alors générer une fatigue prématurée menant à la fissuration de la bague.
Des craquelures dues aux effets thermiques se produisent lorsque deux surfaces glissent lourdement l’une contre l’autre. L’échauffement par frottement ainsi généré entraîne des fissures, généralement dans le sens perpendiculaire au sens de glissement (Fig. 16).
Conclusion
Un pourcentage important des défaillances de roulements pourrait être évité. Une analyse approfondie des dommages peut permettre d’en identifier la cause et de prendre les mesures appropriées pour éviter que le problème se reproduise.
Astuces de maintenance
En appliquant quelques règles élémentaires de maintenance, il est souvent possible d’allonger la durée de service du roulement.
-
Respectez les spécifications : un roulement est conçu pour supporter une certaine charge, tourner à une certaine vitesse, etc..
-
Éviter de soumettre un roulement à une charge excessive (ou trop faible) ou une vitesse trop élevée. Il existe une large gamme de roulements. Il est important de sélectionner le roulement adapté à l’application. Veillez à appliquer les tolérances et ajustements appropriés.
-
Le cas échant, assurez-vous que l’alignement est compris dans les limites appropriées.
-
Propreté : un environnement propre lors du montage constitue un bon départ pour une longue durée de service des roulements.
-
Outils : utilisez toujours les outils adaptés lors du montage ou du démontage. Des outils inadaptés risquent d’endommager le roulement.
-
Étanchéité : veillez à choisir une solution d’étanchéité adaptée et vérifiez son efficacité.
- Lubrification : une lubrification efficace est essentielle. Une lubrification insuffisante, excessive ou inadaptée peut conduire à une détérioration prématurée du roulement. Assurez-vous d’appliquer le bon lubrifiant, au bon moment et en bonne quantité.