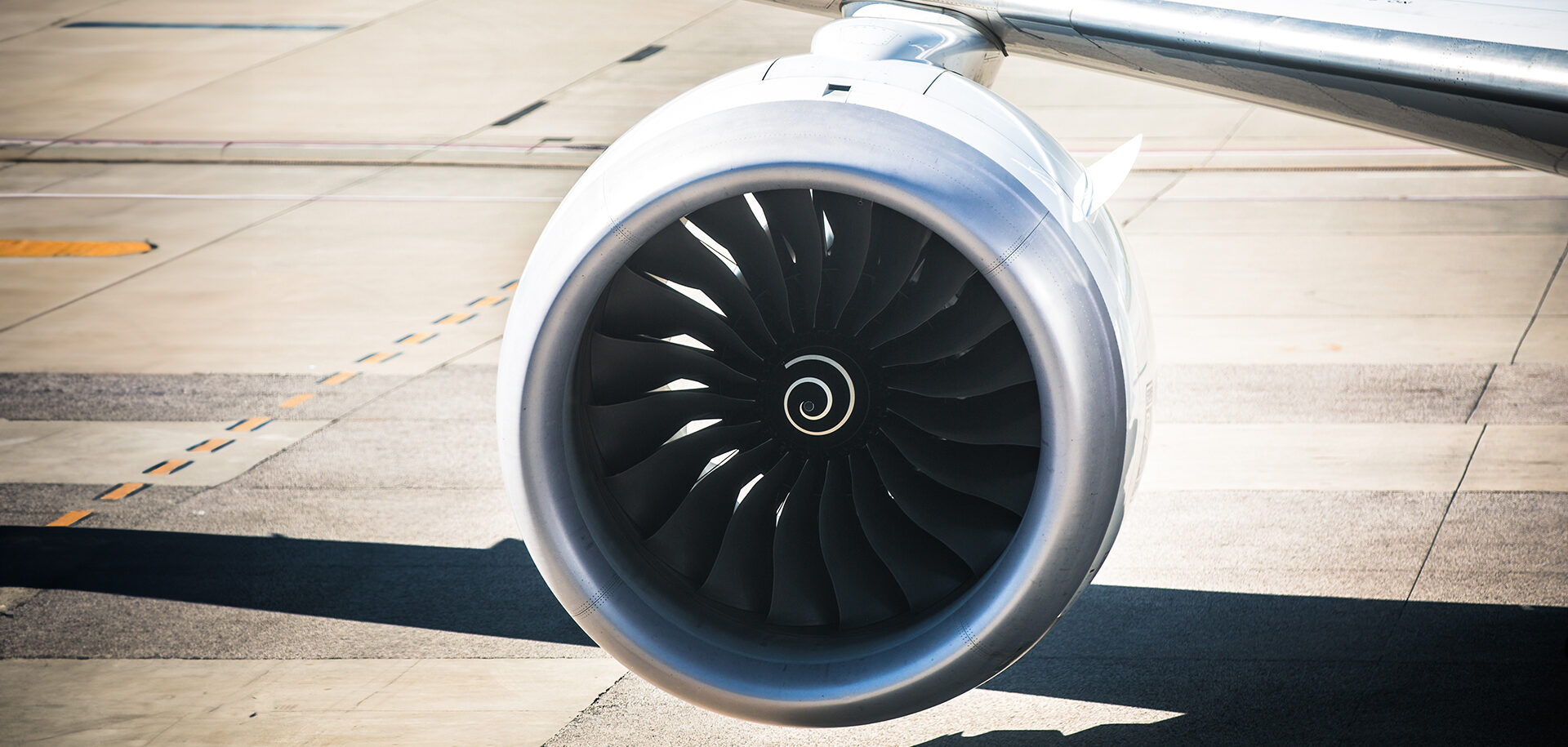
L’innovation collaborative pour assurer l’avenir de l’aviation
Le Centre d’Excellence Aéronautique de SKF élabore en étroite collaboration avec ses clients les technologies de pointe à destination des avions de demain.
L’industrie aéronautique mondiale vient de traverser quelques années de turbulences. Tout d’abord, elle a vu la demande s’effondrer en raison des confinements et des restrictions de voyage liées à la pandémie de Covid-19. Puis, quand tout commencé à revenir à la normale, elle a connu une forte reprise, le nombre de passagers bondissant de 47 % pour la seule année 2022 [par rapport à 2021].
L’Organisation de l’aviation civile internationale s’attend à ce que la demande de transport de passagers dépasse en 2023 les niveaux pré-pandémie, et les avionneurs font état de chaînes de production chargées et de carnets de commandes bien remplis.
Même si tout cela est une excellente nouvelle pour le secteur aéronautique, celui-ci est toujours confronté à d’importants enjeux à long terme, l’un d’eux étant les objectifs de durabilité fixés par les autorités régulatrices dans le monde. Toutefois, à la différence de nombreux secteurs industriels, les solutions technologiques indispensables pour que le transport aérien de masse ne produise plus d’émissions n’existent pas encore.
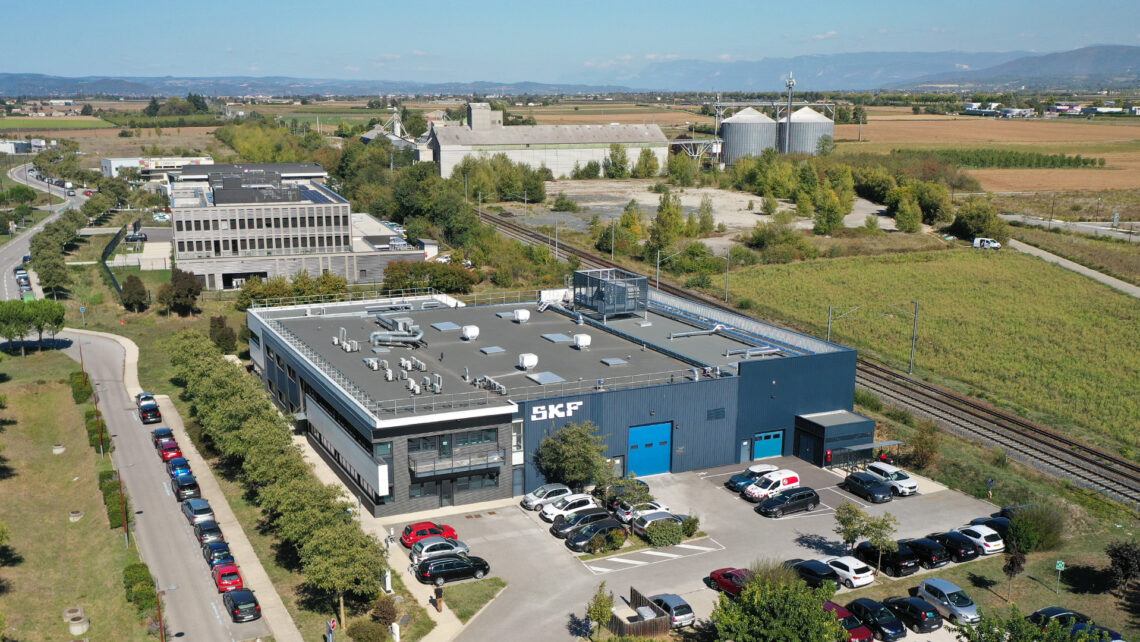
SKF joue un rôle clé de partenaire
SKF contribue au développement des technologies aéronautiques nouvelle génération via son Centre d’Excellence Aéronautique, un site récemment modernisé situé à Valence, en France.
« Bon nombre des projets sur lesquels nous travaillons aujourd’hui ne se concrétiseront sur des avions qu’à partir des années 2030 et au-delà.
Yves Maheo, directeur du Centre d’Excellence Aéronautique SKF.
« C’est la première fois que nous disposons d’une seule et même installation équipée pour tester tous les composants montés sur un avion, qu’il s’agisse d’un mouvement de roulement ou de glissement, de composants qui tournent à des milliers de tours par minute ou qui sont immobiles », explique Paolo Andolfi, responsable de l’ingénierie aéronautique chez SKF.
Le développement des produits aéronautiques est un processus long et particulièrement collaboratif. « Les délais de mise en œuvre d’une technologie innovante peuvent aller jusqu’à dix ans, indique Yves Maheo, directeur du Centre d’Excellence Aéronautique. Bon nombre des projets sur lesquels nous travaillons aujourd’hui ne se concrétiseront sur des avions qu’à partir des années 2030 et au-delà. »
Contrairement à d’autres secteurs, les clients finaux sont impliqués très en amont dans les projets d’innovation. « Nous collaborons avec nos clients à tous les niveaux, reprend Yves Maheo. Ils nous communiquent leurs feuilles de route technologiques et nous, les nôtres. Ils envoient leurs ingénieurs ici à Valence pour travailler avec nos équipes sur les projets de développement et sur les essais. »
Cette étroite relation de travail permet à SKF de s’assurer une totale compréhension des besoins de ses clients à chaque projet. « Exemple, le Textilub, un nouveau composite textile autolubrifiant pour articulation aéronautique. Les avions ont une longue durée de vie, leurs pièces s’usent inévitablement et doivent être remplacées. Une grande partie de notre activité a toujours été axée sur le prolongement de la durée de service de ces composants. Cependant, nos clients nous ont dit que c’est très bien d’avoir des composants qui durent plus longtemps, mais ce qu’ils veulent en réalité, ce sont des pièces qui s’usent de manière régulière et prévisible. Cela permet de gérer plus facilement les réparations et les remplacements. Nous avons pu intégrer ces observations dans le développement du nouveau matériau. »
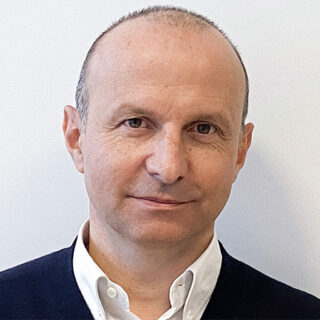
Responsable de l’ingénierie aéronautique chez SKF.
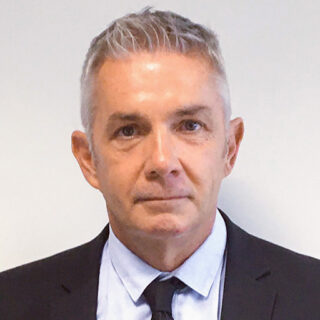
Directeur du Centre d’Excellence Aéronautique SKF.
Roulements hybrides de pointe
La mise au point de roulements pour les futures générations de turboréacteurs est un autre domaine de grand intérêt pour la recherche. Ces composants sont situés au cœur d’un avion moderne : ils supportent l’arbre principal tournant à grande vitesse dans les gros turboréacteurs à double flux montés sur tous les avions de ligne.
Les moteurs modernes comptent plus de dix roulements le long de leur arbre principal. L’avènement de moteurs intégrant un réducteur entre la soufflante à l’avant du moteur et les composants du compresseur à l’arrière a rendu nécessaire le recours à de nouveaux roulements fortement chargés.
Les capacités des roulements pour moteur ont un impact considérable sur les performances de ce dernier. Ils doivent supporter des charges et des vitesses de rotation élevées, et remplir leur mission avec fiabilité pendant une longue durée de service dans un environnement chaud et exigeant. En outre, les ingénieurs doivent tenir compte de l’espace occupé par les roulements au moment où ils conçoivent l’architecture d’un nouveau moteur.
Par ailleurs, à chaque nouveau modèle, les roulements sont soumis à des charges plus élevées, les concepteurs cherchant à optimiser l’efficacité énergétique au sein de l’espace disponible. Du fait de cette tendance, les montages et les matériaux des roulements actuels approchent de leurs limites physiques.
Un projet récemment terminé impliquant l’expertise de l’ensemble du groupe SKF a conduit au développement d’un nouveau matériau susceptible d’améliorer considérablement les performances des roulements de moteur de demain. Le projet ARCTIC (Advanced Bearing Technologies to Increase Capabilities) a été financé par le partenariat public-privé Clean Sky 2 Joint Undertaking, dans le cadre du programme de recherche et d’innovation Horizon 2020 de l’Union européenne, avec, pour principal porteur, Rolls-Royce.
« Actuellement, les roulements les plus performants pour les moteurs aéronautiques sont de conception hybride, indique Alexandre Mondelin, ingénieur en développement produit chez SKF. Leurs éléments roulants sont en céramique et leurs bagues en acier. » Dans ce type de montage, explique-t-il, la limite des performances du roulement est déterminée par la capacité de la bague en acier à résister aux contraintes de contact très fortes exercées par des billes en céramique plus rigides.
L’objectif du projet ARCTIC était de créer un nouvel acier allié associé à des éléments roulants en céramique capables de supporter des contraintes de contact supérieures de 15 % et des vitesses de rotation plus élevées de 25 % par rapport aux aciers conventionnels pour roulements aéronautiques. Développer un tel matériau à partir d’une feuille blanche était un chantier d’envergure. Les aciers utilisés actuellement dans les roulements de moteur remontent à la seconde moitié du 20e siècle. « Il est également très rare de développer un nouvel acier à destination d’une seule et unique application », ajoute Jean-Baptiste Coudert, ingénieur en développement technologique chez SKF.
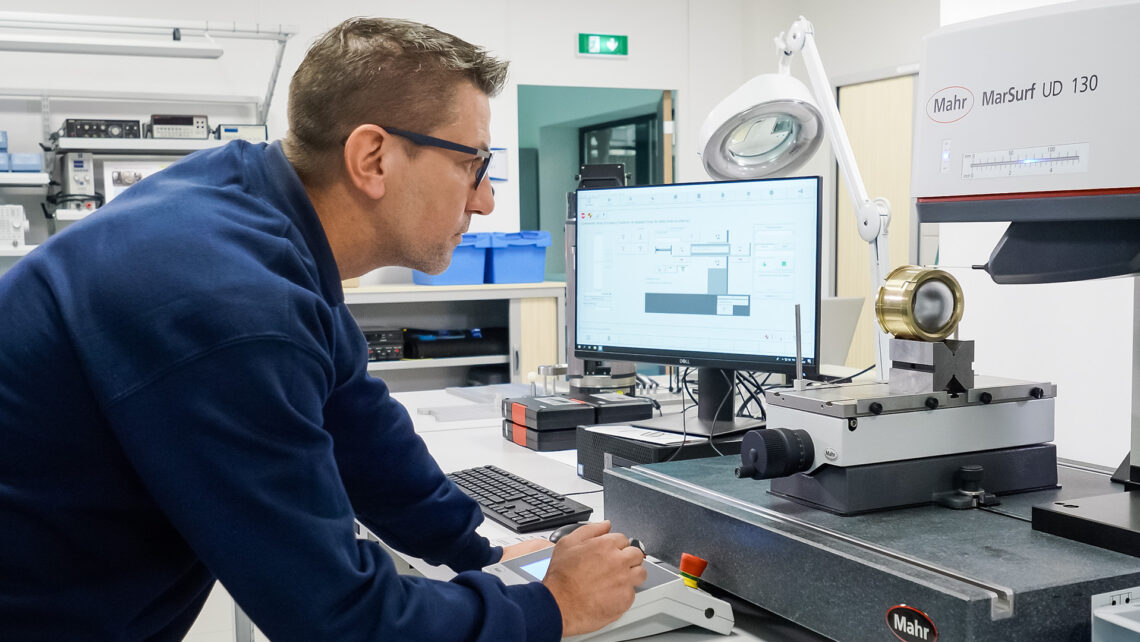
Un alliage innovant
Pour mettre au point ce nouvel acier, une équipe du SKF Research and Technology Development Centre aux Pays-Bas a mis en pratique des décennies d’expertise en matière de science des matériaux. À l’aide du logiciel interne de simulation des matériaux Thermo-Calc, elle a testé des dizaines de formules. Chemin faisant, elle a également dû concevoir un nouveau cycle de traitement thermique et s’assurer que la fabrication des matériaux et leur traitement thermique pouvaient être réalisés de manière économique à l’échelle industrielle. Puis il a fallu qu’Yves Maheo et son équipe à Valence créent et construisent un nouveau banc d’essai à grande vitesse et de forte puissance à destination des roulements grandeur nature pour arbres principaux fabriqués à partir du nouvel acier.
Baptisé ARCTIC15, l’acier allié final breveté a rempli tous les objectifs du projet. Une augmentation de 15 % de la capacité de charge peut sembler modeste, mais elle se traduit par une hausse très notable des performances du moteur. Les roulements hybrides fabriqués à partir du nouvel acier peuvent supporter 50 % de charge en plus que les modèles conventionnels. Cela permet de monter sur les moteurs des roulements de plus petites dimensions sur un arbre principal au diamètre plus réduit.
L’application de cette technologie au modèle actuel a permis de diminuer jusqu’à 25 % la perte de puissance : de ce fait, les dimensions des systèmes de lubrification et de refroidissement ont pu être réduites et l’ensemble du système, allégé. Une optimisation plus poussée de la conception pourrait accroître la densité de puissance, ouvrant la voie à une amélioration du rendement énergétique et à une diminution de 25 à 30 % des émissions de CO₂ et d’oxydes d’azote (objectifs des clients).
ARCTIC15 a montré plusieurs atouts supplémentaires au cours des essais. Il dure plus longtemps que les aciers conventionnels, en particulier en cas de lubrification insuffisante ou d’absence d’huile. En outre, les roulements hybrides en ARTIC15 avec éléments roulants en céramique génèrent moins de vibrations que les roulements traditionnels, ce qui améliorera les performances et la fiabilité globales du moteur.
SKF collabore actuellement avec Rolls-Royce à la mise en œuvre industrielle de cette solution. Puis viendront les essais de roulements hybrides en ARCTIC15 sur les prototypes de l’UltraFan® H2 du motoriste, la nouvelle génération de turboréacteurs ou turbosoufflantes à engrenages (geared turbofans) pour avion de ligne.
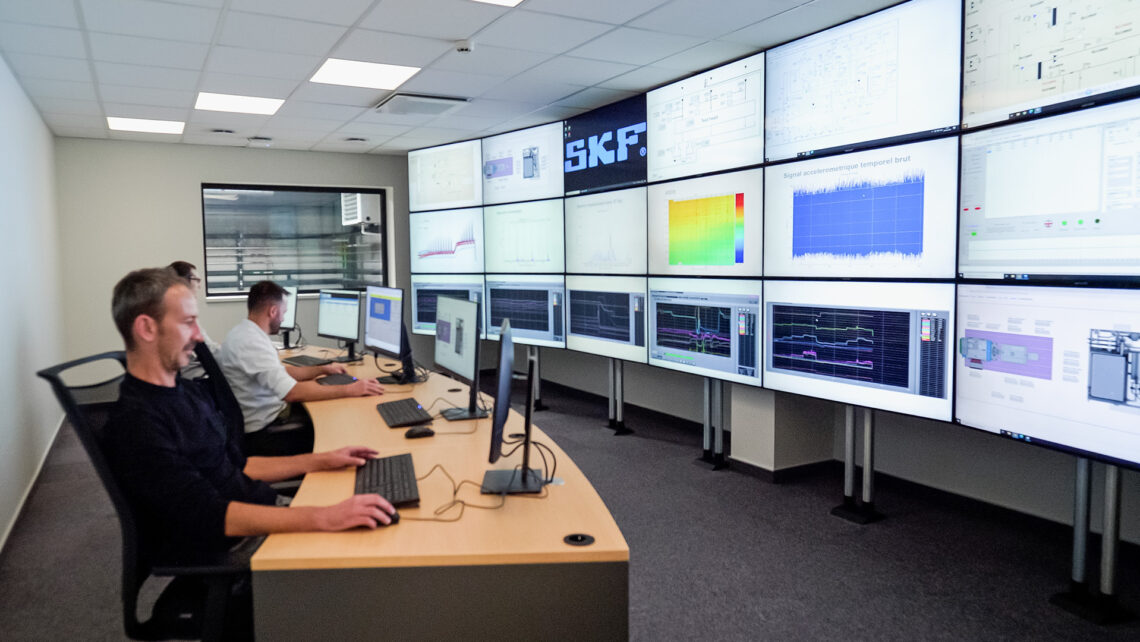
Le nombre de passagers en hausse
Le secteur aérien a été l’un des plus durement touchés par la pandémie de Covid-19, les restrictions liées aux déplacements ayant entraîné partout l’effondrement de la demande de vols. Trois ans après les premiers confinements, la plupart des pays ont supprimé leurs dernières barrières en la matière. Même la Chine, qui a imposé certaines des règles les plus strictes, a annoncé en mars 2023 qu’elle revenait aux règles prévalant avant la pandémie en matière de visas pour les touristes étrangers et les voyageurs d’affaires.
Les avions font de nouveau le plein. En 2022, le nombre de passagers a augmenté de 47 % par rapport à l’année précédente, et, les vols long-courriers ayant retrouvé leur attractivité, le nombre total de voyageurs-kilomètres s’est accru de 70 %.