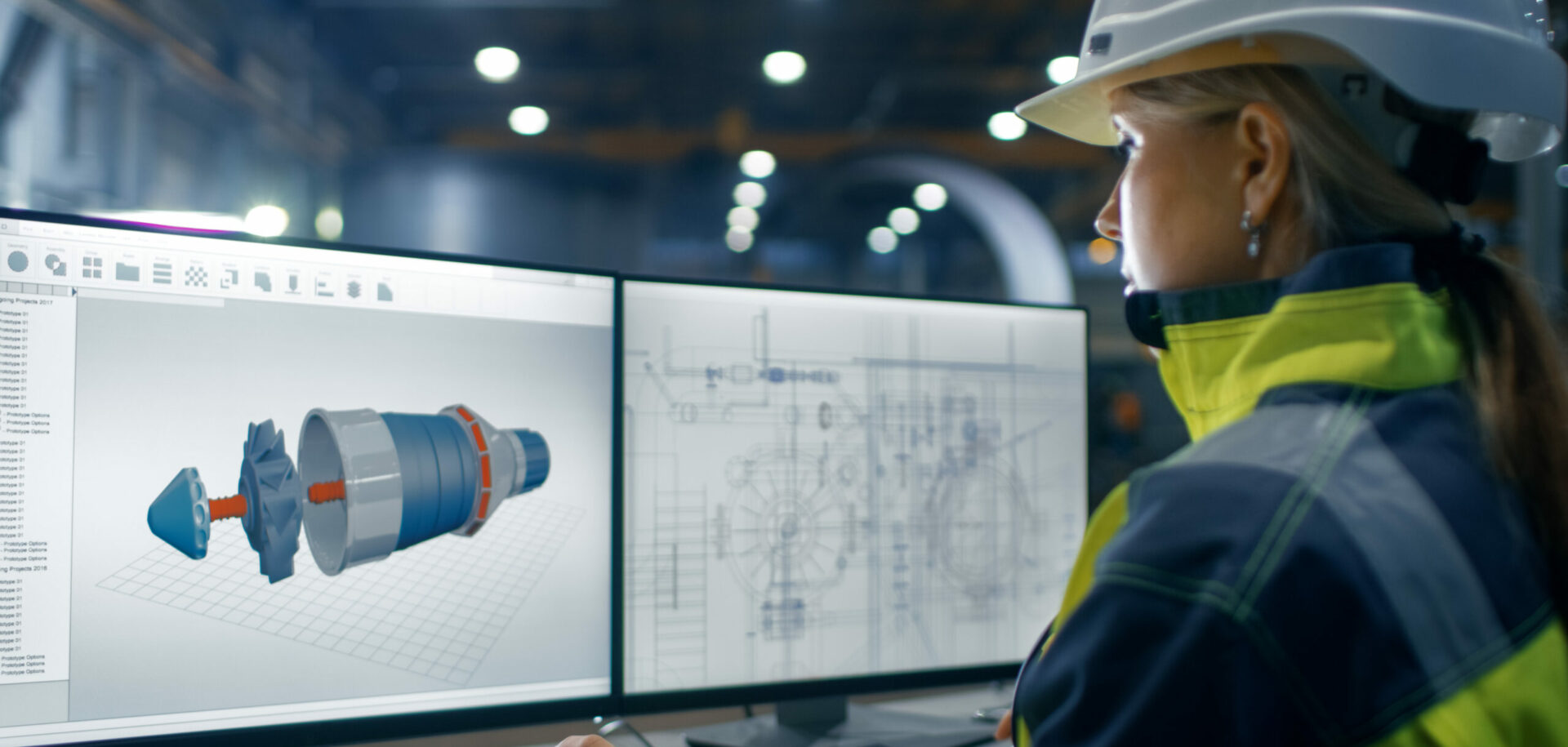
Solutions pour systèmes d’entraînement
Les systèmes d’entraînement destinés à des applications ferroviaires, comme les boîtes de vitesses et moteurs de traction, doivent être puissants, conformes aux réglementations environnementales, extrêmement fiables, économiques et peu exigeants en termes de maintenance. Les cahiers des charges relatifs à ces applications sont beaucoup plus stricts que dans la majorité des autres secteurs en raison du poids élevé des véhicules ferroviaires et de la nécessité d’intervalles de maintenance longs. Cela suppose de recourir à des roulements et ensembles-roulements spécifiques, intégrant des capteurs, et de mettre en place des services spécifiques et une stratégie de maintenance conditionnelle.
Résumé
Les systèmes d’entraînement ferroviaires servent à transmettre à l’essieu monté le couple du moteur de traction ou moteur à combustion, qui fonctionne généralement à des vitesses de rotation supérieures, par le biais d’une ou plusieurs boîtes de vitesses. SKF a développé un portefeuille de solutions pour accroître la fiabilité, allonger les intervalles de maintenance et améliorer la rentabilité. SKF a récemment publié un guide technique sur les systèmes d’entraînement qui couvre les roulements, ensembles-roulements, capteurs, la maintenance conditionnelle et les services associés.
Liens apparentés
SKF Railway Technical Handbook
Contact commercial
Gottfried Kuře, Gottfried.Kure@skf.com
Les systèmes d’entraînement ferroviaires servent à transmettre à l’essieu, le couple du moteur de traction ou du moteur à combustion, qui fonctionne généralement à des vitesses de rotation supérieures, par le biais d’une ou plusieurs boîtes de vitesses.
SKF propose une large gamme de solutions, fruit de connaissances acquises par SKF dans le domaine ferroviaire, qui lui ont permis de développer une gamme unique de produits et solutions pour systèmes d’entraînement. Cette gamme inclut des roulements, des joints, des systèmes de lubrification, des solutions mécatroniques et des services.
Applications historiques
La diminution des coûts de maintenance, la réduction de l’encombrement et l’amélioration de la fiabilité ont été des moteurs clés dans la mise en œuvre de nouvelles solutions de roulements pour les boîtes de vitesses et moteurs de traction.
Les premiers modèles étaient équipés de paliers lisses lubrifiés à l’huile. Ces roulements nécessitaient une intervention humaine quotidienne pour le contrôle du niveau d’huile. En 1918, SKF a affirmé qu’il était possible de réduire de 25 à 70 % les coûts de maintenance des roulements sur les tramways en remplaçant les paliers lisses par des roulements à rotule sur billes (Fig. 1).
Vitesse
Au fil du temps, les vitesses atteintes par les véhicules ferroviaires, de voyageurs comme de marchandises, ont augmenté. La vitesse du véhicule combinée au diamètre de roue détermine la vitesse de rotation de l’arbre de sortie de boîte de vitesses et de ses roulements. La vitesse du moteur de traction et d’entrée de boîte est un multiple de cette vitesse de sortie déterminé par le rapport de vitesse. Le produit des deux facteurs que sont la vitesse du moteur de traction (n) et le diamètre moyen des roulements (dm) est un paramètre important dans le choix de la taille de roulement, du modèle de cage et du jeu de rouleaux, ainsi que du lubrifiant et de sa viscosité.
En dehors de la vitesse du véhicule, la valeur n x dm a augmenté du fait de l’augmentation de la vitesse du moteur de traction permise par une géométrie plus condensée de ce dernier. De plus, des modèles de moteurs de traction puissants ne sont possibles qu’avec des vitesses de moteur supérieures. Cependant, la longueur horizontale totale de l’ensemble boîte de vitesses-moteur de traction est limitée par un facteur de conception en particulier : la distance entre les deux roues qui est déterminée par l’écartement des rails.
Puissance
L’évolution des modèles de moteurs de traction est marquée par une augmentation progressive de la puissance. Prenons l’exemple d’un modèle allemand de locomotive électrique à 4 essieux dotée de quatre moteurs de traction. Aujourd’hui, la puissance délivrée par ses moteurs de traction est 10 fois supérieure à celle du premier modèle mis en circulation (Fig. 2). La puissance motrice liée à la vitesse influe directement sur les charges exercées sur l’arbre d’entrée de boîte de vitesses. Les modèles d’entraînements modernes sont axés sur la réduction des charges supportées par les roulements et sur la lubrification à l’huile dans la mesure du possible.
Intervalles de maintenance
La technologie de propulsion à courant alternatif (CA) pour les véhicules électriques offre l’avantage de réduire les besoins de maintenance.
Les roulements des moteurs de traction doivent pouvoir atteindre une durée moyenne de fonctionnement d’environ 15 ans sans maintenance. Certaines limites, en termes de durée, des roulements de moteurs de traction actuels lubrifiés à la graisse empêchent d’atteindre cet objectif. Toutefois, de nouvelles conceptions, des modèles de calculs et résultats d’essais peuvent servir de tremplin pour s’en approcher progressivement. Le nouveau guide SKF consacré à l’optimisation de la durée de vie des graisses se révèle un outil précieux pour allonger les intervalles de maintenance habituels (Fig. 3).
Opportunités de réduction de l’encombrement
Pour une puissance de traction donnée, l’augmentation de la vitesse du moteur de traction se traduit par une diminution du couple supporté par l’arbre de moteur et l’arbre d’entrée de boîte de vitesses. Les charges supportées par le roulement sont par conséquent réduites, ce qui permet de recourir à des modèles de roulements de dimensions inférieures. Les dimensions des roulements ont par ailleurs diminué au fil du temps du fait de l’augmentation de leur capacité de charge (Fig. 4). L’impact en termes de réduction du frottement a été très positif et le rendement des roulements s’est ainsi amélioré.
Rodage
Un autre exemple d’évolution est la diminution des températures de fonctionnement des roulements à rouleaux coniques lors de la phase de rodage. Pendant cette phase, un montage intégrant des roulements à rouleaux coniques classiques génère un frottement significatif, observable à travers un pic de température, qui entraîne une usure.
Un montage intégrant des modèles de roulements à rouleaux coniques SKF actuels fonctionne avec un frottement et donc un échauffement et une usure nettement réduits, sous réserve que les roulements soient correctement montés et lubrifiés.
Roulements INSOCOAT et hybrides
Les exigences relatives aux roulements de moteurs de traction ont nettement augmenté depuis l’introduction des moteurs de traction contrôlés par des variateurs de fréquence pour les systèmes de propulsion. Le passage du courant électrique à travers les roulements peut causer rapidement des dommages (Fig. 6). Avec les roulements INSOCOAT et hybrides, le risque de passage de courants électriques dommageables à travers le roulement est nettement réduit.
Dans les applications en courant continu (CC), un roulement INSOCOAT se comporte comme une résistance (purement ohmique) ordinaire. La couche d’oxyde d’alumine constitue un isolant ; la résistance ohmique, R, de la couche est le paramètre important. La tension de claquage de la couche standard s’établit à 1 000 VCC et la résistance dépasse les 50 MΩ, ce qui procure une isolation suffisante du roulement.
Les roulements hybrides offrent des propriétés d’isolation électrique supérieures, en particulier pour les applications de systèmes de convertisseurs hautes fréquences modernes, car ils sont équipés d’éléments roulants en nitrure de silicium de qualité roulements (Fig. 7). Ce matériau leur confère des propriétés d’isolation électrique supérieures, y compris en présence de fréquences très élevées.
Des intervalles de maintenance plus longs sont possibles en appliquant les lignes directrices pour une durée de vie optimale de la graisse. Les paramètres clés sont les suivants :
- conception optimisée du roulement, notamment en ce qui concerne le nombre et la taille des éléments roulants ;
- modèle de cage amélioré ;
- joints à chicane pour protéger le système de roulement des impuretés ;
- type de graisse spécifique et quantité étudiée.
Ensembles-roulements pour moteurs de traction
L’ensemble-roulement pour moteurs de traction (TMBU) repose sur une conception compacte qui offre une solution sans entretien pour des intervalles de maintenance plus longs. Il permet de réduire la longueur totale du moteur ou, autre possibilité, d’augmenter la longueur de l’enveloppe métallique du rotor et du stator d’un moteur donné de manière à accroître la puissance nominale. Le principe de conception de ce sous-système réunit plusieurs fonctions au sein d’une seule unité : graisse, étanchéité et fonctions de blocage. La collerette intégrée facilite le montage.
Le TMBU est un ensemble-roulement étanche et prélubrifié, conçu pour un montage sur le carter du moteur par le biais de la collerette (Fig. 8). La graisse utilisée a été sélectionnée pour offrir une durée de service accrue, y compris à des températures de fonctionnement élevées. L’ensemble-roulement est équipé de joints à chicane sans contact qui ne s’usent pas. Il est disponible en version hybride avec des éléments roulants en céramique pour éviter les dommages causés par le passage du courant électrique et des capteurs pour surveiller les conditions de fonctionnement. Les fonctions d’isolation électrique et de surveillance des paramètres opérationnels, comme la température, la vitesse et la position absolue pour le contrôle du système de propulsion, sont proposées en option.
Capteurs
Le concept de TMBU instrumenté (Fig. 9) offre diverses possibilités de détection et de mesure : détection de position absolue pour dispositifs de commande de moteurs de traction, détection du sens de rotation et mesure de la vitesse pour systèmes de commande de freins et mesure de la température dans le cadre d’une surveillance des conditions de fonctionnement.
Dans la plupart des cas, les capteurs sont intégrés dans le dispositif d’étanchéité de la bague extérieure de l’ensemble-roulement. Cette conception offre des opportunités de réduction de l’encombrement et du nombre de pièces.
Maintenance conditionnelle
La maintenance conditionnelle est une technologie aboutie qui offre des opportunités d’amélioration de la sécurité et de la fiabilité et d’allongement des intervalles de maintenance. Des systèmes de détection et l’application d’algorithmes complexes pour le traitement des données permettent de détecter des anomalies à un stade précoce. Cela laisse suffisamment de temps pour entreprendre des réparations avant que des défaillances ou des dommages mécaniques significatifs n’apparaissent.
Rénovation
La rénovation de roulements1) peut se traduire par une réduction significative des émissions de CO2 par rapport à la production d’un roulement neuf. Elle nécessite en effet 97 % d’énergie en moins. En allongeant la durée de service des roulements (Fig. 11), ce processus réduit les déchets et le gaspillage des ressources naturelles. Les spécialistes SKF sont en mesure de déterminer si un roulement peut ou non être rénové.
La rénovation de roulements contribue pour une large part à la réduction du coût du cycle de vie à travers les avantages suivants :
- réduction significative des coûts par rapport à des roulements neufs ;
- allongement de la durée de service ;
- disponibilité supérieure se traduisant par une réduction des stocks ;
- analyse des causes de défaillance et recherche d’actions correctives ;
- possibilité de performances supérieures grâce aux améliorations apportées lors du processus de rénovation ;
- retours d’informations relatives aux applications permettant d’améliorer les conditions de service et la technologie de maintenance du client ;
- réduction de l’impact sur l’environnement à travers une diminution des déchets et de la consommation de matières premières et d’énergie.
Publications
SKF a récemment publié un guide technique qui traite des roulements de moteurs de traction et des boîtes de vitesses, des capteurs, de la maintenance conditionnelle et des services associés. Il fournit également des recommandations pour optimiser la durée de service des roulements.
1) Certains opérateurs et constructeurs ferroviaires utilisent également les termes de « remise en état » et de « reconditionnement » pour distinguer des exigences spécifiques. Le terme « réusinage » suppose généralement des opérations de polissage et de rectification. Il semble cependant qu’il n’y ait pas de définition globale pour ces termes qui peuvent se chevaucher ou être contradictoires.
INSOCOAT et SKF Explorer son des marques déposées du Groupe SKF.