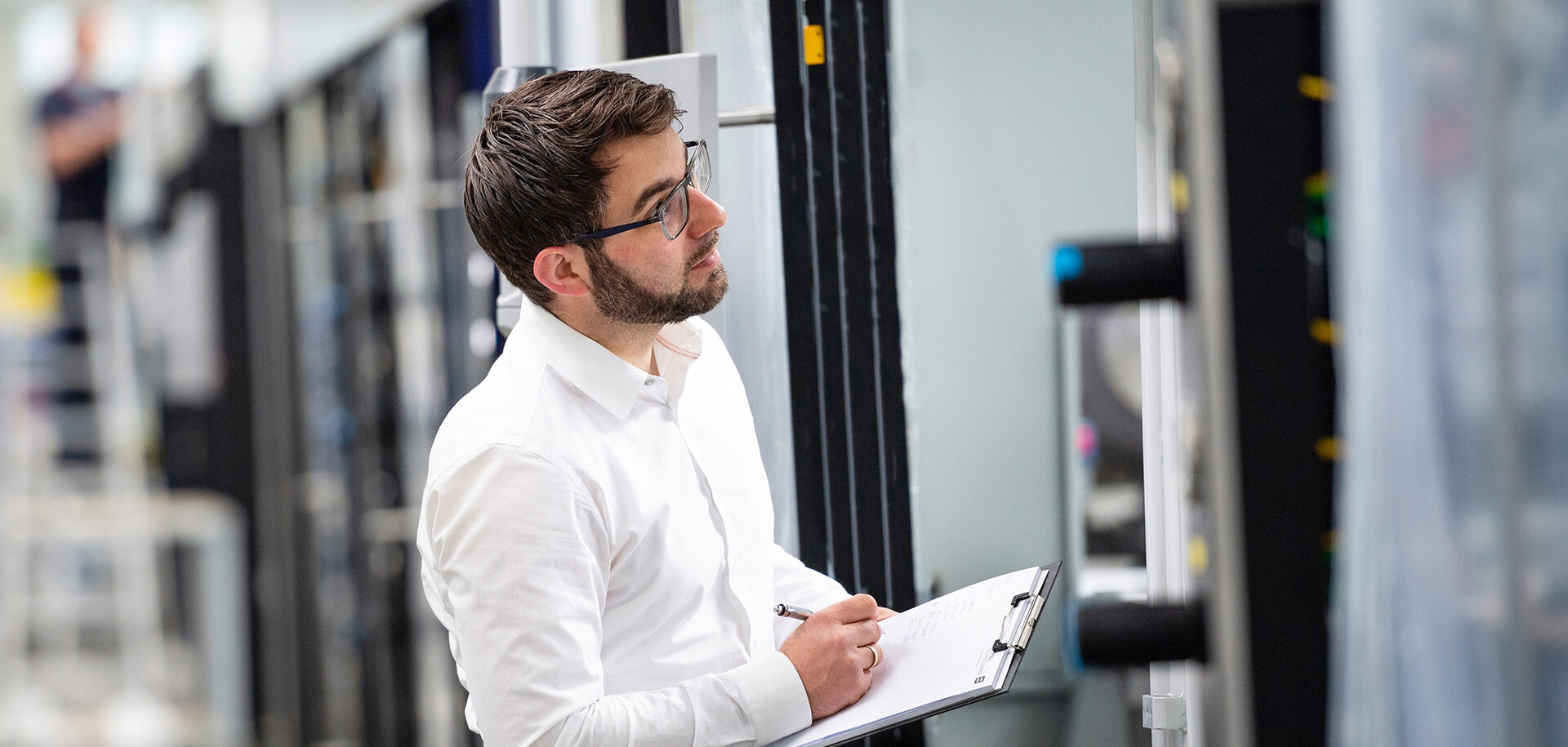
From plastic to fibre – a new packaging machine aligns with sustainable technology
There are many environmental challenges in the packaging industry. The German company Kiefel is stepping up to those challenges with a cutting-edge natural-fibre packaging machine that allows manufacturers to produce and operate their machinery more sustainably. It also uses SKF´s automated lubrication system to make the process safer and cleaner.
An important part of Kiefel’s offering is helping clients with their processes and making them more environmentally friendly. That’s why the company provides its packaging-industry clients with machines that use SKF’s automated lubrication system.
“Our products must not only look good, but also perform to the highest standards,” says Kiefel Fibre Thermoforming Product Manager Richard Hagenauer. “For the optimal running of a machine, it requires constant lubrication.”
To develop the NATUREFORMER KFT 90, a machine for making packaging products out of natural fibres such as paper, Hagenauer says Kiefel needed a partner with world-class expertise in lubrication. It also wanted a partner that fitted Kiefel’s focus on sustainability. SKF proved the perfect match.
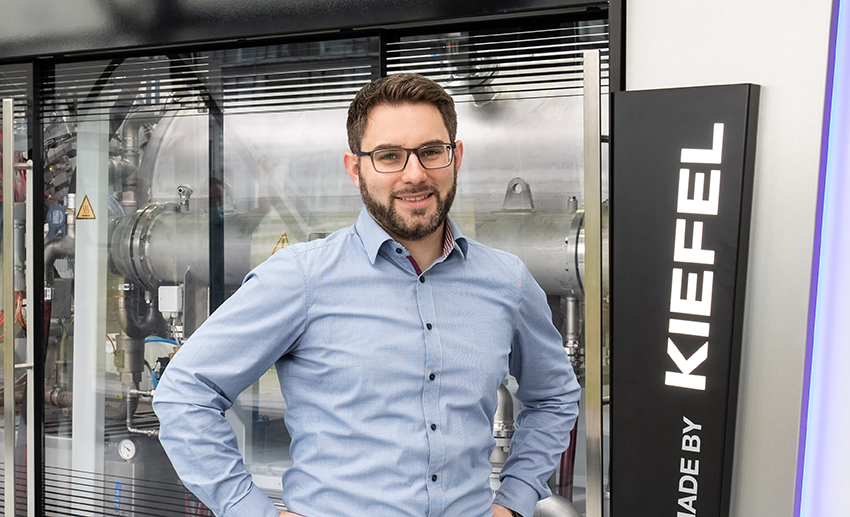
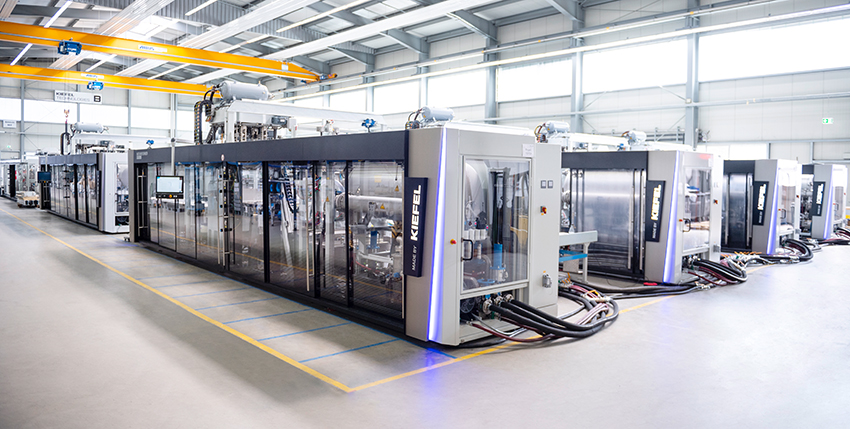
Profit loss with manual lubrication
There are many disadvantages with manual lubrication. Maintenance operators face a task that is not only extremely difficult and unpleasant, but also potenially dangerous. They have to climb inside the machine, trying not to burn themselves on the hot surfaces as they reach over to the awkward lubrication points.
Manual lubrication affects the company’s profit margin because the machine must be shut down for lubrication, but it does not end there. Operators often apply more lubricant than necessary to avoid having to re-open the machine soon afterwards. This results not just in a further waste in expenditure, but also in lubricant leakages and sticky, slippery workfloors.
SKF’s centralized lubrication systems have managed to overcome all these challenges, providing companies such as Kiefel with a solution that in turn drives innovation and produces advanced machines.
Swapping plastic for paper
A fundamental part of Kiefel’s corporate DNA is its focus on sustainability. The company provides clients with state-of-the-art machines, which develop high-quality, hygienic and environmentally friendly products such as the natural-fibre packaging machine, as well as recycled and bio-based polymers.
The SKF lubrication system is ideal for us because everything is automatic, without any climbing inside and without any wastage of lubrication.
Richard Hagenauer, Kiefel Fibre Thermoforming Product Manager
This natural-fibre packaging machine employs fibre thermoforming technology that allows clients to manufacture everything from food containers to inlays for mobile phones or plant pots out of natural fibres, including virgin fibres, cardboard and annual plants. It runs on high-efficiency servo-driven engines and allows fast and easy tool changes. The integrated modules also allow for automated inspection, stacking, sleeving, boxing and palleting.
The machine’s unique feature is its water-extraction function. Using cold pre-pressing technology, it reduces the moisture in the packaging product down to 60 percent. The final press with heated tools then reduces this down to about 7 percent. The result is a recyclable product with extremely high-quality surfaces made from natural fibres – and it occurs within seconds.
Premium customized solutions
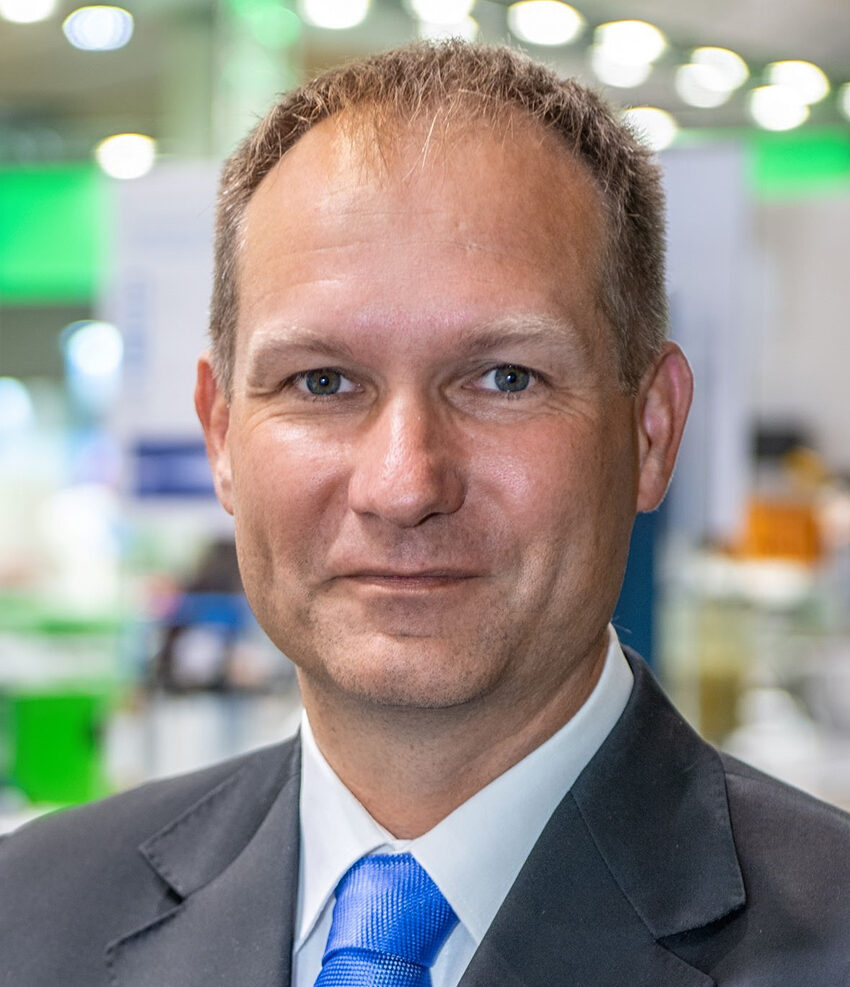
“To fulfil customer requirements, Kiefel needed an automatic lubrication system for their NATUREFORMER KFT 90 series and they chose our proven, reliable lubrication system,” says Norbert Spiegel, account manager SKF.
“Here, we could help them adopt a sustainable and fast approach by customizing our system to fit their existing machines. No new machine design was needed, which is a much more sustainable and much quicker approach than starting from scratch.”
Richard Hagenauer comments, “The SKF lubrication system is ideal for us because everything is automatic, without any climbing inside and without any wastage of lubrication. There is therefore more control there than via the manual lubrication process, which is of course beneficial for our customers.”
Lubrication solution for the NATUREFORMER KFT 90 machine
SKF’s progressive lubrication systems can be used on small to large machines with dispersed lubrication points that require varying lubrication quantities. The systems consist of a pump connected to at least one primary metering device. If needed, further lubrication points can be reached by connecting the primary and second-level metering devices via branch lines.
Here, the pump supplies lubricant to the metering devices with pressure up to 350 bar (5000 psi), depending on the pump model. The metering devices then split the lubricant into even or pre-defined lubricant quantities. The amount of lubricant for each outlet pair depends on the type of metering device being used. Progressive systems can dispense a precise, metered amount of lubricant to up to 100 lubrication points over distances of approximately 20 metres.
For the NATUREFORMER KFT 90, it was important that the system was able to supply automatically and reproducibly a small and exact amount of grease to the lubrication points. It also had to be easy to adapt because it was known and proven on other Kiefel machines.
The system consists of a P203 pump with SSV and SSVD metering devices. It has about 10 lubrication points per machine and the lubrication line length is about 10 metres. The system is prefilled with NLGI 2 grease and the pump reservoir has a capacity of four litres.
The system also proved to be a good match for the NATUREFORMER machine, for which Kiefel required traceability of lubrication cycles, reduced and constant lubricant flow to lubrication points and a real-time defect signal for machine control.