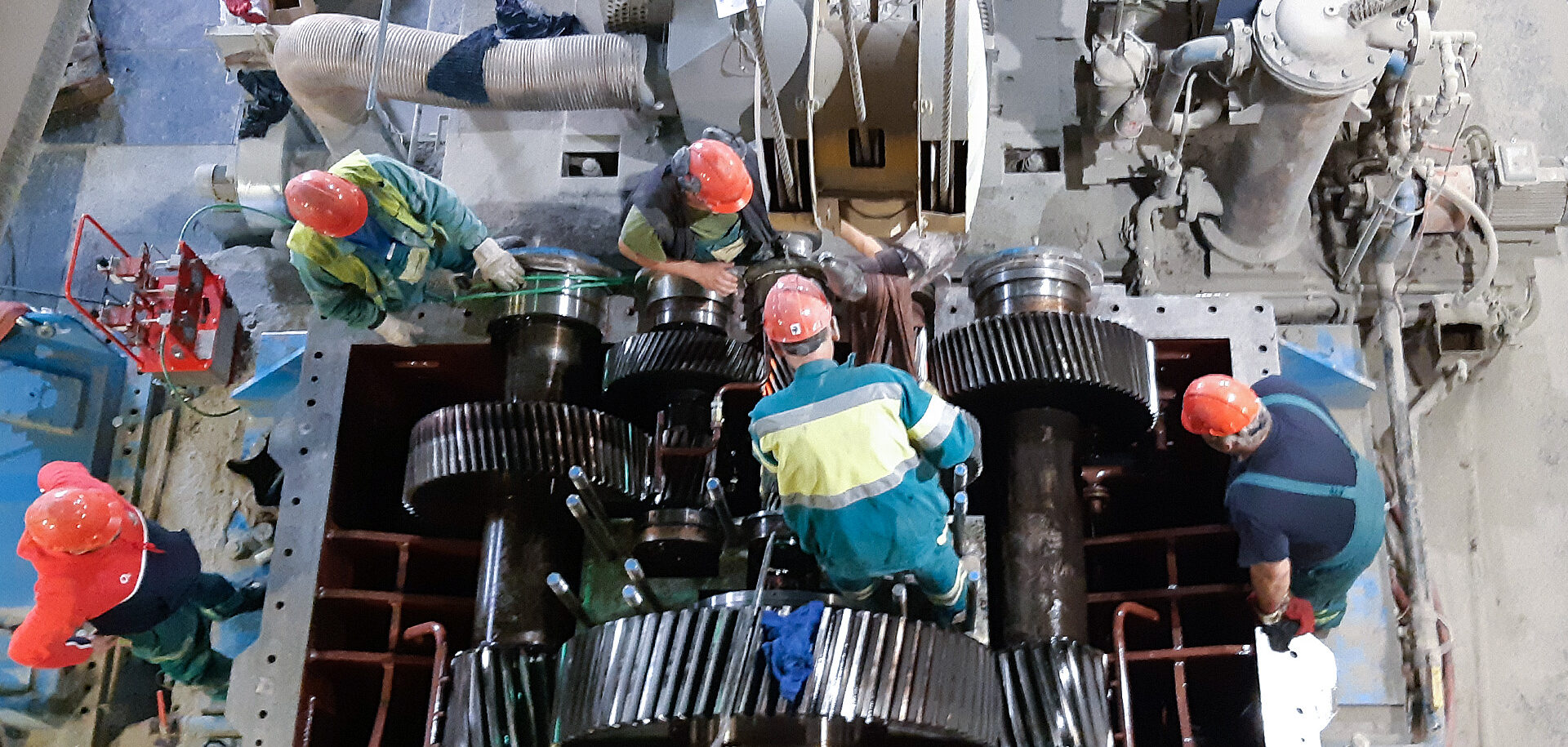
Good vibrations at the cement plant
The Českomoravský Cement plant at Radotín in the Czech Republic had been experiencing unplanned stops due to damaged gearboxes. But thanks to a vibration analysis solution from SKF, the cement producer was able to put an end to the problem.
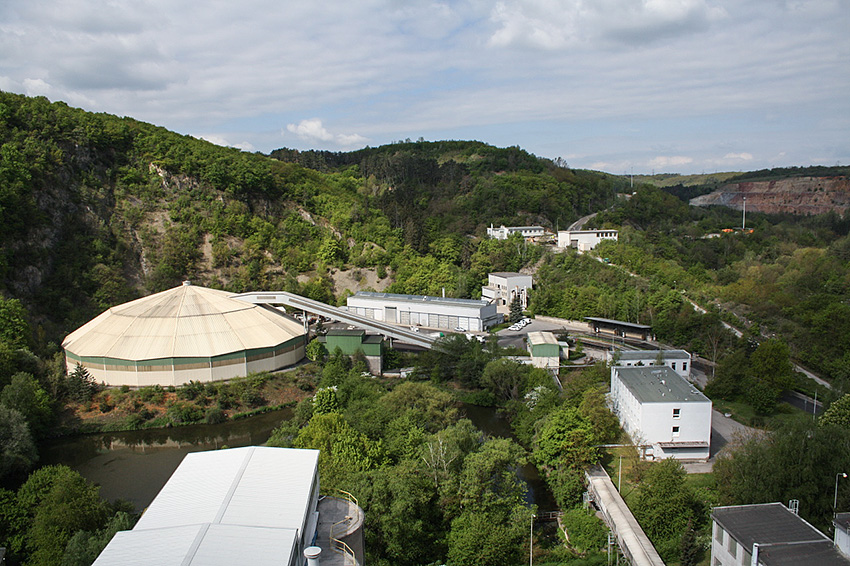
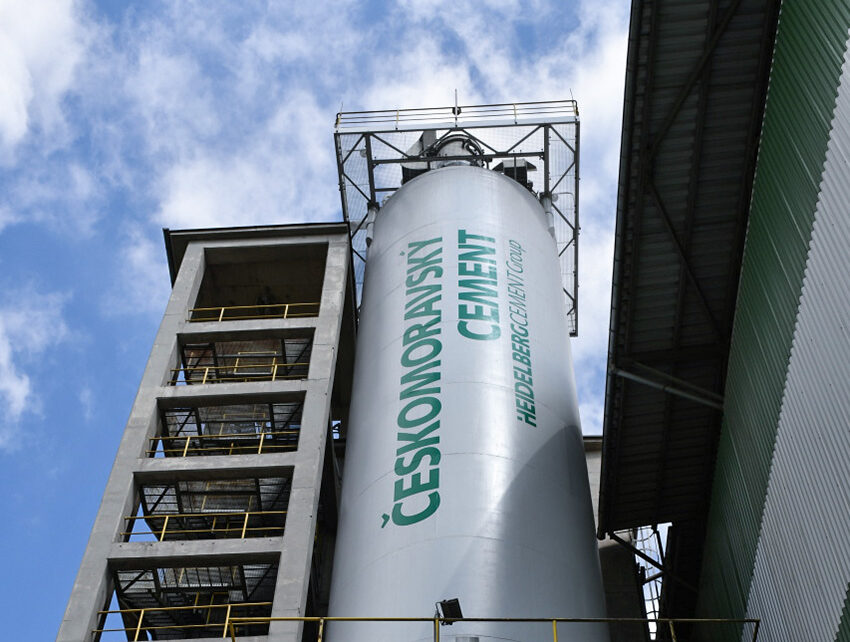
“Each time it happened, it usually meant a shutdown of the whole cement grinding line for several days, which reduced our capacity by half,” explains Pavel Nevlud, head of the plant’s central maintenance department. “And although the machinery suppliers kept adjusting and adapting the components, the rate of failure frequency did not change.”
The trouble was that although the gearboxes were fitted with sensors for monitoring bearing and oil temperatures, and although there was an oil-flow sensor in the lubrication circuit, they were not equipped with vibration sensors. This meant that any damage was usually identified late in the deterioration process, when the gearbox noise was too loud to be ignored or when a significant temperature rise was recorded in a damaged bearing.

It wasn’t until the repair workers called in experts from SKF’s Rotating Equipment Performance Centre that the tide really started to turn.
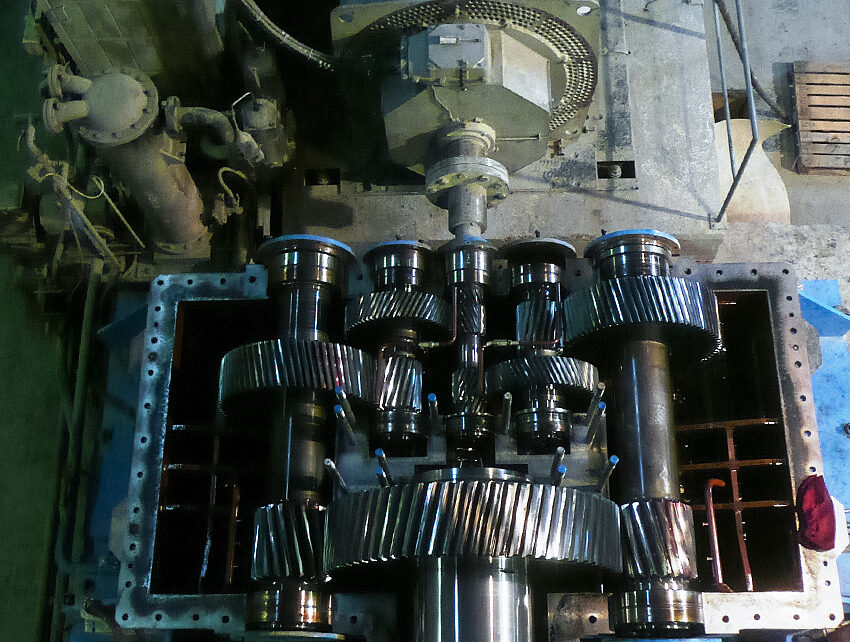
It was the Multilog IMx system’s permanently mounted vibration sensors that allowed SKF’s experts to fix the cement plant’s problems in double-quick time, explains SKF Regional Sales Representative Martin Niesner.
“The bearing damage resulted in increased vibration levels in defined frequencies that could be captured through our sensors,” he explains.
Data collected by the sensors was automatically transferred to a host computer, which then rapidly processed it. That information enabled the Radotín plant’s workers to detect faults early or even to avoid them completely, as the system automatically provided recommendations for eliminating existing or impending glitches.
What we really needed was to eliminate as much as possible the extent of the damage in the event of a future gearbox failure.
Pavel Nevlud, head of central maintenance, Českomoravský Cement
The cement plant’s managers were so impressed by the turnaround in performance that, after the expiry of the gearboxes’ warranty, Českomoravský Cement signed a long-term support contract with SKF.
Under the terms of the deal, SKF specialists monitor operational conditions remotely. The SKF’s Multilog IMx unit constantly checks all sensors, wiring and electronics, and system messages are generated automatically.
“SKF’s remote diagnostics can identify possible damage to the bearings or toothing at the initial stage,” Niesner says. Unlike route-based measurements, which only provide snapshots, permanent online monitoring can distinguish between short-term fluctuations and a genuine, continual deterioration in condition.
The process saves costs and labour and enables better management of repairs, Niesner explains. What’s more, his colleagues are now able to respond to glitches in a much more considered and focused manner.
“It is of course not possible to repair the gearbox while it is running,” Niesner says. “It is necessary to shut down the mill and thus the entire production line. However, early identification of the occurrence of a fault usually allows this outage to be planned and prepared in order to carry out a repair.”
And, he says, early planned intervention means better planning of maintenance, increased efficiency of the machinery and, of course, a greater level of safety for employees, who have permanent access to current data from their control desk.
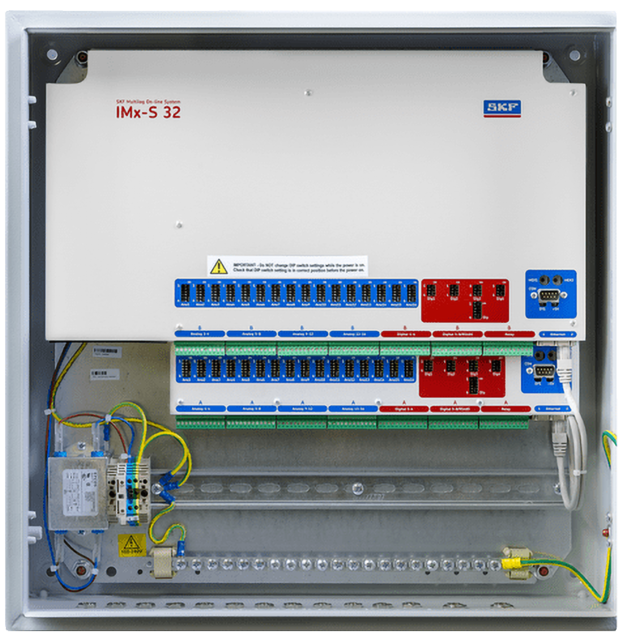