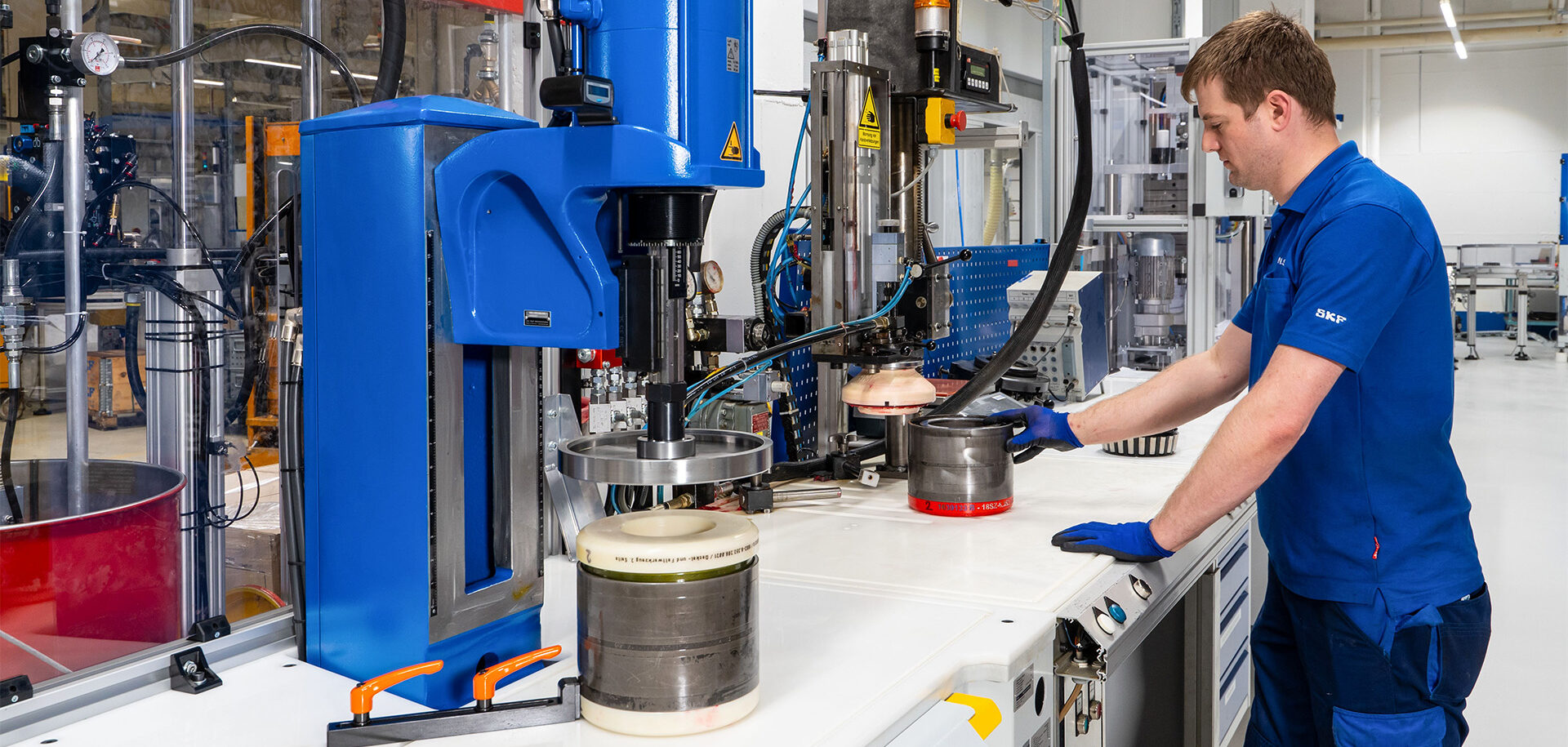
Il ricondizionamento abbatte i costi e la CO2
Il ricondizionamento dei cuscinetti svolge un ruolo essenziale nel settore ferroviario mondiale. Tra i suoi vantaggi, la riduzione dei tempi di fermo e revisione, il taglio dei costi di manutenzione e un minore impatto ambientale.
La ricerca crescente da parte degli operatori ferroviari di soluzioni sostenibili per gestire le attività di manutenzione, riparazione e revisione delle loro macchine trova nel ricondizionamento dei cuscinetti una soluzione più rispettosa dell’ambiente, oltre che decisamente vantaggiosa. Il suo approccio permette infatti di ridurre i costi totali di gestione grazie a minori costi di manutenzione, maggiore sicurezza, affidabilità operativa ed elevata efficienza energetica.
Per il mondo ferroviario, sensibile al fattore tempo, è importante contare su risposte e revisioni più rapide per mantenere l’efficienza del materiale rotabile e, auspicabilmente, anche su un minor numero di scarti per tagliare ulteriormente i costi.
Perché ricondizionare?
Ricondizionare un cuscinetto costa decisamente meno che acquistarne uno nuovo. Nel processo di ricondizionamento, inoltre, si consumano meno energia e risorse, e si produce un minor numero di scarti. Nelle applicazioni ferroviarie questo significa spendere meno della metà del costo di un cuscinetto nuovo. Senza contare che le emissioni di CO2 si riducono addirittura dell’85 percento.
Soluzioni su misura
“SKF ha istituito una rete globale di 20 centri dedicati al servizio di ricondizionamento in ambito ferroviario, dove ogni anno vengono ricondizionati circa 220.000 cuscinetti per sale montate”, dichiara Alfredo Monetti, Manager dei settori railway remanufacturing product line e business development. “Per essere più vicina ai clienti, SKF è presente con cinque centri nel continente americano, sette in Europa, uno in Africa e sette nell’area Asia-Pacifico”. I volumi gestiti sono molto diversi, con i piccoli centri che trattano circa 1.000 cuscinetti all’anno e quelli più grandi che ne trattano anche 100.000. A prescindere dalla domanda, il servizio viene effettuato adottando standard qualitativi sistematicamente elevati.
La digitalizzazione dei processi è importante per sostenere i miglioramenti futuri
Alfredo Monetti, Manager dei settori railway remanufacturing product line e business development di SKF.
Per ottimizzare le prestazioni complessive dei cuscinetti, in accordo alle più recenti modifiche di progetto, SKF offre la sostituzione dei sistemi di tenuta e il passaggio a componenti di categoria superiore. “SKF propone inoltre modelli di business 100/100, dove ogni cuscinetto danneggiato e rottamato è sostituito con uno nuovo, in modo che il cliente riceva dal centro servizi lo stesso numero di cuscinetti inviati”, spiega Monetti.
SKF applica al ricondizionamento gli stessi standard qualitativi, le conoscenze e le competenze che applica al processo di produzione. Nei centri servizi confluisce la notevole competenza nell’analisi dei cedimenti dei cuscinetti, unita a procedure scrupolosamente pianificate per adattarsi ai requisiti di ogni applicazione. Comprendere le condizioni in cui operano i cuscinetti permette di includere nel processo di ricondizionamento migliorie a sistemi di lubrificazione, soluzioni di tenuta e rivestimenti. Ai cuscinetti delle sale montate rimessi in servizio si possono unire dispositivi per il monitoraggio e il rilevamento con sensori al fine di prolungare ulteriormente la durata di esercizio.
Prima di iniziare qualsiasi intervento, SKF fornisce al cliente un’idea chiara riguardo al costo del ricondizionamento e ai potenziali risparmi ottenibili rispetto all’acquisto di cuscinetti nuovi.
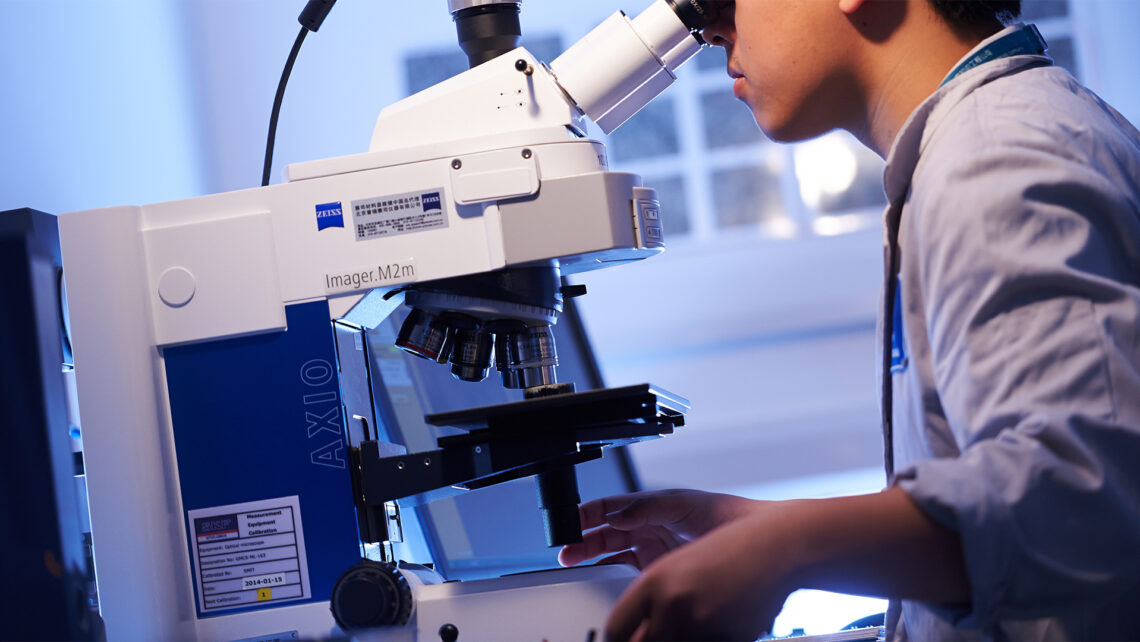
Le fasi del ricondizionamento
I centri SKF sono certificati per offrire un servizio completo, che viene eseguito da tecnici specializzati nell’utilizzo delle tecniche più all’avanguardia. SKF si avvale di un sistema di gestione avanzato, che consente di identificare in maniera univoca i cuscinetti durante il ricondizionamento e garantirne la loro totale tracciabilità nel ciclo di vita attuale e futuro. “La digitalizzazione dei processi è importante per implementare futuri miglioramenti”, commenta Monetti.
Ogni cuscinetto viene smontato, sgrassato e pulito. I componenti sono sottoposti a ispezione e viene stilata una dettagliata relazione. I cuscinetti idonei al ricondizionamento possono essere riportati in condizioni di completa efficienza attraverso procedure di lucidatura, rettifica e sostituzione dei componenti. I cuscinetti che durante il successivo intervallo di esercizio non superano la durata residua calcolata possono essere ricondizionati, il che significa che i risparmi sui costi ottenibili attraverso il ricondizionamento sono sostanziali.
Miglioramento continuo
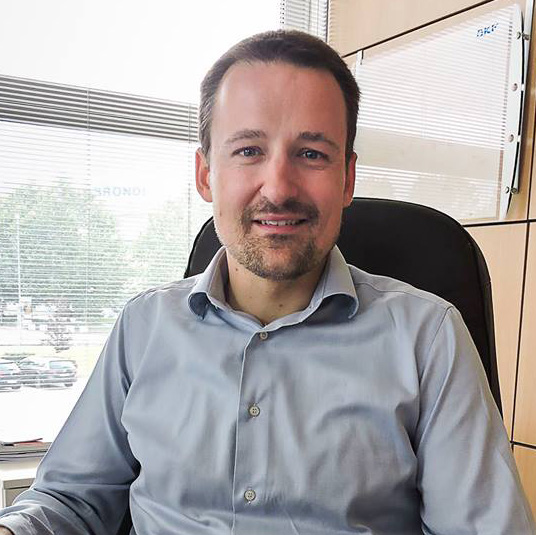
Il feedback professionale e dettagliato sui cuscinetti ispezionati consente di identificare le aree di miglioramento per l’applicazione e il progetto. I clienti del settore ferroviario si orientano sempre più verso i contratti Rotating Equipment Performance, con i quali SKF supporta programmi per il miglioramento continuo del progetto attraverso i dati e le informazioni sulle prestazioni delle applicazioni di SKF railway engineering.
SKF è costantemente impegnata nello sviluppo di nuove tecnologie da applicare ai propri processi, per esempio per rendere più economico il ripristino delle piste e ridurre gli scarti.
“SKF si sta anche adoperando per automatizzare il processo di ispezione visiva utilizzando l’intelligenza artificiale [IA]”, afferma Monetti. “Questo consentirebbe di uniformare le procedure nei vari centri servizi ferroviari, evitando ogni possibile soggettività umana”. E aggiunge che gli stabilimenti SKF sono caratterizzati da un livello di automazione crescente.
Oltre a fornire i propri servizi dedicati, SKF collabora con altre società e clienti per offrire formazione, supporto e servizi. Entro la fine del 2022, entrerà in funzione la prima linea automatizzata di ricondizionamento SKF presso lo stabilimento di un cliente in Brasile.
La domanda di servizi di ricondizionamento per le ferrovie è in rapida crescita, e SKF prevede un incremento del business del 50 percento entro il 2023.
La conoscenza nel campo dei cuscinetti e delle speciali applicazioni in cui operano è stata essenziale per lo sviluppo di processi di ricondizionamento in grado di supportare la necessità dei clienti di ridurre i costi totali di gestione attraverso la riduzione dei costi di acquisto dei cuscinetti, l’ottimizzazione delle scorte e la riduzione degli scarti. Riportare a nuova vita componenti usati contribuisce inoltre in modo significativo a ridurre l’impatto ambientale complessivo. “Il ricondizionamento dei cuscinetti per sale montate è, in sostanza, un pilastro dell’economia circolare, che assicura agli operatori ferroviari di tutto il mondo minori costi totali di gestione”, sintetizza Monetti.
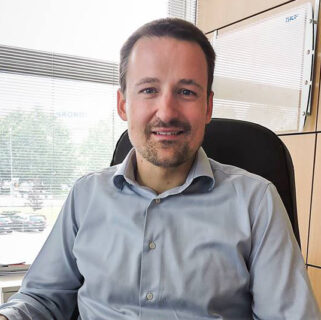
Miglioramento continuo
Il feedback professionale e dettagliato sui cuscinetti ispezionati consente di identificare le aree di miglioramento per l’applicazione e il progetto. I clienti del settore ferroviario si orientano sempre più verso i contratti Rotating Equipment Performance, con i quali SKF supporta programmi per il miglioramento continuo del progetto attraverso i dati e le informazioni sulle prestazioni delle applicazioni di SKF railway engineering.
SKF è costantemente impegnata nello sviluppo di nuove tecnologie da applicare ai propri processi, per esempio per rendere più economico il ripristino delle piste e ridurre gli scarti.
“SKF si sta anche adoperando per automatizzare il processo di ispezione visiva utilizzando l’intelligenza artificiale [IA]”, afferma Monetti. “Questo consentirebbe di uniformare le procedure nei vari centri servizi ferroviari, evitando ogni possibile soggettività umana”. E aggiunge che gli stabilimenti SKF sono caratterizzati da un livello di automazione crescente.
Oltre a fornire i propri servizi dedicati, SKF collabora con altre società e clienti per offrire formazione, supporto e servizi. Entro la fine del 2022, entrerà in funzione la prima linea automatizzata di ricondizionamento SKF presso lo stabilimento di un cliente in Brasile.
La domanda di servizi di ricondizionamento per le ferrovie è in rapida crescita, e SKF prevede un incremento del business del 50 percento entro il 2023.
La conoscenza nel campo dei cuscinetti e delle speciali applicazioni in cui operano è stata essenziale per lo sviluppo di processi di ricondizionamento in grado di supportare la necessità dei clienti di ridurre i costi totali di gestione attraverso la riduzione dei costi di acquisto dei cuscinetti, l’ottimizzazione delle scorte e la riduzione degli scarti. Riportare a nuova vita componenti usati contribuisce inoltre in modo significativo a ridurre l’impatto ambientale complessivo. “Il ricondizionamento dei cuscinetti per sale montate è, in sostanza, un pilastro dell’economia circolare, che assicura agli operatori ferroviari di tutto il mondo minori costi totali di gestione”, sintetizza Monetti.
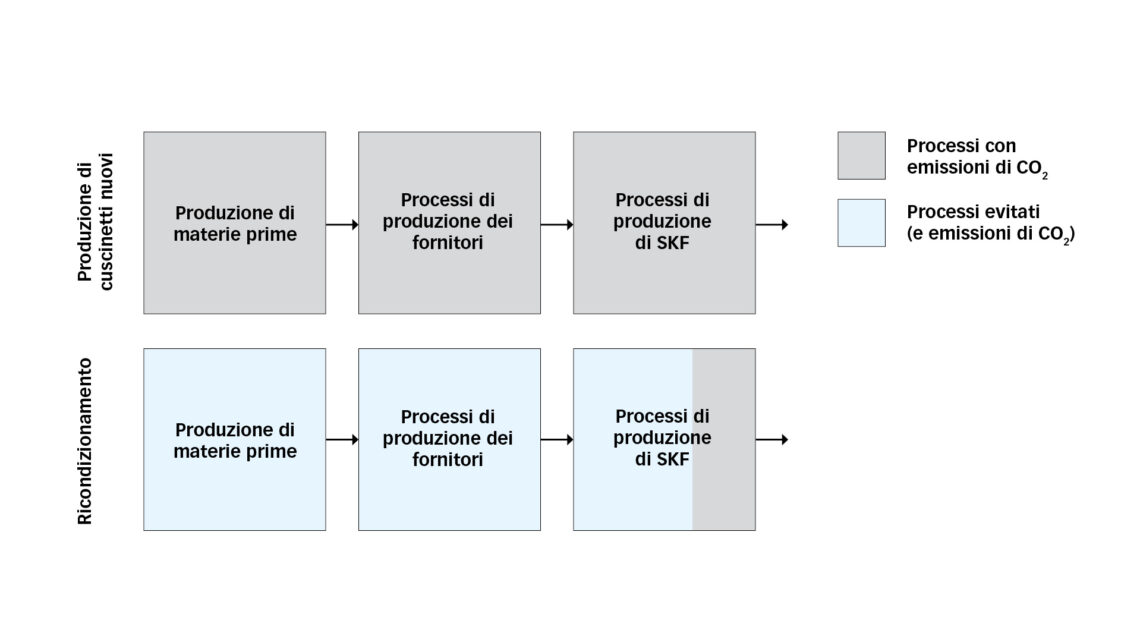
Calcolare il costo della sostenibilità
“Nel 2018, il consumo totale di energia del gruppo SKF è stato di 1.814.000 MWh”, dichiara Alfredo Monetti, Manager dei settori railway remanufacturing product line e business development, facendo riferimento alla relazione annuale SKF 2018. “Si stima che circa 1.350.000 MWh siano legati alla produzione di cuscinetti nuovi, il cui peso complessivo è stato di 457.000 tonnellate”. L’energia impiegata per produrre un kg di cuscinetti può essere calcolata dividendo 1.350.000 MWh per 457.000 tonnellate, pari a 2,9 kWh/kg”.
L’energia viene utilizzata anche nei processi a monte (p. es. fornitori di SKF). “Supponendo che il 60 percento dell’energia totale sia usata nei processi a monte e il 40 percento da SKF, il consumo sale a 7,25 kWh/kg”, spiega Monetti. “Se presumiamo che SKF per il processo di ricondizionamento di un cuscinetto impieghi l’85 percento di energia in meno rispetto a produrne uno nuovo, ne consegue che il consumo di energia per kg di cuscinetti ricondizionati è di circa 1,1 kWh/kg”.
Un bel risparmio netto di 6,1 kWh/kg. Supponendo che la media delle emissioni di CO2 da questa energia sia la stessa della media SKF, possiamo calcolare quanta anidride carbonica in meno è stata prodotta (il fattore di emissione medio SKF basato sul rapporto annuale è 0,273). 6.1 kWh/kg x 0,273 kg CO2/kWh= 1,7 kg CO2/kg. Se consideriamo un peso medio di circa 20 chilogrammi per cuscinetto, il risultato è un risparmio di CO2 di circa 34 chilogrammi per ogni cuscinetto.
“Attualmente sottoponiamo a revisione circa 220.000 cuscinetti all’anno”, dice Monetti. “Quindi il risparmio annuo complessivo di CO2 attualmente prodotto da SKF railway remanufacturing è di 7.480 tonnellate all’anno, e questo valore è destinato ad aumentare con la crescita dei volumi” (La cifra espressa è prudenziale, poiché si considerano solo le emissioni legate all’impiego di energia, esclusi tutti i trasporti).