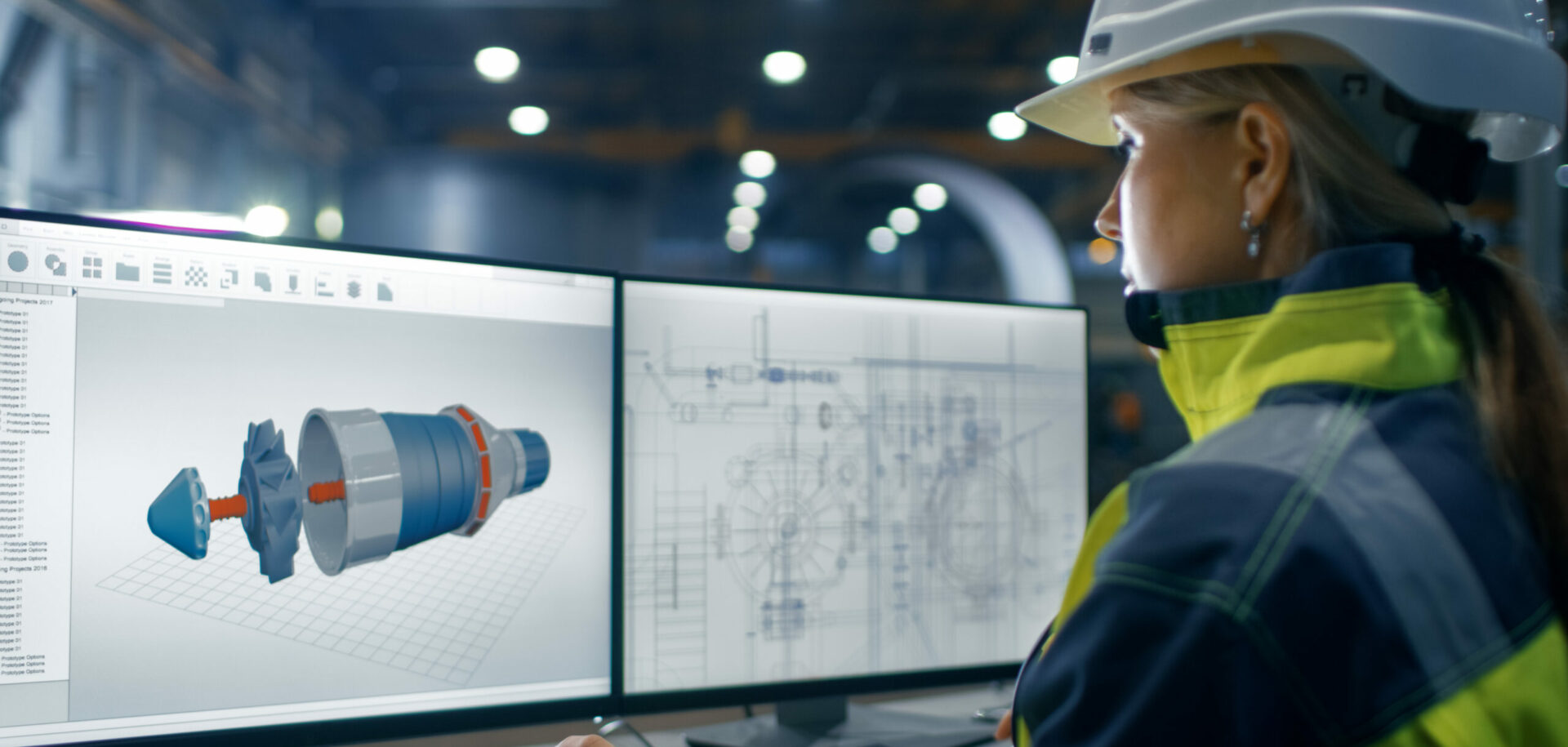
Sempre nel posto giusto
Spandau Pumpen gestisce i sistemi di refrigerazione per le macchine utensili nello stabilimento SKF Lubrication Systems nella Repubblica Ceca.
Un elemento importante nell’assicurare qualità elevata a costi contenuti in applicazioni di lavorazione dei metalli è l’alimentazione affidabile di refrigeranti alle macchine utensili in uso. Nello stabilimento SKF Lubrication Systems nella città ceca di Chodov, le pompe per refrigeranti di Spandau Pumpen (fig. 3) sono utilizzate nel processo di lavorazione e in un sistema di filtraggio modulare a isole (fig. 1), che comprende un trasportatore di trucioli. Fin dalla loro installazione, i supervisori hanno notato una riduzione dei costi di funzionamento e dell’energia e una maggiore affidabilità dei sistemi.
Spandau Pumpen
Nello stabilimento di SKF a Chodov si producono anche distributori progressivi per sistemi di lubrificazione. Tuttavia, nelle prime fasi della linea di produzione si erano verificati alcuni problemi. Negli utensili raffreddati internamente continuavano a verificarsi ostruzioni causate da residui di lavorazione. Inoltre, sulle macchine relativamente lente, come variante ai filtri erano state utilizzate soluzioni con un’unica stazione. Il team di progetto della tecnologia di produzione di SKF, coordinato dal tedesco Steffen Siegemund, fu incaricato di assicurare che la produzione a Chodov fosse più flessibile, con una qualità superiore e a costi contenuti. Si decise di acquistare fresatrici a mandrino singolo rapide.
Per chiarire come si possono manipolare in modo efficiente i trucioli e come è possibile recuperare e immettere nuovamente il refrigerante nel processo di produzione, il team di progetto di SKF e il reparto di acquisto globale si sono consultati con Mayfran GmbH ad Aachen, in Germania. In collaborazione con gli specialisti dei sistemi di filtraggio e dei trasportatori di trucioli, hanno valutato e confrontato i vantaggi e gli svantaggi delle opzioni disponibili per soluzioni con un’unica stazione e a isole e anche con alimentazione centralizzata. Si decise quindi di optare per un sistema modulare a isole con trasportatore di trucioli. Siegemund ha dichiarato che lui e il suo team furono molto soddisfatti della soluzione. “Abbiamo implementato con successo il progetto con Mayfran GmbH”, ha commentato.
Il sistema di filtraggio (fig. 2) serve due linee di produzione, ciascuna con tre macchine utensili ① ② ③ e ④ ⑤ ⑥ e una soluzione con un’unica stazione ⑦. Il sistema gestisce la pulizia in linea di trucioli di dimensioni fino a 25 µm, oltre a quelli di dimensione fino a 5 µm in una seconda fase di filtraggio fine (processo parallelo) con un filtro in carta idrostatica ⑧. Il mezzo filtrato attraverso questo processo viene raccolto nel serbatoio definito ultrapulito ⑬. Il sistema è dotato di un serbatoio protettivo secondario e soddisfa i requisiti della legge federale tedesca sulla protezione delle acque (WHG). Inoltre è dotato di un refrigeratore a immersione ⑨ con una potente unità di controllo. Lo stabilimento di SKF pertanto è pronto ad affrontare un aumento di produzione e, se necessario, può portare il refrigeratore in linea per mantenere il refrigerante a una temperatura di esercizio costante.
Supporto dall’interno
L’ultimo tassello, il produttore della pompa adatta, era ancora mancante, ma il team di progetto di SKF è riuscito a trovarlo all’interno di SKF: Spandau Pumpen, la cui sede si trova a Berlino, fa parte del Gruppo SKF dal 2004. L’azienda sviluppa e costruisce potenti soluzioni per l’alimentazione e il recupero centralizzati e per le lavorazioni connesse alle macchine utensili. “Spandau Pumpen è un marchio indipendente all’interno del Gruppo SKF, perciò la scelta di affidarsi a prodotti propri era evidente”, ha dichiarato Martin Zverina, responsabile dello stabilimento a Chodov.
Spandau Pumpen ha fornito tre pompe a bassa pressione della serie PS (b) e tre pompe ad alta pressione della serie LMP (c), ciascuna con convertitori di frequenza, per la soluzione modulare a isole con trasportatore di trucioli. I motori commerciali standard che sono stati utilizzati potevano essere dotati facilmente di un convertitore di frequenza utilizzando un adattatore. Le pompe con convertitori funzionano in parallelo, riducendo la complessità dei controlli e aumentando l’affidabilità. Alcuni componenti sono progettati in modo ridondante per evitare cedimenti del sistema. Il processo di pulizia segue sempre lo stesso schema. Le pompe di rimando PSH Spandau (a) erogano il mezzo contaminato dalla lavorazione dalle macchine utensili al sistema di filtraggio.
Il fluido pulito e riutilizzabile viene convogliato in un serbatoio ⑫. Le pompe PS (b) erogano il mezzo filtrato da questo serbatoio pulito a bassa pressione, mentre le pompe a vite LMP (c) erogano di nuovo il mezzo filtrato finemente ad alta pressione per il riutilizzo nelle macchine (fig. 2).
Le pompe di lavaggio PSR (d) puliscono gli elementi filtranti del sistema di filtraggio ⑩ ⑪. Le pompe PMS (e) trasferiscono il mezzo dal serbatoio di raccolta degli scarti di lavorazione agli elementi filtranti ⑩ ⑪.
Grazie al controllo parallelo delle pompe, con funzione master, le pompe funzionano sempre in base alle esigenze effettive e assicurano una lunga durata di esercizio, perché lavorano in modo uniforme. Il sistema fornisce solo la quantità di refrigerante necessaria alle macchine collegate. Il controllo master o alternato assicura un tempo di funzionamento uniforme dei singoli gruppi pompa. Poiché non è necessario che tutte le pompe del processo siano in funzione tutti i giorni, ogni 24 ore viene selezionata una pompa master diversa; in questo modo tutti i componenti vengono esposti pressoché agli stessi livelli di usura. Le pompe ridondanti vengono controllate regolarmente per verificarne il corretto funzionamento.
I sensori nei tubi forniscono informazioni sullo stato effettivo della pressione di processo al convertitore di frequenza. Il convertitore quindi controlla la velocità di rotazione delle pompe per mantenere un livello di pressione costante. In questo modo non è necessario un controllo con bypass, perché si evita qualunque fabbisogno energetico supplementare e un inutile apporto di calore nel refrigerante.
Efficienza e potenza con costi di manutenzione contenuti
L’adattamento automatico della velocità mediante il convertitore di frequenza compensa anche una possibile diminuzione nelle prestazioni causata dall’usura di mandrini o rotori. Il punto di lavoro desiderato continua a essere controllato e si evitano involontari fermi del sistema. Un’esigenza immediata di riparazione viene rilevata in tempo, pertanto è possibile programmare in modo efficiente gli interventi di manutenzione. L’avvio graduale del sistema utilizzando la tecnologia del convertitore evita picchi di pressione, proteggendo componenti come i raccordi, i tubi e i filtri e aumentando la durata utile dell’intero sistema. Il risultato complessivo è una riduzione significativa dei costi operativi a Chodov.
Il sistema è anche efficiente dal punto di vista energetico. “In base alle misurazioni dei consumi e ai volumi di lavorazione, abbiamo calcolato un consumo energetico del solo 40% rispetto a quello di un sistema con un’unica stazione”, ha dichiarato Zverina, con un risparmio energetico del 60% (fig. 2). Inoltre, sono state incorporate nel sistema quattro pompe di rimando (serie PSR) per la pulizia dei filtri e due pompe per la contaminazione residua (serie PMS) per la rimozione dei residui. Per ciascun trasportatore di trucioli con stazioni di pompaggio laterali (fig. 4) sono state fornite due pompe di rilancio (serie PSH). Grazie a questa configurazione, lo stabilimento di SKF è perfettamente attrezzato per soddisfare i requisiti produttivi.
Il sistema di filtraggio ha un disegno modulare e può essere ampliato in qualsiasi momento, anche successivamente se necessario. Inoltre, il sistema di filtraggio a isole è flessibile per quanto riguarda l’applicazione delle macchine. Lo stesso tipo di sistema può essere utilizzato se, ad esempio, si aggiunge un centro di rettifica o un’altra linea di fresatrici a Chodov. L’unica cosa da cambiare sarebbe la tipologia dei filtri.
La soluzione fornita da Spandau Pumpen ha impressionato i supervisori a Chodov fin dall’inizio. Sono rimasti soddisfatti dell’elevata affidabilità quando si utilizzano le macchine in modo continuo e nei brevi periodi di manutenzione. SKF ha richiesto un processo completamente automatizzato a Chodov. Davanti alle pompe di rilancio non sono stati utilizzati elementi che richiedono pulizia manuale. Alcuni componenti, come gli elementi filtranti associati, sono stati sviluppati appositamente.
Capacità inutilizzata per altre macchine
Il responsabile dello stabilimento Zverina ha dichiarato che l’affidabilità della lavorazione è migliorata in modo significativo. “Siamo molto soddisfatti delle prestazioni dell’intero sistema, in particolare delle pompe Spandau (fig. 5)”, ha commentato. “Sono in funzione 24 ore su 24, sette giorni su sette, e forniscono il refrigerante in modo affidabile a sette macchine principali nell’area di assemblaggio meccanico. Negli stadi a bassa e ad alta pressione disponiamo di capacità inutilizzata per collegare altre due macchine. Con le soluzioni di Spandau Pumpen, lo stabilimento di SKF a Chodov è ottimamente preparato per il futuro. Se fosse necessario convertire altre aree di produzione in un concetto di produzione simile, sarebbe possibile posizionare e utilizzare un altro sistema a isole come una rete refrigerante.”
“Grazie al disegno modulare”, ha commentato Zverina, “può essere adattato al variare della domanda in qualsiasi momento.”