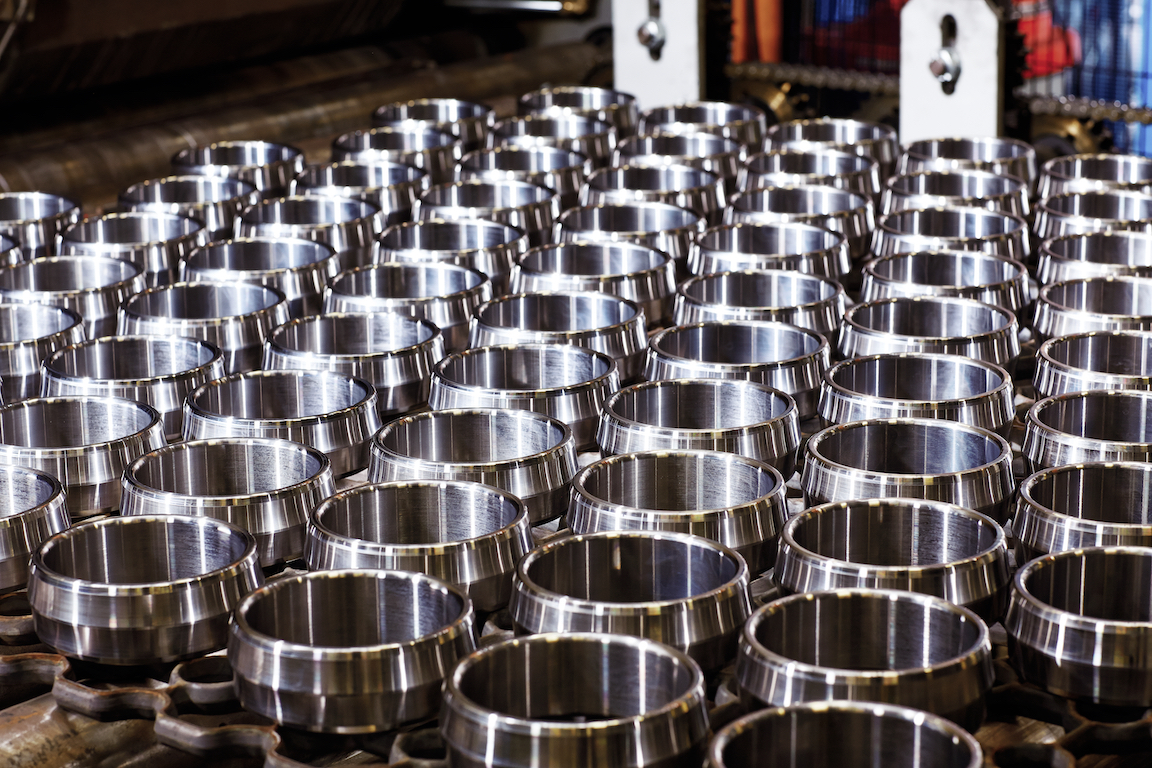
Maintenance in the Mine
Summary
The role of SKF
One of the most important components of the Phelps Dodge copper mine in Morenci, Arizona, is the in-pit crushing and conveying system, or IPCC. It is a system that uses conveyor belts to move ore for processing. Should a main pulley in the system fail, for example, it could stop the flow of the ore and halt processes that depend upon a steady supply of ore.
Like scores of other pieces of machinery and equipment at the mine, the conveyor system relies heavily on SKF bearings to keep it rolling. To ensure the mine employs precisely the right bearings, SKF provides on-site advice to maintenance and engineering staff and holds seminars on installation and maintenance.
SKF trains millwrights in the machine shop and field maintenance staff to mount and dismount bearings, housings, shafts, seals and other components. Training includes the inspection of working parts and choosing lubricants. SKF field staff provides instruction on how to inspect running bearings and find emerging problems. They are available, on short notice, to help replace existing products and recommend products when the mine introduces a new or modified process or piece of equipment.
From infrared cameras to ultrasonic devices, Phelps Dodge has set in place a maintenance programme that some consider to be among the best in the world.Production methods at the Phelps Dodge copper mine in Morenci, Arizona, have come a long way since the days, more than 120 years ago, when mules and brakemen were packed into narrow-gauge railroad cars to coast downhill with loads of ore to a smelter at the nearby town of Clifton. The mules would later be hitched to the emptied rail cars to pull them back up to the mine.
The railroad was retired some years ago. Morenci now has a system of conveyor belts that moves ore more efficiently, and smelters are no longer required because the mine employs an environmentally compatible chemical process called solution extraction/electro winning to extract 99.99 percent pure copper from the ore.
Morenci, the largest copper mine in North America, has evolved into one of the most technologically advanced and environmentally safe mines in the world.
That evolution has created the need for an increasingly sophisticated maintenance system for the thousands of pieces of equipment and machinery that must operate reliably to keep the open-pit mine on its 24-hour-a-day production schedule: Some 70,000 tonnes of ore are produced each day, resulting in about 360,000 tonnes of copper each year.
Reliability-centred maintenance
Over the past three and a half years, Phelps Dodge has implemented a reliability-centred maintenance programme that is designed to reduce costs and improve efficiency by taking over where routine maintenance leaves off.
Reliability-centred maintenance, or RCM, has been used for many years in aircraft manufacturing and other industries, but it is relatively new to the mining world.
The 18-member RCM group at Morenci functions as a service to other departments involved in the maintenance effort. The group’s emphasis is on monitoring equipment and machinery to identify potential failures long before they occur and to determine when a part or a piece of equipment might need to be replaced or repaired. It also focuses on ways to continually improve the maintenance programme, including using its findings to improve future projects and installations.
The RCM group is one of many elements in a broad-based maintenance programme, called PD-EMS (Phelps Dodge Equipment Management System), that involves personnel and departments throughout the mine. PD-EMS is successful at Morenci because all the entities that make up this programme work together toward the common goal of efficiently managing the equipment.
One facet of the programme, for example, is “autonomous maintenance,” in which equipment operators perform some of their own maintenance.
Other departments play essential roles in the planning and scheduling of maintenance crews, ordering and delivering materials, establishing key performance indicators to measure the success of maintenance operations, contractor management and a warranty administration effort to ensure that equipment under warranty is repaired or replaced under that warranty.
Ongoing analysis
Much of the RCM monitoring effort consists of taking readings with handheld infrared cameras to detect temperature differentials, using handheld devices to detect vibration levels or employing handheld ultrasonic devices to detect material flaws such as cracks in shafts. But the RCM programme includes a host of other types of monitoring, equipment analysis and operations that range from small electric motors to trucks, conveyor belts, ore crushers and the mine’s hydrometallurgical operations.
For example, the RCM staff analyses dozens of oil samples daily from engines, gearboxes, pumps, transmissions and hydraulic systems on equipment throughout the mine. This includes samples from the giant power shovels that excavate the ore, the trucks that haul it and the crushers that break it down to a suitable size for processing.
The RCM technicians employ a spectrometer that analyses the oil for chemical changes. Samples are also checked for particle content, cleanliness levels and viscosity. As needed, the technicians can look at the oil through a microscope to determine whether metal particles are present that would indicate bearing wear or gear deterioration.
One of the chief purposes of the oil sampling and other facets of the RCM programme is to provide plenty of advance notice for the maintenance workers who will need to repair or replace the equipment before it fails.
Besides reducing unscheduled down time, identifying potential problems reduces the chance that a component will damage other equipment or ruin an entire piece of machinery when it fails. A failed bearing could gouge and ruin a shaft, for example, or a failed gear could destroy a transmission.
Maintenance hierarchy
The maintenance planning staff classifies every piece of equipment in the mine into one of four categories: critical, essential, nonessential and run-to-failure.
A critical component or machine is one that will cause damage or destruction of the facility or immediately affect safety or the environment if it fails; an essential piece of equipment is one that supports production but is not critical.
A portion of the conveyor system is defined as essential because of the need to maintain stockpiles of ore. If the conveyor is not restored to service, it will ultimately halt production in the mine. On the opposite end of the scale is “run-to-failure” equipment, such as small electric motors that are operated until they fail because the cost of replacement and any down time is less than the expense of maintaining and monitoring them.
While most of the RCM technicians’ work has to do with the millions of mechanical parts at the mine, their monitoring methods can also be used to discover problems or inefficiencies that don’t involve moving parts.
An example is in the mine’s hydrometallurgical department, which is the final step in the solution extraction/electro winning process that produces copper without smelting. In this process, an acidic solution called raffinate percolates through football field-sized beds of ore.
The solution dissolves the copper from the ore. It trickles into a collection basin, whence it is pumped to mixer-settler systems to develop a copper-rich solution called electrolyte, and then it is transferred to one of three tank houses.
At the tank houses, which operate much like huge batteries, stainless steel sheets or “blanks,” which weigh about 8 kilogrammes, are immersed in the copper-rich solution, and a direct electrical current passes through the solution. The electrical current causes copper ions to attach to the blanks, and in about seven days a blank becomes a 99.99 percent pure copper “cathode” weighing about 90 kilogrammes.
Hot spots
The constant flow of electricity in the tank houses produces a coating of corrosion that can accumulate in places and interfere with the flow of electricity, creating “hot spots” that hinder the electroplating process and hence retard the production of copper.
The hot spots are not visible to the naked eye, so the RCM group trained a handful of tank house personnel in how to use handheld infrared cameras to detect them. Each tank house now has its own camera that workers use daily to check for hot spots and clear the problem areas of corrosion.
Infrared monitoring has many other applications, including looking for “cold spots” in a pipeline – portions of the line where the flow is reduced, which could be the result of a plugged line or a malfunctioning pump.
When Phelps Dodge announced in September 1999 that it would convert the entire Morenci operation to the solution extraction/electro winning process, the company called Morenci “one of the world’s exceptional mining operations.”
Visitors to Morenci often tell the RCM staff that the mine is a step ahead of others in its maintenance procedures. The RCM effort and the other elements of the maintenance programme are evolving constantly to adapt to changing technology and are expected to yield even greater benefits in the future, as the Morenci mine continues its commitment to maintaining a world-class equipment management system.
Bob Howard
a freelance journalist based in California, USA