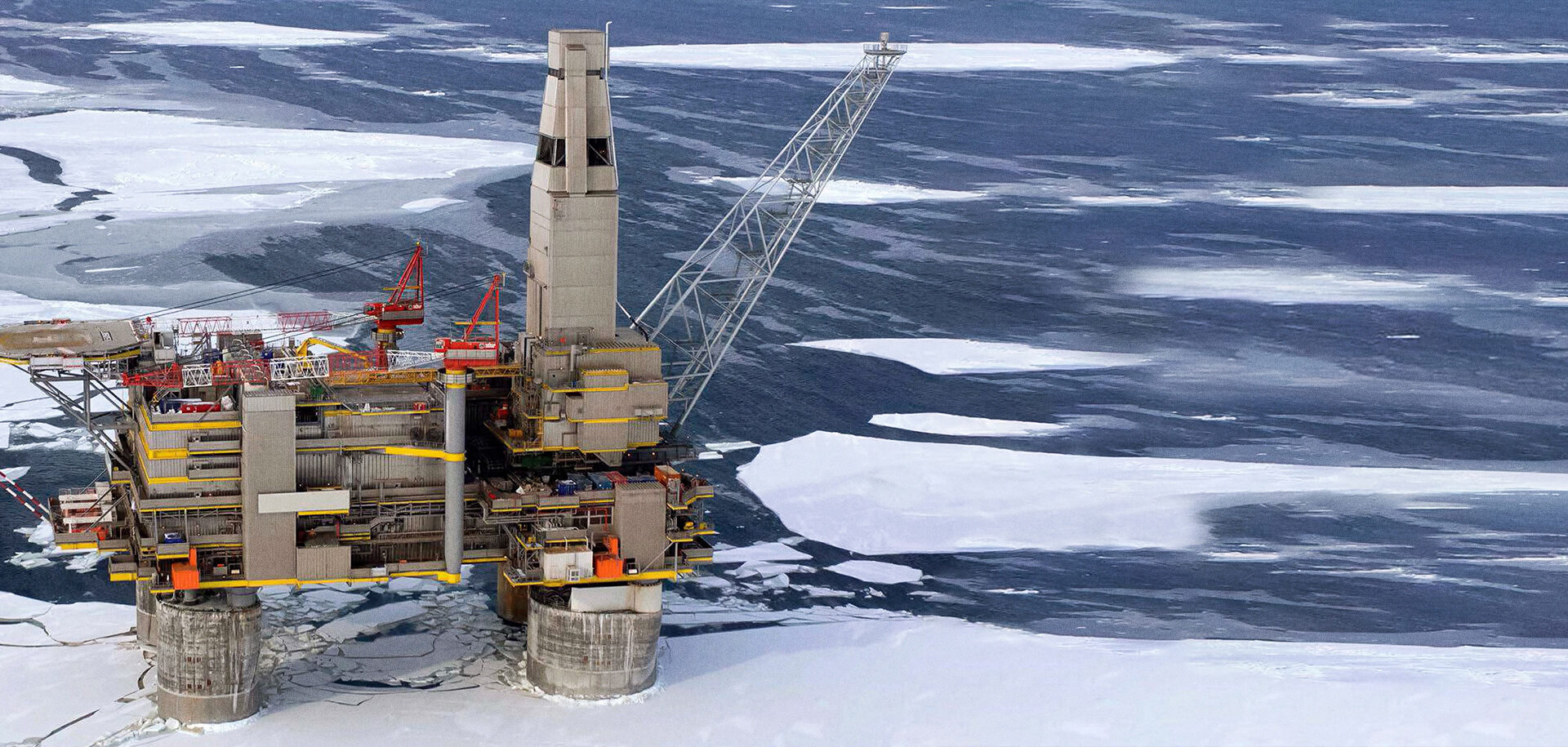
The SKF Generalized Bearing Life Model for hybrid bearings
Recently, SKF introduced the Generalized Bearing Life Model (GBLM) concept for rolling bearings [1]. Since then, work has continued focusing on bearings for specific applications and experimental validation of the model. One suitable application of this model is the rating life calculation of hybrid bearings. Hybrid bearings are bearings with rings made of steel and rolling elements made of ceramic silicon nitride (Si3N4).
Hybrid bearings are used in tough application conditions, e.g., poor lubrication and/or high contamination levels [2], [3]. Because of the higher stiffness of the ceramic material the Hertzian contact area is slightly smaller in a hybrid bearing, leading to higher contact pressure and subsurface stress compared with an all-steel bearing of equivalent geometry. In principle this should cause a reduction of the fatigue life of the bearing. However, it has been observed that in typical applications hybrid bearings last longer. How to explain this odd behaviour? How to model it? This article addresses these questions and also shows that the GBLM can model and explain well the observations in the field. SKF GBLM for hybrid bearings is now being released.
Hybrid bearings have rings made of bearing steel and rolling elements made of bearing grade silicon nitride (Si3N4) (fig. 1). Silicon nitride is a ceramic (i.e., non-metallic) material characterized by high hardness, high modulus of elasticity, high temperature capability and chemical resistance, low density and poor conductivity and ductility. Because the silicon nitride ceramic material is such an excellent electrical insulator, hybrid bearings can be used to effectively insulate the housing from the shaft in both AC and DC motors as well as in electrical generators. Hybrid bearings perform well under poor lubrication and solid contamination conditions compared with all-steel bearings, even though under equal load (due to higher stiffness of ceramic rolling elements) the contact stresses are higher.
In addition, hybrid bearings have higher speed capabilities and provide in most cases much longer bearing service life under the same operating conditions than same-sized all-steel bearings. Hybrid bearings also perform extremely well under high accelerations, vibrating or oscillating conditions. For high-speed applications such as machine-tool spindles and turbochargers, special bearing geometry, materials and lubrication systems might be required. The expectation is that this trend will continue, and many other modern industrial applications will discover and take advantage of the unique capabilities offered by hybrid bearings.
The use of ceramics as bearing material was first proposed in the 1960s for extreme temperature bearings for aero and space applications. By means of component rolling contact fatigue testing, it was established that fully dense hot-pressed silicon nitride has the best rolling contact fatigue (RCF) characteristics when compared with other ceramic materials. Significant variations in fatigue performance were also experienced from seemingly identical production batches of silicon nitride balls. In the 1980s Lorösch et al. (1980) [4] performed fatigue life testing of hybrid angular contact ball bearings. Using the best available quality of silicon nitride balls, they found that hybrid bearing RCF resistance is comparable to one of the all-steel bearings tested under the same load – despite the 12 % increase in contact pressure experienced in the hybrid bearings. However, an additional test of a second batch of silicon nitride balls produced poor fatigue life, indicating the criticality of the quality of the ceramic balls in achieving good fatigue life performance.
Over the years the quality and reliability of ceramic rolling elements have substantially increased. The introduction of non-destructive evaluation (NDE) methods combined with the continuous progress in silicon nitride material purity and sintering technology finally allowed engineers to develop reliable and consistent RCF performance of silicon nitride balls, Galbato et al. (1992) [5]. Because of this, the 1990s saw significant growth in the use of hybrid bearings in high-speed machine tool spindles with significant benefits for the speed capability and precision of these mechanical components, Cundill (1993) [6]. Fig. 2 shows the progress of ceramic fatigue strength, Cundill (1990) [7], attributed to the improved hot-pressing hardening and cleanliness for porosity and surface defects throughout the whole manufacturing process (which could now be controlled by NDE).
Objective of the present work
From the review of hybrid bearing development, it is found that the fatigue strength of bearing grade silicon nitride has made tremendous strides during the past 20 years. RCF performance of silicon nitride balls has risen by two orders of magnitude since the early 1980s. Fatigue life testing of hybrid bearings also shows unequivocally that the ceramic rolling element is the most reliable component in a bearing system. Nevertheless, the impact of the 12 % increase in contact pressure present in hybrid bearings is a characteristic that can be observed under running conditions where subsurface contact fatigue is the predominant damage mechanism dominating the performance of the bearing. Fig. 3a shows the Weibull probability plot of the endurance tests performed by Forster et al. [8] of hybrid and all-steel bearings tested under the same test conditions. The plot shows that under heavy load and favourable lubrication conditions, subsurface fatigue dominates the bearing fatigue performance. Therefore, hybrid bearings that are subjected to a high contact pressure (3.5 GPa) generate a higher failure probability for a given running time, compared with the all-steel base line variant that was running at a pressure of 3.1 GPa. (Note: this is achieved with a weak statistical significance, given the extent of overlapping of the 90 % confidence bar as shown in the Weibull plot of fig. 3a).
Fig. 3b shows the Weibull probability plot of the endurance tests performed by Chiu et al. [9] comparing hybrid and all-steel bearings under the same test conditions. The test was performed at a lighter load, giving rise to a maximum Hertzian contact pressure of 2.6 GPa for the hybrid and 2.3 GPa for the all-steel variant. The test was performed under challenging environmental conditions: high temperature, thin film and raceways run-in with oil contaminated with environmental particles to simulate the actual lubrication condition of the application.
Generalized modelling approach
A generalized life equation was established in [1], with separate terms for the surface and subsurface (fig. 4). Notice that the life L of the bearing in number of revolutions can be related to the number of load cycles N by the relation L=N/u , where u is the number of the load cycles taking place at each revolution.
In bearing life ratings, a standardized slope of the Weibull statistics is adopted, we can set e. L10 is the 10 % bearing life which implies 90 % of bearing survival S=0.9, and the life equation can be written as equation (1):
Equation (1) represents the basis of a generalized bearing life model that explicitly separates the surface damage accumulation from the subsurface fatigue. The subsurface term of equation (1), represented by the volume integral, can be solved using established rolling contact fatigue methods as explained in reference [1]. However, the surface term given by the area integral of equation (1) must be quantified in a radically different manner. Its assessment requires the estimation of the damage originated by the actual stress conditions of the raceway surface under a variety of operating conditions that may occur to the bearing.
This task is complex, but it offers the possibility to consistently consider, in the rating life estimation of hybrid bearings, the tribological phenomena that characterize the performance and endurance characteristics of the ceramic-steel raceway contact as described in [2].
Surface survival of ceramic-steel interface
Equation (1) can be rewritten in a form that clearly indicates the separation between the contribution of the raceway surface to the life of the bearing: equation (2).
For a given bearing size and excluding constant terms, the surface fatigue damage of equation (2) is a direct function of the combined effects of the stress conditions experienced by the raceway surface during the over-rolling of the rolling contact: equation (3).
The assessment of the surface damage integral (3) can be accomplished by integrating the surface originated stresses of the raceway resulting from a variety of operating conditions of the bearing.
In the current formulation, surface stressing and damage accumulation can be treated using advanced surface distress modelling for elastohydrodynamic lubricated rolling-sliding rough contacts, i.e., micro-EHL models, Morales-Espejel et al. [10]. This approach can also handle boundary lubrication conditions and the presence of dents and requires the use of 3D area samples of the raceway roughness (including indentation microgeometry) (fig. 5).
The use of advanced surface stress analyses based on Micro-EHL can be time-consuming and impractical for general bearing rating life calculations. Therefore, a parametric study was carried out to derive a simplified analytical equation to allow fast estimation of the surface fatigue damage of hybrid bearings for given operating conditions of the bearing application. For this parametric study several surface topographies were collected using 3D optical interferometry measurements of the bearing raceway (fig. 5).
For this work some 100 raceway samples of deep groove, angular contact and radial roller hybrid bearings were collected. The sampling included bearing raceways that were run-in under different environmental conditions, i.e., clean and contaminated lubrication conditions.
From the collected surface micro-geometries, several numerical simulations of hybrid contacts surface fatigue stress integral were performed. The effect of lubricant contamination was included in the simulations by accounting for the presence of dent topographies and local surface tractions. In the numerical simulations, the lubrication conditions of the bearing were modelled by performing the transient Micro-EHL simulations of the rolling contact for different lubricant film thicknesses.
The numerical results of the parametric study of the surface stress integral to hybrid bearings indicated the possibility of representing this quantity using an analytical formulation. It was found that all numerical results could be approximated well by an exponential function. Essentially, this function depends on two main parameters – the relative load Pr = P/Pu of the rolling contact and the environmental lubrication factor of the bearing application, ηenv = ηlub ∙ ηcont , equation (4):
The c1⋯cn terms of equation (4) are dependent on the environmental condition of the application (ηenv), which can be directly obtained from the lubrication (ηlub) and contamination (ηcont) factors used in the bearing application.
Application of the model
The generalized bearing life model of equation (4) can be applied to represent the endurance test data of Forster [8] and Chiu [9] that have been discussed earlier.
The tests were performed on size 7208 angular contact ball bearings. A total of 40 hybrid bearings were tested, leading to 12 failures. For the all-steel variant 32 bearings were endurance tested, leading to 21 failures. Geometrical details of the test sample and related loading and stress conditions used in the endurance tests are shown in Table 1.
A major difference between the two tests is related to the loading conditions and lubrication environment in which the tests were conducted. In the case of the Forster endurance tests, the load was heavier, leading to a Hertzian contact pressure of 3.5 GPa for the hybrid bearing variant. The oil circulation system was provided with good filtration. Furthermore, the lubrication conditions were good with a kappa value of around 2.5. The GBLM environmental factor resulting from the given lubrication conditions is then ηenv=0.85. This gives rise to a low value in the index of surface stress. Indeed, under the given operating conditions, subsurface fatigue controls the performance of the rolling contact. Therefore, the Forster test operating conditions are of advantage to the 7208 all-steel bearing variant, which operates at a lower Hertzian stress of 3.1 GPa and thus will generate lower fatigue damage per over-rolling cycle.
In case of Chiu’s endurance testing, the applied load was significantly lower, leading to a maximum Hertzian stress of 2.6 GPa for the hybrid bearing variant. The running temperature of the tests was higher (150 oC), providing less favourable lubricating conditions for the bearing. Furthermore, the tests were conducted with induced raceway defects to reproduce the typical contamination conditions encountered in many bearing applications. This was achieved by running-in the bearings for 15 minutes in oil containing 2.5 ppm aluminium oxide particles of 20 µm size. The resulting GBLM environmental factor that characterizes the given operating conditions is, in this case, low, i.e., ηenv=0.035.
In the case of Chiu’s endurance testing, with the given loading and environmental conditions, the role of the surface fatigue strength dominates the survival of the bearing. In other words, there is a high index of surface stress so surface fatigue will control the fatigue performance of the bearing. The surface stress index specifically developed for hybrid bearings will play here in favour of the fatigue performance of hybrid bearings, compensating for the higher Hertzian stress (2.6 GPa) present in the ceramic-steel contact.
The running conditions discussed above of the hybrid bearing endurance testing were introduced into in an ad hoc bearing life computation code with the implementation of the generalized bearing life model according to equation (4). The life performance of the 7208 bearing, all-steel variant was also computed using an equivalent version of the GBLM as discussed in Morales-Espejel [1]. The results of the calculated 10 % fatigue life corresponding to the different test and bearing variants are presented in the Weibull plots of figs. 7a and 7b. The predicted endurance lives, in millions of revolutions, are shown in the plots with thin vertical lines labelled according to the corresponding bearing variant of the calculation.
The examination of the GBLM model results, related to the Forster’s test results, is presented in fig. 7a. The plot shows that predicted fatigue lives for the hybrid and all-steel variants are set at about the lower end of the 90 % confidence interval of the 10 % failure probability of the endurance test results. This means that the Forster endurance tests validate the GBLM model results with a high degree of statistical significance.
The model results related to Chiu’s endurance tests are presented in fig. 7b. In this case the prediction has a lower degree of statistical significance. This may be due to the low number of failures obtained for the hybrid variant and one early failure affecting the results of the all-steel test results. However, the GBLM bearing endurance results are all well below the experimental L10,50 and fully consistent with the experimental observations. Indeed, the model indicated the ability to represent well the significantly longer rolling contact fatigue life of the hybrid variant despite the higher contact pressure present in this bearing during the test.
Summary and conclusions
The substantial progress in the improvement in ceramics quality for rolling bearings has allowed hybrid bearings to become reliable and performing, especially in tough tribological conditions (poor lubrication and/or high contamination). Thus, bearing rating life for these kinds of bearings can now be reliably predicted. The SKF generalized bearing life model (GBLM) that allows for the separation of surface and subsurface survival has been applied to calculate the rating life of hybrid bearings. SKF has developed a model and a computer tool for this calculation. This model has been applied for demonstration purposes in two series of published endurance tests, which show counter-intuitive results. In one case (well-lubricated, clean and heavy load) the hybrid bearing shows lower performance than its counterpart all-steel bearings, while in the other case (lighter loaded but poorly lubricated and more contaminated) the hybrid bearing shows superior performance. Only GBLM, a model that can separate surface and subsurface survival, can reproduce these results.
The following conclusions can be summarized:
- The estimation of the rolling contact fatigue of hybrid bearings requires the accounting of the subsurface fatigue, which is less favourable for hybrid bearings, and the surface fatigue, which is substantially more favourable for hybrid bearings.
- By separating surface and subsurface survival, SKF GBLM can balance the two fatigue-damaging mechanisms and provide a good description of the RCF behaviour of hybrid bearings.
- SKF has developed and implemented in computer tools the SKF GBLM rating life calculation for hybrid bearings. Thus, customers can now take full advantage of the application of hybrid bearings.