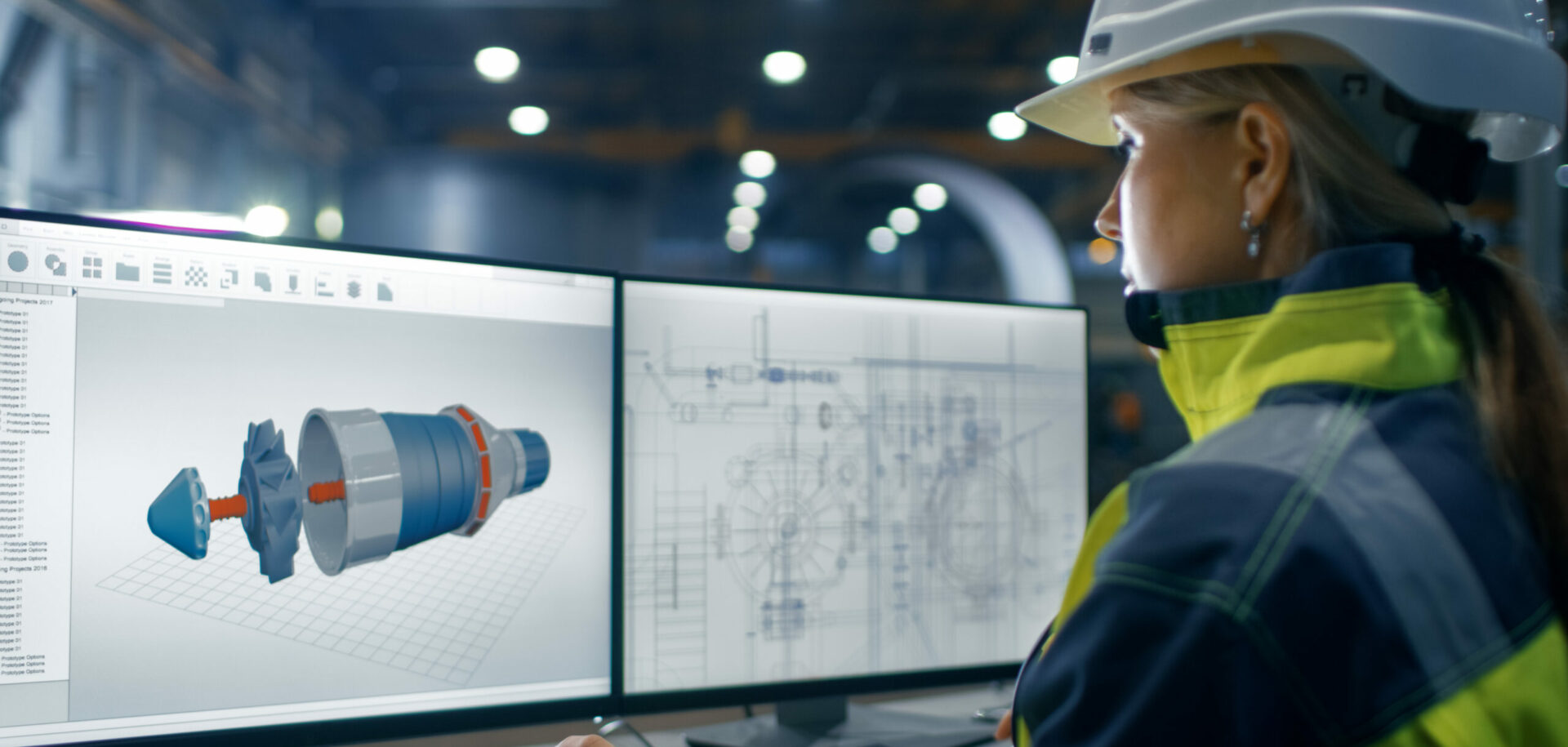
Summary
Submerged propulsion technology
In any propulsion system with spinning parts, bearings play an integral role. With a submerged Azipod unit, however, there is the difficulty of a harsh, salty and sometimes icy environment.
An Azipod typically has three bearing positions: a slewing bearing, making it possible to turn the whole pod; a cylindrical roller bearing or a CARB® toroidal roller bearing, acting as a non-locating bearing; and an axial thrust bearing unit. The last function includes two spherical roller thrust bearings, holding the propeller shaft, or rotor, in place.
SKF has worked with ABB Azipod since 2000. Already, SKF supplies a tailor-made solution to the Azipod compact units that includes two axial thrust bearings, complete with housing and insulation on the thrust end. SKF also supplies the cylindrical roller bearing on the propeller end of the shaft.
On the bigger Azipod units, from 5MW up to 38MW, SKF’s CARB bearings have become the industry standard. The reason for this is that the heat from the electrical motor inside the Azipod can create an elongation of the propeller shaft of 5 to 10 mm.
A CARB bearing permits axial movement of the shaft internally in the bearing as well as angular misalignment caused by shaft deflections or coaxiality between the two rotor bearing positions. ABB is currently installing such bearings on large Azipod units.
Something new is propelling ships to their destinations. It’s a pod that hangs off the ship and allows it greater manoeuvrability, while at the same time saving space and fuel.Of all the interconnected systems on a ship, the system that actually propels it from point A to B is probably the most vital. But there are many ways to push, or pull, a ship through the water.
In the early 1990s, ABB and Kvaerner Masa-Yards in Finland jointly developed a revolutionary new propulsion system known as the Azipod. The unit, which contains an electric motor, a shaft and a propeller, hangs like a pod off the underside of a ship’s hull. It swivels 360 degrees, eliminating the need for rudders.
The Azipod offers many advantages over a standard propeller and shaft set-up. These include better manoeuvrability, space and fuel savings, and less environmental impact. Today, Azipod is a registered trademark manufactured and marketed exclusively by ABB Azipod, a division of ABB Marine.
“We see it as a young product,” says Jari Ylitalo, manager of ABB Azipod Oy’s compact division. Based on the success of the bigger units, since January 2000 the compact division has been making smaller and more modular Azipod propulsion systems. Compact Azipods are designed for a power range of between 400 kilowatts and five megawatts. Larger units go up to 38 megawatts. “In the past 10 years, the product has come to market and proven itself,” says Ylitalo.
Adapting to habitat
In many ways, the development of the Azipod in Finland mirrors the development of Nokia, although Azipod is only a household name to ship’s captains and shipbuilders. Just as the Finns used the vast distances of their country and its sparse population to develop mobile telephony, they used their ice-clogged waterways to develop the Azipod.
“Our roots are in the development of icebreakers,” continues Ylitalo. “The key issue for an icebreaker is to be able to manoeuvre out of a channel, where the ice is often thickest, to allow a boat to pass. With an azimuthing electric thruster, it can achieve that. But ice is a difficult environment, and the loads on the system are much higher than in open water.”
The system is not only for new vessels. One of the first ships to be retrofitted with an Azipod was the M/T Uikku, a 16,000-tonne product tanker built in Germany in 1978. After its retrofit in 1993, this ice class 1A ship became the first Western vessel to navigate through the ice-infested Northeast Sea route from Murmansk to Provideniya in eastern Siberia.
According to Ylitalo, the Azipod system was the only way to make the sailing economically viable, as the M/T Uikku could operate safely without icebreaker assistance.
Getting wind of Azipod’s excellent performance on tankers, service vessels and icebreakers, in 1995 Carnival Cruise Lines retrofitted two of its cruise ships, the M/S Elation and the M/S Paradise. The positive results paved the way for making the Azipod propulsion system standard on most new cruise ship projects.
On the M/S Elation, the installation of two 14-megawatt Azipod units freed up 1,200 square metres of internal space that was previously occupied by diesel engines and propeller shafts. The free space was used to install additional waste-handling equipment. Additionally, the redundant shaft tunnels were used to increase the fresh-water tank facility.
On the manoeuvring front, the M/S Elation gained a drastically reduced turning circle diameter, full controllability when the ship was moving astern and shorter stopping distances. In addition, the ship was the first merchant vessel ever to have its propellers facing forward, pulling the ship through the water. This configuration dramatically improved the ship’s manoeuvrability.
As a rule of thumb, ships that need high thrust at low speeds would choose a pushing Azipod. And rather counterintuitively, ships that need speed will go for a pulling set-up. Either way, the Azipod offers unparalleled manoeuvring possibilities, especially in tight channels and ports.
But the Azipod has other benefits as well. Besides eliminating the need for two long propeller shafts, with the Azipod the ship can also do away with stern thrusters and rudders. And the Azipod units make a ship quieter, virtually free of vibration, even at 23 knots, because the main propulsion motor is outside the machinery spaces and submerged in water.
“In other words, ice cubes don’t shake around in the cocktail glasses when the ship picks up speed,” says Ylitalo.
Fuel efficiency
Carnival Cruise Lines’ M/S Elation discovered something else during the sea trials after the retrofit. Compared to her sister ships – same hull, traditional propulsion – the Azipod used 10 percent less fuel.
There is an environmental corollary to this. A normal shaft-and-propeller driven ship accelerates by injecting more fuel into the huge diesels. Until the heavy, slow-moving engines have managed to reach the desired speed, unburned fuel is passing through the system. This is what often leads ships to belch out black clouds of soot from their funnels.
Here, a diesel-electric system such as the Azipod unit has a clear advantage. The propellers are driven by electric motors, with diesels providing the electric power via generators. The diesels operate at a constant speed, eliminating the wasteful excess of fuel needed for acceleration. The speed of the electric motors, and the ship, is regulated through transformers and frequency converters.
Since the diesels run constantly at an optimised rpm, no fuel is wasted during acceleration and – no black smoke.
Carnival Cruise Lines currently has four Azipod-powered ships in service, with an additional
10 ships scheduled for delivery in 2005. Royal Caribbean International, another leading cruise operator, launched the biggest cruise ship in the world in autumn 2000 and equipped it with Azipod units. The Voyager of the Seas has two 14-megawatt Azipods with one stationary 14-megawatt Fixipod in between them. Currently some 40 ships in the world are propelled by Azipods.
“The Voyager of the Seas is extremely easy to handle,” says Harri Kulovaara, senior vice president of Royal Caribbean International. “It achieves 25 knots forward, 17 knots astern and
3 knots sideways, which is extraordinary performance.”
Alexander Farnsworth
a feature writer based in Stockholm,
photos Alexander Farnsworth and ABB