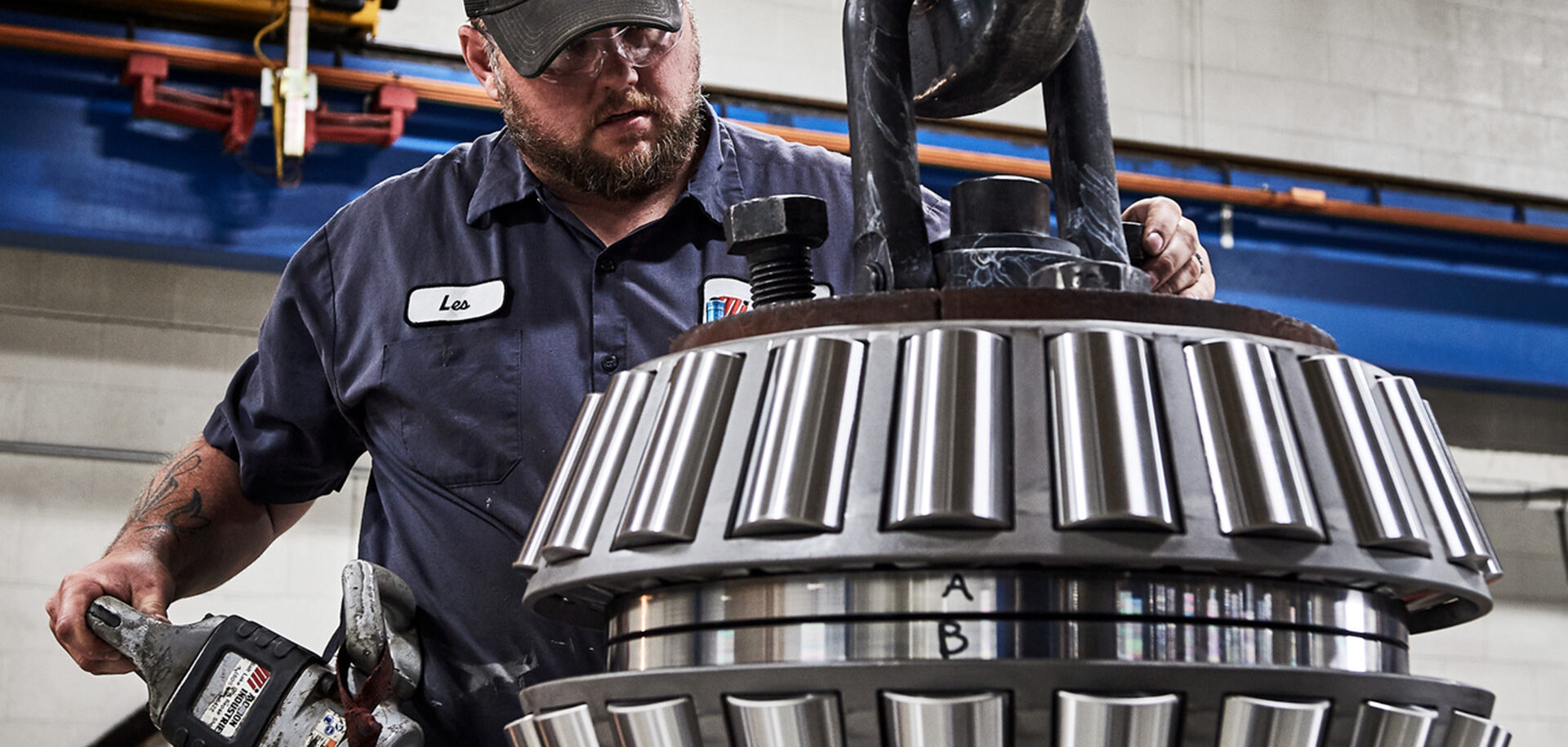
Understanding vertical shaft mounting for bearings
When mounting bearings, one of the most common procedures is to use a vertical shaft mounting position and work with heat. Considering all common mounting methods, as many as one in six bearings may fail because of inadvertent damage sustained during mounting. Commonly used as is, the vertical shaft procedure presents some lesser-known risks. This article discusses potential problems and how to overcome them.
It is important that mounting after heating is accomplished rapidly to avoid temperature losses that may cause the component to become stuck in the wrong position or cause other damage.
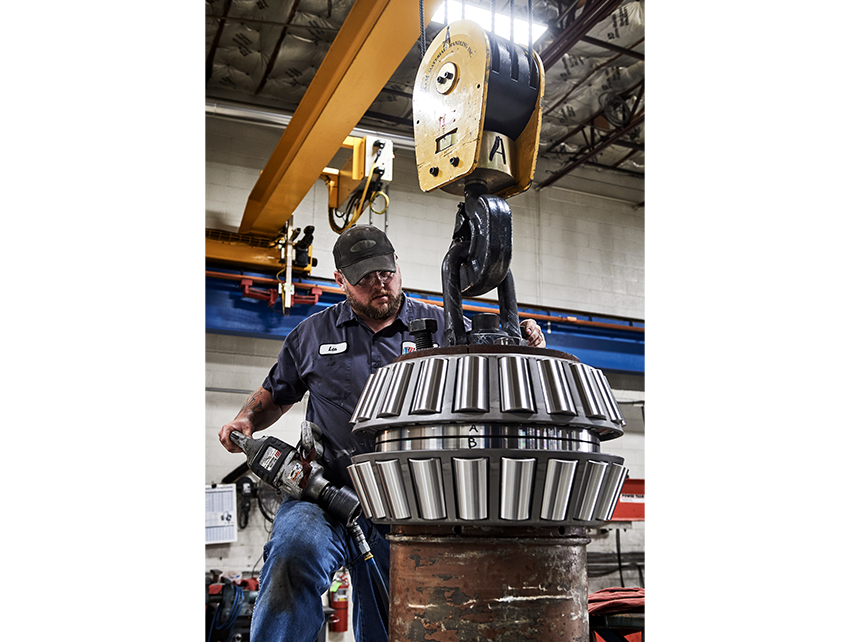
Options for heating and mounting
There are a number of different options for the mounting procedure using heat. Common ones include:
- warm bearing fitted on a room-temperature shaft seat;
- room-temperature shaft placed in a warm bearing;
- room-temperature bearing placed in a warm housing; and
- warm housing fitted on a room-temperature shaft-mounted bearing.
However, bearings behave differently than other components during vertical mounting. All the options will initiate an increase in clearance in the bearing followed by a decrease during the various heating and cooling cycles. Bearings have a relationship between the axial and the radial clearance that is defined by the contact angle. In double-row bearings this is given by the equation:
∆ a = 2.3 x Yo x ∆ r (∆ a is typically 5 – 15 times the radial clearance).
So a small radial movement (i.e., a change of clearance) results in a large axial movement.
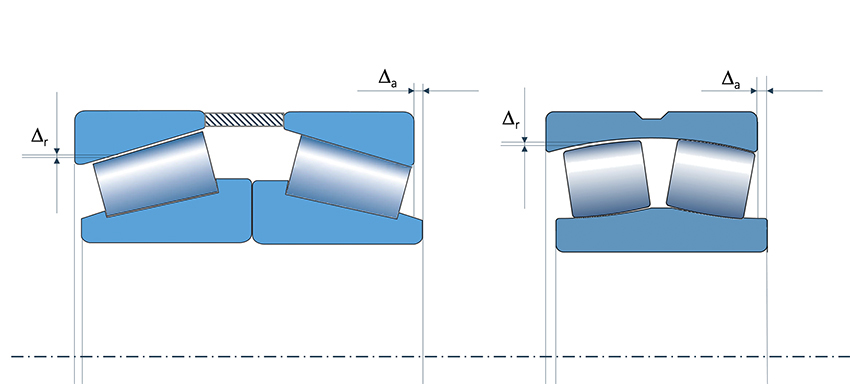
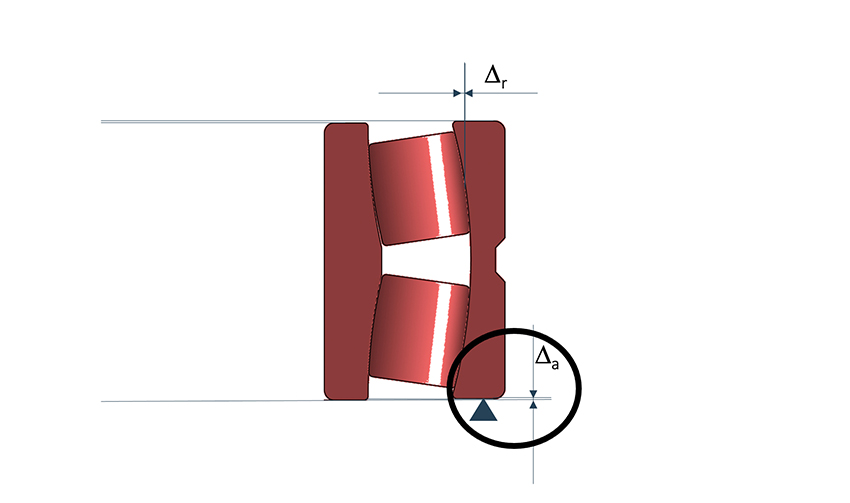
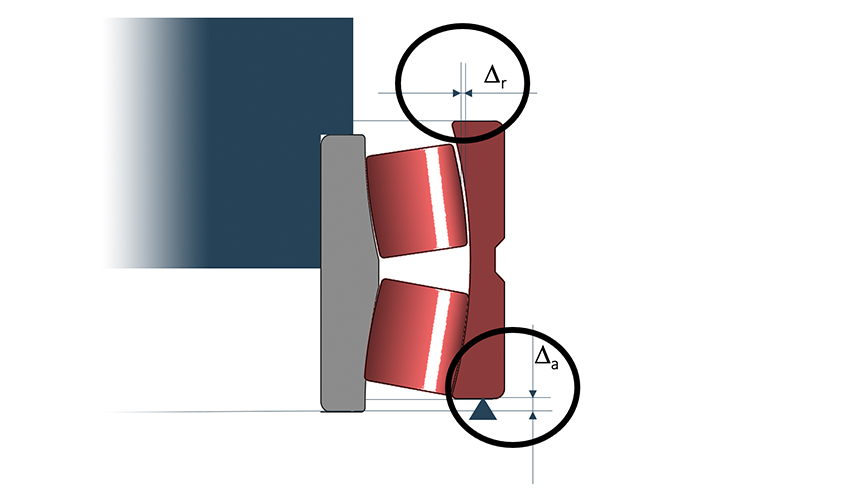

Firstly, we have to consider the movements and forces inside the bearing (fig. 6).
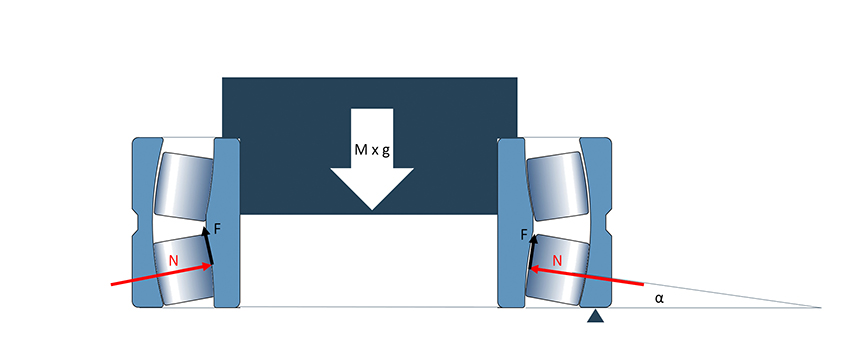
There is also a contact angle, α and a number of rollers, Z. Using the equation:
N=(M x g)/Z(sin(α)+µ x cos(α)) we see that friction reduces the roller load.
However, in the second sequence, when the inner ring moves upwards, the vertical load (M x g) is now carried by the lower row. Hence the equation becomes N=(M x g)/Z(sin(α)-µ x cos(α)) and the friction is reversed (fig. 7). If sin(α) = µ x cos(α), the upwards motion will create very large roller loads, and the practical consequence is a risk of self-locking or smearing.
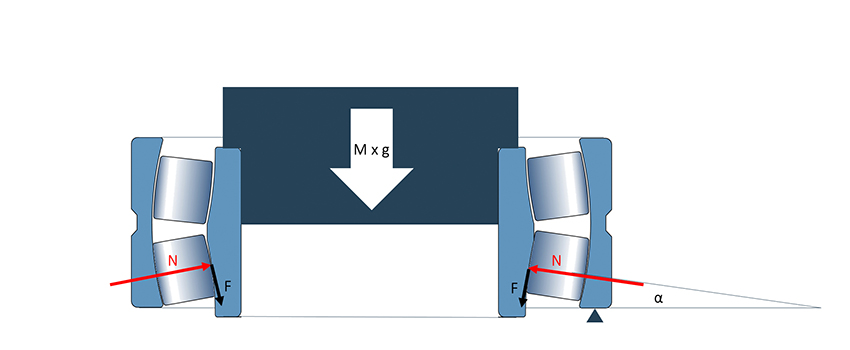
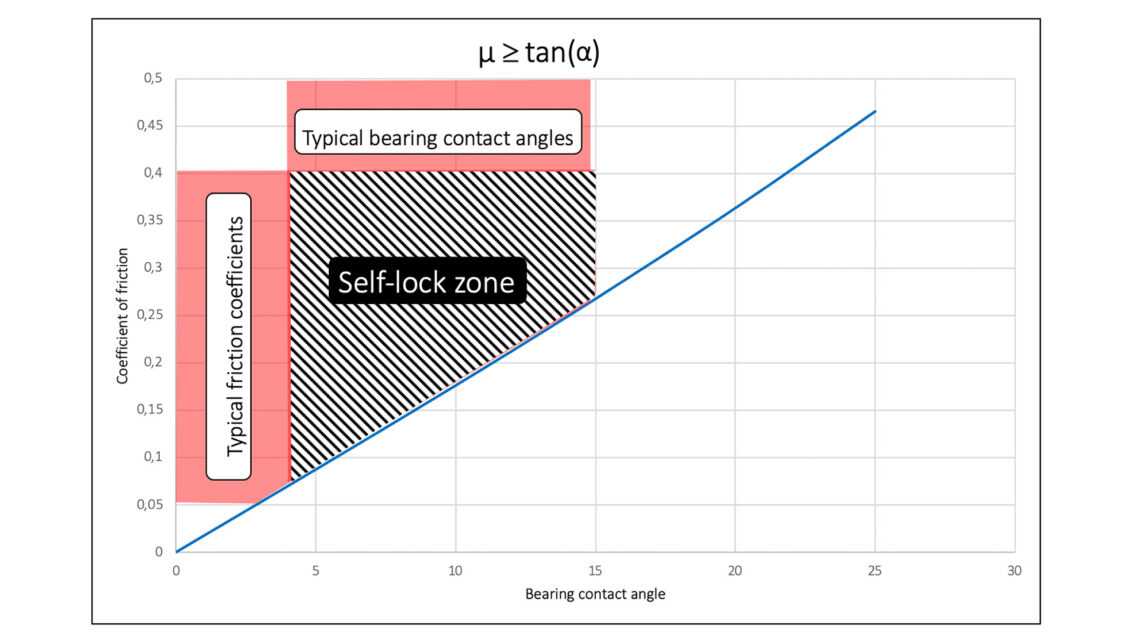
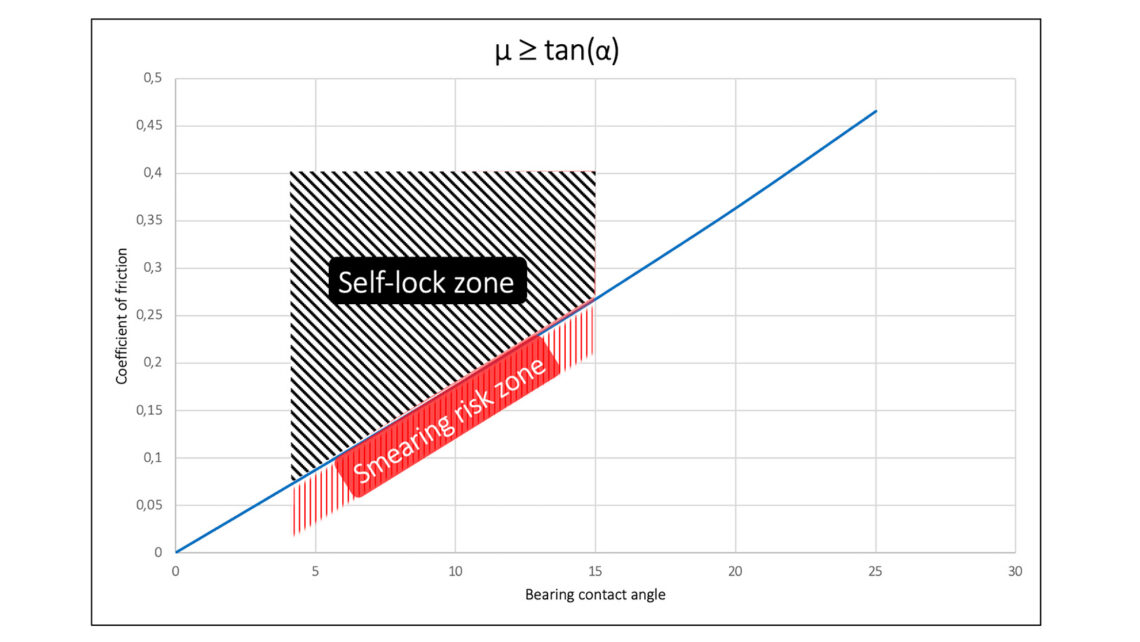
Practical outcomes
From this, two potentially harmful outcomes have been identified for both self-locking and “almost self-locking”, which are often seen in machines but rarely considered as directly related to mounting procedures. Fig. 10 shows some of the common damages to bearings.
Measurements are taken during the first hour of temperature equalization (fig. 11).
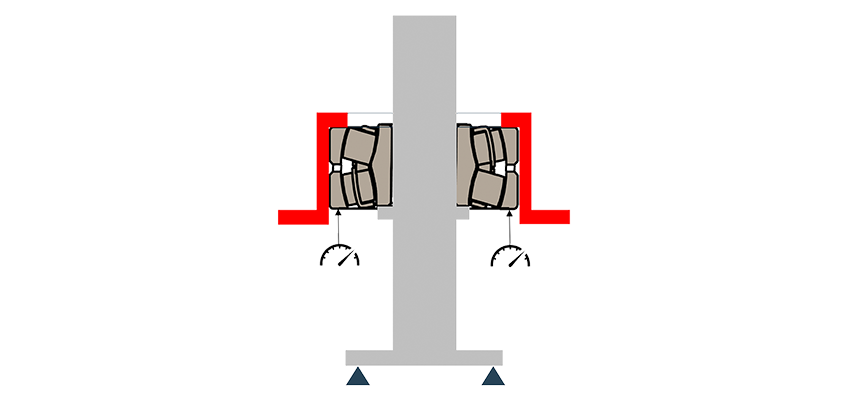
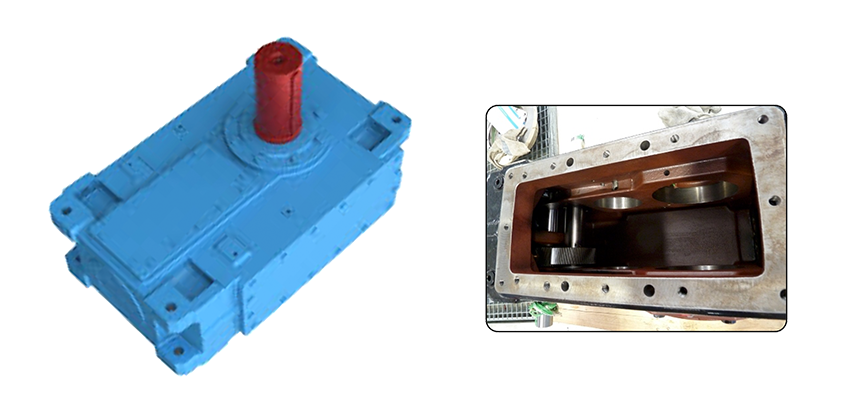
Measurements were taken during the first 90 minutes of temperature equalization. A dummy housing was used to facilitate the measurements (fig. 14).
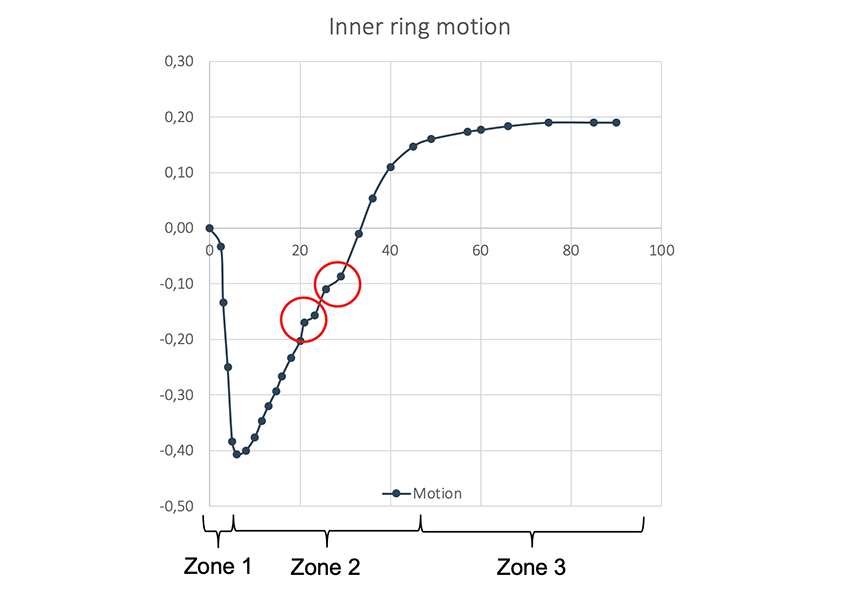
In this case, the appearance of the lower inner ring raceway in the test bearing was studied after dismounting the test bearing. Thin axially oriented marks were visible.
However, not all roller contacts left such marks. Under the microscope, the thin axially oriented marks showed to partially consist of smeared material.
This damage will copy due to the overrolling and develop into surface distress/wear.
To avoid mounting-initiated damages there are three factors to work on. Firstly, it is important to reduce or eliminate the bearing load during the mounting sequence. The logical path is to avoid vertical mounting and/or to counteract gravity. If this is not possible, mount vertically, but then tilt horizontally to reduce the axial loading during cooling. Try to release friction by rotating to release and avoid motion by centring axially during cooling. Above all, awareness is key, as being aware of the potential damage during mounting helps reduce risk.
SKF has considerable strengths in bearing mounting, and its BearingAssist app can help with mounting issues. SKF can also support with training fitters on best practice as well as help to review machine design and bearing mounting procedures for all types of equipment.