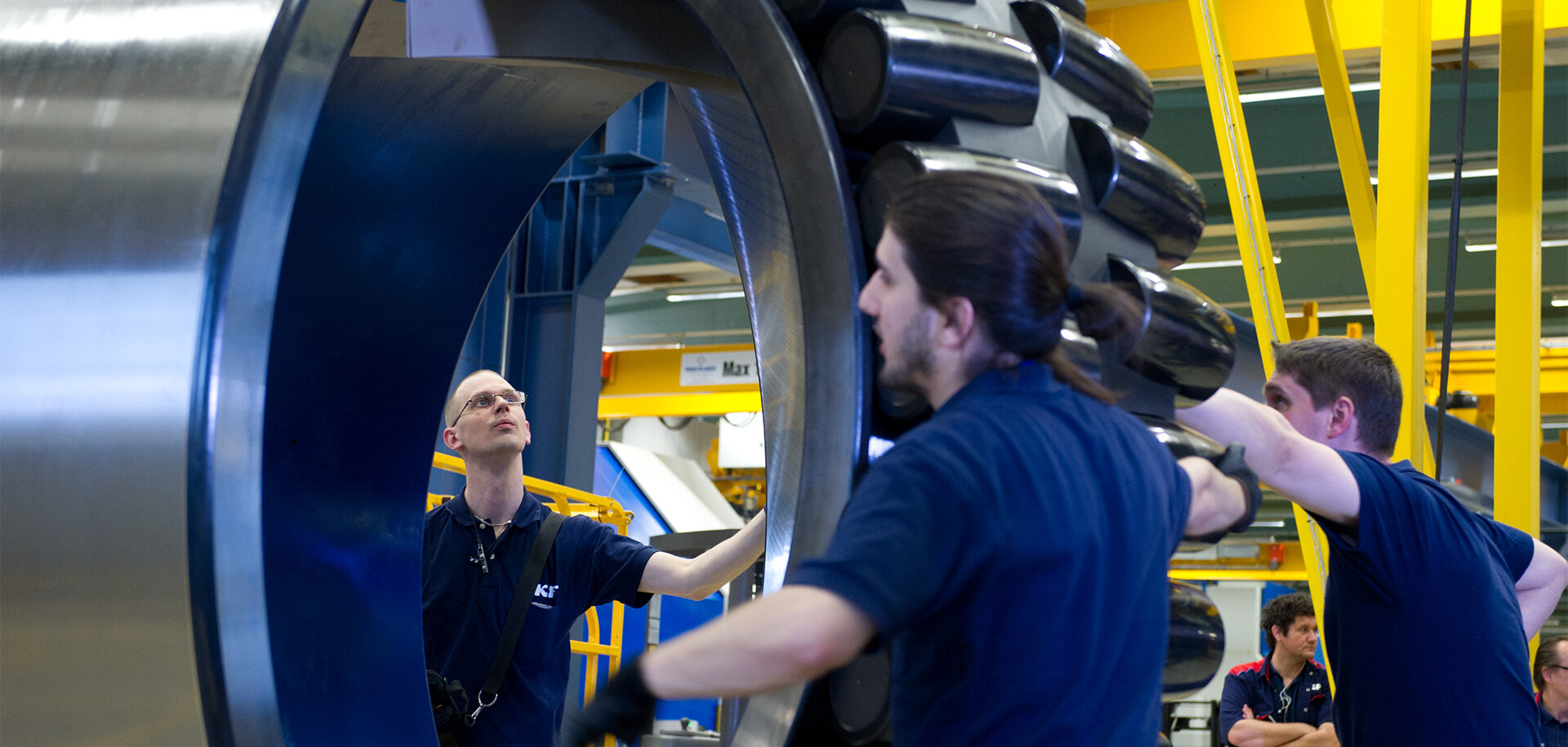
Beschichtungen zur Steigerung der Lagerleistung
Beschichtungen verlängern die Lebensdauer und steigern die Leistung von Wälz- und Gleitlagern. Sie sind für eine Vielzahl von Betriebsbedingungen geeignet und erfüllen unterschiedliche anwendungsspezifische Leistungsanforderungen. Das Angebot von SKF umfasst derzeit mehr als 35 verschiedene Spezialbeschichtungen.
Heutzutage wird erwartet, dass ein Wälzlager nahezu unbegrenzt betrieben werden kann, sofern drei Bedingungen erfüllt sind: 1. die jeweilige Beanspruchung bleibt unter einem bestimmten Wert, 2. die Schmierung ist ausreichend und 3. es gibt keine Verschmutzung. Natürlich ist eine Anwendung manchmal alles andere als optimal, und es können unerwartete Probleme auftreten, die eventuell höhere Betriebs- und Wartungskosten nach sich ziehen.
Um die Lebensdauer und die Leistung eines Lagers bei nicht idealen Bedingungen zu optimieren, wurden verschiedene Strategien entwickelt. Eine davon ist das Aufbringen von Beschichtungen, die eine Vielzahl von Eigenschaften verleihen können, wie zum Beispiel:
- Verschleißfestigkeit
- erhöhte oder verminderte Reibung
- Korrosionsbeständigkeit
- Gleitverhalten und Notlaufeigenschaften
- verbesserte Schmierung oder geringerer Schmierbedarf während der Betriebszeiten
- bessere Benetzung durch den Schmierstoff
- elektrische Isolation
- Wasserstoffbarriere
- Schutz vor Passungsrost
- Verbesserung des optischen Erscheinungsbilds.
Durch das Beschichten eines Standardlagerstahls mit Materialien, die die gewünschten Merkmale aufweisen, kann die Leistung des ganzen Lagers erheblich gesteigert werden. Beschichtete Lager können auch dazu dienen, die Lücke zwischen Lagern aus Standardlagerstahl und keramischen Hybridlagern zu schließen. Keramische Wälzkörper stellen für manche Anwendungen eine gute Lösung dar, allerdings sind sie teuer und teilweise nicht im Handel erhältlich. In solchen Fällen können Standardlager durch das Aufbringen von Beschichtungen auf das richtige Anforderungsniveau gebracht werden.
Manche Beschichtungen werden sehr dünn aufgetragen; dies kann sehr vorteilhaft sein. Durch die Verwendung von nur wenigen Mikrometer dünnen Beschichtungen können Standardlager aus der Produktion verwendet werden, ohne dass die Bearbeitungseinstellungen aufwändig geändert werden müssen.
Überblick über die Beschichtungsverfahren
Bei SKF kommen verschiedene Beschichtungsverfahren zum Einsatz (siehe Bild 1). Diese können in drei Hauptkategorien unterteilt werden:
- Verfahren im gasförmigen Zustand, bei denen das Beschichtungsmaterial eine gas- oder dampfförmige Phase durchläuft, bevor es auf der Oberfläche abgeschieden wird. Hierzu zählen Vakuumbeschichtungsverfahren wie die physikalische Gasphasenabscheidung (PVD) und die plasmaunterstützte chemische Gasphasenabscheidung (PACVD).
- Verfahren im gelösten Zustand, bei denen das Beschichtungsmaterial in einer flüssigen Phase vorliegt, bevor es als Feststoff auf die Oberfläche abgeschieden wird. Die Verfahren lassen sich in folgende Kategorien einteilen: die chemische Abscheidung (z. B. stromlose Abscheidung, chemische Umwandlung, homogene chemische Reaktionen sowie Tauchen und Flüssigkeitsspritzen) und die elektrochemische Abscheidung, wie die galvanische Abscheidung einer metallischen Beschichtung auf einer Elektrode durch einen Elektrolyseprozess.
- Verfahren im geschmolzenen Zustand, bei denen der Beschichtungswerkstoff geschmolzen oder halbgeschmolzen (erweicht) wird, bevor er mittels einer starken Energiequelle als Feststoff auf die Oberfläche aufgebracht wird. Die jeweiligen Verfahren werden unterteilt in das Spritzbeschichten – hierbei wird Material mit sehr unterschiedlichen Techniken in einem heißen gasförmigen Medium schnell erhitzt und gleichzeitig mit hoher Geschwindigkeit zwecks Erzeugung einer Beschichtung auf eine Oberfläche aufgebracht – und das Laserbeschichten.
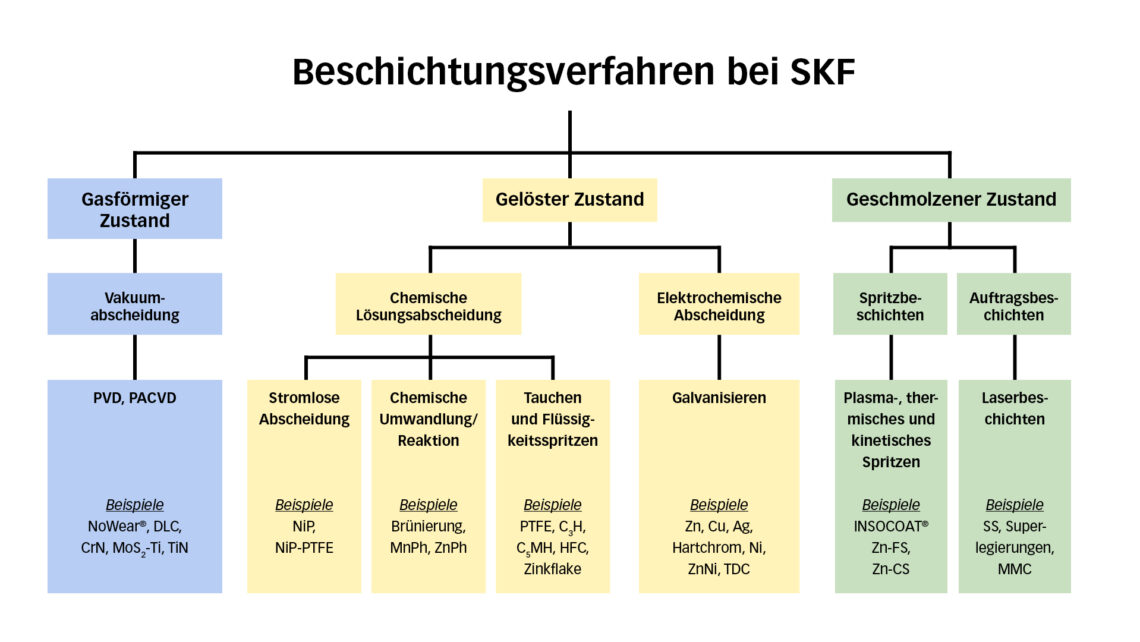
Beschichtungen bei SKF
SKF bietet mehr als 35 verschiedene moderne Beschichtungen, die für eine Vielzahl von Anwendungen oder unterschiedliche Teile der Lager verwendet werden können. Alle Beschichtungen wurden im Hinblick auf die spezifischen Anforderungen von Lagern optimiert, basieren auf genauen Spezifikationen und unterliegen einer strengen Qualitätskontrolle. Sie werden in hochmodernen Beschichtungsanlagen hergestellt, die oft weit über die üblichen Beschichtungs- und Ausrüstungsstandards hinausgehen und ein Höchstmaß an Qualität, Zuverlässigkeit und Wiederholbarkeit bieten.
Manche Beschichtungen werden in sehr dünnen Schichten aufgebracht, was einen großen Vorteil darstellt.
In diesem Artikel werden einige der am häufigsten verwendeten SKF Beschichtungen vorgestellt. Die vollständige Liste der SKF Beschichtungen wurde kürzlich zusammen mit den jeweiligen physikalischen und tribologischen Eigenschaften und sämtlichen Anwendungen im Online-Katalog SKF Coatings veröffentlicht.
Wälzlager
Bild 2 zeigt 12 Hauptbeschichtungsarten, die fünf wichtige Funktionen bei Wälzlageranwendungen erfüllen: Schutz vor Gleitverschleiß bei Käfigen, elektrische Isolation, Schutz vor Passungsrost, Schutz vor Korrosion und Schutz vor Verschleiß der Lagerlaufbahnen.
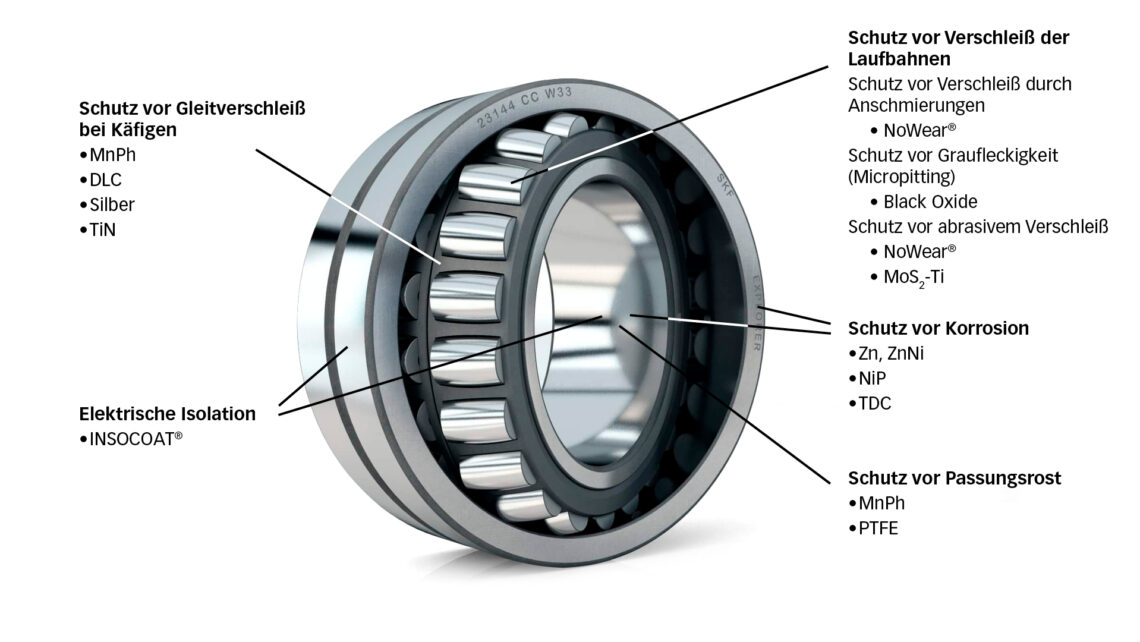
a) Schutz vor Verschleiß der Lagerlaufbahnen
Brünieren: Hierbei handelt es sich um eine Oberflächenbehandlung, die durch eine chemische Reaktion an der Oberfläche des Lagerstahls erfolgt, wobei sämtliche Komponenten der Lageroberfläche beschichtet werden. Die Teile werden in verschiedene alkalische wässrige Salzlösungen mit Temperaturen im Bereich von 140–150 °C getaucht. Durch die Reaktion zwischen dem Eisen der Stahllegierung und den Reagenzien entsteht eine etwa 1 μm dicke schwarze Schicht, die aus einer genau festgelegten Mischung von FeO, Fe2O3 und Fe3O4 besteht. Diese Beschichtungsart bietet viele Vorteile, wie zum Beispiel die Minimierung von Gleitverschleiß und adhäsivem Verschleiß. Außerdem verbessert sie das Einlaufen, da eine sehr glatte Oberfläche entsteht, die geringere stationäre Reibwerte als unbeschichtete Lager aufweist. Ein weiterer Vorteil ist die bessere Ölhaftung an der Oberfläche, die einen leichten Korrosionsschutz bietet. Die Brünierung bildet auch eine Barriere gegen Wasserstoff und schützt den darunter liegenden Stahl. Zudem erhöht die Brünierschicht die Widerstandsfähigkeit gegen Graufleckigkeit, Anschmieren, Ausbrüche, Passungsrost und die Bildung von Oberflächenrissen sowie die vorzeitige Lagerermüdung. Und schließlich schützt die Brünierschicht die Oberfläche vor schädlichen EP (Extreme Pressure)-Additiven, die häufig in Schmierstoffen für Windgetriebe verwendet werden.
NoWear: SKF war weltweit der erste Lagerhersteller, der kohlenstoffbasierte Beschichtungen bei Lagern einsetzte. Alle Komponenten der Lageroberfläche können auf diese Weise beschichtet werden, aber die besten Ergebnisse werden erzielt, wenn nur die Rollen beschichtet werden. Die Teile werden in einer Vakuumkammer einem PACVD-Verfahren unterzogen, bei dem durch Chemikalien und physikalische Reaktionen in Gegenwart eines Plasmas ein Gemisch aus Kohlenstoff- und Metalldampf entsteht, das bei Temperaturen unter 180 °C auf dem jeweiligen Teil kondensiert. Die daraus resultierende etwa 3 μm dicke, dunkelgraue amorphe Beschichtung, die sich durch eine mittlere Härte und sehr geringe Reibwerte auch im trockenen Zustand auszeichnet, ist für den Einsatz auf Lagerlaufbahnen bei hohen Kontaktdrücken optimiert. Das 1999 patentierte NoWear Verfahren reduziert Adhäsion, Anschmierungen, Oberflächenermüdung und Graufleckenbildung und sorgt für einen sehr geringen Verschleiß bei Mangelschmierung. Zudem besteht die mehrschichtige Beschichtung aus einer speziellen unteren Schicht zur Verbesserung der Adhäsion und einer graphitischen Deckschicht, die für ein optimiertes Einlaufen sorgt.
MoS2+Ti: Hier geht es um eine mit Titan (Ti) dotierte etwa 1–3 μm dicke amorphe Molybdändisulfid (MoS2)-Schicht mit einer ähnlichen Härte wie die NoWear Beschichtung, die jedoch speziell für eine sehr geringe Reibung und hohe Verschleißfestigkeit in trockenen, Vakuum- und Reinraumumgebungen entwickelt wurde. Die Lagerteile werden in einer Vakuumkammer einem PVD-Verfahren unterzogen, bei dem durch physikalische Reaktionen in Gegenwart eines Plasmas Dampf entsteht, der bei Temperaturen unter 180 °C auf dem Werkstück kondensiert.
b) Schutz vor Korrosion
Zn und ZnNi: Bei Zink und der Zink-Nickel-Legierung handelt es sich um 1–15 μm dicke Schichten, die durch elektrolytische Verfahren abgeschieden und später zum besseren Schutz passiviert werden. Sie werden typischerweise in anderen Anwendungen als Lagerlaufbahnen eingesetzt. Zum Schutz vor Korrosion wird zwar traditionell Zink verwendet, aber durch die Legierung mit Nickel konnten einige der Nachteile einer reinen Zinkbeschichtung, wie beispielsweise die geringe Härte, ausgeglichen werden. Neben seinen Korrosionsschutzeigenschaften bewirkt Zink eine hohe Reibung, die als Gleitschutz oder Schutz vor Passungsrost an den Außenflächen von Lageraußen- und -innendurchmessern oder den Bohrungen der Lagergehäuse dienen kann.
NiP: Die 10–50 μm dicke silberfarbene Nickel-Phosphor-Legierung wird durch ein autokatalytisches stromloses Verfahren abgeschieden. Es gibt drei Varianten mit unterschiedlichen Phosphorkonzentrationen zwischen 6 % und 14 %; die Erhöhung des Phosphorgehalts verbessert die Korrosionsschutzeigenschaften, wirkt sich jedoch nachteilig auf die Härte und die Verschleißfestigkeit aus. Diese Beschichtung wird typischerweise für andere Anwendungen als Lagerlaufbahnen verwendet, bei denen eine Kombination aus Korrosions- und Verschleißschutz erforderlich ist. Allerdings könnte sie auch mit einer Dicke von weniger als 3 μm bei Laufbahnen eingesetzt werden.
TDC (engl. Thin Dense Chromium, dünnes, dichtes Chrom): Es handelt sich hierbei um eine 2–5 μm dicke silberfarbene polykristalline Chromschicht. Die Beschichtung wird mittels Elektrolyse mit einem Chromsäureelektrolyten aufgebracht. Der Prozess wird weiter katalysiert, zum Beispiel mit Kaliumdichromat, um eine dünne Chromschicht mit einer knotenförmigen Struktur zu bilden. TDC-Beschichtungen können auf Lagerlaufbahnen und Lageraußenflächen aufgebracht werden. Neben einer guten Korrosionsbeständigkeit zeichnen sie sich durch eine hohe Härte, geringe Reibung und hohe Verschleißfestigkeit aus.
c) Schutz vor Passungsrost
PTFE: Es handelt sich um eine 10–20 μm dicke Polymerbeschichtung. Polytetrafluorethylen (PTFE)-Pulver wird mittels Zerstäubungs- oder elektrostatischem Spritzen auf die Oberfläche gesprüht, und die Schicht entsteht durch ein thermisches Sinterverfahren. Die Beschichtung hat hervorragende Gleiteigenschaften, eine sehr geringe Reibung und keine Stick-Slip-Eigenschaften. Sie sorgt für einen starken und dauerhaften Schutz vor Passungsrost im Innendurchmesser oder am Außendurchmesser von Lagerringen.
d) Elektrische Isolation
INSOCOAT: Hier handelt es sich um eine etwa 100–300 μm dicke elektrisch isolierende Schicht aus Aluminiumoxid, die mit einem atmosphärischen Plasmaspritzverfahren aufgebracht wird. Dabei werden geschmolzene Al2O3-Partikel auf das Stahlsubstrat aufgesprüht, und die poröse Struktur wird anschließend versiegelt. Ein zusätzlicher Feinschliff sorgt für richtige Lagerabmessungen. Die Beschichtung wird entweder auf die Außenflächen des Lageraußenrings oder auf die innere Bohrungsfläche des Innenrings aufgebracht. Die wichtigsten Vorteile der INSOCOAT Beschichtung liegen im Bereich der elektrischen Isolation; hierbei wird verhindert, dass ein elektrischer Strom durch das Lager fließt, der eine Erosion der Laufflächen verursacht.
e) Schutz vor Gleitverschleiß bei Käfigen
Ag: Mit galvanischen Verfahren werden 2–4 μm dicke Silber (Ag)-Schichten abgeschieden, meist mit einer Kupferunterschicht zur Verbesserung der Haftung. Es ist eine weiche Metallschicht mit Trockenschmiereigenschaften, die bei hohen Temperaturen und in Vakuumumgebungen zum Einsatz kommt. Sie weist eine ausgezeichnete elektrische Leitfähigkeit auf und bietet einen guten Korrosionsschutz gegen (leicht alkalische und saure) Chemikalien. Diese Beschichtung wird hauptsächlich bei Stahlkäfigen und in seltenen Fällen bei Ringen und Rollen für bestimmte anspruchsvolle Anwendungen eingesetzt, wie zum Beispiel für die Trockenschmierung in Vakuumanwendungen sowie in der Lebensmittel- und Luft- und Raumfahrtindustrie.
TiN: Titannitrid (TiN)-Beschichtungen bestehen aus 1–5 μm dicken goldfarbenen Schichten. Die Teile werden in einer Vakuumkammer einem PVD-Verfahren unterzogen, wo durch physikalische Reaktionen bei Vorhandensein eines Stickstoffplasmas ein Dampf erzeugt wird, der von einem Titantarget gesputtert wird und bei Temperaturen unter 180 °C auf dem Werkstück kondensiert. Diese verschleißfesten Beschichtungen werden bei Käfigen unter Verwendung von Schmierstoffen und bei beschichteten Hülsen eingesetzt, die in der Lebensmittelindustrie verwendet werden.
Gleitlager
Bild 3 zeigt die acht wichtigsten Beschichtungsarten für Gleitlager, die drei Hauptfunktionen erfüllen: Schutz vor Korrosion und Verschleiß, letzteres bei Lagern mit und ohne Fettschmierung.
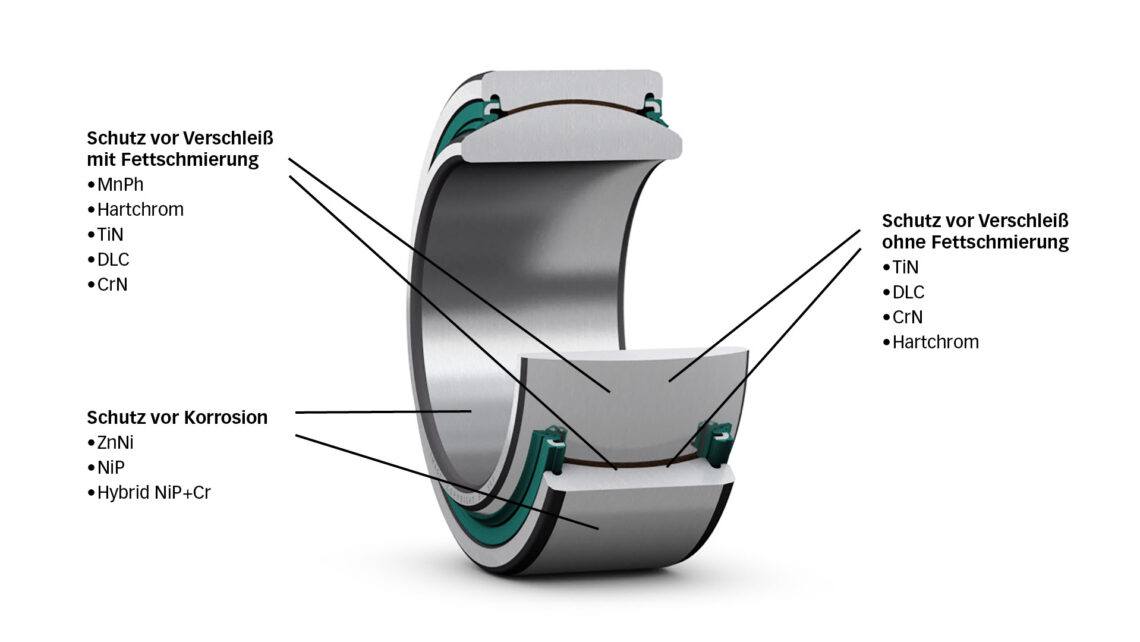
a) Schutz vor Verschleiß ohne Fettschmierung
Hartchrom: Dabei handelt es sich um eine 3–15 μm dicke silberfarbene Hartchrom (Cr)-Schicht, die durch ein galvanisches Verfahren mit einem Chromsäure-Elektrolyten abgeschieden wird. Das Verfahren endet mit einer Reinigung, dem Entfernen von sechswertigem Chrom [Cr(VI)] und einer Ölkonservierung. Die Beschichtung sorgt für einen guten Gleitkontakt zwischen den Gleitlagerkomponenten und verleiht ihnen eine hohe Härte und Verschleißfestigkeit. Die so entstandene Chromschicht weist Mikrorisse auf, was bedeutet, dass sie bei geringer Dicke nur begrenzten Korrosionsschutz bietet.
CrN: Chromnitrid (CrN) ist eine 1–6 μm dicke silbergraue Schicht, die mittels PVD-Verfahren abgeschieden wird. Die Teile werden in eine Vakuumkammer gebracht, wo Feststofftargets aus reinem Chrom mit einem Plasma aus Ar+N-Ionen beschossen werden, die das Cr-Material verdampfen („Sputtering“-Verfahren). Die Cr-Atome verbinden sich mit dem Stickstoff und kondensieren auf den Werkstücken, die auf einer Temperatur unter 180 °C gehalten werden. Das Resultat ist eine harte Beschichtung mit sehr guten Gleitverschleißeigenschaften, die auch in einigen korrosiven Umgebungen eingesetzt werden kann. Die Beschichtung kann auch in Wälzlageranwendungen verwendet werden, bei denen CrN-beschichtete Ringe und NoWear beschichtete Rollen kombiniert werden. Sie wird auch als Unterlage für andere Beschichtungen verwendet, um einen höheren Kontaktdruck zu erzielen.
DLC (engl. Diamond-Like Carbon, diamantähnlicher Kohlenstoff): Dies ist der Oberbegriff für eine Gruppe von Beschichtungen auf Kohlenstoffbasis, die sich aus einer Mischung von Graphit- und Diamantgefügen zusammensetzen. Sie enthalten entweder Wasserstoff oder sind wasserstofffrei, und sind normalerweise zwischen 2 und 4 μm dick. Die zu beschichtenden Teile werden in eine Vakuumkammer gebracht, in der je nach Anwendung mehrere Schichten mittels PVD- oder PACVD-Verfahren auf die Oberflächen der Lagerkomponenten aufgebracht werden. Ihre Zusammensetzung beeinflusst die Eigenschaften der Beschichtungen. DLC-Beschichtungen sind für hohen Verschleiß und Mangelschmierung ausgelegt. Sie zeichnen sich aus durch eine hohe Gleit- und adhäsive Verschleißfestigkeit, eine hohe Tragfähigkeit, einen ausgezeichneten Abriebschutz und eine geringe Reibung. Zudem bieten sie einen Oberflächenschutz bei Mangelschmierung. DLC-Beschichtungen sind ideal für Gleitlager, Linearantriebe von Lagern, Lagerwellen, Buchsen, Kurvenrollenstifte und gleitende Teile in Wälzlagern (wie Käfige und Dichtungen). Die NoWear Beschichtung aus Kohlenstoff und Metall gehört ebenfalls zu dieser Familie der kohlenstoffbasierten Beschichtungen; es gibt jedoch einige Unterschiede. Die Härtewerte von DLC-Beschichtungen für Gleitanwendungen liegen im Bereich von 18–30 GPa (1800–3000 HV), während NoWear Beschichtungen (für Wälzanwendungen) Härtewerte von etwa 12 GPa (ca. 1200 HV) aufweisen.
b) Schutz vor Verschleiß mit Fettschmierung
MnPh: Manganphosphat (MnPh) ist eine 2–15 μm dicke graue bis schwarze Schicht. Die Beschichtung erfolgt durch eine chemische Reaktion, und normalerweise werden alle Oberflächen des Werkstücks beschichtet. Beim Manganphosphatieren werden die Teile in eine Flüssigkeit getaucht, und das Eisen im Werkstück reagiert mit den Mangankationen und Phosphatanionen in der Flüssigkeit. Die Beschichtung schützt vor Verschleiß und Passungsrost und ist deutlich beständiger gegen Anschmierungen und Graufleckigkeit (Micropitting). Sie bietet auch Schutz bei niedrigen Kappa-Werten und Mangelschmierung und zeichnet sich durch eine verbesserte Ölhaftung aus. Zudem verfügt MnPh über einen guten Korrosionsschutz (im geölten Zustand) und besitzt elektrische Isolationseigenschaften.
c) Schutz vor Korrosion
Hybrid NiP+Cr: Hierbei handelt es sich um eine 10–30 μm dicke harte, silberfarbene Zweifachschicht bestehend aus einer Nickel-Phosphor- und einer Chrom-Beschichtung. Der gesamte Beschichtungsprozess ist zweigeteilt. Zunächst wird die Oberfläche mit stromlosem NiP beschichtet, um den Korrosionsschutz zu verbessern und die Chemikalienbeständigkeit zu erzielen; anschließend wird mittels elektrolytischer Abscheidung eine Hartchromschicht aufgebracht, die für mechanische Beständigkeit sorgt.
Beschichtungen und das Thema Nachhaltigkeit
Nachhaltigkeit bei Lagern umfasst Aspekte wie die Energie- und Ressourceneinsparung, Abfallminimierung, Steigerung der Verfahrenseffizienz und den Einsatz von erneuerbaren Materialien. Als weltweit führendes Technologieunternehmen sieht SKF den heutigen technologischen Wandel als Verantwortung und große Chance. Die Wiederverwendung industrieller Werkstoffe und Komponenten wie Öl und Lager stellt einen guten Anfang dar. Die Angebote – von einzelnen Dichtungen und Lagern bis hin zu industriellen Schlüsselkomponenten und -systemen – können beispielsweise zur Entwicklung reibungsarmer, leichter Automobillösungen beitragen, die den CO2-Ausstoß senken. Ein weiterer nachhaltiger Ansatz besteht darin, die Vorteile der Beschichtungstechnologie zu nutzen, die bei einigen Anwendungen die Reibung verringert (und damit den Energieverbrauch senkt) und die Lagerlebensdauer verlängert (und damit den Verbrauch neuer Rohstoffe reduziert).
Fazit
Beschichtungen für Lageranwendungen gewinnen zunehmend an Bedeutung. Durch eine gezielte Auswahl von Werkstoffen und Beschichtungen ist es möglich, spezielle physikalische, mechanische und tribologische Eigenschaften zu erzielen, um den immer höheren technischen Anforderungen gerecht zu werden. SKF Beschichtungen werden sorgfältig analysiert, um optimale Eigenschaften zu bieten. In einigen Fällen werden die Verfahren sogar über die jeweiligen DIN- und ISO-Normen hinaus an die verschiedenen Anwendungen angepasst.
Dieser Artikel behandelt in erster Linie einige der verschiedenen SKF Beschichtungsarten, um die Fachbegriffe, die technischen Aspekte und das Beschichtungsdesign zu erläutern. Weitere Informationen finden Sie in unserem Katalog SKF Coatings.