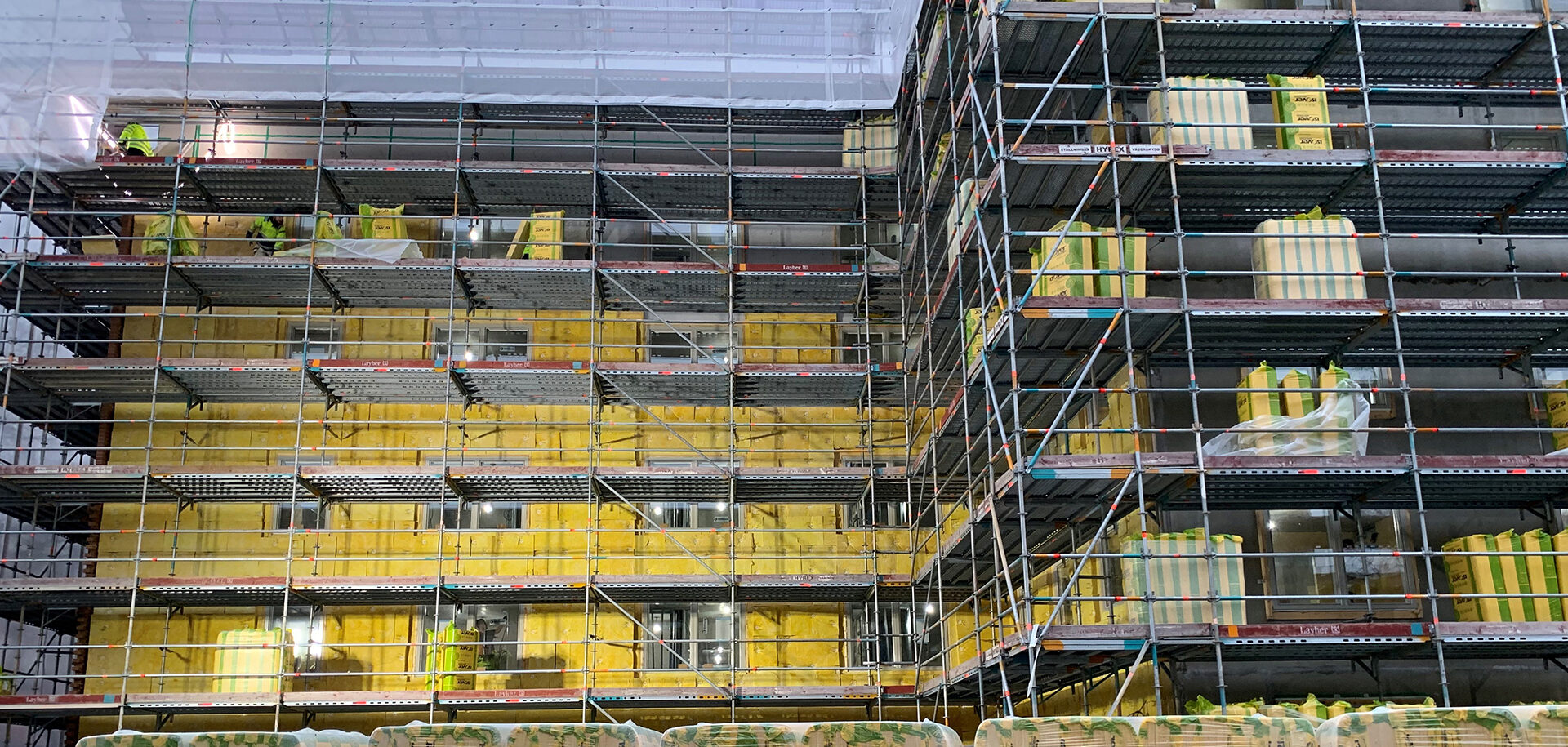
Saint-Gobain Isover dämmt das Ausfallrisiko ein
Mit den Möglichkeiten der Digitaltechnik steigern Wartungsteams von Saint-Gobain Isover die Produktionsleistung eines Artikels, der zur Rettung unseres Planeten beitragen kann.
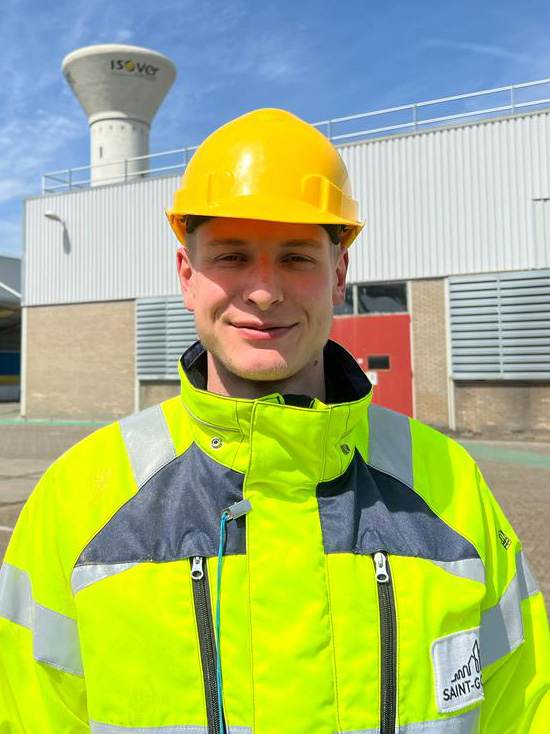
Wie können wir unseren Komfort zu Hause und am Arbeitsplatz beibehalten, ohne die Erdatmosphäre weiter aufzuheizen? Gebäude verursachen weltweit fast 40 Prozent der energiebezogenen CO2-Emissionen, und mehr als Zweidrittel dieser Emissionen stammen von der Energie, mit der wir im Winter heizen und im Sommer kühlen.
Wenn die Weltgemeinschaft ihre Ziele für die Reduzierung von Treibhausgasen erreichen will, muss der Übergang zu einem saubereren und effizienteren Gebäudebestand schneller gehen. Das erfordert Investitionen in neue Technologien, die mit erneuerbaren Energien betrieben werden, zum Beispiel dachmontierte Solaranlagen oder Wärmepumpen. Eine der wirksamsten Maßnahmen, um die CO2-Bilanz eines Gebäudes zu senken, ist jedoch die Wärmedämmung. Sie ist gleichzeitig auch eine der einfachsten Lösungen.
Gute Wärmedämmung verhindert, dass wertvolle Wärme über Wände und Dächer nach außen gelangt. Die Methode ist unkompliziert, erprobt und zudem kostengünstig. Investitionen in zusätzliche Gebäudedämmung machen sich in den meisten Fällen schon nach wenigen Jahren durch niedrigere Energiekosten bezahlt.
Das Werk von Saint-Gobain Isover im niederländischen Etten-Leur arbeitet schon seit 1962 im Bereich Energieeffizienz. Hier werden jährlich rund 45.000 Tonnen Glaswolle in Form von Dämmmatten für Dächer und als loses Fasermaterial zum Dämmen von Hohlwänden und Dachzwischenräumen hergestellt.
Die Fabrik in Etten-Leur hat drei Produktionslinien zur Herstellung von Glaswolle sowie eine weitere zur Fertigung des Glasfasermaterials, das als Belag für einige ihrer Produkte verwendet wird. Maschinenbauingenieur Bas Beishuizen ist dort für die Wartungstechnik zuständig. Seine Aufgabe ist es, dafür zu sorgen, dass die Produktionslinien stets zuverlässig und effizient arbeiten.
Die Herstellung von Glaswolle ist ein energieintensiver und mit hohen Geschwindigkeiten verbundener Massenfertigungsprozess. Das Instandhaltungspersonal muss sehr viel technische Ausrüstung warten. „Wir haben 57 kritische Anlagen in diesem Werk“, erläutert Beishuizen. „Dabei handelt es sich hauptsächlich um Pumpen und Lüfter, die allerdings recht groß sein können. Unser größter Lüfter zum Beispiel wird von einem 500-Kilowatt-Motor angetrieben.“
Wie können wir unseren Komfort zu Hause und am Arbeitsplatz beibehalten, ohne die Erdatmosphäre weiter aufzuheizen? Gebäude verursachen weltweit fast 40 Prozent der energiebezogenen CO2-Emissionen, und mehr als Zweidrittel dieser Emissionen stammen von der Energie, mit der wir im Winter heizen und im Sommer kühlen.
Wenn die Weltgemeinschaft ihre Ziele für die Reduzierung von Treibhausgasen erreichen will, muss der Übergang zu einem saubereren und effizienteren Gebäudebestand schneller gehen. Das erfordert Investitionen in neue Technologien, die mit erneuerbaren Energien betrieben werden, zum Beispiel dachmontierte Solaranlagen oder Wärmepumpen. Eine der wirksamsten Maßnahmen, um die CO2-Bilanz eines Gebäudes zu senken, ist jedoch die Wärmedämmung. Sie ist gleichzeitig auch eine der einfachsten Lösungen.
Gute Wärmedämmung verhindert, dass wertvolle Wärme über Wände und Dächer nach außen gelangt. Die Methode ist unkompliziert, erprobt und zudem kostengünstig. Investitionen in zusätzliche Gebäudedämmung machen sich in den meisten Fällen schon nach wenigen Jahren durch niedrigere Energiekosten bezahlt.
Das Werk von Saint-Gobain Isover im niederländischen Etten-Leur arbeitet schon seit 1962 im Bereich Energieeffizienz. Hier werden jährlich rund 45.000 Tonnen Glaswolle in Form von Dämmmatten für Dächer und als loses Fasermaterial zum Dämmen von Hohlwänden und Dachzwischenräumen hergestellt.
Die Fabrik in Etten-Leur hat drei Produktionslinien zur Herstellung von Glaswolle sowie eine weitere zur Fertigung des Glasfasermaterials, das als Belag für einige ihrer Produkte verwendet wird. Maschinenbauingenieur Bas Beishuizen ist dort für die Wartungstechnik zuständig. Seine Aufgabe ist es, dafür zu sorgen, dass die Produktionslinien stets zuverlässig und effizient arbeiten.
Die Herstellung von Glaswolle ist ein energieintensiver und mit hohen Geschwindigkeiten verbundener Massenfertigungsprozess. Das Instandhaltungspersonal muss sehr viel technische Ausrüstung warten. „Wir haben 57 kritische Anlagen in diesem Werk“, erläutert Beishuizen. „Dabei handelt es sich hauptsächlich um Pumpen und Lüfter, die allerdings recht groß sein können. Unser größter Lüfter zum Beispiel wird von einem 500-Kilowatt-Motor angetrieben.“
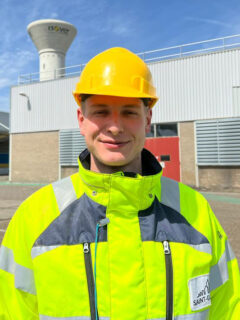
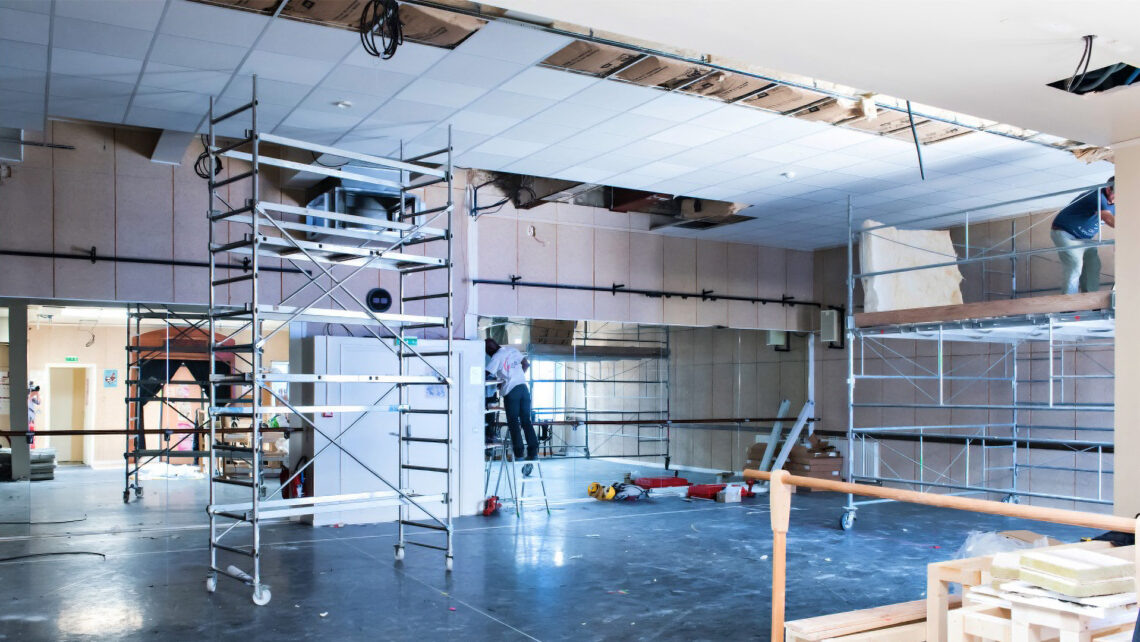
Ungeplante Ausfälle vermeiden
Der Ausfall einer entscheidenden Anlage könnte zum Stillstand der gesamten Produktionslinie führen und damit potenziell eine ganze Materialcharge vernichten. Wenn es geht, arbeitet das Instandhaltungsteam in Etten-Leur nach einem Konzept der vorbeugenden und zustandsbasierten Wartung. „Um die Instandhaltung von Lagern zu verbessern, verwenden wir die tragbaren SKF QuickCollect Sensoren zur Schwingungsmessung. Die Häufigkeit der Schwingungsmessungen hängt davon ab, wie wichtig und kritisch das Bauteil ist. Zunächst führt ein Techniker die Messungen durch. Danach werden die Lager in Zusammenarbeit mit SKF analysiert. So können wir mithilfe der Daten feststellen, ob etwas auf Probleme hindeutet.“
Mit Unterstützung der Zustandsüberwachungsexpertise von SKF erhielt das Wartungsteam durch die tragbaren Sensoren sehr bald nützliche Einblicke.
Bas Beishuizen, Wartungsingenieur bei Saint-Gobain Isover
Mit Unterstützung der Zustandsüberwachungsexpertise von SKF boten die tragbaren Sensoren sehr bald nützliche Einblicke. So zeigte die Analyse der Schwingungsspektren, dass eine Reihe von Lagern mangelhaftgeschmiert waren. „Als wir uns die Sache näher anschauten, fanden wir heraus, dass an einigen Maschinen die Schmierstellen falsch angebracht waren, sodass das Schmierfett nicht an die richtige Stelle im Lager gelangte“, sagt Beishuizen. „Nachdem wir die Ursache gefunden hatten, war das Problem schnell behoben.“
Schwingungsmessungen weisen nicht nur auf Lagerprobleme hin, sondern auch auf andere Mängel in einer Anlage. „Ein häufig auftretendes Problem bei Saint-Gobain Isover sind Unwuchten in den Lüftern“, fährt Bas Beishuizen fort. „An den Lüfterflügeln können sich Verunreinigungen ansammeln, die die Effizienz des Lüfters beeinträchtigen und eventuell zu Störungen führen. Schwingungsmessungen geben den Wartungstechnikern die Möglichkeit, die verschmutzten Lüfter während eines geplanten Stillstands der Anlage zusammen mit dem Bedienpersonal zu reinigen und auszuwuchten. So lassen sich Betriebsunterbrechungen durch schwingungsbedingte Probleme bei Lagern oder Motorhalterungen reduzieren.“
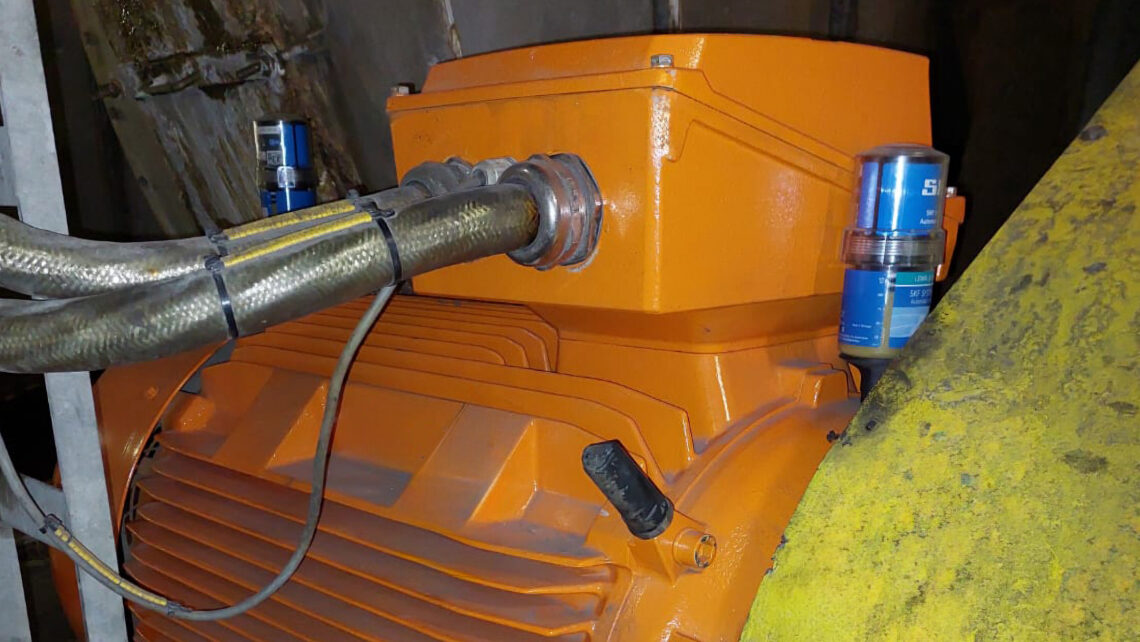
Zustandsüberwachung online
Ermutigt vom Erfolg der Schwingungsmessungen wollte Beishuizen mit dem Konzept einen Schritt weiter gehen. „Messungen mit tragbaren Sensoren liefern wirklich sehr nützliche Daten. Aber sie werden nur ein paar Mal pro Jahr durchgeführt“, erklärt er. „Das Wartungspersonal will mehr Daten, und das heißt, wir brauchen häufigere Messungen, um einen guten Datenbestand aufzubauen.“
Dazu stiegen Beishuizen und sein Team auf Online-Zustandsüberwachungstechnik um. An besonders wichtigen Anlagen des Etten-Leur-Werks wurden IMx-1 Sensoren von SKF fest installiert. Diese kompakten, batteriebetriebenen Geräte erfassen kontinuierlich Schwingungs- und Temperaturdaten. Sie übertragen diese Daten über ein drahtloses Mesh-Netzwerk an ein Gateway, das sie über eine 4G-Mobilfunkverbindung an die SKF Cloud sendet. „Innerhalb der Saint-Gobain Gruppe haben wir unsere eigene Softwareplattform für das Wartungsmanagement. Dank der API-Verbindung zwischen SKF und Saint-Gobain können wir nun sämtliche Schwingungsdaten abrufen und mit allen unseren anderen Daten kombinieren“, so Beishuizen. „So sind wir in der Lage, alle Daten an einer Stelle zu organisieren.“
Die kontinuierliche Schwingungsüberwachung bringt dem Werk zahlreiche potenzielle Vorteile. Sollten zum Beispiel die Schwingungswerte plötzlich und unerwartet ansteigen, kann das System das Wartungs- oder Bedienpersonal auffordern, der Sache auf den Grund zu gehen. Auf längere Sicht lassen sich an den aufgezeichneten Daten schleichende Trends ablesen, die auf eine nachlassende Maschinenleistung hindeuten.
„Das Wartungsteam entwickelt ein Dashboard für Zustandsüberwachung, um eine zustandsbasierte Wartung im Werk von Isover durchzuführen“, erklärt Beishuizen. „Das Dashboard vermittelt uns einen Überblick über alle unsere kritischen Anlagen und zeigt an, welche Maschinen vorrangig unserer Aufmerksamkeit bedürfen. Mehrmals pro Jahr wird jede Produktionslinie für geplante Wartungsmaßnahmen abgeschaltet. Wir möchten dahin kommen, dass wir anhand der Daten vorab genau erkennen, welche Maßnahmen während einer jeden Betriebsunterbrechung durchgeführt werden müssen.“ Das würde die Instandhaltungsarbeit verbessern und die Stillstände verkürzen. Inspektionen vor dem Abschalten der Produktionslinie wären bereits durch die Datenanalysen erfolgt.
Aber das sei erst der nächste Schritt, betont Beishuizen. Das Wartungsteam hat noch zahlreiche andere Pläne für das digitalisierte Instandhaltungskonzept des Werks: „Indem wir Zustandsdaten mit Betriebs- und Wartungsdaten kombinieren, können wir uns ein besseres Bild über die Leistung unserer Anlagen verschaffen. Wir sehen auch, wie und wann die Leistung nachlässt. Dadurch können wir uns auf Projekte konzentrieren, die die Zuverlässigkeit und Effizienz unserer Tätigkeit verbessern“, schließt Bas Beishuizen.
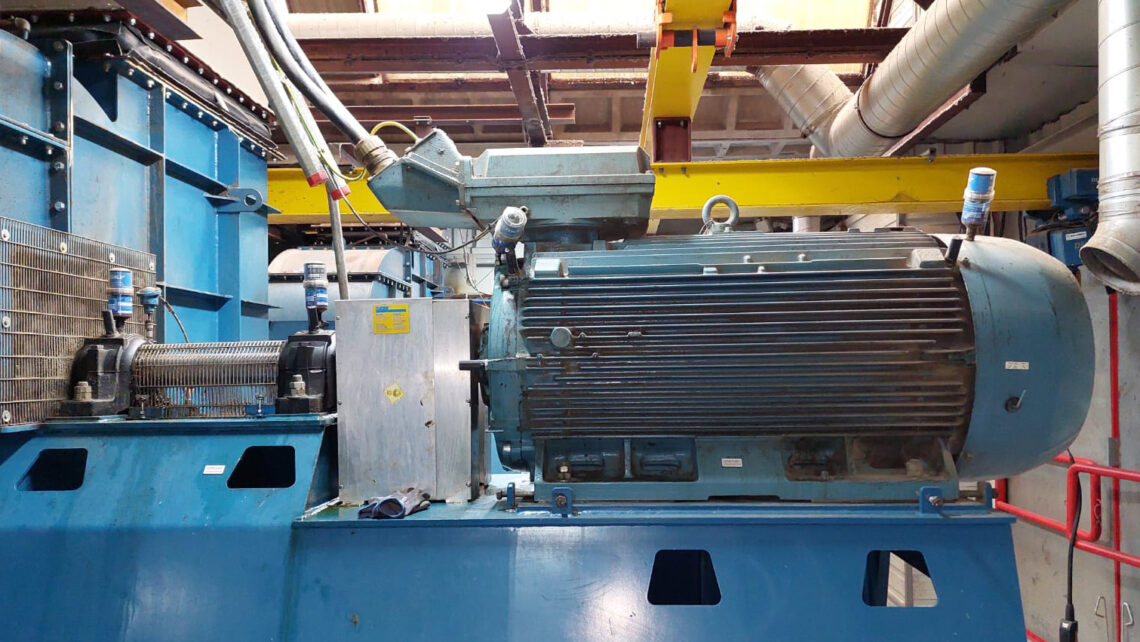
Glaswolle ähnlich wie Zuckerwatte
Die Produktion von Glaswolle gleicht ein wenig der Herstellung von Zuckerwatte. Die Zuckerwattemaschinen auf dem Jahrmarkt verwandeln den geschmolzenen Zucker mit einem Spinnkopf in eine lockerleichte, watteähnliche Süßigkeit. Der Produktionsprozess der Glaswolle ist jedoch mit erheblich höheren Temperaturen verbunden und findet großtechnisch.
Zunächst werden die Rohstoffe einer Charge gemischt und in einem Schmelzofen auf circa 1.400° C erhitzt. Früher handelte es sich bei den Rohstoffen um die Grundbestandteile von Glas: Quarzsand, Soda und Kalk. Heute besteht ungefähr die Hälfte der bei Isover verwendeten Mischung aus recyceltem Glas. Das senkt den Verbrauch von Primärrohstoffen und spart Energie im Produktionsprozess, da Glas bei einer niedrigeren Temperatur schmilzt als Sand.
Das flüssige Glas wird einer sich schnell drehenden Scheibe zugeführt und mittels Zentrifugalkraft durch Tausende kleiner Löcher in der Außenwand der Scheibe herausgeschleudert. Bei diesem Prozess entstehen haarfeine Fasern. Zur Herstellung von Glasfasermatten werden die Fasern mit einem Bindemittel besprüht und zu Matten geformt. Im nächsten Schritt werden die Matten in einem Härteofen auf ihre endgültige Dicke komprimiert. Das ausgehärtete Bindemittel hält die Fasern an ihren Knotenpunkten zusammen. So entsteht ein haltbares Material, das für den Transport auf ein Zehntel seines Volumens zusammengedrückt werden kann. Beim Auspacken nimmt es sofort wieder seine ursprüngliche Größe an. Je nach Einsatzanforderungen können die Matten für noch bessere Haltbarkeit und leichtere Handhabung mit einer Glasvlieskaschierung versehen werden.
Schmierstoff perfekt dosiert
Nachdem das Werk in Etten-Leur die Auswirkungen von mangelhafter Schmierung an betriebswichtigen Anlagen erfahren musste, wählte man für viele Maschinen eine andere SKF Technik. „Wir wissen, dass ein Lager für eine Betriebsdauer von sechs Monaten etwa 50 Gramm Schmierstoff benötigt“, erklärt Bas Beishuizen, von der Wartungstechnik bei Saint-Gobain Isover. „Bei einmaliger Zugabe der gesamten Schmierstoffmenge erzielt man allerdings nicht die optimale Wirkung. Außerdem ist nicht immer sichergestellt, dass das Lager wirklich geschmiert ist.“
Das Werk entschied sich stattdessen für den funkgesteuerten Einzelpunkt-Schmierstoffgeber TLDD von SKF. Dieses System versorgt jedes Lager regelmäßig in vorab festgelegten Intervallen mit einer kleinen Menge Schmierstoff aus einer integrierten Schmierstoffkartusche. Ein Statusbericht wird über ein drahtloses Netzwerk und ein Gateway zum 4G Mobilfunknetz an die SKF Cloud übertragen. Damit weiß das Wartungspersonal, dass die Lager geschmiert wurden, wann jede Einheit nachgefüllt werden muss und ob etwas den Schmierstofffluss unterbrochen hat.