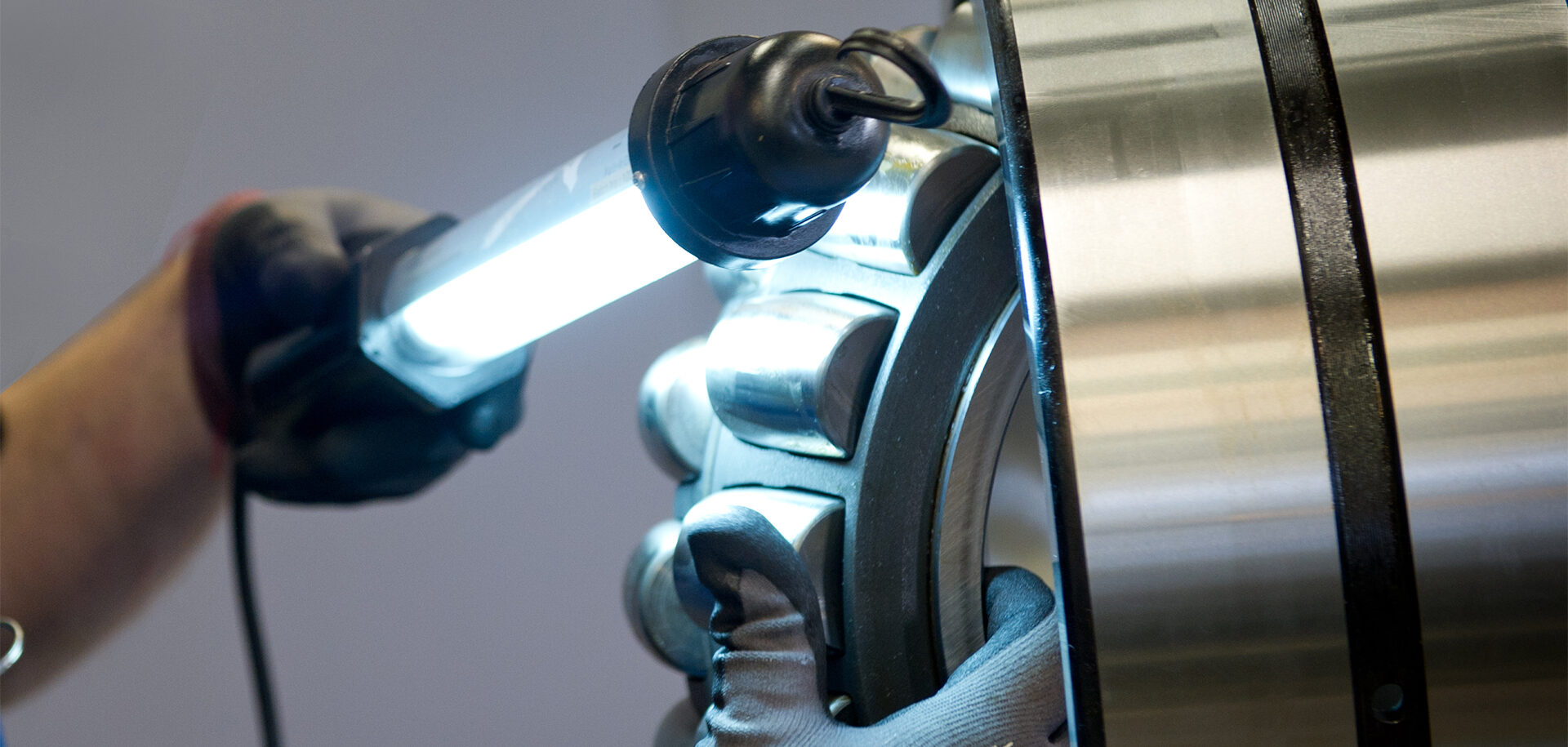
Schadensanalyse bei Wälzlagern mithilfe der Norm ISO 15243
Der erste Schritt auf dem Weg zur Vermeidung von Wiederholungsschäden und zur Steigerung der Maschinenzuverlässigkeit ist die Fähigkeit, Lagerausfallarten und Ursachen von Wälzlagerschäden feststellen zu können.
Lager gehören zu den am häufigsten verwendeten Bauelementen in modernen Industriemaschinen. Sie verbinden den rotierenden Teil (Welle) mit dem feststehenden Teil (Gehäuse), und zwar mit minimaler Reibung. Lager sorgen für den ordnungsgemäßen Betrieb von Maschinen und Anlagen, angefangen bei Autos und Flugzeugen bis hin zu Generatoren, Förderanlagen, Druckmaschinen und sonstigen Arten von rotierenden Maschinen und Anlagen.
Jeder, der mit Maschinen und Anlagen in der Industrie befasst ist, tut gut daran, besser verstehen zu lernen, wie sie funktionieren und warum sie manchmal vorzeitig ausfallen.
Vor diesem Hintergrund hat die Internationale Organisation für Normung (ISO) die Norm ISO 15243 veröffentlicht, die eine Klassifikation der verschiedenen Ausfallarten von Wälzlagern beinhaltet. In ihrer neusten Fassung von 2017 werden für jede Ausfallart die entsprechenden Merkmale und das jeweilige Erscheinungsbild beschrieben und die möglichen Ausfallursachen genannt.
Allerdings ist es nicht nur wichtig, die Merkmale und das Erscheinungsbild einer Ausfallart zu kennen, sondern auch die Ausfallursache zu verstehen. So können Empfehlungen für Abhilfemaßnahmen gegeben werden, die dazu beitragen, den jeweiligen Ausfall in Zukunft zu vermeiden. Natürlich lassen sich Ausfallart und -ursache so gut wie gar nicht mehr feststellen, wenn das Lager bis zum Ausfall betrieben wurde und sich festgefressen hat.
Im Folgenden wird ein Überblick über die verschiedenen Ausfallarten von Wälzlagern und deren Ursachen nach ISO gegeben. Doch zunächst ein paar grundlegende Anmerkungen:
Grundlagen der Wälzlagertechnik
Bei Wälzlagern handelt es sich um hochpräzise Maschinenelemente aus hochfestem Wälzlagerstahl, die immer häufiger mit Keramikwälzkörpern ausgestattet sind. Ein solches Lager besteht aus einem Innen- und einem Außenring, Kugeln oder Rollen sowie einem Käfig und ist möglicherweise mit Dichtungen oder einer Deckscheibe versehen. In Bild 1 sind die üblichen Bestandteile eines Wälzlagers dargestellt und benannt. Lager mit Deckscheiben werden vom Hersteller mit Fett befüllt. Für den Aufbau der Schmierfilmdicke, die für die Trennung von Wälzkörpern und Laufbahnen erforderlich ist, ist eine Schmierung mit Fett oder Öl sehr wichtig. Ein Lager muss nicht nur speziell für die jeweilige Maschine ausgewählt werden, sondern auch ordnungsgemäß montiert und eingebaut sowie gut geschmiert und frei von Verunreinigungen sein. Um Anzeichen von Schäden feststellen zu können, ist es wichtig, die innere Lagergeometrie zu kennen und zu wissen, wie sich ein Lager im Betrieb
Ausfallursachen
Was verhindert den ordnungsgemäßen Betrieb eines Lagers und führt zu dessen Ausfall?
Ebenso wichtig, und vielleicht noch wichtiger als die Ausfallart zu kennen, ist zu verstehen, was den Ausfall verursacht hat.
Auf diese Frage gibt es unterschiedliche Antworten, je nachdem, wen man fragt. SKF führt viele Lageruntersuchungen und Schadensanalysen für Kunden und die eigene Forschung durch. Die Ergebnisse dieser Untersuchungen werden bei SKF mit einer cloudbasierten Software, dem BART-Tool (Bearing Analysis Reporting Tool), dokumentiert. Die Gründe und Ursachen für die Außerbetriebnahme von Lagern werden zusammen mit einer Reihe anderer Daten aufgezeichnet. Mit diesen Daten kann SKF dann einige Antworten auf die Frage geben, weshalb ein Lager nicht mehr weiterbetrieben werden kann.
Die Daten zeigen, dass die meisten Lager wegen zu starker Schwingungen und einer übermäßigen Geräuschentwicklung außer Betrieb genommen werden. Die Lager werden auch außer Betrieb genommen, wenn Wartungsarbeiten an der jeweiligen Maschine durchgeführt werden oder zu hohe Temperaturen auftreten (Bild 2).
Klassifikation der Lagerausfallarten während des Betriebs nach ISO 15243
Die Norm ISO 15243: 2017 [Ref. 1] behandelt die Ausfallarten, die in der Zeit, in der das Lager in einer Anlage oder Maschine eingebaut ist, und während des Betriebs auftreten. Das heißt, sie bezieht sich nicht auf Herstellungsfehler, wie beispielsweise fehlende Teile. Die Ausfallarten nach ISO werden in sechs Kategorien unterteilt: Wälzermüdung, Verschleiß, Korrosion, Elektroerosion, plastische Verformung sowie Rissbildung und Bruch (Bild 4). Jede dieser Kategorien ist wiederum in Unterkategorien unterteilt, um eine genauere Klassifizierung der Ausfallarten zu ermöglichen.
Die Nummerierung (z. B. 5.1.2) der Klassifikation basiert auf ISO 15243 Kapitel 5.
Das Handbuch „Bearing damage and failure analysis“ [Ref. 2] bietet eine gute Hilfestellung bei der Feststellung der jeweiligen Lagerausfallart und -ursache.
Die sechs Kategorien werden wie folgt beschrieben:
Wälzermüdung (ISO 5.1)
Die Wälzermüdung wird in zwei Unterkategorien eingeteilt: Ermüdung beginnend unterhalb der Oberfläche und Ermüdung von der Oberfläche ausgehend. Die Ermüdung beginnend unterhalb der Oberfläche (ISO 5.1.2) (Bild 5) wird durch die zyklische Belastung der Oberflächen im Wälzkontakt verursacht, die im Laufe der Zeit zu einer Veränderung der Materialstruktur führt und Mikrorisse entstehen lässt. Die Mikrorisse zeigen sich unterhalb der Oberfläche, oft an einem Mikroeinschluss im Werkstoff, und breiten sich als Ausbrüche bis an die Oberfläche aus. Die Ermüdung wird durch die Lagerqualität, die auferlegten Belastungen, die Schmierung und die Sauberkeit beeinflusst. Dies ist vergleichbar mit der Lagerlebensdauer L10mh. Die Ermüdung unterhalb der Oberfläche kann sich beschleunigen, wenn das Lager hohen Spannungen ausgesetzt ist, beispielsweise durch eine vorübergehende Überlastung oder ein anderes Ereignis, das den Werkstoff schwächt. In diesen Fällen ist die Ermüdungslebensdauer kurz (5 %-10 % von L10mh). Die Ermüdung von der Oberfläche ausgehend (ISO 5.1.3) (Bild 6) ist eine Ermüdungserscheinung auf den Laufflächen, die in der Regel durch Oberflächenzerrüttung aufgrund von Mangelschmierung oder Verschmutzung verursacht wird. Ein unzureichender Schmierfilm und das Überrollen bei verunreinigtem Schmierstoff können einen Metall-Metall-Kontakt zur Folge haben, bei dem die Oberflächenrauheiten übereinander reiben. Danach können Mikrorisse auftreten, gefolgt von Mikroausbrüchen und schließlich kommt es zu einer von der Oberfläche ausgehenden Ermüdung.
Verschleiß (ISO 5.2)
Als nächste Kategorie folgt der Verschleiß, der nach ISO in zwei Unterkategorien eingeteilt wird: abrasiver Verschleiß und adhäsiver Verschleiß. Abrasiver Verschleiß (ISO 5.2.2) (Bild 7) ist die fortschreitende Abtragung von Werkstoff, meist in Verbindung mit abrasivem Material wie zum Beispiel Schmutzpartikeln. Abrasiver Verschleiß kann auch aufgrund von Mangelschmierung auftreten und ist im Allgemeinen durch ein mattes Aussehen der Oberflächen erkennbar. Es handelt sich dabei um einen degenerativen Prozess, der schließlich die Mikrogeometrie der Laufflächen eines Lagers zerstören kann. Abrasive Partikel können einen raschen Verschleiß der Laufbahnen von Ringen und Wälzkörpern sowie der Käfigtaschen herbeiführen. Abrasiver Verschleiß kann durch das Eindringen von verunreinigtem Material in den Schmierstoff und in das Lager sowie durch eine Mangelschmierung im Wälzkontakt verursacht werden.
Korrosion (ISO 5.3)
Die nächste Kategorie, nämlich Korrosion, wird in drei Unterkategorien eingeteilt: Feuchtigkeitskorrosion, Reibkorrosion und falsches Brinelling. Die Feuchtigkeitskorrosion (5.3.2) (Bild 9) geht auf das klassische Problem des Eindringens von Feuchtigkeit in das Lager zurück. Der hochfeste Lagerwerkstoff weist eine geringe Korrosionsbeständigkeit auf. Die Feuchtigkeit führt zu Schäden an den Wälzkörperzwischenräumen, wenn das Lager stillsteht. Die Schädigung der Oberfläche kann im späteren Betrieb zu einer von der Oberfläche ausgehenden Ermüdung führen. Feuchtigkeit beeinträchtigt in erheblichem Maße die Fähigkeit des Schmierstoffs, in einem in Betrieb befindlichen Lager eine Filmdicke aufzubauen. Passungsrost (ISO 5.3.3.2) (Bild 10) tritt auf, wenn Mikrobewegungen an einer Schnittstelle zwischen Passflächen auftreten, wie beispielsweise zwischen dem Lagerinnenring und der Welle und dem Lageraußenring und dem Gehäuse. Dies kann je nach Belastung auf einen falschen Sitz des Lagers auf der Welle oder im Gehäuse zurückzuführen sein. Ein Lager mit einem rotierenden Innenring und einer gleichmäßig auferlegten Belastung erfordert beispielsweise eine gewisse minimale Presspassung des Innenrings auf der Welle, um Passungsrost zu vermeiden. Ebenso erfordert ein Lager mit einem rotierenden Innenring und einer rotierend auferlegten Belastung des Innenrings einen entsprechenden Presssitz des Lageraußenrings im Gehäuse, um Passungsrost zu vermeiden. Passungsrost zeigt sich als rot-schwarze Oxidation auf der Berührungsfläche. Falsches Brinelling (ISO 5.3.3.3) (Bild 11) tritt an der Berührungsfläche zwischen den Wälzkörpern und der Laufbahn auf, die kleinen oszillierenden Bewegungen oder Schwingungen ausgesetzt ist. Der Verschleiß zeigt sich im Bereich der Wälzkörperzwischenräume. Durch den Verschleiß wird die ursprüngliche Fertigungsoberfläche abgetragen, und es kann auch zu einer rot-schwarzen Oxidation auf den Oberflächen kommen, ähnlich wie beim Passungsrost. Das Ausmaß des Verschleißes ist abhängig von der Intensität der auferlegten Belastung, der Intensität der Oszillationen und Schwingungen sowie den Schmierverhältnissen.
Elektroerosion (ISO 5.4)
Elektroerosion wird in zwei Unterkategorien eingeteilt: Erosion durch übermäßigen Stromdurchgang und Erosion durch Kriechstrom. Erosion durch übermäßigen Stromdurchgang (ISO 5.4.2) (Bild 12) entsteht, wenn elektrischer Strom durch einen Lagerring, die Wälzkörper und den anderen Lagerring fließt. An den Berührungsflächen ähnelt der Prozess dem Lichtbogenschweißen (hohe Stromdichte auf einer kleinen Berührungsfläche). Der Werkstoff wird so auf Temperaturen erwärmt, die vom Anlassen bis zum Schmelzen reichen. Dies führt dazu, dass an den Stellen, an denen der Werkstoff angelassen, nachgehärtet oder geschmolzen wurde, unterschiedlich große verfärbte Bereiche sichtbar werden. Krater bilden sich dort, wo der Werkstoff geschmolzen ist und durch die Drehbewegungen des Lagers weggebrochen ist. Der überschüssige Werkstoff wird abgetragen. Erosion durch übermäßigen Stromdurchgang kann durch Blitzeinschlag in eine Maschine verursacht werden oder wenn Schweißarbeiten an einer Maschine mit unsachgemäßer Erdung der Schweißausrüstung durchgeführt werden usw. Erosion durch Kriechstrom (ISO 5.4.3) (Bild 13) entsteht, wenn ein elektrischer Strom mit geringer Stromstärke durch das Lager fließt. Das typische Schadensbild zeigt kleine Krater, die nahe beieinander liegen und im Laufe der Zeit ein graues Waschbrettmuster entstehen lassen. Die Wälzkörper können grau und matt aussehen und der Schmierstoff kann sich verfärben. Wie groß der Schaden ist, hängt von der Stromstärke, der Dauer des Stromdurchgangs, der Lagerbelastung, der Drehzahl und dem Schmierstoff ab. Erosion durch Kriechstrom tritt häufig bei Elektromotoren mit Streuströmen auf, wenn die Welle nicht ordnungsgemäß geerdet ist und der Motor durch einen Frequenzumrichter (VFD) gesteuert wird.
Plastische Verformung (5.5)
Die plastische Verformung wird nach ISO in zwei Unterkategorien eingeteilt: Verformung durch Überlastung und Eindrückungen durch Teilchen. Bei der Verformung durch Überlastung (ISO 5.5.2) (Bild 14) handelt es sich um einen mechanischen Schaden, der durch statische Überlastung verursacht wird, wie beispielsweise durch unsachgemäße Handhabung (Herunterfallen des Lagers aus einer bestimmten Höhe), unsachgemäße Montage (Hämmern auf das Lager), Spitzenbelastungen durch den Betrieb der jeweiligen Maschine usw. Ein solcher Schaden kann sich in Form von Laufbahneindrückungen oder Schlagkerben an den Wälzkörperzwischenräumen, Beschädigungen an Käfigen, Dichtungen und Deckscheiben usw. zeigen. Eindrückungen durch Teilchen (ISO 5.5.3) (Bild 15) entstehen, wenn Verunreinigungen in Form von Feststoffen oder Schmutzteilchen im Wälzkontaktbereich des Lagers überrollt werden und dadurch Eindrückungen (Verformungen) in den Laufbahnen und an den Wälzkörpern entstehen. Die Größe, Art und Härte der Teilchen bestimmen das Ausmaß des Schadens. Ein anschließendes Überrollen der Eindrückungen kann zu einer von der Oberfläche ausgehenden Ermüdung führen (ISO 5.1.3).
Rissbildung und Bruch (ISO 5.6)
Die letzte Kategorie nach ISO behandelt Rissbildung und Bruch und umfasst drei Unterkategorien: Gewaltbruch, Ermüdungsbruch und Wärmerisse. Ein Gewaltbruch (ISO 5.6.2) (Bild 16) entsteht, wenn Spannungen die Zugfestigkeit des Werkstoffs überschreiten. Häufige Ursachen für einen Gewaltbruch sind zu hohe Ringspannungen bei der Montage eines Lagers auf einer Welle mit übermäßiger Presspassung oder das zu weite Aufschieben eines Lagers mit kegeliger Bohrung in seinen kegeligen Wellensitz oder seine Montagehülse. Es kommt zu einem Ermüdungsbruch (ISO 5.6.3) (Bild 17), wenn die Schwingfestigkeit eines Werkstoffs unter zyklischer Biegebeanspruchung überschritten wird. Eine wiederholte Biegebeanspruchung verursacht einen Riss, der sich durch den Ring oder Käfig ausbreitet. Dies kann in einem Lager auftreten, wenn es starken Belastungen ausgesetzt ist und das tragende Gehäuse keine gleichmäßige Steifigkeit aufweist, so dass der Außenring hohen zyklischen Spannungen ausgesetzt ist. Wärmerisse (ISO 5.6.4) (Bild 18) zeigen sich, wenn zwei Oberflächen aufeinander gleiten und dabei Reibungswärme entsteht. Bei starkem Gleiten führt die lokale Nachhärtung der Oberflächen in Verbindung mit der Entstehung hoher Zugeigenspannungen zu Rissen, die meist im rechten Winkel zur Gleitrichtung verlaufen. Wärmerisse können beispielsweise auftreten, wenn ein stillstehendes Gehäuse mit dem rotierenden Lagerring in Berührung kommt.
Eine ausführlichere Beschreibung der Lagerausfallarten und -ursachen ist in Referenz 2 zu finden.
Zudem ist zu beachten, dass der Schmierstoff (Öl oder Fett), der sich im beschädigten Lager befindet, ebenfalls Aufschluss über den Lagerschaden geben kann. Daher sollte eine Schmierstoffprobe entnommen werden, um sie mit einer frischen Schmierstoffprobe zu vergleichen. So können bei einer Schmierstoffanalyse Verunreinigungen durch Teilchen und Feuchtigkeit sowie Änderungen der Viskosität, der Fettkonsistenz usw. festgestellt werden.
Auch eine Untersuchung der Lagerdichtungen oder der Deckscheibe und anderer Lagerkomponenten wie der Hülse könnte aufschlussreich sein.
Verfahren der vorausschauenden Instandhaltung (Predictive Maintenance, PdM) oder der zustandsorientierten Instandhaltung (Condition Based Maintenance, CBM), wie beispielsweise die Schwingungsanalyse, die Thermografie, die Ölanalyse usw., können dazu genutzt werden, Störungen zu erkennen, bevor es zu schweren Lagerschäden und möglichen Schäden an der Anlage, in der das jeweilige Lager betrieben wird, kommt. Ein solches Vorgehen kann dazu führen, dass eine Ausfallart besser festgestellt werden kann. Die Außerbetriebnahme größerer Lager (Bohrung > 200 mm) vor dem Auftreten schwerwiegender Schäden kann eine Wiederaufarbeitung dieser Lager ermöglichen. Auf diese Weise können solche Lager wieder in einen neuwertigen Zustand versetzt werden, was eine Senkung der Wartungskosten und eine Reduzierung der Umweltbelastung zur Folge hat (Bild 19).
Die häufigsten Ausfallarten
Das Datenmaterial von SKF1 weist den abrasiven Verschleiß (26 %), die von der Oberfläche ausgehende Ermüdung (16 %), die Feuchtigkeitskorrosion (14 %), den adhäsiven Verschleiß (7 %) und die Erosion durch Kriechstrom (7 %) als die fünf häufigsten Ausfallarten nach ISO aus (Bild 20). Diese Ausfallarten stellen etwa 70 % aller bei Lageruntersuchungen festgestellten Ausfallarten dar, obgleich Passungsrost, wenn auch geringfügig, bei den meisten Lagern auftritt. Die anderen Ausfallarten nach ISO werden ebenfalls beobachtet, jedoch in geringerem Maße.
SKF BART (Bearing Analysis Reporting Tool)
Die bislang nur von SKF Technikern und Ingenieuren eingesetzte SKF BART Software steht nun auch den Kunden von SKF zur Verfügung. Sie erhalten eine Basisschulung zur Wälzlagertechnik und zu den Lagerprüfverfahren sowie zur Anwendung der SKF BART Software. Dabei arbeitet der Kunde eng mit einem SKF Anwendungstechniker oder Spezialisten zusammen, um den Prüfbericht zu erstellen. Der BART Prüfbericht wird dann vom SKF Experten freigegeben. Das Prüfverfahren kann Aufschluss darüber geben, ob ein Lager zu ersetzen ist, wiederverwendet werden kann, für eine Wiederaufarbeitung in Frage kommt oder verschrottet werden muss. Der Prüfbericht kann auch dazu verwendet werden, die Überprüfung eines neuen Lagers zu dokumentieren, bevor es in Betrieb genommen wird. Dies ist dann sinnvoll, wenn ein Lager schon längere Zeit im Lager aufbewahrt wurde.
Falls gewünscht, kann ein SKF Anwendungstechniker eine vollständige Lagerschadensanalyse durchführen und Empfehlungen zur Steigerung der Zuverlässigkeit abgeben. Die Techniker und Ingenieure von SKF können auf künstliche Intelligenz (KI) [Ref. 3] zugreifen, um die Genauigkeit ihrer Lagerschadensanalyse zu verbessern. Die KI bedient sich dabei eines Computer-Vision-Systems, das Lagerschäden anhand von digitalen Bildern beurteilt. Das System nutzt KI in Form eines Bilderkennungsalgorithmus über ein neuronales Netz, der mit Tausenden von Bildern schadhafter Lager aus den Archiven von SKF trainiert wurde.
Fazit
Zusammenfassend lässt sich sagen, dass die Norm ISO 15243 zur Klassifizierung der Ausfallarten von in Anlagen betriebenen Wälzlagern gut geeignet ist und zur Feststellung der Ausfallursachen herangezogen werden kann. Wer sich mit den häufigsten Lagerausfallarten und deren Ursachen vertraut macht, kann Abhilfemaßnahmen ergreifen, um eine Wiederholung der Ausfälle zu vermeiden. Auf diese Weise kann das Risiko ungeplanter und schwerwiegender Ausfälle erheblich verringert und die Zuverlässigkeit und Verfügbarkeit der Anlagen potenziell gesteigert werden. Lager, die zu Wartungszwecken außer Betrieb genommen werden, können so auf eine Wiederverwendung oder eventuelle Wiederaufarbeitung hin überprüft werden.
Daten über die Lagerausfallart und -ursache sowie andere damit zusammenhängende Daten werden gesammelt, um einen besseren Einblick in die Vorgänge im Lager zu erhalten. Die bislang nur bei SKF genutzte SKF BART Software steht nun auch den Kunden zur Verfügung, um Lagerprüfberichte und Schadensanalysen zu erstellen.
1 SKF BART (Bearing Analysis Reporting Tool)
References
[1.] Internationale Norm ISO 15243:2017: „Rolling bearings – Damage and failures –Terms, characteristics and causes“
[2.] SKF Broschüre 14219: „Bearing damage and failure analysis“
[3.] SKF Evolution Artikel: „Die Zukunft der Lagerausfallanalyse ist jetzt“ (2022)