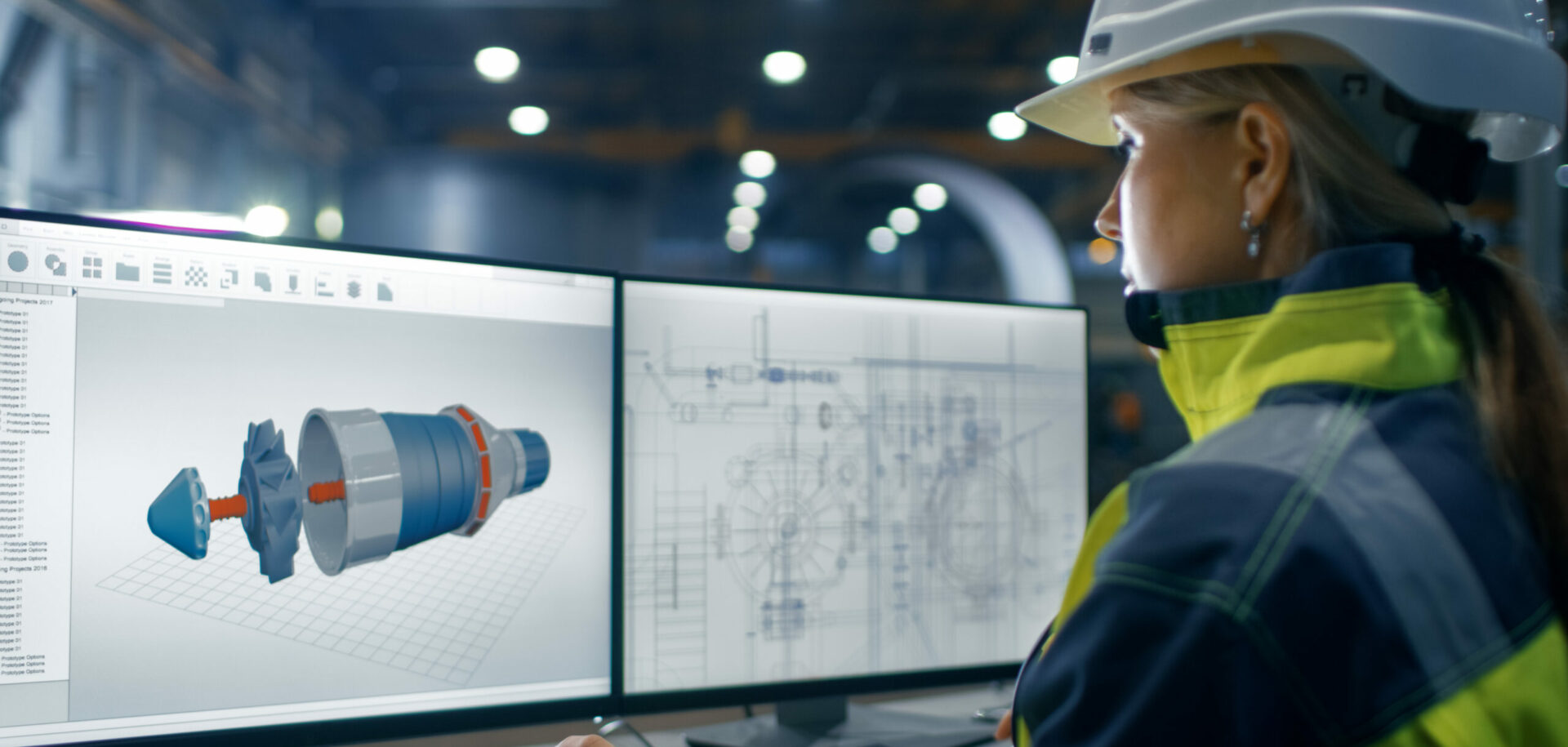
Wie brünierte Lager dazu beitragen, Betriebs- und Wartungskosten für Windkraftanlagen zu senken
Die Reduzierung der Betriebskosten von Windkraftanlagen hat hohe Priorität für Windturbinenhersteller und Betreiber. Brünierte Lager leisten hierzu ihren Beitrag. SKF bietet diese zum Einbau in neue und vorhandene Anlagen mit einem verbesserten Brünierungsverfahren an.
Zusammenfassung
Für Windkraftanlagen – zunehmend in rauer Umgebung errichtet – werden die Hersteller und Betreiber vor die Herausforderung gestellt, die Verfügbarkeit ihrer Anlagen zu verbessern und gleichzeitig die Betriebs- und Wartungskosten zu senken. Mit dem verbesserten Brünierungsverfahren leistet SKF durch einen verbesserten Schutz der Lager für diesen herausfordernden Industriezweig einen Beitrag zur Leistungssteigerung von Windkraftanlagen.
Links
Die Reduzierung der Betriebskosten von Windkraftanlagen hat hohe Priorität für Windturbinenhersteller und Betreiber. Brünierte Lager leisten hierzu ihren Beitrag. SKF bietet diese zum Einbau in neue und vorhandene Anlagen mit einem verbesserten Brünierungsverfahren an.
Bei Windkraftanlagen können die Betriebs- und Wartungskosten einen beträchtlichen Anteil an den Gesamtkosten ausmachen: bis zu 25 Prozent über die gesamte Nutzungsdauer einer Anlage1. Daher sind die Hersteller und Wartungsdienstleister an Möglichkeiten interessiert, den Wartungsaufwand zu verringern und Stillstandszeiten zu verkürzen. Zu diesem Zweck setzt sich SKF für ein verbessertes Brünierungsverfahren von Lagern in Windkraftanlagen ein.
Sowohl für neue Anlagen in der Auslegungsphase als auch bei routinemäßigen Wartungsarbeiten von Windparks können herkömmliche Lager durch brünierte Lager ersetzt werden. Somit lassen sich die Vorteile der Brünierung für die gesamte Windbranche nutzen. Als weltweit agierendes Engineering-Unternehmen und einer der führenden Anbieter von Lagern für die Windkraftindustrie hat SKF umfassende Erfahrungen mit Windkraftanlagen gesammelt, die vom Lagerdesign über breit gefächerte Dienstleistungen in den Bereichen Zustandsüberwachung, Schmiersysteme und Anlagenmanagement bis hin zur Lieferung von Ersatzteilen reichen. Im Rahmen der langjährigen Zusammenarbeit mit der Windbranche hat SKF viele Möglichkeiten zur Verbesserung der Betriebszuverlässigkeit mittels neuer Produkte und Verfahren, wie der speziell entwickelten Brünierung, aufgezeigt. Bei diesem Verfahren handelt es sich um einen Oberflächenveredlungsprozess, der signifikante Leistungsverbesserungen zu akzeptablen Kosten bietet.
Gesteigerte Anforderungen an Windkraftanlagen
Lager in Windkraftanlagen sind vielfach wechselnden Temperaturen, Drehzahlen und Belastungen ausgesetzt. In Kombination mit Verschmutzung, Feuchtigkeit und der chemischen Einwirkung von Schmierölen mit hoher AW-Additivierung führt dies dazu, dass die Lagerlebensdauer in manchen Fällen erheblich verkürzt wird, falls keine Gegenmaßnahmen ergriffen werden. Zudem werden mit zunehmender Größe von Windkraftanlagen und gesteigerter Leistungserzeugung an wichtige Systemkomponenten, wie beispielsweise Getriebe, höhere Anforderungen gestellt.
Das von SKF verwendete Brünierungsverfahren bietet Lagerkomponenten einen verbesserten Schutz vor Schäden, die aufgrund der anspruchsvollen Betriebsbedingungen, z.B. bedingt durch den Wechsel von Onshore- zu Offshore-Einrichtungen und bei den Anlagen in zunehmend raueren Umgebungen weltweit auftreten.
Während die Schadens- und Ausfallraten von Windkraftgetrieben je nach Quelle der veröffentlichten Daten variieren, wurde in der von der EU-finanzierten Reliawind-Studie ein Wert von rund 6 Prozent pro Jahr angegeben. In dieser Studie werden auch öffentlich verfügbare Daten über Ausfallraten und Stillstandszeiten aus großen Zuverlässigkeitsstudien ausgewertet, die von der Landwirtschaftskammer Schleswig-Holstein und dem Wissenschaftlichen Mess- und Evaluierungsprogramm des Fraunhofer Instituts in Kassel durchgeführt wurden, wobei Ausfallraten von rund 10 Prozent genannt werden. Selbst wenn diese Zahlen im Vergleich zu Ausfällen anderer Komponenten , wie Komponenten des elektrischen Systems, als recht niedrig angesehen werden können, sind die Folgen dieser Ausfälle eventuell doch schwerwiegend: Schäden und Ausfälle am mechanischen Antriebsstrang können aufgrund langer Stillstandszeiten und des aufwändigen Austauschs der beschädigten Komponente sehr hohe Kosten verursachen.
Beispielsweise können beim Ausfall eines auf der Ausgangswelle eines Onshore-Windgetriebes eingebauten Lagers Reparaturkosten von mehreren Tausend Euro anfallen, vorausgesetzt, das Lager wird in der Höhe ausgetauscht. Wenn jedoch ein Planetenlager ausfällt, muss in der Regel das ganze Getriebe ersetzt werden, und die Gesamtkosten können leicht mehrere Hunderttausend Euro übersteigen.
Die Hauptausfallmechanismen
Die Schadensarten, denen eine Brünierung der Lagerkomponenten (z.B. Ringe, Rollen) entgegenwirken kann, lassen sich im Allgemeinen in Kategorien wie Risse, schlupfbedingte Schäden (z.B. Anschmierungen) und Oberflächenzerrüttung unter Umgebungseinflüssen wie Feuchtigkeit und chemische Angriffe einteilen.
1. Risse
Viele vorzeitige Windgetriebelagerschäden basieren auf einem Versagensmechanismus, der nicht durch die klassischen Wälzkontaktermüdungsmechanismen hervorgerufen wird. Die klassischen Mechanismen betreffen die unter und an der Laufbahnoberfläche entstehende Ermüdung und können mithilfe von bekannten Lagerlebensdauerberechnungsverfahren prognostiziert werden, während vorzeitige Ausfälle aufgrund von weiß anätzenden Rissen, sogenannten „White Etching Cracks“ (WEC), wie sie bei Windgetriebelagern auftreten, nicht hierunter fallen. WEC zeigen sich im veränderten Stahlgefüge durch Polieren und Ätzen eines Mikroschliffs (Bild 1a). Ausfälle können an verschiedenen Lagerstellen auftreten, und zwar typischerweise bei Planetenradlagern sowie bei Lagern der Zwischen- und Ausgangswelle.
In der Windindustrie sind vorzeitige WEC-bedingte Ausfälle ein häufig diskutiertes Thema, welches von Windkraftanlagen-, Windgetriebe- und Lagerherstellern sowie von Universitäten und verschiedenen Instituten unabhängig voneinander untersucht wird. Die aktuellen Hypothesen gehen entweder von wasserstoffbegünstigten, rein last-/spannungsbedingten (vorzugsweise an Einschlüssen), als auch von an der Oberfläche entstehenden WEC-Entwicklungen aus, oder bestehen aus Kombinationen dieser Hypothesen.
2. Anschmierungen (adhäsiver Verschleiß)
Bei niedrig belasteten Rollenlagern kann es zu überlagertem Gleiten zwischen den Wälzkörpern und v.a. dem Innenring kommen, wenn der Unterschied in den Abwälzgeschwindigkeiten zwischen Innenring und Rollensatz sehr groß ist. Bei Ausgangswellen von Windgetrieben können Leerlaufbedingungen und Lastzonenwechsel zu einem hohen Risiko von gleitbedingten Lagerschäden führen.
Bei radial belasteten Rollenlagern ist die kritischste Zone, in der ein Schlupfschaden auftreten kann, der Bereich, in welchem die Rollen in die belastete Zone eintreten. Beim Rotieren verlangsamen sich die Rollen aufgrund von interner Reibung in der unbelasteten Zone des Lagers und müssen beim Eintritt in die belastete Zone wieder beschleunigt werden. Hierbei kann es zu Anschmierungen kommen (Bild 1b). Das Gefüge bzw. Material an der Rollenoberfläche und den Ringlaufbahnen ist beschädigt. Dies führt zu lokalen Beanspruchungen, die letztendlich Ausbrüche und Lagerausfälle verursachen.
Bei vollrolligen Zylinderrollenlagern baut sich aufgrund der entgegengesetzten Oberflächengeschwindigkeiten der sich berührenden Rollen nicht immer ein trennender Schmierfilm auf. Dünne Schmierfilme bzw. Mischreibung bei hohen Rolle-Rolle-Kontaktdrücken können einen metallischen Kontakt zwischen benachbarten Rollen erzeugen. Dies bewirkt eine Zunahme der Reibung, was wiederum zu Anschmierungen und einer Zerstörung der Oberfläche führen kann.
3. Oberflächenzerrüttung /Grauflecken
Viele Maschinenelemente mit Wälz- und Gleitkontakten (z.B. Wälzlager, Zahnräder, Kurvenrollen) unterliegen verschiedenen Arten von Schäden, wozu auch leichter abrasiver Verschleiß und Grauflecken zählen. Oberflächenzerrüttung oder Grauflecken treten infolge von Mangelschmierung zwischen den sich gegeneinander bewegenden Kontaktflächen auf. Dabei handelt es sich um eine Art von lokalem Oberflächenschaden, der insbesondere bei Verzahnungen, aber teilweise auch bei Lagern in Windgetrieben auftreten kann. Verzahnungen sind für gewöhnlich stärker betroffen als Lager. Dieser Schaden kann sich nachteilig auf die Lagerfunktion auswirken. Er verändert die Geometrie der Rollen und Laufbahnen, erhöht die Lagerluft und bewirkt lokal erhöhte Beanspruchungen, die letztendlich zu Ausbrüchen und Lagerausfällen führen (Bild 1c). Ein erhöhter Wassergehalt in Windgetrieben kann je nach Öltyp diesen Fehlermechanismus begünstigen.
4. Feuchtigkeits- /Stillstandskorrosion
Der Wassergehalt in Windgetriebeölen wird oft unterschätzt. Die hohen Temperaturgefälle können zusammen mit einem hohen Wasseranteil im Öl (je nach Ölsorte) zu Risiken durch „freies Wasser“ und somit Stillstandskorrosion führen (Bild 1d). Während die von freiem Wasser ausgehende Gefahr ausreichend bekannt ist, sind die Risiken unterschiedlicher Anteile von gelöstem Wasser in Getriebeöl noch nicht ausreichend erforscht. Untersuchungen von SKF haben gezeigt, dass immer dann mit negativen Auswirkungen auf die Lagerleistung zu rechnen ist, wenn ein bestimmter Anteil von gelöstem Wasser vorliegt.
5. Passungsrost
Ist die Innenringbohrung auf dem Wellensitz oder die Mantelfläche des Außenrings im Gehäusesitz Mikrobewegungen ausgesetzt, dann kann die natürliche Oxidschicht der Stahloberflächen abgetragen werden. Des Weiteren können die Oberflächenrauheitsspitzen korrodieren und abbrechen. Die Verschleißpartikel sind teilweise im Kontakt eingeschlossen. Sind noch Oxidationsmittel wie Feuchtigkeit vorhanden, so setzt sich die Korrosion an der Oberfläche weiter fort (Bild 1e). Unter Last korrodiert die Oberfläche weiter, was zu Verunreinigung durch Partikel, einem losen Sitz und somit erhöhtem Ringkriechen führen kann, oder schlimmstenfalls (falls die Korrosionspartikel im Sitz eingeschlossen bleiben) zum Ringbruch aufgrund einer erhöhten bzw. zu großen Ringspannung.
Das SKF Brünierungsverfahren
Für die oben genannten möglichen Ausfallarten bedeutet das Aufbringen einer Brünierung auf den funktionalen Lagerflächen eine verbesserte Sicherheit. Vorteilhaft für den Lagerbetrieb sorgt eine Brünierung beispielsweise für einen verbesserten Einlauf, verbesserte Oberflächeneigenschaften nach dem Einlaufen, bessere Eigenschaften bei Mangelschmierung (niedrigen κ -Werten), eine bessere Haftung des Schmiermediums und ein reduziertes Risiko von Schlupfschäden. Darüber hinaus kann das Risiko der Bildung von Passungsrost, Grauflecken und Rissentstehung vermindert werden. Des Weiteren zeichnet sich die Brünierschicht durch eine moderate Korrosionsfestigkeit aus und weist im Vergleich zu unbehandelten Oberflächen eine erhöhte chemische Beständigkeit auf. Die chemische Beständigkeit vermindert den schädlichen Einfluss aggressiver Ölbestandteile. Die erhöhte Korrosionsbeständigkeit ist ausreichend, um Stillstandskorrosion und Passungsrost entscheidend zu verringern. Ferner verbessert eine Brünierung das Reibungsverhalten und vermindert den Verschleiß bei Mischreibung. Neueste Forschungsergebnisse zeigen, dass die Brünierung zusätzlich wie eine Barriere für Wasserstoffdurchdringung im Wälzlagerstahl agieren kann.
Zur Verdeutlichung der möglichen Verbesserung der Ausfallraten dient folgender Vergleich: Ein Windgetriebehersteller hat bei einer Stichprobe von 1.000 unbeschichteten Zylinderrollenlagern in einer Getriebeanwendung eine Ausfallrate von 40 bis 70 Prozent (nach 2 Jahren) festgestellt. Bei einer darauffolgenden Stichprobe von 1.150 brünierten Zylinderrollenlagern in einer ähnlichen Anwendung ergab sich eine Ausfallrate von 0,1 Prozent über den gleichen Zeitraum2.
Zusammenfassend lässt sich sagen, dass brünierte Lager von SKF gegenüber unbehandelten Lagern in Windgetriebeanwendungen (Bild 4) folgende Vorteile bieten:
- verbessertes Einlaufverhalten
- höhere Korrosionsbeständigkeit
- verbesserte Beständigkeit gegen Anschmierungen (Schlupfschäden)
- bessere Eigenschaften bei Mangelschmierung
- bessere Haftung des Schmieröls bzw. Schmierfetts
- verminderte chemische Einwirkung aggressiver Ölbestandteile auf den Lagerstahl
- geringere Wasserstoffdurchdringung in den Lagerstahl
- geringeres Risiko von Passungsrost.
Mit mehr als 50.000 brünierten Lagern im Feldeinsatz hat SKF einen überzeugenden Erfahrungsschatz, dass dieses kostengünstige Verfahren zu Leistungsverbesserungen in der Windkraftindustrie führt und sich somit vorzeitige Ausfälle reduzieren sowie Betriebs- und Wartungskosten insgesamt verringern lassen.
Brünieren
Beim Brünieren handelt es sich um eine Oberflächenbehandlung, die zur Bildung einer schwarzen Oxidschicht auf der Lagerstahloberfläche infolge einer chemischen Reaktion führt. Diese Schicht bildet sich beim Eintauchen der zu behandelnden Teile in eine alkalisch-wässrige Salzlösung bei einer Temperatur von rund 150 °C. Die chemische Reaktion zwischen dem Eisen der Eisenlegierung und den Reagenzien lässt eine Oxidschicht aus dem Oberflächenmaterial der Lagerkomponenten entstehen, die aus einer wohldefinierten Mischung aus FeO, Fe2O3 und Fe3O4 besteht. Das Ergebnis ist eine tiefschwarze Schicht von etwa 1 bis 2 μm.
Die Vorteile des Brünierens müssen für jede Anwendung gesondert beurteilt werden. Aber bislang sind keinerlei nachteilige Folgen dieser Behandlung bekannt geworden. Dieses Verfahren wird bereits erfolgreich bei Lagern in anderen Industriezweigen angewendet, wie beispielsweise bei Papiermaschinenwalzen, Werkzeugmaschinen und Industriegebläsen.
Beim Brünieren gilt es, eine Vielzahl von Parametern zu berücksichtigen. Das Verfahren besteht insgesamt aus rund 15 unterschiedlichen Eintauchvorgängen, wobei diese hinsichtlich Chemikaliengehalt, -konzentration, Temperatur, Eintauchdauer und Fluidverhalten in den einzelnen Behältern variieren können.
Seit 2006 hat SKF dieses Verfahren intensiv weiterentwickelt, um Spezifikationen für eine optimierte Handhabung des Brünierverfahrens festzulegen sowie die Behandlung von Großlagern zu ermöglichen. Die Brünierverfahren von SKF sind auf jeden Lagertyp und jede Anwendung speziell angepasst. Die Verfahren eignen sich für zahlreiche Lagergrößen, bei Windkraftanlagen bis zu einem derzeitigen Außendurchmesser von 2,20 m, wobei das Gewicht der einzelnen Lagerkomponenten bis zu 1.000 kg betragen kann. Die Oberflächenbehandlungsmethode sowie die Größen- und Gewichtsbereiche sind rechtlich geschützt.
Um die Vorteile voll auszunutzen, empfiehlt SKF, sowohl die Innen- und Außenringe als auch die Wälzkörper zu brünieren. Die Brünierung kann für alle Lagerarten, die in kritischen Windkraftanlagen im Einsatz sind, angewendet werden. In den letzten Jahren wurden insbesondere Zylinder- und Kegelrollenlager für Getriebe erfolgreich brüniert (Bild 2 und 3).
Mit dem spezifizierten Brünierverfahren von SKF können über das globale Firmennetzwerk qualitativ hochwertige Lager hergestellt werden. So stehen die Vorteile der brünierten Lager den Windkraftanlagenherstellern, Endkunden und Dienstleistern überall auf der Welt zur Verfügung.
Bild 1: Arten von möglichen Lagerausfallarten bei Windgetrieben:
a) Risse / Ausbrüche
b) schlupfbedingter Lagerschaden / Anschmierungen
c) Oberflächenzerrüttung / Grauflecken
d) Feuchtigkeits- / Stillstandskorrosion auf einer Laufbahn
e) Passungsrost in der Bohrung eines Innenrings
Anmerkungen
1. Bei einer neuen Windkraftanlage betragen die Betriebs- und Wartungskosten nicht selten 20 bis 25 Prozent der gesamten Stromgestehungskosten – gerechnet über die gesamte Lebensdauer der Turbine. In den ersten Jahren des Betriebs einer Windkraftanlage liegt der Kostenanteil lediglich bei 10 bis 15 Prozent. Gegen Ende der Nutzungsdauer der Windkraftanlage erhöht dieser sich auf mindestens 20 bis 35 Prozent. Diese Zahlen stammen von Wind Energy – The Facts (WindFacts), einem europäischen Projekt, das vom Programm „Intelligente Energie – Europa“ der Exekutivagentur für Wettbewerbsfähigkeit und Innovation (EAWI) finanziert wurde.
2. J.Luyckx: Hammering Wear Impact Fatigue Hypothesis WEC/irWEA failure mode on roller bearings, NREL workshop, Broomfield, Colorado, USA, November 2011