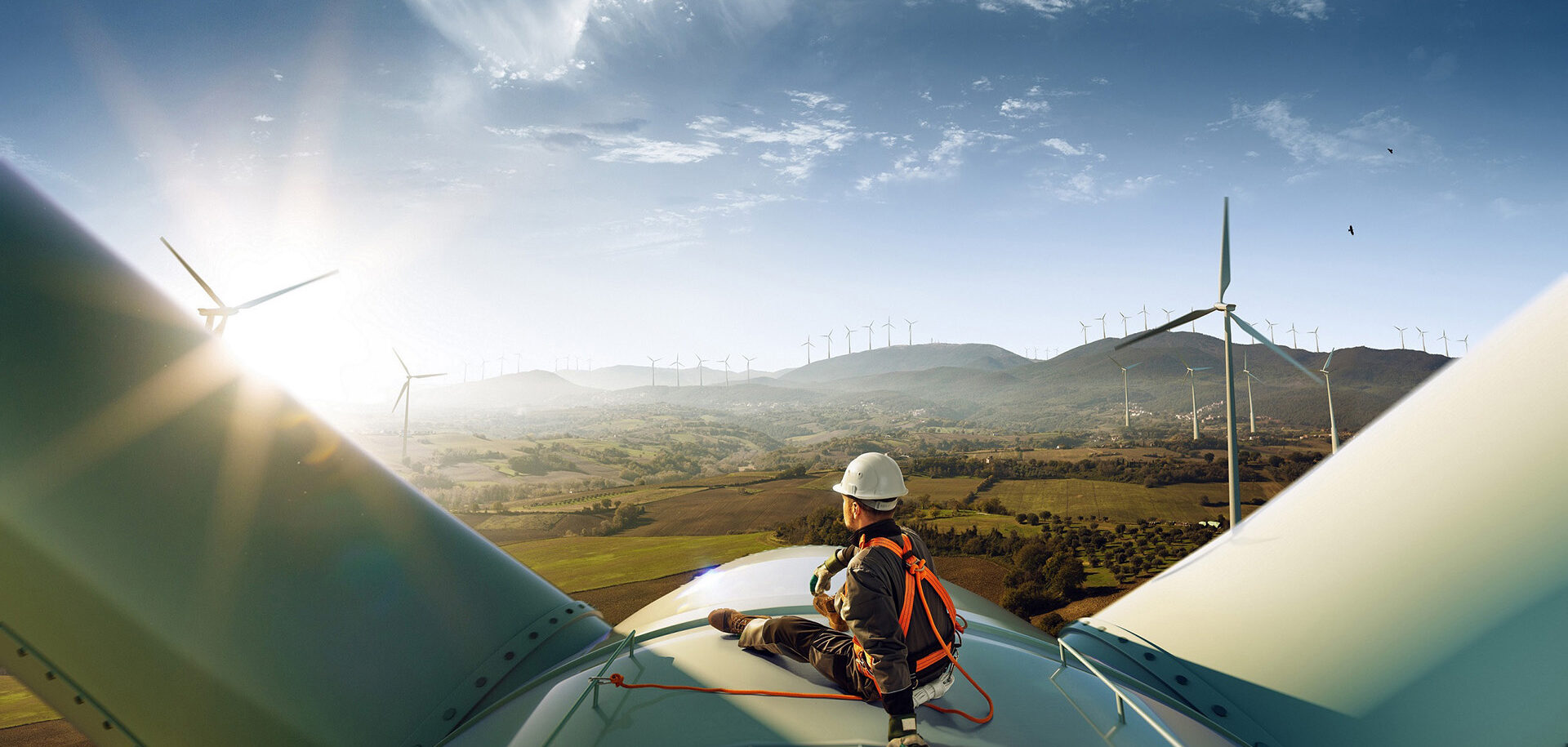
Des données pour réduire le coût actualisé de l’énergie
Les multiplicateurs et les roulements d'arbre principal sont des composants critiques des éoliennes. Leurs défaillances peuvent induire un manque à gagner, des surcoûts dus aux réparations d'urgence et, in fine, des coûts de production d'énergie plus élevés que prévu. SKF et le fabricant de multiplicateurs ZF ont uni leurs compétences pour faire évoluer la maintenance conditionnelle des multiplicateurs d'éoliennes dans le but d'accompagner les propriétaires des parcs éoliens, de réduire le coût actualisé de l'électricité et de faire de cette énergie renouvelable une activité plus rentable.
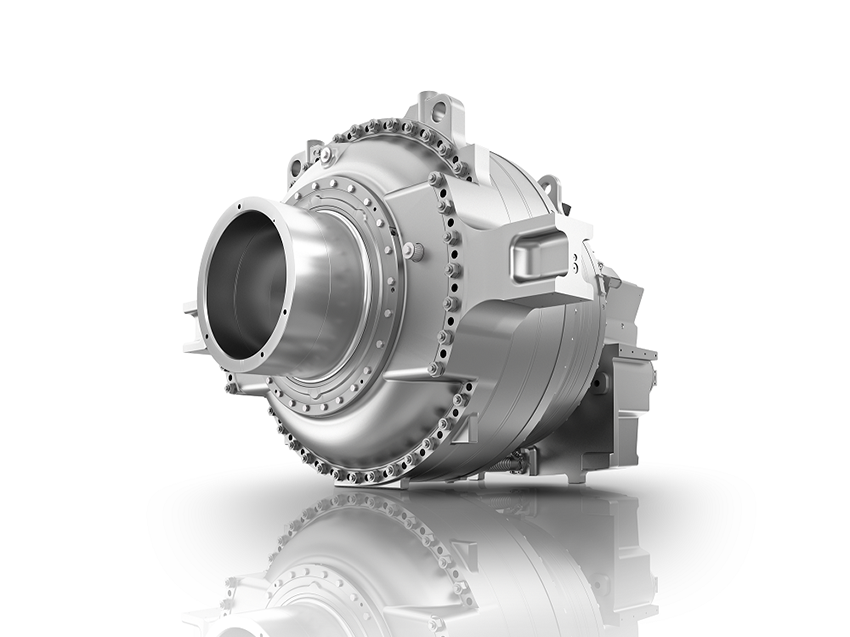
Mais pour assurer un prix compétitif de l’électricité produite par le vent, il est essentiel que les éoliennes ne s’arrêtent pas de tourner. L’un des moyens d’y parvenir est de se concentrer sur la réduction du coût actualisé de l’électricité (LCoE pour Levelized Cost of Energy) en ayant recours à la maintenance conditionnelle. Le LCoE est un concept qui prend en compte le coût de la production d’électricité tout au long de la durée de vie de l’éolienne. La réduction de la maintenance non planifiée permet effectivement d’améliorer la rentabilité du producteur d’énergie, mais elle n’entraîne pas forcément une hausse de la production ou une production plus stable. Toutefois, le fait de remédier aux défaillances récurrentes permet à la fois de diminuer le coût du cycle de vie de l’éolienne et de produire une plus grande quantité absolue d’électricité au cours de sa durée de vie.
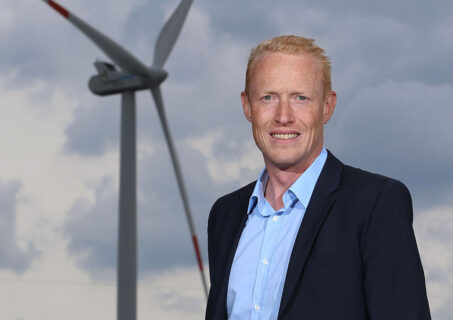
Nous avons discerné une demande des clients et nous sommes rendu compte qu'ensemble on pouvait créer de la valeur ajoutée pour eux.
Joris Peeters, responsable de la digitalisation du pôle technologie énergie éolienne de ZF
Simplifier les processus pour créer de la valeur ajoutée
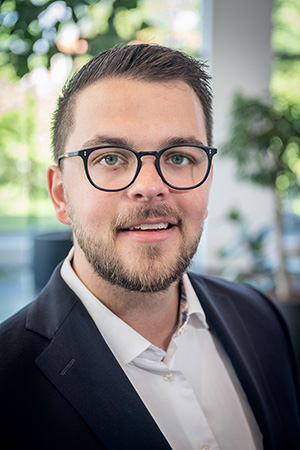
La maintenance conditionnelle à distance convient particulièrement à l’industrie éolienne, car elle permet aux exploitants de surveiller les composants pendant que l’éolienne produit de l’énergie. SKF et le fabricant de multiplicateurs ZF ont fait évoluer la maintenance conditionnelle. Leur approche simplifie considérablement les processus pour toutes les parties concernées et réduit de plus de 85 % les délais de réparation pour l’opérateur. Le projet exploite la capacité des capteurs à détecter les anomalies, dans les roulements mais aussi dans l’ensemble du multiplicateur.
« Les grandes entreprises ne mettent pas leurs données en commun, cela a toujours été l’un des principaux obstacles à cette démarche, explique Dennis Nordmark, responsable digitalisation secteur de l’énergie chez SKF. Nous cumulons 150 ans de métier à nous deux. L’intégration de nos connaissances est un véritable bond en avant. »
Comme le souligne Joris Peeters, responsable digitalisation au sein du pôle technologie éolienne de ZF, « SKF et ZF ont mis à profit un projet pilote d’un an pour montrer aux clients ce que nous pouvons réaliser conjointement. Nous avons discerné une demande de la part des clients et nous sommes rendu compte qu’ensemble on pouvait créer et leur offrir de la valeur ajoutée. »
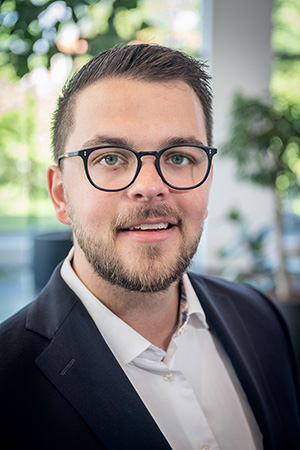
Simplifier les processus pour créer de la valeur ajoutée
La maintenance conditionnelle à distance convient particulièrement à l’industrie éolienne, car elle permet aux exploitants de surveiller les composants pendant que l’éolienne produit de l’énergie. SKF et le fabricant de multiplicateurs ZF ont fait évoluer la maintenance conditionnelle. Leur approche simplifie considérablement les processus pour toutes les parties concernées et réduit de plus de 85 % les délais de réparation pour l’opérateur. Le projet exploite la capacité des capteurs à détecter les anomalies, dans les roulements mais aussi dans l’ensemble du multiplicateur.
« Les grandes entreprises ne mettent pas leurs données en commun, cela a toujours été l’un des principaux obstacles à cette démarche, explique Dennis Nordmark, responsable digitalisation secteur de l’énergie chez SKF. Nous cumulons 150 ans de métier à nous deux. L’intégration de nos connaissances est un véritable bond en avant. »
Comme le souligne Joris Peeters, responsable digitalisation au sein du pôle technologie éolienne de ZF, « SKF et ZF ont mis à profit un projet pilote d’un an pour montrer aux clients ce que nous pouvons réaliser conjointement. Nous avons discerné une demande de la part des clients et nous sommes rendu compte qu’ensemble on pouvait créer et leur offrir de la valeur ajoutée. »
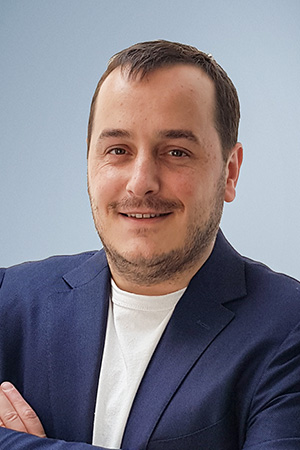
Le système fonctionne selon le principe VOIR-RÉFLÉCHIR-AGIR, indique Joris Boeye, spécialiste en analyse de données chez ZF : « Le système de maintenance conditionnelle détecte un écart, l’analyse de SKF l’amène à nous avertir, et nous avons à notre disposition les données de fabrication et la connaissance du système pour traiter l’alerte : c’est le volet VOIR. Ensuite, nous déterminons la nature de la défaillance, l’endroit où se trouve l’éolienne et le temps qu’il nous reste avant qu’elle tombe en panne : c’est RÉFLÉCHIR. Enfin, nous nous occupons du bon de travail, des techniciens et des pièces de rechange requis : c’est AGIR. »
Mais, comme le souligne Dennis Nordmark de SKF, « la difficulté était de mutualiser nos connaissances sur les vibrations des roulements avec celles des spécialistes des données chez ZF. Ces derniers doivent replacer les données dans leur contexte, sinon celles-ci restent simplement des données et non des informations. »
L’analyse des écarts fait partie du savoir-faire de SKF et de ZF dans leur métier respectif, poursuit-il. « À l’instar d’une voiture qui roule sur un nid de poule, les capteurs du système de maintenance conditionnelle enregistrent une “bosse” en cas de problème survenant dans une partie du multiplicateur. Naturellement, il est beaucoup plus difficile de détecter les minuscules écarts de vibration dans les roulements que de sentir un trou sur la route, mais le principe est le même. On détecte l’anomalie par l’intermédiaire des roues et de la suspension du véhicule. Notre expérience d’automobiliste nous permet de deviner que la cause probable est la dégradation du revêtement. Selon le même principe, les modèles de vibration des roulements changent en présence, par exemple, d’un défaut d’alignement de l’arbre. Grâce à leurs compétences spécialisées, les analystes de SKF et ZF peuvent déterminer ensemble ce que signifie le changement enregistré dans les vibrations, quel composant du multiplicateur est susceptible de le provoquer, quel type de réparation est nécessaire et quand celle-ci doit être effectuée.
« L’objectif est de repérer les défaillances potentielles avant qu’elles ne mènent à un arrêt non planifié. Chaque heure compte : si on se base sur un prix de l’électricité de 60 euros par mégawattheure, la perte de production d’une éolienne de 3,5 MW peut atteindre 1 800 euros par jour. Si l’éolienne ne tourne pas pendant quatre semaines, un arrêt non planifié comme celui-ci peut se traduire par un manque à gagner de 55 000 euros. »
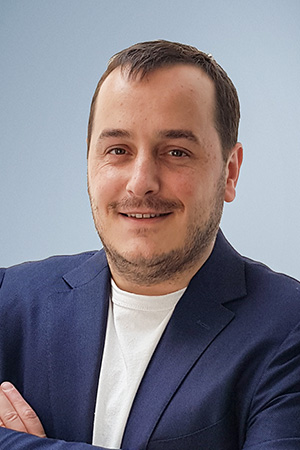
Le système fonctionne selon le principe VOIR-RÉFLÉCHIR-AGIR, indique Joris Boeye, spécialiste en analyse de données chez ZF : « Le système de maintenance conditionnelle détecte un écart, l’analyse de SKF l’amène à nous avertir, et nous avons à notre disposition les données de fabrication et la connaissance du système pour traiter l’alerte : c’est le volet VOIR. Ensuite, nous déterminons la nature de la défaillance, l’endroit où se trouve l’éolienne et le temps qu’il nous reste avant qu’elle tombe en panne : c’est RÉFLÉCHIR. Enfin, nous nous occupons du bon de travail, des techniciens et des pièces de rechange requis : c’est AGIR. »
Mais, comme le souligne Dennis Nordmark de SKF, « la difficulté était de mutualiser nos connaissances sur les vibrations des roulements avec celles des spécialistes des données chez ZF. Ces derniers doivent replacer les données dans leur contexte, sinon celles-ci restent simplement des données et non des informations. »
L’analyse des écarts fait partie du savoir-faire de SKF et de ZF dans leur métier respectif, poursuit-il. « À l’instar d’une voiture qui roule sur un nid de poule, les capteurs du système de maintenance conditionnelle enregistrent une “bosse” en cas de problème survenant dans une partie du multiplicateur. Naturellement, il est beaucoup plus difficile de détecter les minuscules écarts de vibration dans les roulements que de sentir un trou sur la route, mais le principe est le même. On détecte l’anomalie par l’intermédiaire des roues et de la suspension du véhicule. Notre expérience d’automobiliste nous permet de deviner que la cause probable est la dégradation du revêtement. Selon le même principe, les modèles de vibration des roulements changent en présence, par exemple, d’un défaut d’alignement de l’arbre. Grâce à leurs compétences spécialisées, les analystes de SKF et ZF peuvent déterminer ensemble ce que signifie le changement enregistré dans les vibrations, quel composant du multiplicateur est susceptible de le provoquer, quel type de réparation est nécessaire et quand celle-ci doit être effectuée.
« L’objectif est de repérer les défaillances potentielles avant qu’elles ne mènent à un arrêt non planifié. Chaque heure compte : si on se base sur un prix de l’électricité de 60 euros par mégawattheure, la perte de production d’une éolienne de 3,5 MW peut atteindre 1 800 euros par jour. Si l’éolienne ne tourne pas pendant quatre semaines, un arrêt non planifié comme celui-ci peut se traduire par un manque à gagner de 55 000 euros. »
Amélioration du coût actualisé de l’énergie
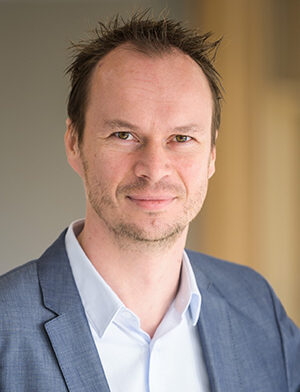
Le projet pilote mené dans un parc éolien comptant une centaine d’éoliennes a démontré que l’objectif était atteignable. Cette étude s’est traduite par une diminution de 60 % des inspections non planifiées sur le terrain, une réduction de 85 % des délais de réparation et une hausse de 0,4 % de la production annuelle d’électricité. Il est maintenant prévu que le programme soit déployé officiellement courant 2021.
Selon Raf Kerkhofs, responsable du développement commercial exploitation et maintenance des éoliennes chez SKF, le potentiel est considérable : « SKF et ZF recueillent toutes deux des informations sur le fonctionnement de leurs produits et peuvent aider les clients à réfléchir en amont aux solutions et à l’optimisation. »
Et Joris Peeters de ZF de suggérer : « Nous mettons actuellement la nouvelle solution en œuvre sur les systèmes de maintenance conditionnelle existants. Ensuite, on pourra l’intégrer aux nouvelles installations. On peut améliorer les paramètres d’alerte et, par la suite, on pourrait même imaginer avoir des ensembles de propulsion autonomes, lesquels permettront à l’usine de déclencher elle-même les réparations. »
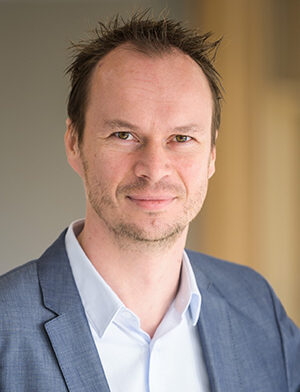
Amélioration du coût actualisé de l’énergie
Le projet pilote mené dans un parc éolien comptant une centaine d’éoliennes a démontré que l’objectif était atteignable. Cette étude s’est traduite par une diminution de 60 % des inspections non planifiées sur le terrain, une réduction de 85 % des délais de réparation et une hausse de 0,4 % de la production annuelle d’électricité. Il est maintenant prévu que le programme soit déployé officiellement courant 2021.
Selon Raf Kerkhofs, responsable du développement commercial exploitation et maintenance des éoliennes chez SKF, le potentiel est considérable : « SKF et ZF recueillent toutes deux des informations sur le fonctionnement de leurs produits et peuvent aider les clients à réfléchir en amont aux solutions et à l’optimisation. »
Et Joris Peeters de ZF de suggérer : « Nous mettons actuellement la nouvelle solution en œuvre sur les systèmes de maintenance conditionnelle existants. Ensuite, on pourra l’intégrer aux nouvelles installations. On peut améliorer les paramètres d’alerte et, par la suite, on pourrait même imaginer avoir des ensembles de propulsion autonomes, lesquels permettront à l’usine de déclencher elle-même les réparations. »
Le système de maintenance conditionnelle SKF IMx
SKF IMx est la nouvelle génération de solutions efficaces et économiques dédiées à la maintenance conditionnelle des éoliennes. C’est une unité de mesure robuste conçue pour être installée dans les parcs éoliens sur terre et en mer.
Les entrées de signaux dynamiques du système sont configurables pour une variété de capteurs. Associé au logiciel SKF @ptitude Observer, SKF IMx constitue un système complet de détection et de prévention précoces des défauts, de conseils automatiques pour corriger les états existants ou imminents, et de maintenance conditionnelle avancée pour améliorer la fiabilité, la disponibilité et les performances.